Andrew Storer, CEO of the Nuclear Advanced Manufacturing Research Centre, discusses the UK’s plans for a strong nuclear power future and explains how the Nuclear AMRC is helping to support companies in the sector.
Nuclear power has operated in the UK for decades and it looks set to only accelerate on an upwards trajectory moving forward. In April 2022, the UK government announced the British Energy Security Strategy, following a successful decade in which it approved the first nuclear power plant in a generation and achieved a fivefold increase in renewables. Amongst promises such as vastly increasing hydrogen production, the Strategy set out a variety of measures to improve its nuclear power capacity. A statement on the Strategy from Prime Minister Boris Johnson read: “We’re embracing the safe, clean, affordable new generation of nuclear reactors, taking the UK back to pre-eminence in a field where we once led the world.” The statement added that the government will “massively invest in nuclear power.”
The Strategy builds on the government’s Ten Point Plan for a Green Industrial Revolution, outlining approaches to support green jobs and accelerate the UK’s path to net zero. The Plan details that the UK is pursuing large-scale nuclear power and is seeking to advance the future of nuclear through further investment in small modular reactors (SMRs) and advanced modular reactors (AMRs). The plan includes a £120m Future Nuclear Enabling Fund to progress new nuclear, a £210m investment to develop SMRs with Rolls-Royce, and a £100m investment to support the development of EDF Energy’s Sizewell C nuclear power station in Suffolk. Some of this investment will come from the Advanced Nuclear Fund of up to £385m to support the next generation of nuclear technology.
With the rise of the nuclear industry within the UK, it is essential that there are suitable research and testing facilities to support companies in the field. The Nuclear Advanced Manufacturing Research Centre (Nuclear AMRC), backed by industry leaders and government and owned by the University of Sheffield, helps UK manufacturers win work across the nuclear sector – in new build, operations and decommissioning – and in other quality-critical industries. Its facilities and services are open to all.
The centre’s engineers and sector specialists work with companies to develop innovative techniques and optimised processes for large-scale high-precision manufacturing. Companies can use the Nuclear AMRC’s state-of-the-art workshops to develop and test new processes on production-scale machines without losing capacity in their own factories.
The Nuclear AMRC also provides a range of supply chain development support to help manufacturers enter the nuclear market and compete worldwide. Its flagship Fit For Nuclear programme is a unique diagnostic tool which lets companies measure their operations against industry requirements and close any gaps.
As well as its core research factory on the Advanced Manufacturing Park in South Yorkshire, the centre operates a modularisation R&D facility at Birchwood Park, and is developing new technology capabilities at Nuclear AMRC Midlands in Derby. It is part of the High Value Manufacturing Catapult – a national alliance of seven leading manufacturing research centres.
The Innovation Platform spoke to Andrew Storer, CEO of the Nuclear AMRC, to find out more about the current and future nuclear outlook in the UK and the Nuclear AMRC’s role in furthering nuclear development.
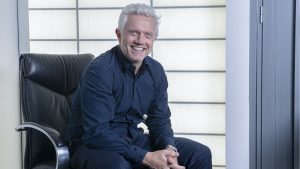
What does the UK nuclear energy landscape look like currently and how has this changed in recent years?
The nuclear landscape in the UK looks brighter than it has for many years. As a nation, we are committed to reducing our greenhouse gas emissions to net zero by 2050, with a target of decarbonising electricity generation by 2035. The only realistic way this can be achieved is by deploying nuclear power alongside renewables, as nuclear is the only proven low carbon generation technology which can provide reliable baseload power to balance the inherent variability of wind, solar, and tidal.
There has been a lot of detailed modelling of potential pathways to net zero – by international bodies such as the International Panel on Climate Change and the International Energy Authority, as well as UK bodies such as the Climate Change Committee and Energy Systems Catapult – and all show the need for nuclear as part of the energy mix. The UK government has recognised this, with a target for 24 GW of nuclear capacity by 2050 announced in April as part of the British Energy Security Strategy.
Around 12 years ago, when the Nuclear AMRC was first established, there were plans for about 19 GW of new nuclear capacity in the UK. Apart from EDF Energy’s Hinkley Point C, those projects have not yet happened, largely because of financial challenges. Under the old Contracts for Difference model introduced in the 2000s, plant developers had to finance the entire construction cost of a nuclear project – tens of billions of pounds over a decade or more – and only start receiving revenue when the station starts generating electricity. That is not an attractive investment profile, and the cost of financing has greatly increased the total cost of building Hinkley Point C.
The UK has now legislated for the Regulated Asset Base (RAB) financing model for nuclear power projects. RAB is designed to provide a more attractive investment profile for major infrastructure projects by providing an income stream during construction through a small surcharge on consumers, reducing project risk for the investor.
The other big change we have seen in recent years is the emergence of small modular reactors as a viable complement to gigawatt-scale reactors, such as the Framatome EPRs being built at Hinkley Point. As they are smaller and quicker to build, SMRs should be more attractive to institutional investors. And, because they are designed to be made in factories, manufacturers will be able to use techniques from other sectors, such as aerospace, to drive down costs and improve productivity.
We are also seeing growing interest in other new designs of advanced reactor, particularly high-temperature gas-cooled reactors which can be used for efficient low carbon hydrogen production and industrial decarbonisation by the 2040s.
There is fusion power – an area where the UK is genuinely a world-leader. The UK Atomic Energy Authority (UKAEA) is now working towards a prototype fusion power plant, the Spherical Tokamak for Energy Production (STEP), in the early 2040s. Commercial fusion power will be the key to limitless low carbon power in the second half of this century.
How important is it to develop a strong nuclear energy infrastructure within the UK?
It is vital that we develop a strong infrastructure for nuclear power in the UK – not just because we need to decarbonise the economy, but because it offers a greater degree of energy security and frees us from the wild price fluctuations of the fossil fuel markets.
The UK has strengths across the nuclear lifecycle. We can manufacture nuclear fuel – though we do depend on imports of uranium – and we have a very well-established and world-leading decommissioning sector. Now, we have several domestically owned reactor technologies in development, including the Rolls-Royce SMR and a variety of advanced modular reactors and fusion technologies.
Developing the UK nuclear power sector will also deliver significant economic benefits across the UK – more than any other energy technology. Those benefits will be felt nationwide – around 90% of jobs in the industry are based outside London and the southeast, and the average value of jobs in nuclear is around twice the national average.
How is the Nuclear Advanced Manufacturing Research Centre working to support nuclear development and innovation within the UK? What are the most significant projects/developments?
Our mission at the Nuclear AMRC is to help UK manufacturers win work across the nuclear sector. We do that in two ways. Like the other centres in the High Value Manufacturing Catapult, we deliver manufacturing innovation to help companies optimise their production or develop new technical capabilities which can improve productivity while maintaining the strictest quality standards. We also do a lot of work in supply chain development, to ensure that UK suppliers can meet the requirements of nuclear projects.
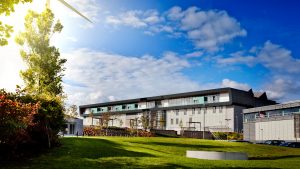
On the manufacturing R&D side, our original focus was on the mechanical engineering aspects of nuclear new build. That means large-scale quality-critical machining, welding, cladding and metrology, and our Rotherham research factory is home to some of the largest and most advanced machining platforms and joining cells available for independent industrial research anywhere in the world. In recent years, we have expanded into new technology areas including modularisation, controls and instrumentation, digital engineering and various kinds of additive and near-net shape manufacturing.
We have helped some of our founding partners to achieve really significant improvements in productivity. For example, we worked with Rolls-Royce to show that assembly time for a complex heat exchanger, featuring some 5,000 tubes threaded through 11 plates, can be reduced by at least half. We helped Sheffield Forgemasters to reduce rough milling time for a large nuclear forging by over 40%.
In one long-term collaboration, we have worked with partners in the US to demonstrate that electron beam welding and other techniques can help cut production time for an SMR pressure vessel from about two and a half years to less than 12 months. One of our biggest achievements there was showing that welding time for a vessel section could be cut from 60 hours to just one hour, with energy savings equivalent to almost two tonnes of CO2 per weld.
We have also worked extensively with partners from the nuclear decommissioning sector. We supported Sellafield Ltd and its suppliers in reducing the cost of waste containers for the long-term storage of hazardous waste. Tens of thousands of these boxes will be needed to decommission the UK’s legacy nuclear sites, and we have demonstrated how design changes and advanced manufacturing techniques could save the taxpayer hundreds of millions of pounds over the lifetime of the programme. We are looking at the manufacturing requirements of the proposed Geological Disposal Facility for permanent waste storage, and our instrumentation researchers have worked on smart sensors which can monitor the condition of waste containers over decades by harvesting ambient radiation to power themselves.
The other side of our work is about developing the UK supply chain, helping manufacturers meet the requirements of the industry in terms of quality management and safety culture, as well as technical capabilities. We also work with reactor developers and the industry top tier to ensure that new power plants can be manufactured cost effectively, with as much UK content as possible.
Our flagship programme, Fit For Nuclear (F4N), has helped around 1,000 UK manufacturers to measure their operations against industry standards and take the necessary steps to close any gaps. F4N has been hugely successful, and we are now adapting the model to support other growing low carbon sectors, including offshore renewables, carbon capture, and hydrogen production.
The companies we have worked with on supply chain programmes have told us that our support has helped them win £2.5bn of new contracts, and create or safeguard more than 10,000 jobs. That is really just the tip of the iceberg if you look at the investment we need to reach net zero, and the opportunities for UK manufacturers.
How are you ensuring the safety and sustainability of nuclear development?
A lot of our manufacturing development work is about ensuring that new manufacturing processes meet the requirements for nuclear safety. The big challenge is that the international nuclear codes and standards often specify the use of old manufacturing technologies which are much less productive, so we need to demonstrate that these newer methods can produce components which will be at least as safe and reliable over decades of service.
In some cases, we are taking a technique such as electron beam welding, which is already well established in other sectors such as aerospace or shipbuilding, and demonstrating through rigorous trials and analysis that it can meet nuclear standards. In other projects, we are developing more innovative methods for shaping and joining the exotic alloys which will be required for fusion reactors.
We also look at sustainable manufacturing processes which can reduce the environmental cost of production – for example, by moving from huge amounts of oil-based machining fluids to much smaller quantities of advanced coolant, or power beam welding techniques which can join a thick section in a single pass without the need for repeated heat treatment.
In one recent project, we worked with Cavendish Nuclear and other partners to develop an automated system for real-time identification of weld defects. That can be a gamechanger for high-integrity fabrications – by reducing inspection time by hours, it improves productivity, schedule certainty and resource efficiency.
Safety is the overriding priority of the nuclear power industry, and a large part of our F4N service is helping manufacturers develop a good safety culture.
It is thought that small modular reactors will have a large role to play in the global energy transition. What does it mean for Rolls-Royce to be building the UK’s first SMR? What is your involvement in the process and how is progress going so far?
The Rolls-Royce SMR can play a huge part in the UK’s journey to net zero emissions. As a small factory-built reactor, it is a much better fit for the current capabilities of the UK nuclear supply chain, which will help us maximise the economic benefits of the energy transition.
We were part of the UK SMR Consortium which carried out the first phase of development, with £18m match-funding from government. Our work focused on demonstrating how advanced manufacturing techniques can reduce capital costs and production time, in areas such as portable machining, post-process cleanliness, welding and cladding, measurement, and digital manufacturing.

Last November, we hosted the launch of the Rolls-Royce SMR business with £210m government support matched by private investment. We are continuing to focus on developing the manufacturing capabilities for the SMR, including the creation of a fully integrated pre-production proving facility for SMR manufacturing within our Rotherham centre.
We will produce two advanced manufacturing prototypes – a representative-scaled heavy pressure vessel, measuring some 6m in length and weighing 27 tonnes, and a full-scale vessel closure head of around 4.5m diameter and 40 tonne mass. Both will be produced from forgings to be provided by Sheffield Forgemasters, and fully welded and clad to nuclear-quality standards.
These will be some of the largest and most challenging parts we have worked on, and will bring together many of the technologies and techniques we have been developing over the past decade.
Essentially, our task is to help ensure that as much of the Rolls-Royce SMR as possible can be made in UK factories, as cost-effectively as possible, while meeting all the quality and safety standards expected by nuclear customers and regulators.
About Andrew Storer
Andrew was appointed as Nuclear AMRC’s Chief Executive Officer in August 2017, having originally joined the centre as Managing Director 18 months earlier. Prior to this, he spent six years as Programme Director for Rolls-Royce’s civil nuclear business, leading customer engagement and bids with new build developers. Before working in civil nuclear, he was General Manager for submarine fleet support, ensuring at-sea availability.
He started work as an apprentice at the Nuclear Energy Institute (NEI) and developed his career through various engineering roles working on large coal and gas fired power stations, as well as delivering components for Sizewell B. He represents the Nuclear AMRC on the Nuclear Industry Council, is leading the Winning UK Business work programme as part of the Nuclear Sector Deal, and is part of the steering group for the Great British Nuclear Vehicle announced in the British Energy Security Strategy.
He is a board member of the Nuclear Industry Association and the Nuclear Innovation Research Advisory Board; UK representative and materials and manufacturing lead on the Generation IV International Forum; and a member of the Royal Society’s Nuclear Cogeneration Steering Group. He is Visiting Professor of Nuclear Manufacturing and Capability Development at the University of Sheffield.
Andrew Storer
CEO
Nuclear Advanced Manufacturing Research Centre
https://namrc.co.uk
https://www.linkedin.com/company/nuclear-amrc/
https://twitter.com/NuclearAMRC
Please note, this article will also appear in the eleventh edition of our quarterly publication.