Dr Ryan M Paul, Graffin Lecturer for 2021 for the American Carbon Society, details the development of graphite in batteries during the last 125 years.
Carbon materials have been a crucial component of battery technology for over 125 years. One of the first commercially successful batteries, the 1.5 Volt Columbia dry cell, used a moulded carbon rod as a current collector.1 The Columbia dry cell was a specific version of a zinc-carbon battery, where the cathode was a mixture of carbon and manganese oxide, and the anode was zinc, which was formed into a can to serve as the battery container. The Columbia dry cell included several practical improvements over previous battery designs and was successfully produced and sold on a mass market scale beginning in the 1890s.
The availability and popularity of the Columbia dry cell, and other zinc-carbon batteries, contributed significantly to the growth of consumer electronics applications in the early age of electrification by powering telephones, flashlights, alarm systems, and automobile ignition systems, among numerous others. Zinc-carbon batteries held a dominant spot until the development and commercialisation of alkaline batteries in the 1950s.1
Graphite’s role in battery technology
Carbon’s role in electrochemical energy storage has only increased over time since the days of the dry cell. As research progressed on lithium-ion battery technology, it was well known that graphite, one of the crystal structures of carbon that is built of a stack of graphene layers, was an excellent host of lithium ions inside its structure and could be almost ideal as an anode material.3
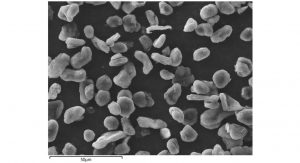
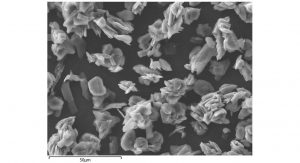
As lithium ions are electrochemically inserted between the graphite layers, a process known as intercalation, the chemistry changes from carbon (C) to LiC6. This resulted in a theoretical specific energy density of 372 mAh/g. However, there were several issues with graphite. In 1972, M Stanley Whittingham identified titanium disulfide (TiS2) as a suitable intercalation cathode.2 However, after the identification of lithium cobalt oxide (LiCoO2) as a high-voltage cathode material in 1981 by John B Goodenough, using polycarbonate (PC) based electrolytes, it seemed like graphite might not work with that combination.2
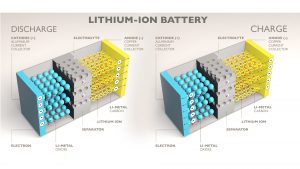
The issue was the PC would irreversibly exfoliate the graphite structure, which caused rapid degradation. However, in the early 1980s, Akira Yoshino and colleagues found that amorphous carbon was a workable anode material when combined with PC-based electrolytes and LiCoO2 as a cathode. This combination was found to have acceptable performance, safety, and stability and was commercialised by Sony in 1991. The contributions of Whittingham, Goodenough, and Yoshino to the advancement of lithium-ion battery technology were firmly acknowledged when they were awarded the Nobel Prize in Chemistry in 2019.2,3
Eventually, advancements in electrolyte chemistry and understanding led to graphite and not amorphous carbon being the anode material of choice by the mid-1990s.2,4 One of the most important developments was identifying a nano-meter scale layer that forms on the graphite surface called the solid electrolyte interphase (SEI). The SEI is exceptionally critical to the anode performance and remains an important research area.5
The processes and uses for natural and synthetic graphite
Both natural and synthetic forms of graphite can be used as an anode material for lithium-ion batteries.6-7 The term ‘natural graphite’ generally refers to multiple types of graphite, including amorphous, flake, and vein graphite. However, practically only flake graphite is typically suitable for lithium-ion battery applications.8
Natural graphite is first mined, separated from heavier mineral matter through intensive crushing, milling and floatation, and the resulting flakes are separated by size and purity. Natural graphite flakes are not used as-is; instead, they are micronised and spherodised through mechanical milling, a process that can have yields of less than 50%.8 The rounder shapes of spherodised graphite will pack with higher density and allow for easier access of lithium-ions to the graphite structure. The purest forms of as-mined natural graphite may have up to 98% purity, but for battery applications, the purity needs to be greater than 99.9%, so separate purification steps are performed.8 The graphite may also undergo a surface treatment or coating step.4,6
One challenge is that natural graphite’s quality, purity, and yield varies, depending on the mine and sometimes within a single mine, as a direct result of the natural geologic processes that produced the graphite.8 Said a different way, the natural graphite cannot be fundamentally changed outside of the milling, sizing, shaping, and purification steps. Furthermore, natural graphite mining is geographically concentrated. Due to its importance in many applications, the lack of direct access to active natural graphite mines has led to graphite being considered a ‘critical’ material.8
Synthetic graphite does not have the benefit of being graphitised through natural processes. For synthetic graphite, the starting point is a highly aromatic petroleum or coal-based residue.4 The residue is thermally treated through successive steps to create a carbonaceous material called coke, which at that stage possesses a mostly amorphous carbon structure. It was amorphous carbon coke that Akira Yoshino used for his battery.2,3
The coke may undergo sizing and shaping steps but will be thermally treated to high temperatures in a process called graphitisation where the product may be heated to 2,800 °C or higher. After graphitisation, the synthetic graphite does not have a flake structure like that of natural graphite but does possess a high degree of crystalline order at the nanometer scale. Synthetic graphite particle shapes tend to be more elongated and contain some voids. Not all aromatic precursors will produce higher quality graphite. The quality of synthetic graphite directly depends on the starting precursors and the processes used.4
Natural and synthetic graphites are not necessarily interchangeable for use in lithium-ion batteries.4,6 Generally, natural graphite possesses a higher degree of crystalline order at the nanometer scale. The quantity of lithium-ions that fit in the structure gives a gravimetric capacity closer to the theoretical one. However, the high degree of crystalline order is more susceptible to exfoliation (degradation) over many cycles. Also, because lithium-ions can only enter the lattice structure through the edges of the graphite and not directly through the planes, the process of electrochemically inserting lithium-ions can be slower.4 Practically, the result is slower charging times, as battery charging is the intercalation (lithiation) step of the graphite. Accordingly, the rate capability of natural graphite is generally lower than synthetic graphite.9
Synthetic graphite has the ability to be engineered.9 However, the amount of electricity required for graphitisation is a significant cost factor. Both natural and synthetic graphite can suffer from low overall product yields of around 50% or less due to the number of steps involved. Synthetic graphite is considered better for higher performance applications, such as electric vehicles, although some natural graphite may be blended in.4,6,7
The final graphite anode powder product is in the size range of 20 microns.9 The desirable anode powder characteristics are:
• High capacity;
• High first cycle efficiency;
• High rate capability;
• Long calendar (cycle) life;
• High pack density; and
• High electrical and thermal conductivity.
Graphite applications and research
For automotive (EV) applications, a typical 400-kg lithium-ion battery may contain around 71kg of graphite, according to data from Volkswagen Group Components.10 This is the second most needed material in the battery besides aluminium.10 Despite being called a lithium-ion battery, the actual amount of lithium is about 8kg.10
The availability and quality of graphite is a crucial consideration. Although graphite is well known as a battery anode material, it is a highly engineered and processed form of graphite used in lithium-ion batteries. Whether natural or synthetic, the process to get to a final anode powder product is intensive. Today, approximately 200,000 metric tons of graphite anode powder is used for lithium-ion batteries; however, predictions for future demand of graphite anode powder range from 3 to 20 times the current amount.11
The main growth driver for graphite demand is EVs, although growth is expected in all applications. While significant research is underway on new battery chemistries and technologies that may not require graphite, there is a substantial burden on demonstrating safety, stability, and manufacturability.11 Indeed, for the next decade, it is difficult to see any other material besides graphite meeting the demands considering the safety, stability, performance, cost, and availability.11
There are several active research areas for graphite anode materials. It is desired to have higher energy storage capacity and faster charging times.4 Speed of charging may be one of the most critical areas, which requires enhancing the lithiation kinetics into the graphite.4 Also, a better understanding of SEI formation, evolution, and stability is needed to improve cycle life and overall performance.5 There is also the critical question of recycling the graphite at the end of the battery life.12 This is made challenging by the chemicals used in the battery and the methods of manufacture.12
Dr Ryan M Paul
Ryan is a R&D Associate in the Carbon and Composites group in the Chemical Sciences Division at Oak Ridge National Laboratory. He has a B.E. and M.S. from Youngstown State University, and a M.S. and Ph.D. from The Ohio State University. Prior to joining ORNL, Ryan spent over nine years in industry, as Associate Director of R&D and materials scientist at GrafTech International Holdings Inc., in Cleveland, OH. At GrafTech, he led the commercialisation of several new products and processes using advanced materials science understanding and intelligently applied modelling and simulation tools. From 2014-17, he was Principal Investigator for a US Department of Energy Advanced Manufacturing Office cooperative agreement (DE-EE0005779) named ‘Low-Cost Bio-Based Carbon Fibers for High-Temperature Processing’, a collaboration with ORNL.
Ryan is internationally recognised in the field of carbon materials science. He is a prolific technical writer and speaker, with 11 publications, 6 invited talks, 26 public presentations, and 30 GrafTech proprietary internal technical memoranda. He is co-inventor on two patent applications.
He is passionate about mentoring and inspiring others in science and engineering for both industry and academic roles, and promoting scientific literacy. He serves on the advisory board for the American Carbon Society and the Ohio Academy of Science, and was an active executive committee member for the Cleveland Chapter of ASM International, and now for the Oak Ridge Chapter. He was named a STEM Exemplar by the Believe in Ohio Program. His awards include the Technical Achievement Award by the Cleveland Technical Societies Council, the Young Members Award by ASM Cleveland, and the Chairperson’s Award by ASM Cleveland. In recognition of his achievements in carbon materials science, the American Carbon Society selected him as the prestigious Graffin Lecturer for 2021.
References
- The Columbia Dry Cell Battery. National Historic Chemical Landmarks. American Chemical Society. Accessed 2021-11-17.
- Xu, Kang. ‘Li-ion battery electrolytes’. Nature Energy 6, no. 7 (2021): 763-763.
- The Nobel Prize in Chemistry 2019. NobelPrize.org. Nobel Prize Outreach AB 2021. Fri. 19 Nov 2021.
- Asenbauer, Jakob, Tobias Eisenmann, Matthias Kuenzel, Arefeh Kazzazi, Zhen Chen, and Dominic Bresser. ‘The success story of graphite as a lithium-ion anode material–fundamentals, remaining challenges, and recent developments including silicon (oxide) composites’. Sustainable Energy & Fuels 4, no. 11 (2020): 5387-5416.
- An, Seong Jin, Jianlin Li, Claus Daniel, Debasish Mohanty, Shrikant Nagpure, and David L. Wood III. ‘The state of understanding of the lithium-ion-battery graphite solid electrolyte interphase (SEI) and its relationship to formation cycling’. Carbon 105 (2016): 52-76.
- Wissler, Mathis. ‘Graphite and carbon powders for electrochemical applications’. Journal of power sources 156, no. 2 (2006): 142-150.
- Mao, Chengyu, Marissa Wood, Lamuel David, Seong Jin An, Yangping Sheng, Zhijia Du, Harry M. Meyer, Rose E. Ruther, and David L. Wood. ‘Selecting the Best Graphite for Long-Life, High-Energy Li-Ion Batteries’. Journal of The Electrochemical Society 165, no. 9 (2018): A1837-A1845.
- Jara, Allah D., Amha Betemariam, Girma Woldetinsae, and Jung Yong Kim. ‘Purification, application and current market trend of natural graphite: A review’. International Journal of Mining Science and Technology 29, no. 5 (2019): 671-689.
- Buqa, Hilmi, Dietrich Goers, Michael Holzapfel, Michael E. Spahr, and Petr Novák. ‘High rate capability of graphite negative electrodes for lithium-ion batteries’. Journal of the Electrochemical Society 152, no. 2 (2005): A474.
- “Transforming old into new: Volkswagen Group Components commences battery recycling” (Press Release), Posted 2021-01-29, Accessed 2021-11-19
- Xu, Chengjian, Qiang Dai, Linda Gaines, Mingming Hu, Arnold Tukker, and Bernhard Steubing. ‘Future material demand for automotive lithium-based batteries’. Communications Materials 1, no. 1 (2020): 1-10.
- Moradi, Bahar, and Gerardine G. Botte. ‘Recycling of graphite anodes for the next generation of lithium ion batteries’. Journal of Applied Electrochemistry 46, no. 2 (2016): 123-148.
Dr Ryan M Paul
Graffin Lecturer for 2021 for the American Carbon Society
paulrm@ornl.gov
www.americancarbonsociety.org
https://www.linkedin.com/company/american-carbon-society
Please note, this article will also appear in the eighth edition of our quarterly publication.