Justin Wood, Vice President and Head of Europe, Middle East & Africa of the Alliance to End Plastic Waste, explains why cascade recycling is the best method for creating a circular plastics economy.
Touted for its versatility, durability, convenience, and cost-effectiveness, plastic has now become ubiquitous in contemporary society, used as an essential material in wide-ranging sectors spanning packaging, construction, and healthcare among others. Yet its usage has resulted in 360 million tonnes of plastic waste generated annually, with much of the ensuing waste improperly managed and left unrecycled.
Unmanaged plastic waste poses a significant global environmental challenge, often remaining uncollected, leaking into the environment, or being dumped in landfills.
Key to tackling the plastic waste problem is making the fundamental shift from a linear ‘take-make-dispose’ model to a circular one. Alongside reduction, reuse, and refill strategies, recycling is the engine that will drive the transition to a circular economy, allowing existing materials and products to be kept in circulation and in use to the fullest extent.
Recycling is a process that produces new products or packaging from plastic waste. An optimal recycling system aims to maximise recycling rates, retain the value of materials, and reduce carbon footprint. Among the many different technologies that exist today, recycling is often broadly categorised into mechanical or chemical recycling.
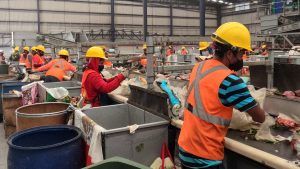
However, no single recycling solution is optimal. Instead, a sequence of multiple technologies is what will get us closer to circularity. Termed ‘cascade recycling’, various technologies and methods are employed – mechanical, chemical, closed-loop, open-loop, downcycling, and upcycling – one after another sequentially to retain materials at the highest level of quality and economic and environmental value for as long as possible.
Closed-loop recycling
Currently, the most established form of recycling, mechanical recycling, is the process by which plastic waste is converted into recyclates without significantly altering the chemical structure of the material. It is by far the most cost-effective, environmentally friendly, and accessible form of recycling, reaping significant environmental benefits as compared to other recycling solutions.
For instance, studies show that by avoiding the production of virgin materials, mechanical recycling saves around 1.4 to 2.1 tonnes of carbon dioxide per tonne of plastic recycled. In addition, under ideal conditions, mechanical recycling can process plastics like PET bottles back into new bottles, and into high-value textiles in certain situations.
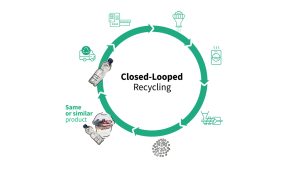
Originally a supply chain concept, a closed loop supply chain aims to reuse or recycle materials in the manufacturing process, thereby reducing or even eliminating waste. Adopting this to a broader context, a closed loop can be taken to mean recycling back to a similar quality as the original material, in which the product is able to be used again in the original or in an equally demanding application.
Despite being the ideal recycling choice, closed-loop recycling has its limitations. The inadequate segregation, collection, and sorting of used plastic can impact the availability of high-quality feedstock. This can be attributed to several factors. For one, waste management still poses a significant challenge – to date, 2.7 billion people still do not have their waste collected, with many less-developed countries often having little to no waste segregation at source or post-collection.
At the same time, the presence of different types of plastics, mixed grades of the same plastic, and organic contamination also compromise the quality of the plastic available. All of these hinder the use of closed-loop recycling, thereby contributing to the insufficient supply of quality feedstock. Some plastics also degrade after each round of the recycling loop and, after three to ten cycles, are no longer fit for purpose.
Open-loop recycling
Where quality is compromised, the used plastic can be mechanically recycled into a lower quality application – a process known as ‘downcycling’ – creating products that do not require the highest grades of plastic, such as garden furniture, basic construction materials, and textiles.
Although not as economically and environmentally effective as closed-loop recycling, the open-loop method still offers economic value and a reduction in carbon footprint in comparison to producing new virgin plastic or sending the plastic to landfills or to waste-to-energy facilities. What makes downcycling a practical option is the long life cycle for these applications, where the carbon that is used to manufacture the product is contained rather than released into the atmosphere for a period of time.
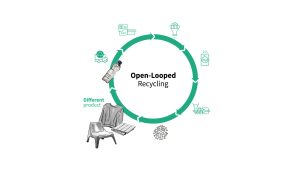
However, much like closed-loop recycling, open-loop recycling still faces scalability issues due to the challenge of finding markets that are large enough to take on all the production, even if feedstock was readily available. In addition, mechanical recycling cannot be carried out indefinitely – that is, once the quality of the plastic deteriorates to the point when the quality of the downcycled product is no longer acceptable.
Chemical recycling
From pyrolysis and gasification to depolymerisation, various chemical recycling technologies are being developed, offering solutions to different recycling challenges. By accepting different streams of clean plastic waste, including degraded plastics, chemical recycling technologies can break down or depolymerise a plastic product back to a raw material. The raw material can then be used to replace fossil feedstock, producing plastic of virgin-like quality – which helps in meeting the need for more demanding applications such as for food or medical use.
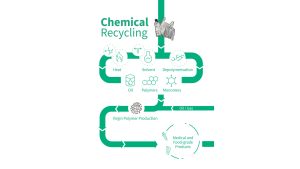
However, chemical recycling typically entails a higher carbon footprint and operating cost than closed-loop or open-loop recycling. Taken in this context, it can be argued that chemical recycling should only be deployed when mechanical recycling options have been exhausted. Therefore, as part of the recycling technology mix, it is important to determine which chemical recycling solutions are the most appropriate choice for different types of plastic waste, ensuring that its overall environmental footprint is commensurate with the gains in material circularity.
Cascade recycling
While the recycling debate is often framed in terms of mechanical versus chemical methods, it is clear that there is no one optimal solution. Instead, a series of complementary recycling technologies should work in tandem to ensure further gains in material circularity, allowing the plastic to be recycled over and over to maintain the quality of the recyclate and to keep the material in circulation for the maximum amount of time possible.
Defined as ‘something arranged or occurring in a series or in a succession of stages so that each stage derives from or acts upon the product of the preceding’, the notion of “cascade recycling” is exactly what a “cascade” is – a series of recycling methods carried out in sequential order. Think of recycling as a cascade of quality and value, where mechanical recycling should be the first option in the cascade. Once all the possibilities for mechanical recycling have been exhausted, then chemical recycling can come in as the final step of the cascade, upcycling the material back to virgin quality.
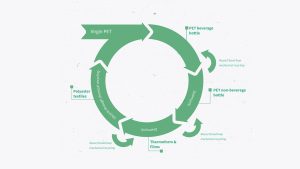
To illustrate how cascade recycling works, let us look at the journey of a PET beverage bottle. Mechanical recycling is well-established and should be utilised as the first step of the cascade to recycle the bottle back to a new beverage bottle as much as possible.
However, each time you mechanically recycle the bottle, the plastic composition gets increasingly mixed and the quality deteriorates. Once the quality is compromised, the plastic can then be downcycled into other products that do not require food or medical-grade quality, such as bottles for household cleaners, food trays, or buckets. Only when all of this is exhausted do we look at chemical recycling methods such as glycolysis or methanolysis to upcycle the material into virgin plastic.
Circularity in action
Today, less than 10% of the world’s plastic waste is recycled. Further investments are still needed to scale recycling capacities in order to create this cascade of closed-loop, open-loop, and chemical recycling. Despite this, solutions to drive this transition already exist and many emerging technologies are being developed at a remarkable pace. With second and third generation technologies, significant improvements will continue to be made – innovative concepts that can increase scale and improve reliability and yields, and the use of heat-integrated design and renewable energy sources are but some of the possibilities.
With the right investment and know-how, cascade recycling is capable of enhancing recycling rates, paving the way for a more circular economy for plastics. Just as a journey of a thousand miles begins with a single step, so too does the path to circularity. As in the cascade recycling process – closed-loop recycling first, then open-loop recycling, and finally chemical recycling – each step takes us closer to achieving circularity.
And then we repeat this cycle – over and over again. This is circularity in action.