Virginia Commonwealth University is developing innovative metal treatments to increase corrosion resistance in molten salt systems, improving cost-efficiency and reducing waste.
Corrosion of materials is a major aspect of many countries’ economic status, regularly reported as over 3% of the global Gross Domestic Product (GDP) and between $2-3tr.1,2
Many corrosion studies have been done by a myriad of universities and national labs across molten salt reactors (MSRs), pyro-processing systems and concentrated solar plant (CSP) salts.3,4,5,6,7,8,9,10
While the variety of molten salts across this spectrum have distinct properties that make them excel in their individual fields, the underlying issue of corrosion and the need for corrosion resistance can be seen throughout them all, particularly in how the mechanism for corrosion resistance is based in the alloy content of the least noble element and preventing its dissolution.3
At a molecular level, the ionic nature and high temperature of molten salt systems create a uniquely aggressive and corrosive operating environment. In an attempt to subdue this damage and decrease corrosion losses, high-cost material alloys, chemical/electrical redox potential control, and various metal treatments are among previously tested solutions.
Pre-treatment to form oxide layers via high-temperature oxidation atmospheres has proven useful in CSP studies, and laser ablation treatments within the automotive industry have shown corrosion resistance improvements.11,12,13
By utilising metal treatments like laser ablation to fine-tune oxide layer application, increased corrosion resistance can be developed to prevent the dissolution at the heart of salt system material loss.3
Corrosion explained
Corrosion is an electrochemical reaction, often on the surface of a metal, that can be described as destructive and unintentional.14 A full electrical circuit is made between two metals with an electrochemical potential difference, bridged by a conductor on one side and the ions of a molten salt electrolyte on the other (see Fig. 1 below).15
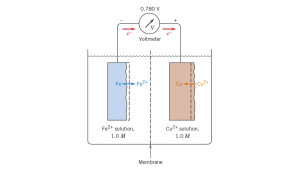
The potential difference removes electrons from the metal with the lower reduction potential, causing a positive ion of that metal to separate from the anode. This electrode corrodes. Following the electrical path, an electron from the other electrode is attracted to a positive metal ion in the salt solution, creating a neutral metal atom that deposits on that electrode. This second electrode, where deposition happens, is the cathode.
In the case of corrosion in molten salt environments, the metals of the equipment are anodes that dissolve via oxidation, and impurities (like moisture, oxygen, or fission products) are cathodically reduced. 3
Some materials, when subjected to high temperature, high pH or high energy interactions like laser ablation in the presence of oxidants, will undergo a layer of corrosion at the surface.16,17 This reduction-oxidation (redox) reaction will create a layer of scale across the surface of the metal that requires a higher electrochemical potential difference in order to corrode, if it is possible at all.
This reaction is referred to as passive corrosion or, in terms of the scale specifically, can be referred to as creating a passivation layer. Though less effective when incomplete and porous, creating a solid, fully-formed oxide layer prior to use in the environment can ensure that the layer is fully passivating prior to being subjected to the harsh environment.
By achieving this passivation, the surface becomes resistant to pitting and crevice corrosion that may be otherwise caused by imperfections in the surface layer and impurities in the environment.18 Active metals with porous layers are prone to localised attack with relatively high rates of corrosion due to the inequality of diffusion and consumption rates of oxidants in the melt.19
In the event of a fully formed, protective scale, the corrosion rate is limited by the transportation of metal ions rather than the diffusion of oxidants.19
Passivation to prevent corrosion
Many studies have pointed to passivation as a means of corrosion prevention based on its ability to block active sites on alloy surfaces.3,4,19,20,21,22,23,24 Specifically, layers are likely to naturally form on many alloys when used in molten salt systems.
However, these layers are generally porous and incomplete due to impurities within the salt, causing localised oxidant attacks.19,15 The Gomez-Vidal, Guo and Chowdari groups point to aluminium oxide layers as effective passivation barriers against chromium dissolution as the predominant mechanism in high-temperature salt corrosion.3,11,5
It is likely, however, that the oxygen content or energy distribution of the passivation method was lacking in the attempts researched by Gomez-Vidal et al., as evidenced by the unstable alumina layers present and spalling during thermal cycling and Cr depletion after testing was completed.12 This depletion can likely be attributed to the presence of porous oxide layers rather than the desired complete layers.
Analysing data like Nyquist plots, the corrosion resistance of porous passivation layers is generally higher than that of bare, active metal.25 However, unless the parameters of the system are such that it will facilitate a full film, over time, the corrosion resistance of the material decreases due to the deterioration of the partial layer.
A fully formed layer will have a much longer lasting and more significant corrosion resistance (as seen by the Nyquist plot studies shown in Zeng, Wang, and Wu’s 2001 work) without the diffusion and subsequent electrolyte resistance increase.19 These are representative of lower, long-term corrosion rates.
Because of the success of layer formation in high-temperature CSP environments, as well as the decrease in corrosion rates due to laser ablation of automotive aluminium joints, utilisation of laser ablation on nuclear-based materials to be used in molten salt appears feasible. Beyond current work being done on the subject, plasma-sprayed aluminium coatings in aqueous chloride environments have already shown decreased corrosion rates on steel.12
Additionally, the minimisation of environmental control requirements and ultimate adjustability of laser parameters in the application of passivation layers over different sizes, shapes and materials bodes well for increased usability.
By being able to fine-tune the application of oxidation layers specifically to ionisation energies of the desired material, passivation layers most likely to prevent alloy dissolution are expected to not only be feasible but repeatable at lower costs than temperature-based methods or currently recommended alloys.
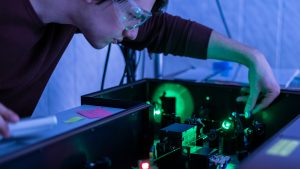
Utilising lasers
Laser ablation is the use of focused photons at certain energies to create a high-power-density plasma at a sample’s surface. This energy is transferred to the material through thermal conduction, radiative transfer and shockwave heating, ultimately ejecting particles and ions from the surface.26
It is characterised by small ablation craters along the material surface, proportional to the laser beam diameter. When used in the application of oxidation layers, the high temperature of the plasma at the surface can also break atmospheric oxygen bonds, allowing the oxide to form from ejected metal ions and environmental oxygen ions. As the plasma cools and energy is released, the formed oxides deposit on the sample surface.
The adjustment and combination of laser parameters, including laser diameter/spot size, wavelength, spacing/overlap, etc., directly affects the energy deposited and, subsequently, the ability to form oxide layers in addition to their thickness. The latter is also directly affected by oxygen partial pressure in the application environment.11
High-temperature environments at low oxygen partial pressures created dense and smooth alpha phase alumina, most likely to create fully formed passivation layers, whereas higher partial pressures showed mixed-oxide and theta phase alumina, which proved to be non-protective.11
This smooth, fully formed, protective layer will not only minimise corrosion potential but ideally present primarily terrace ions for dissolution, minimising the more readily available kink sites.3
An evolving solution
Reducing the corrosion of the array of metallic alloys used for molten salt systems is of significant importance to our society and economy.
The current state of the literature regarding this field shows a varied and in-depth range of experimental testing, but it can always use improvement.
The implementation of innovative approaches to corrosion resistance and passivation is vital to improving corrosion mitigation and the overall state of corrosion damage not only in this field but across the engineering spectrum.
The utilisation of laser ablation as a precise and flexible means of applying passivation layers stands to reduce the cost of materials required to employ molten salts in solar and reactor power, as well as the future of fuel waste recycling.
References
- B Fuente, I Díaz, J Simancas Morcillo M Annual atmospheric corrosion of carbon steel worldwide. An integration of ISOCORRAG ICP/UNECE and MICAT databases. Materials, 10 (2017), p. 601
- Kania, Henryk. “Corrosion and Anticorrosion of Alloys/Metals: The Important Global Issue.” Coatings 13, no. 2 (2023): 216
- Guo, Shaoqiang, Jinsuo Zhang, Wei Wu, and Wentao Zhou. “Corrosion in the molten fluoride and chloride salts and materials development for nuclear applications.” Progress in Materials Science 97 (2018): 448-487
- Chowdari, Jagadeeswara Rao, and Sublime Ningshen. “Molten salt corrosion of candidate materials in LiCl–KCl eutectic for pyrochemical reprocessing applications: a review.” Corrosion Reviews 41, no. 2 (2023): 117-141
- Alimgulov, Ruslan R., Anastasia I. Trubcheninova, Aleksandr V. Abramov, Arkadiy Yu Zhilyakov, Sergey V. Belikov, Oleg I. Rebrin, and Ilya B. Polovov. “Corrosion of Metallic Materials in 3LiCl-2KCl and 3LiCl-2KCl-UCl3.” ECS Transactions 98, no. 10 (2020): 307
- Park, Jun Woo, and Jong-Il Yun. “Corrosion Behaviors of SS316 and Ni-base Alloys in Molten LiCl-KCl Salt at High Temperature.” order 101, no. 001: 111
- Shankar, A. Ravi, A. Kanagasundar, and U. Kamachi Mudali. “Corrosion of nickel-containing alloys in molten LiCl-KCl medium.” Corrosion 69, no. 1 (2013): 48-57
- Jia, Yanhong, Shuangshuang Chang, Xin Du, and Shaoqiang Guo. “Corrosion Performance of Commercial Alloys and Refractory Metals in Conditions for Electrorefining of Spent Nuclear Fuels.” Crystals 13, no. 5 (2023): 817
- Ghaznavi, Touraj, Suraj Y. Persaud, and Roger C. Newman. “Electrochemical corrosion studies in molten chloride salts.” Journal of the Electrochemical Society 169, no. 6 (2022): 061502
- Zhongdi, Yu, Jinping Wu, Wei Liu, Wei Zai, Longfei Xie, and Meng Cao. “Interfacial Corrosion Behavior of the Hastelloy N and C276 Alloy in Molten Licl-Kcl Salt at 550° C.” Available at SSRN 4365732
- Gomez-Vidal, J. C., A. G., Fernandez, R., Tirawat, C. Turchi, and W., Huddleston. “Corrosion resistance of alumina-forming alloys against molten chlorides for energy production. I: Pre-oxidation treatment and isothermal corrosion tests.” Solar Energy Materials and Solar Cells 166 (2017): 222-233
- J.C. Gomez-Vidal, A.G. Fernandez, R. Tirawat, C. Turchi and W. Huddleston. “Corrosion Resistance of Alumina Forming Alloys Against Molten Chlorides for Energy Production. II: Electrochemical Impedance Spectroscopy Under Thermal Cycling Conditions,” Solar Energy Materials & Solar Cells, 166, 234–245 (2017)
- H. Wan, J. Lin and J. Min. “Effect of Laser Ablation Treatment on Corrosion Resistance of Adhesive-Bonded Al Alloy Joints,” Surface and Coatings Technology, 345, 13-21 (2018)
- Materials Science and Engineering AN INTRODUCTION WILLIAM D. CALLISTER, JR. DAVID G. RETHWISCH (2018,) 10th edition. | Hoboken, NJ: Wiley, [2018]
- Denny A. Jones (1996) Principles and Prevention of Corrosion. Prentice Hall
- Protectiveness, morphology and composition of corrosion products formed on carbon steel in the presence of Cl−, Ca2+ and Mg2+ in high-pressure CO2 environments Yong Hua*, Amir Shamsa, Richard Barker, Anne Neville Applied Surface Science 455 (2018) 667–682
- Torbatisarraf, Seyedhamidreza, “Effect of Microstructure on Corrosion of Structural and Advanced Alloys” (2019). All Dissertations. 2652.
- Investigation on the efficiency of corrosion inhibitor in CO2 corrosion of carbon steel in the presence of iron carbonate scale Mehdi Javidi*, Reza Chamanfar, Shima Bekhrad Journal of Natural Gas Science and Engineering 61 (2019) 197–205
- Zeng CL, Wang W, Wu WT (2001) Electrochemical impedance models for molten salt corrosion. Corrosion Science 43:787-801.
- Srdjan Nešić, Key issues related to modelling of internal corrosion of oil and gas pipelines – A review, Corrosion Science, Volume 49, Issue 12, 2007, Pages 4308-4338, ISSN 0010-938X
- Corrosion of carbon steel and the passivating properties of corrosion films formed under high-PT geothermal conditions Niklas Mundhenka Kevin G. Knaussa Siva R.S. Bandarub Robert Wonnebergerc Thomas M. Devineb Science of The Total Environment Volume 677, 10 August 2019, Pages 307-314
- Protectiveness, morphology and composition of corrosion products formed on carbon steel in the presence of Cl−, Ca2+ and Mg2+ in high-pressure CO2 environments Yong Hua*, Amir Shamsa, Richard Barker, Anne Neville Applied Surface Science 455 (2018) 667–682
- Cement and Concrete Composites Volume 112, September 2020, 103661 Mechanistic study on initial passivation and surface chemistry of steel bars in nano-silica cement pastes Haibing Zhenga Chi Sun Poona Weihua Libc
- Study of the passivation of carbon steel in simulated concrete pore solution using scanning electrochemical microscope (SECM) H. Torbati-Sarrafa A. Poursaeeb Materialia Volume 2, October 2018, Pages 19-22
- V. Venegas, F. Caleyo, T. Baudin, J.H. Espina-Hernández, J.M. Hallen, On the role of crystallographic texture in mitigating hydrogen-induced cracking in pipeline steels, Corrosion Science, Volume 53, Issue 12, 2011, Pages 4204-4212, ISSN 0010-938X
- Singh, J. P., & Thakur, S. N. (Eds.). (2020). Laser-induced breakdown spectroscopy. Elsevier
Please note, this article will also appear in the 18th edition of our quarterly publication.