Steve Allin, Founder of the International Hemp Building Association (IHBA), speaks to The Innovation Platform about the challenges of establishing a sustainable hemp building industry, as well as some of the benefits of using hemp as a building material.
The International Hemp Building Association (IHBA) aims to develop, promote, and support the production and use of all sustainable hemp based construction materials and their by-products in a sustainable and bio-regional manner for the benefit of the ecology and communities of all regions of the world. It also aims to work for the gathering and dissemination of knowledge about the materials and systems from those developing and using them to those wishing to. The IHBA will assist members developing systems both from the point of view of production of the materials to their use in vernacular and new styles of architecture appropriate to their region. The association is also designed to work to educate and inform the relative government and trade bodies to help in the establishment of the infrastructure necessary to create a hemp building industry throughout the international community. At all times, the IHBA works to ensure that the use of such materials has the least environmental impact possible.
The Innovation Platform spoke with the IHBA’s founder, Steve Allin, about why the establishment of a hemp building industry is important and, moreover, some of the hurdles which must be overcome if this is to be made a reality.
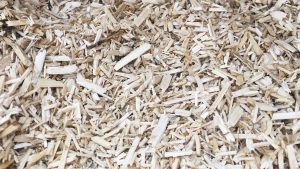
What are the main benefits of using sustainable hemp as a building material? What are hemp’s main strengths?
Hempcrete can be used in any building, from a warehouse to a home. All of these buildings use energy, and if we can reduce that energy (both in terms of the amount of energy being used in its construction but also in terms of the energy used within it during its lifetime), then we are obviously on the right track, and hempcrete can do that. Furthermore, if we can produce the materials used to construct houses in a more ecological way, perhaps even in a carbon negative way, then that is even better. And, again, this is where hempcrete can play a role.
A final point is that it is important to strengthen the resilience of communities, to create a working relationship between farmers, builders, and homeowners through the development of a localised building industry with hemp at its core.
The fibres from the outside of the hemp stem can be used to make insulation, but it is the woody core that is primarily used to create hempcrete – which can be a little confusing in as much as it is not a replacement for concrete. Hempcrete is used to create an envelope around a structure, and the structure can be made from anything: concrete, steel, timber, and so on. It can also be produced in various densities to provide more or less insulation, to make it lighter, or to increase load bearing capacity.
The hemp woodchip called ‘hurds’, from the core of the plant, are combined with lime to make the hempcrete, but clay and other additives and combinations are also being used around the world with materials and ingredients which are more geographically and geologically suitable. This is an important point: the typical housebuilding materials industry is monopolised by big businesses which operate form huge centralised production and manufacturing bases and therefore take a one-size-fits- all approach. This results in off the shelf products which are almost carbon copies of one another regardless of location. Rather than being a mirror of this, hempcrete is a material which lends itself to being very much localised. That is, it can be grown and processed locally, sold to local builders, and used in buildings that are developed to work in that particular environment. In many ways, hempcrete offers the prospect of returning to many of the aspects of construction which have been lost in the last two or three decades in favour of importing new technologies.
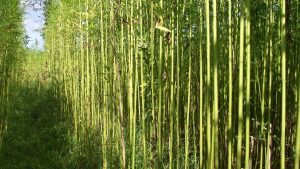
For a country to establish a hemp building industry, the infrastructure needs to be in place. What does this consist of? Are there any countries who have already achieved this and who could export best practice?
The industry needs significant investment for this to happen. However, it needs to be understood that any investment in this area is going to be long term – there will be no immediate, or even short-term, return on investment. Furthermore, and this can perhaps tie into certain elements of the resistance to globalisation, many countries around the world need to start thinking about ecosystems that can be developed at the national level and which, in addition to being ecologically sound, will also enable them to be self-reliant. A hempcrete building industry ticks all these boxes, and, what is more, could even operate at a local/regional rather than national level.
As such, rather than conducting a European project which would necessarily involve participants or tenders from different countries, we should create projects for individual countries which explores how all the different elements of the ecosystem can be developed. This plan can then be used as a template for other regions.
Approaches such as this grew in importance following the last financial crash over a decade ago when, in a reaction to both the overuse (and increasing price) of fossil fuels – particularly oil – and climate change saw the rise of the Transition Initiative, which sought to identify ways that the basic needs of food, transport, housing, money systems, and clothing could be sustainably maintained in a dramatically changing world. This is not too dissimilar to the situation we are now in with the COVID-19 pandemic, in that the building sector is widely believed to be one which will be hit extremely hard by the financial crash which is surely to result from this, and as global debt continues to increase (it is now in the region of US$257 trillion) there really are no easy answers as to how we can expect to come out of the other side. And so, we need to think about how we can do things more sustainably – and perhaps more locally – as paying off these new debts means even greater extraction and emissions for our planet’s already ravaged resources.
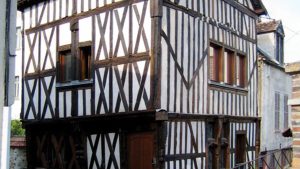
How important is it to educate policy makers on the benefits of hemp in the building sector – not just in terms of climate change etc. but also in terms of establishing local level industry?
One of the main problems is creating the sustainable hemp production and processing capabilities from the raw stage and to be able to support that long enough for the other parts of the value chain to develop. National level policy makers need to be involved in this dialogue because, as previously discussed, the industry can be made specific to any geographical location.
Over the last 10-20 years, we have seen a marked shift towards processes – across almost all sectors – which are faster but not necessarily better and which are, in many cases, toxic. Indeed, we are building houses which are potentially making people sick and we are repairing old buildings in inappropriate ways, making them places that are unhealthy to live in or which become unsafe – like the Grenfell Tower in London, which caught fire in 2017. Or, the buildings being constructed use too much energy to heat them or to keep them cool because of the way they have been constructed or the materials that have been used – or, in some instances, they use hardly any energy for these purposes because they are essentially plastic boxes which use a fan to draw in small amounts of fresh air. None of these things are healthy, and none are acceptable.
Many will argue that the hempcrete industry will be opposed by the concrete industry and will therefore be unable to flourish. However, hempcrete is not a threat to cement; rather, it will be opposed by the insulation sector and those companies responsible for rock-wool and fibreglass insulation or polyurethane foam which don’t work in the way they are advertised and, in some cases, involve toxic gases and in others will only work in a specific situation which is only replicable in a laboratory setting and unlikely in the real world.
Hempcrete offers a product which is absolutely sound in all technological and behavioural ways and which can be adapted to suit whatever need there is in any given location – once we understand what the need is, we can work with Nature, rather than against it, to provide a solution which will outperform any other material. If, for instance, Grenfell tower had been spray coated with hempcrete, then it would not have caught fire.
Policy makers, as well as those in the building sector and elsewhere, need to be made aware of the benefits of using hemp as a building material, but also of the challenges that are going to be faced when attempting to grow this sector at either the national or local level, so that viable solutions can be developed.
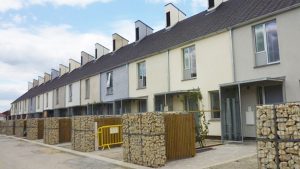
How do you predict the future of the sustainable hemp sector will evolve moving forwards? Do you have any particular hopes or concerns regarding the future? What role will the IHBA continue to play?
Our association is been primarily concerned with promoting the benefits of hempcrete, and to that end we have complied a Best Practice Guide and we also organise an annual symposium – which has been delayed this year, of course – where we feature the latest developments and showcase great examples of building projects. I have also written several books on the subject and am in the process of writing another which will feature 50 different case studies (totally different types of buildings) from around the world, all of which exceeded expectations.
As we have discussed, hempcrete can offer solutions to the building industry almost across the board, and the establishment of an industry would see the development of new relationships within communities. For instance, a builder may need to form a relationship with a local farmer to grow enough sustainable hemp for a building project – whether this is for just one house for a client, or for the construction of 100+ houses (which may require a partnership with multiple farmers simultaneously). But for these things to happen, we need support to expand production, and many of the challenges here are similar to those that some (small) companies might experience within the pharmaceutical industry, where the large and well-established players have created a whole vetting scheme and for a company to be able to manufacture in the big leagues they have to jump through a series of expensive hoops, meaning that it becomes more of an exclusive club. Attempts have been made to do the same with the building industry, and while there are numerous ways to get around this, there is a huge job to be done in terms of educating architects (and the schools of architecture especially) about the fact that sustainable hemp is a real alternative and not just a crazy idea like some which have been touted in the past.
Steve Allin
Founder
The International Hemp Building Association (IHBA)
steve@hempbuilding.com
Tweet @IHempBA
https://internationalhempbuilding.org/
Please note, this article will also appear in the second edition of our new quarterly publication.