Dr James Edmonson and Dr Alex Holland, Senior Technology Analysts at IDTechEx, examine EV battery cell and pack trends, including the varying battery material demands.
2021 is cementing the electric car’s dominant position in the auto industry’s future as OEMs have increased electrification targets, announced more battery-electric models, and planned new technology adoption strategies.
The lithium-ion batteries in electric vehicles (EVs) present very different material demands at the cell and pack level compared with the internal combustion engine (ICE) vehicles they replace. Whilst ICE drivetrains heavily rely on aluminium and steel alloys, Li-ion batteries utilise many materials such as nickel, cobalt, lithium, copper and much more at a cell and pack level. The markets for these materials will see a rapid increase in demand that would not have been present without the take-off of electric vehicle markets.
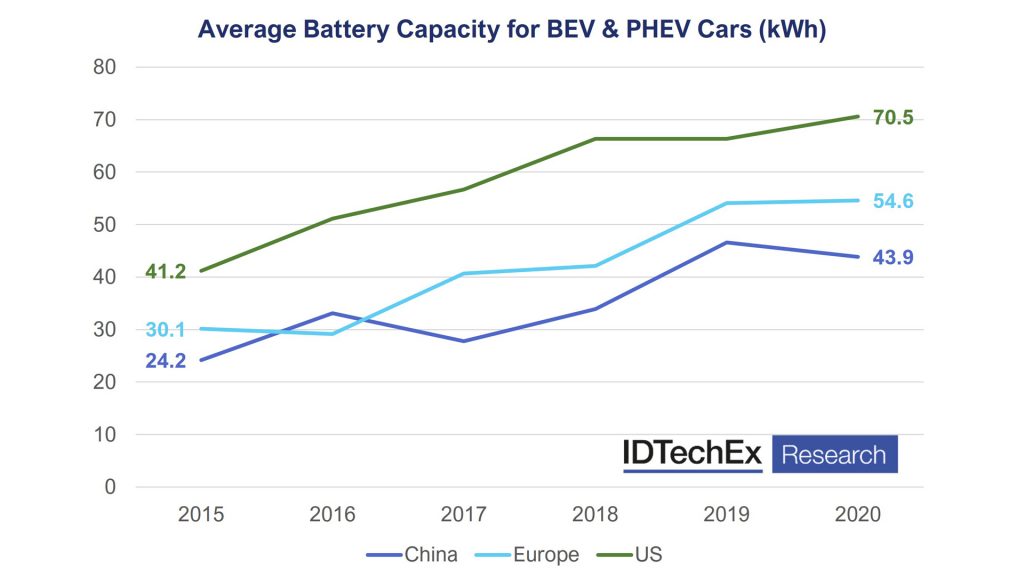
Growing battery sizes and critical battery material demands
When considering the more critical materials in an EV battery, this is tied closely to the battery pack’s capacity. Therefore it is essential to understand the trends in the industry regarding capacity. Between 2015 and 2020, the average battery capacity for plug-in cars rose by 64%, and IDTechEx expects it to continue growing (albeit not at the same rate) throughout the next decade. With the growing battery capacity per vehicle and overall huge sales increase in electric cars, we expect a 21.8-fold increase in battery demand in 2031 compared to 2020. According to IDTechEx’s research, this increase will drive demand for lithium in EVs to 14 times its 2020 value in 2031.
Lithium is not the only critical material; the material demands vary significantly depending on the cathode chemistry and anode used. The popular cathode choices include nickel manganese cobalt (NMC), nickel cobalt aluminium (NCA) and lithium iron phosphate (LFP). Graphite is the standard choice for the anode, but adopting smaller weight percentages of silicon is common, and silicon dominant anodes are an option in the future. Despite the different options and trends around alternative chemistries, we are still expecting a significant increase in demand for all of these materials, thanks to the rapidly growing EV market. As the market scales, it is essential to consider the supply chain for these materials, not just from a total demand standpoint but also from a diversity aspect.
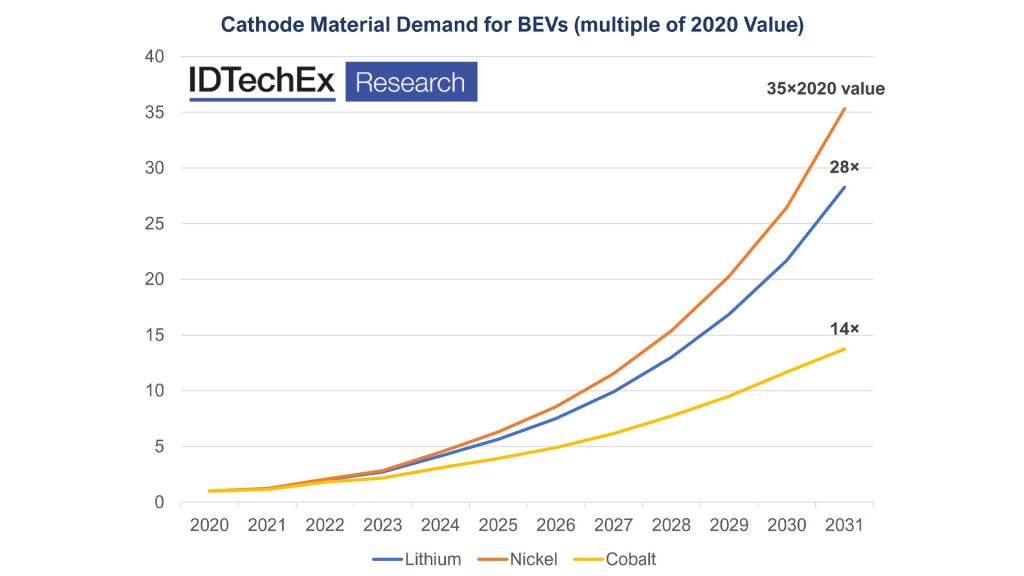
The supply chain concerns
There are almost always environmental and sustainability concerns with any form of material extraction. The topic is more important for Li-ion batteries and EVs because they are a vital component of a green economy. So their environmental and sustainability credentials rightly take on added significance. We think there is recognition in the industry that environmental and social impacts need to be carefully considered and accounted for. For example, there are attempts in the industry to improve supply chain transparency for cobalt. The European Commission has proposed a regulation that could impose a maximum lifecycle carbon footprint for batteries and recycling requirements.
The supply chain for most raw materials used in batteries is now reasonably well distributed globally, except for cobalt. Cobalt is primarily mined in the Democratic Republic of the Congo, with a significant portion still mined by artisanal and small-scale mining operations. Historically, many human rights groups have documented issues in these operations. However, you cannot remove these smaller-scale operations as they are vital to the DRC’s economy. Some companies are starting to take greater responsibility here, implementing more regulations on their practices, but diversifying cobalt supply may become critical with the growing demand.
Battery recycling, in general, has seen a lot of investment and activity and has become a much more widely discussed topic over the past one to two years across the industry. Investment is ongoing as a means to try and mitigate supply chain concerns, though given forecast growth for demand, recycling alone will not be able to meet the material demand.
Global deposits of lithium, nickel, manganese, graphite and even cobalt are likely sufficient to meet long-term demand. The issue comes from getting the material out of the ground fast enough. Here, more investment is needed to expand mining and processing capacity to avoid material supply bottlenecks.
Potentially more of a concern than the raw material mining diversity is processing these materials for batteries. This predominately takes place in China. Historically, we have seen China restrict the export of certain materials (like neodymium used in electric motors), causing massive price rises and uncertainty in supply. Diversification and scaling up of raw material processing are required globally to ensure future reliability and resiliency of the supply chain.
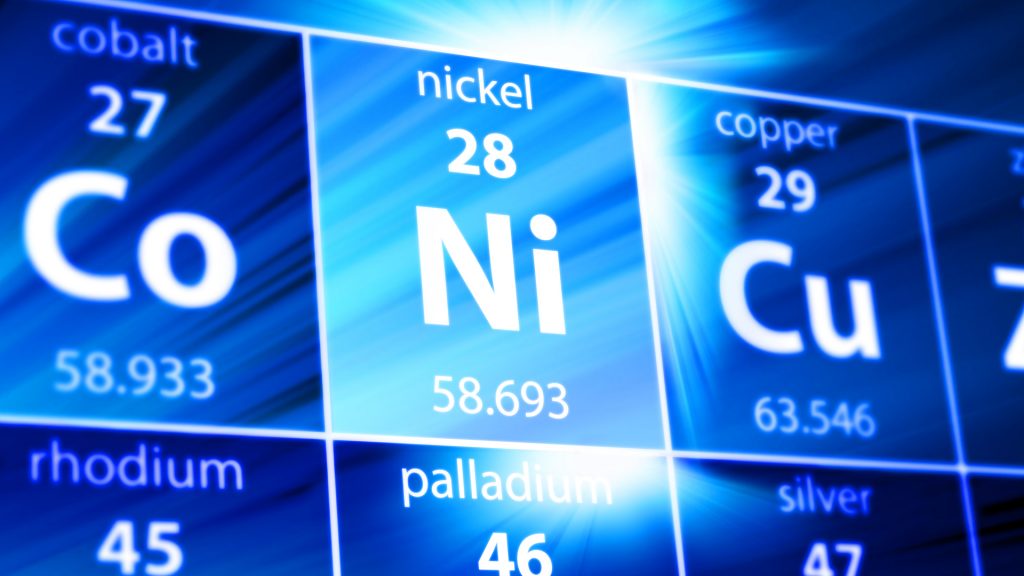
How battery design is changing, and the impact this will have
The EV market has a lot of activity to reduce reliance on the most problematic or costly materials, including cobalt and nickel, by moving towards high nickel layered oxides or high-manganese content cathodes. There has also been a lot of recent activity around LFP, and CATL’s (Contemporary Amperex Technology Co., Ltd.) summer announcement re-ignited interest in Na-ion. These battery technologies can help alleviate potential supply bottlenecks by replacing NMC/NCA type Li-ion in less demanding applications, i.e., energy density can be sacrificed to some extent.
Battery designs continue to evolve at a cell and pack level to improve energy density and simplify battery assembly. The industry is trending towards larger form factor cells such as the 4680 announced by Tesla, the Blade LFP cells deployed by BYD, or the larger pouch cells from LG Chem to be used in GM’s Ultium platform. By increasing the size of individual cells, the proportion of the ‘inactive’ cell (e.g. separators, current collectors etc.) is reduced. This does not directly reduce the amount of cathode materials like nickel and cobalt. Still, less overall material will be required to give the same total battery capacity with improved energy density. A manufacturer could opt for less material for the same capacity or increase the overall capacity to further range. Even with these improvements, the total amount of cathode and anode materials will remain broadly similar, and hence the overall market growth will continue to drive increased demands.
Another design trend (typically combined with larger form factor cells) is the adoption of cell-to-pack batteries and further integration of the battery pack with the vehicle’s structure. Once again, this improves energy density and aids in the ease of construction by removing the casings and housing used around individual modules. However, typically these designs become more challenging to recycle, and one example of this would be considering the thermal materials used.
Whilst a reworkable gap filler may hold the cells in place within bolted modules in the past, with a cell-to-pack design, more adhesives are used which are not reworkable or serviceable, leading to a more complicated disassembly. Second life applications may be preferable here, and given the ramp-up material demand, recycling alone would not be sufficient to supply the market anyway. While automakers are starting to think more about what to do with EV batteries at the end of their life, few vehicles have reached this point yet. Hence, we are yet to see the full repercussions of a rapidly growing supply of end-of-life EV batteries.
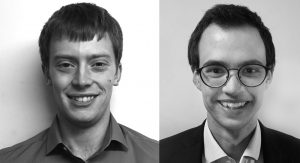
Dr James Edmonson and Dr Alex Holland
IDTechEx
research@IDTechEx.com
www.IDTechEx.com
https://www.linkedin.com/company/idtechex/
https://www.facebook.com/IDTechExResearch/
Please note, this article will also appear in the eighth edition of our quarterly publication.