Dr John L Burba, CEO of International Battery Metals Inc, highlights the need to focus on the environmental impact of spodumene mining and the wider lithium production industry.
As the world shifts away from a hydrocarbon economy to one based on renewables, critical battery metals, particularly lithium, are being catapulted into the hottest resource play that we are likely to see in our lifetimes. The explosion of electric vehicles on our highways is an example of this.
However, as renewable energy and lithium take the place of oil production, we must reconsider the extractive technologies that have been the mainstay of the lithium industry since the 1940s. Unlike the early years of oil production, when crude oil was pumped into open earthen pits, with the brine that was produced and the mud from waste drilling being released to flow into rivers and the ocean, our fledgling industry must utilise superior extraction and processing technologies from the start.
We must all agree that squandering resources because of inefficient extraction techniques; wasting water; polluting streams; leaving chemical waste pits, tailings ponds, and salt piles; and disenfranchising indigenous peoples are all completely unacceptable.
Over the last several years, a number of articles have been written on the production of lithium from brine resources, particularly in Chile. These articles have focused on dreadfully poor recovery efficiencies, groundwater depletion, and the impacts on local indigenous people. All these issues are real and must be addressed. However, very little attention has been placed on lithium extraction from spodumene and other lithium containing pegmatites.
The environmental impact of spodumene mining
In essence, spodumene mines and processors, who today are producing most of the lithium carbonate and hydroxide in the industry, have been given a giant environmental pass. In fact, there is very little published information concerning the environmental impact of spodumene mining and processing. This is largely because the majority of the world’s spodumene production is exported to China for processing and the production of lithium carbonate and lithium hydroxide. As a result, the environmental impacts are essentially invisible to the rest of the world.
To understand issues associated with spodumene mining and processing, we need to begin with the mineral itself. Spodumene is a lithium aluminosilicate mineral, LiAl(SiO3)2, that occurs in granitic pegmatites. Large quantities of spodumene have been found in Africa, Australia, and North America. Today, Australian spodumene ore represents the highest grade with Li2O concentrations of around 4% at the Greenbushes mine. African ore bodies are quite large, but typically only have about 1.6% Li2O. Spodumene ores in North America typically fall between about 0.6% to about 1.2% Li2O.
Ore grade and the rock matrix that the spodumene is associated with have a huge impact on mining processes, lithium extraction, purification, and the corresponding GHG emissions, mine, and chemical waste. For instance, for a given amount of lithium product production, an ore with 4% Li2O requires much less mining and beneficiation than one that is only 0.8% Li2O. There will also be correspondingly lower GHG emissions and mine waste.
When we evaluate the environmental impacts of a mining and refining project, we must break the operation into parts. As stated above, spodumene mining, separation, and the refining processes are very resource specific. The process described in this article is general in nature. It does not represent any specific operation. However, it does illustrate typical processes that one might find in most operations. It should also be noted that several companies have announced improved spodumene processes. The author cannot comment on these due to lack of public information. Hopefully, these companies will bring much needed environmental improvements to this portion of the lithium industry.
Mining and the processing of spodumene to lithium products requires several operational blocks, described in the table, above.
Mining
Spodumene mining is typically an open pit process. These are classical mining processes that require overburden removal, blasting, and removal of ore with large mining equipment. Correspondingly, large ‘overburden’ and rock piles are closely associated with the mining site.
Beneficiation
Once the ore has been removed from the pit, it is graded, crushed, and blended to produce a constant feed concentration for the operation. The next step is to concentrate spodumene. This step is called beneficiation. In low grade operations, the ore will be ground in a ball mill and processed through a multi-stage counter-current flotation process. Here, the gangue is separated from the spodumene mineral. The gangue waste flows into a tailings pond.
Tailings ponds are problematic but necessary. The tailings slurry from the beneficiation process will contain a number of chemicals that are used to selectively separate the spodumene from the gangue minerals. These chemicals progress through the process into the tailings pond.
Today, environmental agencies in most industrial countries require lined ponds. Typically, the lining materials are thick high strength polymer systems. The lining is designed to minimise the movement of mine water and waste into local soils and ground water. However, the old adage that all ponds leak is actually true. Invariably, chemical wastes will be found in local ground water.
Roasting
After the spodumene is beneficiated, it moves to a dryer and a kiln that will operate at about 1,000°C. This is necessary to convert the spodumene to a form that can be easily extracted with acid.
Hot Leaching
The hot ore is typically leached with sulphuric acid at about 250°C. Approximately 60-80% of the lithium is solubilised at this step. Solids are filtered and transported to the tailings pond.
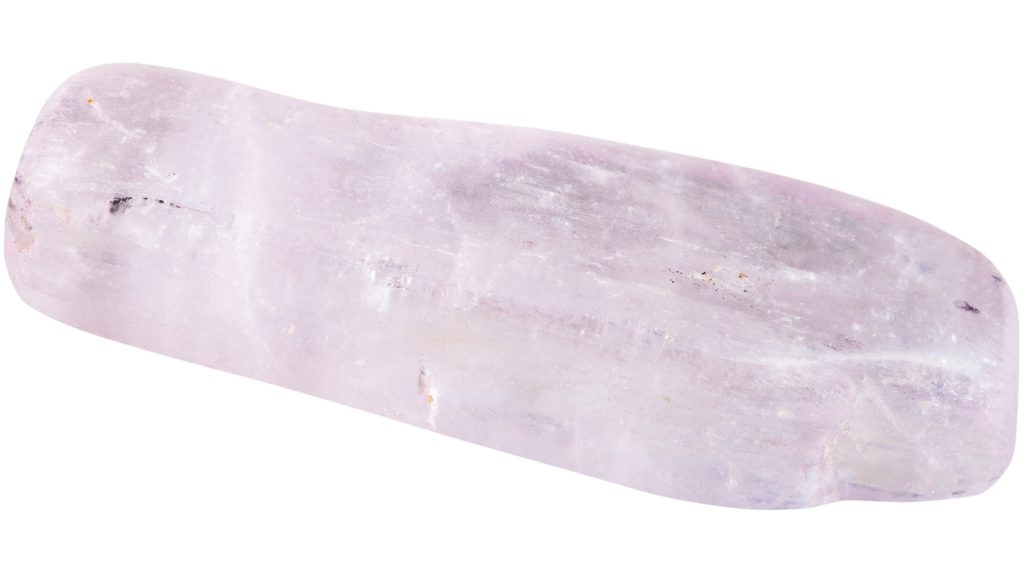
Purification
The acidic lithium sulphate solution is treated with lime which neutralises the excess sulphuric acid by producing gypsum. Gypsum waste may end up in the tailings pond. However, some operations may be required by local regulators to isolate it in separately permitted ponds.
After the separation of gypsum, the lithium sulphate can then be further processed to remove other metal impurities such as calcium, magnesium, iron, etc. This process will likely utilise ion exchange or solvent extraction techniques. By definition, purification processes produce waste streams that contain various waste chemicals, including salts, surfactants, organic extractants, and solvents from the solvent extraction circuits. The waste products must go to some sort of impoundment, such as a wastewater pond or the tailings pond.
The key thing to note is that in each of these steps, while the pollutants have been separated from the product stream, they still exist. They do not magically disappear. Dealing with them can be very expensive. Therefore, there is always a financial incentive to discharge wastewater from the facility.
Product production
At this point, the purified lithium sulphate can be converted to either lithium carbonate or lithium hydroxide by the addition of either soda ash or lime, respectively. In these steps, sodium sulphate or gypsum is the respective by-product. These wastes must also be dealt with, most likely in a pond.
Final Purification
Additional purification steps are necessary to meet ‘battery grade’ standards. All waste streams from these purification steps will ultimately end up in waste ponds or lagoons. The products will then be filtered, dried, and packaged. Wastewater from the filtration system will be either purified and recycled or go to one of the waste ponds.
There is a painful theme to this story. Each step in spodumene processing to battery grade products requires a lot of energy and produces copious amounts of GHG. Post mining and crushing, all of the remaining steps require significant additional chemical input. The formula is simple: more mining and processing steps equal more energy, more GHG, more chemicals, and more chemical waste. This leads to more inevitable air, ground, and surface water pollution.
The key message of this discussion is that if lithium is going to be a mainstay of our global economy, we must be focused on the environmental impact of our lithium production industry, which is now in its infancy.
The author applauds the recent attention that has been placed on lithium from brine operations. Clearly, changes in this segment of our industry must take place. We believe that International Battery Metals will play a very large part in the necessary improvements. However, we must also pay attention to environmental impacts of the entire lithium extraction industry. This article has focused on spodumene processing. However, we must also focus on lithium extraction from clays and other emerging lithium resources.
Please note, this article will also appear in the seventh edition of our quarterly publication.