The realisation of a fusion plant faces multiple challenges, for example controlling the heat load on the wall. An expert team of the Dutch Institute for Fundamental Energy Research (DIFFER) is helping Commonwealth Fusion Systems (CFS) to develop the SPARC tokamak.
In 2024 the Dutch Institute for Fundamental Energy Research (DIFFER) and the American private fusion company Commonwealth Fusion Systems (CFS) signed a two-year Statement of Work to advance the realisation of fusion energy. The collaboration project aims to develop a framework for exhaust control, including models, observers, and controllers for CFS’s SPARC tokamak fusion machine.
Challenges for SPARC
CFS is building the SPARC tokamak in Devens, Massachusetts, possibly the world’s first demonstration plant that will generate net energy from fusion using magnetic confinement, generally seen as the path to a commercial power plant. In terms of size, it’s a tokamak smaller than ITER in France, similar in size to ASDEX Upgrade in Germany or KSTAR in South Korea.
With SPARC, CFS aims to pave the way for ARC, the first fusion power plant that will supply energy to the power grid. The road to a tokamak like ARC has several major challenges, such as controlling the heat load on the wall. That’s the challenge DIFFER will focus on in this project.
SPARC is planned to achieve a ‘burning plasma’, a self-sustaining fusion reaction in which different isotopes of the element hydrogen fuse together to form helium without the need for any further input of energy. CFS aims to be the first company to achieve that on the path to a commercial power plant.
The SPARC design would be far more powerful than existing fusion plants, achieving fusion performance comparable to that expected in the much larger ITER tokamak. The high power in a small size is made possible by advances in superconducting magnets that allow for a much stronger magnetic field to confine the hot plasma.
New insights
DIFFER is known for its leading role in controlling the heat load on the wall of a fusion plant by controlling the exhaust of the machine. The institute has past experience and expertise in developing control frameworks for fusion machines. In former projects, DIFFER researchers developed and demonstrated exhaust control on ASDEX-U, TCV, and JET (the largest tokamak in the world).
Moreover, DIFFER has been on the front of developing dynamic exhaust models that are necessary for the development of advanced control.
Requirements for SPARC
Despite all efforts, more research is needed. Heat exhaust control on a SPARC tokamak is a complex problem which requires managing core and edge performance at the same time. SPARC is designed to operate in a highly dissipative edge plasma regime using impurity gas puffing.
Previous edge plasma modelling work using the 2D SOLPS-ITER code (SOLPS stands for ‘Scrape-Off Layer Plasma Simulation’) has successfully informed the SPARC technical requirements of the gas puffing time scales, its location, and the pumping louvres. Whilst gas puffing can help with heat exhaust management, it can also help mitigate plasma core disturbances and help maintain high-performance plasmas.
However, given the compact design of SPARC, gas puffing can adversely impact core performance if not properly orchestrated with the requirements of plasma scenarios. Therefore, an exhaust-control-oriented controller is required to manage gas puffing for SPARC plasma scenarios.
DIFFER’s expertise
Due to the compact size of a fusion-producing plant made possible by a super high magnetic field, a really precise and quick cooldown of the plasma towards the wall becomes extra challenging. The specific knowledge required for this will be provided by the DIFFER expert team.
SOLPS-ITER simulations will help map out the operational space of the SPARC exhaust conditions for the so-called divertor, a region that redirects the plasma-wall interaction further away from the core plasma where the fusion process should take place. This helps to minimise the impact of seeded impurities and gas puffing on the overall plasma performance. The exhaust operational space will be provided as a function of (controllable) parameters, like the neutral pressure in the divertor (responding to the gas puff applied) that helps to mitigate the heat-flux arriving at plasma-facing components (PFCs) by plasma-neutral interactions. A second parameter is the impurity concentration from seeded impurities (inter gases like Argon or Krypton) that additionally reduces the PFC heat-flux by redistributing energy through line-radiation. SOLPS-ITER is also capable of assessing the Helium particle exhaust, the latter a product of the fusion process that takes place in the plasma core.
Driving a fusion plasma is also very dynamic: the core plasma will be likely required to be fuelled from the core with hydrogenic ice pellets (D & T isotopes), and the expel of particles transient ablated from a fuelling pellet and transients in the power fluxes from the core into the edge require capabilities to model the exhaust problem in a time-dependent way. Ultimately, advanced high-fidelity models must be interconnected with dynamic models that will provide the foundation for further analysis of the controllability of the plasma exhaust.
One of the biggest challenges is to get the exact amount of hydrogen gas and noble gasses into the exhaust to cool down the plasma sufficiently without degrading the core plasma where the fusion process takes place. As these gas injection systems are generally slow, slower than the plasma processes that modify the exhaust, prediction is needed to counteract these variations.
Therefore, DIFFER is developing model predictive control for SPARC using core power fluctuation predictions and safety constraints such as melting limits and disruption limits. This work requires both good models of the exhaust, which are partly based on SOLPS-ITER simulations of the exhaust partly being developed at DIFFER, and simulations of the core with other codes.
The JINTRAC integrated code suite combines the plasma core and plasma edge models together, which, in principle, allows whole-device modelling ‘from the wall to the core’. However, SOLPS-ITER simulations at high fidelity by themselves are relatively slow with respect to their numerical speed. DIFFER, in recent years, has gained significant experience in the establishment of fast surrogate models using artificial intelligence techniques in collaboration with other European institutions.
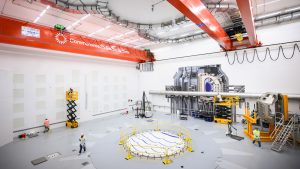
These fast models, which can also be improved to work at higher fidelity, will finally allow for a fast integration at reasonable computing times of the simulation and thus will allow for full-device modelling required for integrated core/edge control techniques within a reasonable timeframe of the project.
Leveraging the numerical expertise, DIFFER will develop a control-oriented framework that can be executed on CFS computing resources. In the framework, the focus will lie on exhaust control, including models, observers, and controllers; DIFFER is going to make state-of-the-art controllers which will effectively decouple the heat flux from the core plasma in the tokamak and the power on the divertor tiles. The project scope is limited to the activities that take place before the start of SPARC plasma operations.
In the future, the scope could be expanded to the demonstration and testing of controllers and models on SPARC.
Relevant topical areas the Dutch research institute will work on:
- Development of both static and dynamic modelling of the exhaust
- Exploiting AI techniques to speed up the numerical capabilities
- Supporting the development of exhaust diagnostic and observer development
- Developing the model predictive control
Implementation
As CFS gets closer and closer to SPARC operation, control system development and campaign planning become increasingly important to the project. Results from plasma heat exhaust simulations and controller tests on simulated plasma parameters will inform the development of the final SPARC control system and will be an important input to plans for early operations. SPARC operations will continually improve understanding of the physics of heat exhaust and will provide the data necessary to improve future modelling and controllers.
For DIFFER, the collaboration with a private company like Commonwealth Fusion Systems underscores DIFFER’s commitment to conduct fundamental research on materials, processes, and systems for a sustainable global energy infrastructure, all in close partnership with (inter)national academia and industry.
Please note, this article will also appear in the 20th edition of our quarterly publication.