Dr Carlos Ziebert, head of IAM-AWP’s Calorimeter Center, KIT, explains how battery calorimeters can help researchers enhance the lifetime and safety of batteries.
Established in 2011, the IAM-AWP Calorimeter Center currently operates Europe’s largest Battery Calorimeter Laboratory. It provides six Accelerating Rate Calorimeters (ARCs) of different sizes – from coin to large pouch or prismatic automotive format – which allow the evaluation of thermodynamic, thermal, and safety data for lithium-ion (Li) and post-Li cells on material, cell and pack level under quasiadiabatic and isoperibolic environments for both normal and abuse conditions (thermal, electrical, mechanical). These data can be used on all levels of the value chain – from the safe materials design up to the optimisation of thermal management and safety systems.
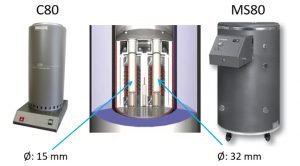
On the materials level, differential scanning calorimeters (DSC), laser flash analysers (LFA), and an extremely sensible Setaram C80 Tian-Calvet calorimeter (Fig. 1, left) provide thermodynamic parameters such as heat capacity, thermal conductivity, or formation enthalpy. In the larger Setaram MS80 Tian-Calvet calorimeter (Fig. 1, right) cylindrical cells up to 21700 format fit inside and their heat generation during cycling can be determined with great accuracy by direct heat flow measurement. The heat flow is determined by the 3D Tian-Calvet Sensor arrangement, where both the sample and the reference vessel are surrounded by rings with hundreds of thermocouples (Fig. 1, centre).
These studies are especially important for post-Li cells, which make use of more abundant materials such as sodium or magnesium instead of Li, nickel (Ni), and Cobalt (Co). These materials focused on by the POLiS (Post Lithium Storage) Cluster of Excellence, which was jointly acquired in late 2018 by KIT and Ulm University. In this cluster, the IAM-AWP Calorimeter Center is responsible for the thermal characterisation and safety testing, both of which must now be conducted on the smaller scale level and need to be continued to ensure that the cells can be safely up-scaled.
Check out our page on battery calorimeters to learn more about the safety and thermal management of energy storage.
Thermal Management and safety
It is clear that safety issues have a major influence on consumers’ willingness to adopt the current Li-ion battery technology because an uncontrollable temperature increase (so-called ‘thermal runaway’) can cause an ignition or even explosion of the battery with simultaneous a release of toxic gases. Thus, thermal management and safety are of utmost importance for the electrification of transport and stationary storage. The six robust Accelerating Rate Calorimeters (ARCs, Thermal Hazard Technology) can bring advancements for the thermal management, lifetime, and safety of batteries.
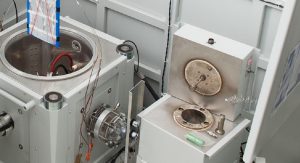
For studies on heat generation and dissipation during charging and discharging, the batteries are coupled to battery cyclers. Isoperibolic or quasiadiabatic ambient conditions are adjusted by heaters and thermocouples located in the lid, bottom, and sidewalls of the calorimeter chamber, in which the cell is inserted (Fig. 2).
‘Isoperibolic’ means that the temperature of the calorimeter chamber is kept constant and the temperature change at the surface of the cell is measured. In this case, the cell temperature reaches its initial temperature again after each cycle.
In the quasiadiabatic mode, the heaters in the calorimeter chamber immediately follow any change of the cell temperature, thereby preventing the heat transfer to the chamber. This simulates ambient conditions for a cell in a pack, where the densely packed neighbouring cells prevent, or at least greatly reduce, the heat release to the environment. Such conditions lead to a continuous increase of the cell temperature with every cycle.
For application in the thermal management system, the measured temperature data are converted into generated and dissipated heat data by determination of specific heat capacity and heat transfer coefficient. For a deeper scientific understanding of various reaction mechanisms, the following special electrochemical and thermodynamic analyses can be performed:
- The identification of the reversible heat contributions associated with the entropy of the cell reaction
- The quantification of the irreversible heat contributions from the internal resistance of the cell
- The analysis of the contributions from side reactions
Ageing studies
The lifetime was studied by performing calendaric and cyclic ageing tests and characterising the cells with respect to changes in heat generation and temperature profile. First, fresh cells were stored at different temperatures in temperature chambers and then characterised at fixed time intervals in order to investigate the influence of this storage (calendar ageing) on cell performance. Secondly, cells were aged at a constant charging/discharging rate in temperature chambers (cyclic ageing).
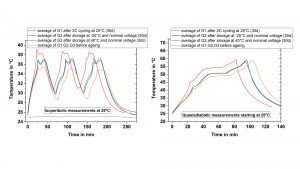
Figure 3 compares the temperature curves measured in the ARC between the cells in fresh condition and after cyclic (G1) or calendaric (G2, G3) ageing under isoperibolic conditions (Fig. 3, a) or adiabatic conditions (Fig. 3, b). Under both conditions, cyclic ageing leads to the largest changes, which manifests under isoperibolic conditions in the form of an increase in the maximum temperature by 4°C and under adiabatic conditions by earlier reaching the maximum permitted operating temperature of 60°C.
Calendar ageing also leads to the same effects. However, regardless of the storage temperature; the increase in the maximum temperature is only 1.5°C. In addition, cyclic ageing also changes the curve shape, which is a further indicator for the ageing status or history. Thus, recording the temperature profile serves as a ‘fingerprint’ for the state-of-health (SOH) and as fast and reliable method for the characterisation of ageing processes.
Once the cells have reached their termination criterion, the reversible and irreversible heat are measured using entropy measurement and electrochemical impedance spectroscopy (EIS). This data can be used for the parameterisation of impedance-based electrical equivalent circuit models (EECMs) and ageing models. In addition, some cells are analysed post-mortem – i.e. disassembled in an inert gas atmosphere – and the changes in the chemical composition, the morphology, and the structure of the electrodes are determined.
Want to learn more about the Karlsruhe Institute of Technology’s Calorimeter Center? Click here to view their partner profile page.
Safety studies
Moreover, the safety of fresh cells and the influence of ageing on the hazard potential can be quantitatively determined by performing the following three types of safety tests in the ARCs:
Electrical abuse: external/internal short circuit test, overcharge test, overdischarge test
In the ARC, temperature increases from the application of an external short circuit or during an internal short circuit (which might be caused, for example, by a production fault) can be measured. The cell can also be overcharged or overdischarged, leading to different failure modes.
Mechanical abuse: nail test
In the ARCs, a mechanical system allows a nail to be pushed into the cell. This provides not only a pass/fail type test to qualify cells, but also quantitative data.
Thermal abuse: heat-wait-seek test, ramp heating test, thermal propagation test
The Heat-Wait-Seek (HWS) test in the ARC starts with the heating up of the sample in small steps, with the system ‘waiting’ at the end of each step to see whether the cell generates heat that leads to a measurable temperature increase (‘search’ step). As soon as self-heating of the cell is detected, the system switches to a quasiadiabatic mode so that the heaters in the calorimeter chamber immediately follow any change in the cell’s temperature, so preventing the heat transfer to the chamber. Thus, the cell is increasingly heating up until a thermal runaway occurs or the chemicals for this exothermal reaction are completely consumed. For the Ramp Heating test, which mimics a Hot Box test, the cells are heated up at a constant rate instead of a stepwise heating of the cells as in the HWS test.
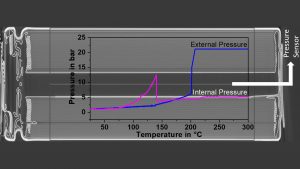
Pressure measurement
In addition, innovative methods for the measurement of external and internal cell pressures during thermal abuse have recently been established on 18650 cells. The external pressure was measured utilising a gas-tight cylinder inside the calorimeter chamber in order to detect the venting of the cells, as can be seen in the blue curve in Fig. 4. For internal pressure measurements, first an x-ray tomography image was recorded to find a suitable place. Then, a pressure line connected to a pressure transducer was directly inserted into the cell and the pressure was recorded during a thermal abuse test, as can be seen in Fig. 4 in the curve coloured in magenta. This plot clearly shows that the cell goes into thermal runaway even if the safety vent opens at a pressure of around 12 bar and releases gases leading to a pressure drop. Thus, the measurement of the internal pressure could be used for the early prediction of processes leading to thermal runaway. This method has been adapted from cylindrical cells to pouch cells and prismatic automotive cells.
Moreover, the calorimeters allow for the study of the thermal runaway propagation in small battery packs in order to develop and qualify suitable countermeasures, such as heat protection barriers.
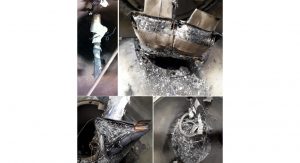
Venting gases
In the different safety studies, self-heating, thermal stability, and thermal runaway are characterised and the critical parameters and their thresholds for safe cell operation determined. Another important issue is the venting gases, which can be collected during the abuse tests and analysed ex-situ. Gas chromatography (GC) method with two detectors, mass spectrometry (MS) and thermal conductivity detector (TCD), are available to detect and quantify the gases. Knowledge of the gas composition under the various cell abuse scenarios reveals the relevant decomposition paths and gives an idea of which protective measures are necessary, e.g. to delay or prevent the cell fire caused by ignition of vent gases or thermal runaway.
Since the establishment of the IAM-AWP Calorimeter Center, more than 200 safety tests have been carried out, from coin cell size to cylindrical cells to pouch and large prismatic automotive cells (Fig. 5).
To summarise: battery calorimetry is an innovative approach to provide quantitative and system-relevant data for the temperature, heat, and pressure development of materials and cells as fast feedback for cell development and input data for simulations.
Learn more about increasing the lifetime and safety of batteries with the Calorimeter Center’s latest eBook.
Dr Carlos Ziebert
Leader of Group Batteries – Calorimetry and Safety
Head of the Calorimeter Center
Institute of Applied Materials
Applied Materials Physics
Karlsruhe Institute of Technology
+ 49 721 608 22919
carlos.ziebert@kit.edu
www.iam.kit.edu/awp/english
Please note, this article will also appear in the second edition of our new quarterly publication.