Eldert J van Henten, a Professor of Biosystems Engineering at Wageningen University and Research’s Farm Technology Group, speaks to The Innovation Platform about the evolution of agricultural technology – from the hand tools to AI.
The evolution of agricultural technology began some 10,000 years ago. Simple hand tools providing relief at the beginning gradually evolved into the mechanical equipment commonly available to farmers today. Taking a closer look at the body of currently available technology reveals commercially available solutions for roughly every operation in farming that can be easily mechanised – think of the tractors, ploughs, seeders, planters, and harvesters in arable farming we are so used to see on the fields (for the sake of clarity I will denote this kind of equipment as ‘low-tech mechanisation’).
Though stacked with many ingenious bits and pieces based on very clever engineering, low-tech mechanisation replaces and supports a human being or human activity only in relatively simple tasks and does not have much flexibility with respect to the task, the objects it has to handle, and the working environment in which the machine operates. Commonly, this kind of technology is largely based on mechanical engineering solutions and does not contain much electronics, sensors, or software, nor, if you will, ‘intelligence’.
The tractor very successfully replaced the horse, ox, and even the human in terms of on- and off-field mobility and muscle power, but it does not have a clue about what operation to perform on the field, where to do it, and how to do it. When it comes to supervision of the operation and maintaining safety, a human operator (that is, the farmer or one of her employees) is still in charge. Of course, a wide range of implements have been adopted to be connected to the tractor and to perform the tasks crucial to crop production. Yet again, the flexibility of these implements is limited, and their operation has for a long time now been aimed at a full field ‘one size fits all’ approach.
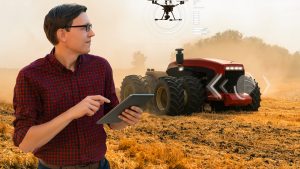
From low- to high-tech
Agriculture currently goes through a transition from low-tech mechanisation to high-tech mechanisation. ‘High-tech mechanisation’, in my definition, is more flexible with respect to the natural variation in the objects it has to handle and the working environment in which the machine operates, is flexible with respect to the task(s) to perform, and is able to switch from one task to another. To achieve that performance, this technology uses sensors and concepts like sensor fusion, it contains a considerable amount of software-based ‘Artificial Intelligence’ and is based on a mix of mechanics and electronics, or so-called ‘mechatronics’ or robotics.
Where low-tech mechanisation mainly replaced or supported the mechanical functionalities of the human, high-tech mechanisation aims to support or replace human functionalities and capabilities like sensing, cognition, decision making, and effective eye-hand co-ordination to perform an operation more precise (think of precision agriculture operations) or to perform the more complex agricultural operations such as selective harvesting. Though the advent of this kind of technology in agriculture has been predicted for more than half a century, relatively recent progress in sensor technology, computer vision, cost effective computing power, and artificial intelligence were required to facilitate the considerable progress we see in this field today.
The evolution of robotic agricultural technology
The milking robot is the first successful implementation and practical adoption of robotic technology in agriculture. Started as a research challenge in the early 1980s, the robotic milking parlour is a commonly used technology in agricultural practice today.1-3 Complementing the technology package available to this domain in livestock farming are autonomous barn cleaning robots and feed dispensers.1 In poultry production, robotic floor egg collection has been addressed in research to deal with floor eggs when switching from the cage systems to loose housing systems for laying hens.4
Providing a glimpse at what the future of arable farming might look like is the research project ‘Hands free hectare’ at Harper Adams in the UK. For instance, the project’s website shows ‘Automated machines growing the first arable crop remotely, without operators in the driving seats or agronomists on the ground.5
Autonomous tractors
Fully replacing human capabilities in all aspects of arable farming is still quite challenging. Yet, advanced technology to support the farmer is already there. GPS-based autosteer systems for tractors support human labour in one aspect of tractor driving. This technology has been embraced by agricultural practice in the past two decades for reasons of efficiency of operation and reduction of fuel costs. Fully autonomous tractors or robots are on the drawing tables of both research and industry for quite some time already, but safety and liability concerns hamper progress in that domain. It is expected that developments in the field of autonomous car driving facilitate developments in agricultural robotics as well.
A tractor-pulled implement for computer vision-based precision weeding constitutes a partially autonomous solution. The breakthrough in camera vision and Artificial Intelligence, specifically Deep Learning, techniques, offers promising results in the detection of weeds amongst cash crops. This technology is currently entering agricultural practice.6,7
Building on the same advances in technology, sensors map fields, arable crops, or fruit tree crops, demonstrating the variability in fields and crops and by doing so support farmers in their decision making process within the precision agriculture paradigm. These sensor platforms are carried either by small mobile robots or drones. Companies offer services to collect these images, analyse the obtained data, and offer decision support-based on these images.8,9 It is worth noting that when using these technologies, the farmer still plays a crucial role in the operational management of the farm. Similar sensor-based technologies are currently being adopted at the global scale for the plant breeding industry. Faster and more consistent and objective identification of plant breeds are key drivers for using these technologies.10,11 The selective harvesting of broccoli tackled in a parallel project in the Netherlands and the USA is yet another example of ongoing research in open field crop production.
Autonomous harvesting
In greenhouse horticulture much attention has been paid to autonomous fruit harvesting.12 This still proves to be a big challenge due to the poorly-structured environment, fruits being occluded by leaves and stems, the significant natural variation amongst plants and fruits, and the poor lighting conditions in the greenhouse. In contrast, building on an R&D track of some 15 years, a robot to remove leaves from tomato in a high-wire cultivation growing system is currently close to market as we speak and very similar to the ‘Hands free hectare’, AI capabilities are successfully being tested in the autonomous greenhouse challenge.13,14
Fruit tree cultivation is facing similar challenges as fruit crop production in greenhouses. Autonomous harvesting has been on the research agenda for a long time. Solving this challenging problem key to the evolution of agricultural technology. In the meantime, farmers have adopted a solution in which workers are supported and transported by an autonomous mobile platform. Not having to move and climb ladders has improved work efficiency considerably, and there might come a time when for harvesting advanced skills of the human worker are also replaced by robotic technology.
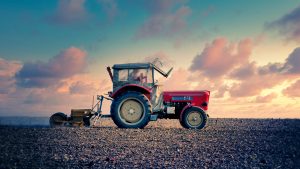
The challenge of technology adoption
Developing robotic technology is one thing, but adoption in agricultural practice is a different matter entirely. First, it seems the technology ecosystem is changing. With strong skills in robotics and AI, a different kind of company is entering the agricultural technology market.7 Secondly, matching technology to the needs of the farmers and training farmers in the use of more high tech equipment are crucial critical success factors for the adoption of robotic technology. Thirdly, being very data intensive, embedding robotic technology in the data infrastructure of the future farm is a challenge on its own. Clearly, robots will become a part of the IoT framework in farming. Data ownership and privacy need to be addressed. The same holds for topics like safety and liability. European projects like the Internet of Farming – IoF202015 and AgRoboFood16 aim to embed these novel technologies into the agrifood sector. Yet, technology adoption is not a farmer’s concern only. In the mind of consumers, the relation between food and technology is a sensitive matter. Ethical issues of high-tech in that respect require our attention.17
The drivers of development
What then drives the development of high-tech mechanisation and agricultural robotics? A commonly heard statement is that the application of robotics in farming is detrimental to the farming industry and takes us away from the true origins of farming. But what exactly is the true origin of farming? Is farming in its original basic shape able to provide a growing population with food, fibres, and fuels? Certainly, efficiency and cost reduction have been relentless drivers for technical innovation. But there is more. There have been times that mechanisation pushed human labour out of agriculture. Today, the situation seems different. In the European Union, the pool of young farmers is declining. When economies develop, the agricultural workforce declines. ‘Young people and people with higher education levels are more likely to be employed in non-agricultural sectors, in particular services.’18 Yet, to youngsters who grew up with computer games and smartphones, high-tech agriculture might become appealing again.
Besides efficiency and cost reduction, the reduction of the use of crop protection chemicals and the reduction of emissions to the environment provide another focus point for this technology. So far, it seems technology has played the role of problem solver. But there is another way of looking at technology and high-tech mechanisation in agriculture: in current agriculture, the scale and size of machinery demands large scale farming and monocultures, a quite unsustainable combination. Robotic technology offers the opportunity to down-scale technology and provide small-sized modular systems to farmers. Small scale machines will reduce soil compaction.19 Downscaling also offers the opportunity to re-think agricultural production, as it might unlock intercropping or even pixel-farming as a more sustainable approach to farming in the future.20
References
- lely.com
- gea.com
- fullwoodpacko.com
- https://www.wur.nl/en/show/Poultry-bot-for-floor-egg-collection.htm
- handsfreehectare.org
- https://www.steketee.com
- http://www.bluerivertechnology.com
- https://bioscope.nl
- https://www.precisionhawk.com/agriculture/technology
- https://emphasis.plant-phenotyping.eu
- https://www.plant-phenotyping.org
- http://www.sweeper-robot.eu
- https://www.priva.com/discover-priva/stay-informed/news/priva-kompano-deleaf-line
- http://www.autonomousgreenhouses.com
- https://www.iof2020.eu
- https://www.agrobofood.eu
- https://www.europarl.europa.eu/RegData/etudes/STUD/2016/563501/EPRS_STU%282016%29563501_EN.pdf
- https://www.europarl.europa.eu/RegData/etudes/STUD/2019/629209/IPOL_STU(2019)629209_EN.pdf
- https://www.smaragd-smartfarming.nl/en
- https://www.wur.nl/en/project/Pixel-cropping.htm
Professor Dr Ir Eldert J van Henten
Professor of Biosystems Engineering
Farm Technology Group
Wageningen University and Research
+31 317 48 33 28
eldert.vanhenten@wur.nl
Tweet @eldertvanhenten
www.wur.nl/en/Research-Results/Chair-groups/Plant-Sciences/Farm-Technology-Group.htm
Please note, this article will also appear in the second edition of our new quarterly publication.