Black Diamond Structures discusses its efforts to produce carbon nanotube-derived products on the scale required for the emerging North American lithium-ion market.
Black Diamond Structures’ de-aggregated carbon nanotube technology, MOLECULAR REBAR®, enables lithium-ion cells to hold more energy, recharge quicker, and output more power.
After stealthily working to perfect its technology and secure key patents, Black Diamond Structures is readying plans to ramp-up production to provide the emerging North American lithium-ion industry with the tools it needs to secure the nation’s energy independence.
Electric vehicles (EVs) are driving the lithium-ion (Li-ion) cell market, but cost and performance of those cells has historically limited the speed of their adoption. Now, thanks to advancements in material chemistries, cell architecture, manufacturing automation, and enabling technologies like MOLECULAR REBAR, cells are capable of answering consumer demands in a cost-effective package. This innovation spurred original equipment manufacturers (OEMs) to begin switching their fleets to all-electric over the next decade, including BMW (50% electric by 2030, 25 electrified models by 2025, 12 plug-in1), Daimler-Mercedes (new platforms 100% electric from 20252), and Ford (40-50% electric by 20303).
A nexus of technological readiness, consumer Greentech appreciation, and government incentives such as the Bipartisan Infrastructure Bill4 – which dedicates around $14.5bn to electric vehicle production, charging infrastructure, and the supply chain that support both – will rapidly increase demand for advanced Li-ion cells. Black Diamond Structures intends to capitalise on this unprecedented series of events by securing its place as the dominant supplier of carbon nanotube-derived products in the US.
MOLECULAR REBAR materials service commercial chemistries like SiGr, NMC, and LFP today, and will find great utility in the advanced solid-state, sulfur, or post-lithium technology of tomorrow.
Fast charging and responsive acceleration
MOLECULAR REBAR replaces carbon and aggregated carbon nanotubes in OEM cathode designs, offering improved, long-lasting rate capability and extended life with lower loadings than other nanotube providers, thanks to our fully de-aggregated, custom-formulated products.
When contemplating the purchase of an EV, consumers often express concern about running out of fuel. The phenomenon is termed ‘range anxiety’, referring to consumers’ worries about charging station accessibility. This could be solved by rapid-charging battery packs that can return a large amount of energy in a short time. The consumer desires 100% recharging in under three to five minutes to bring equivalency to the refilling of a typical gas tank. This is outside the realms of possibility for all but the most advanced designs. A compromise is found if a substantial percentage of energy can be returned in three to five minutes, providing enough fuel to ‘make it home.’ Exactly how large that percentage can be is becoming a sales proposition for EV marketers, a metric for cell developers to improve, and a challenge for charging infrastructure projects to debottleneck. Improved chargeability is also important for personal electronics, mobile phones, and traction applications.
Another focus for some consumers is the travel experience itself. These buyers want access to more power or, in battery terms, high-rate discharge capability. Due to battery inefficiencies, there is less energy available at high discharge rates – i.e., an acceleration manoeuvre or drag race – than there is at lower discharge rates, like maintaining 35mph in an urban setting. The relationship between rate and capacity, also known as ‘Peukert’s Law’, is not as extreme for Li-Ion as it is for Pb-Acid thanks to the difference in chemistries, but the desire remains for batteries which can discharge longer at high-rates (>5C), reproducibly. Improved discharge capacity at high rates is also required for drone applications, electric aircraft, e-cigarettes, and other non-automotive applications.
Both sets of consumers can be satisfied with the same solution: make cells more conductive or design cells with lower impedance. Compared to graphite, which is frequently used as an anode active material, cathode active materials comprising lithium iron phosphate (LFP) or nickel manganese cobalt oxides (e.g. 532, 622, 811) are typically far less conductive. The use of high loadings (~2-10%) of conductive filler, like carbon black or aggregated, raw-form carbon nanotubes, is necessary. These materials improve electrical and thermal conductivity but decrease overall energy density since they do not participate in lithium intercalation. Raw-form carbon nanotubes are often more conductive than carbon and can be used at lower concentrations (~1%) which drives their adoption. Indeed, LG Chem, one of the two largest cell manufacturers in the world, recently integrated CNT manufacture and cell manufacture under the banner LG Energy, citing CNT as one of the “four key materials for batteries”, next to anode material, cathode material, and electrolyte additives5. LG Energy is not alone in establishing the importance of nanotubes to the Li-ion market, with various industry reports indicating that CNT manufacturers are rising to meet a demand for thousands of additional tons over the coming years. Sources believe ~30-35% of the >5500 MT worldwide CNT production in 2022 is dedicated towards batteries; enough for around 160 GWh of cathode production6.
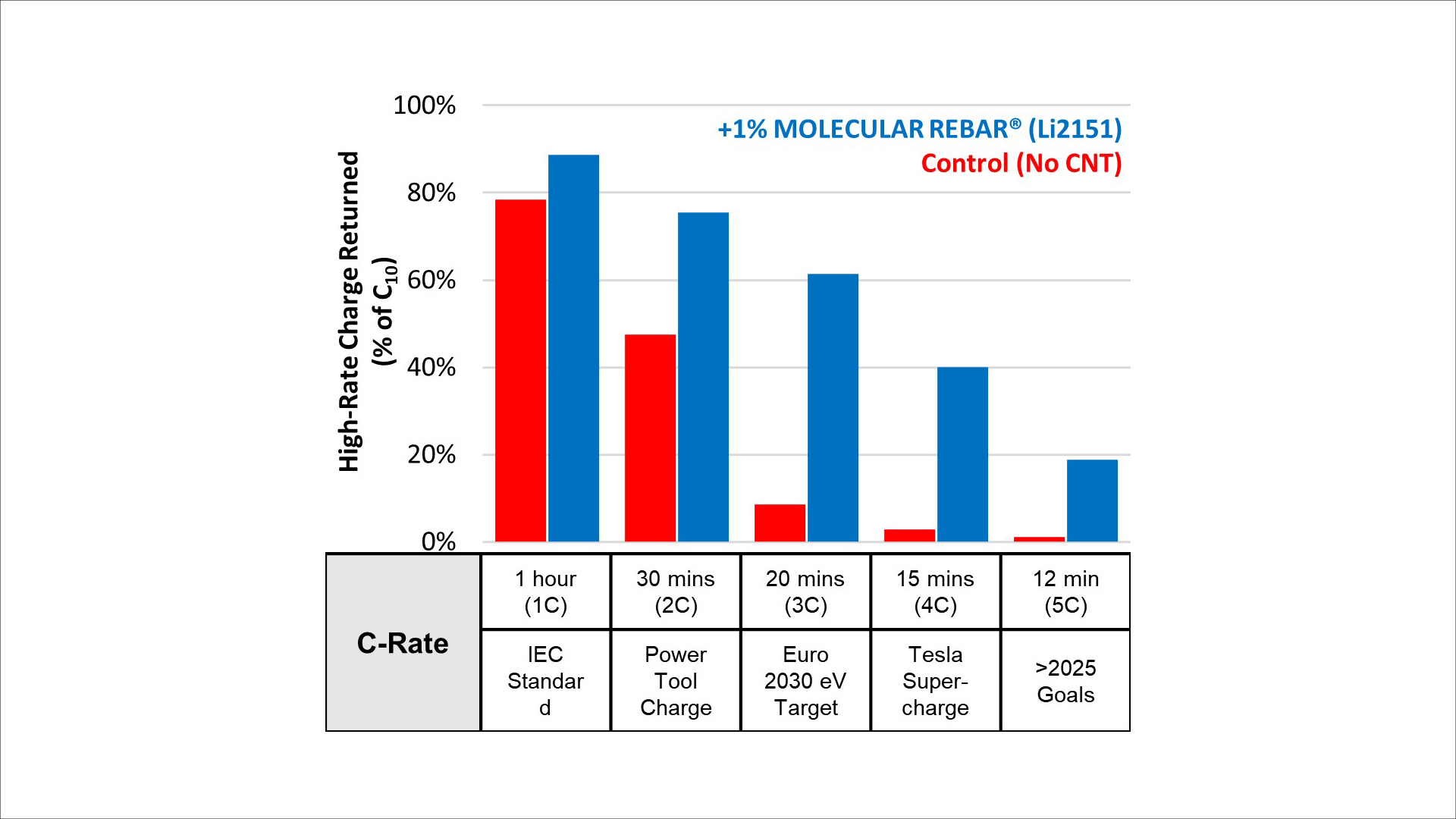
And yet, these aggregated CNT lack the level of performance brought by MOLECULAR REBAR which are de-aggregated, free of metallic and carbonaceous impurities, and often functionalised to suit various systems. These differences make MOLECULAR REBAR patently distinct from mass produced carbon nanotube aggregates. When incorporated into conventional cathode recipes, MOLECULAR REBAR improves charging capability by more than 20 times, depending on the magnitude of current supplied (C-rate), at loadings of 0.1-1.0% (Fig. 1). When compared to other nanomaterials in advanced cells, MOLECULAR REBAR offers roughly 5-10% improvements in constant-current charge duration, but partners have seen as high as a 50% improvement. Discharge performance is similarly impressive versus a standard carbon formulation (Fig. 2) or aggregated nanotube slurries. In some manufacturers’ hands, MOLECULAR REBAR can replace around ten times its weight in carbon or other forms of nanomaterial to build an energy-rich, lean cell capable of high-rate performance (data not shareable). These manufacturers utilise the structure-reinforcing properties of our material to bolster particle-particle connectivity, build thicker cathodes, and increase adhesion to current collectors. MOLECULAR REBAR is a crucial tool in the cell designer’s repertoire, helping to drive EV capability and adoption forward.
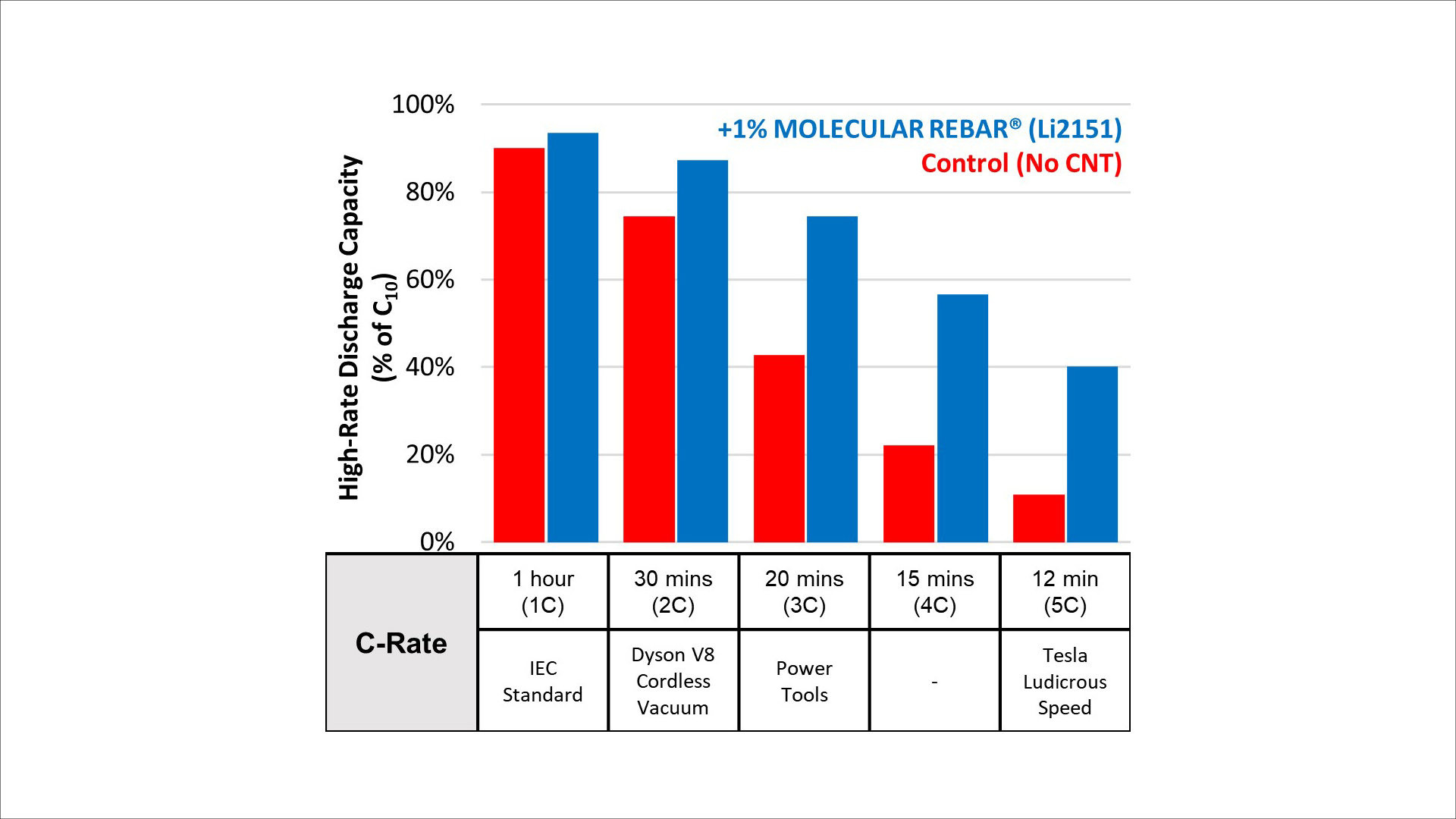
Prolonging drive time through advanced materials
MOLECULAR REBAR empowers cell makers to use high specific-capacity materials which would otherwise cause cells to swell and fail. By providing fully de-aggregated nanoscale reinforcement, uniformly and consistently across an anode’s active mass, our materials deliver best-in-class cycling performance at less than 0.05% loading. Competitive nanotube products are incapable of reaching this level of in-anode dispersion or, in turn, performance.
The concept of range anxiety can also be mitigated by using a larger ‘fuel tank’. Instead of adding capacity to existing packs, creating heavier, inefficient vehicles with design elements limited by unwieldy battery pack constructions, cell designers challenge themselves to find ways to pack more energy into the same volume; to increase the energy density of the battery.
Lithium-ion cells have come a long way from their humble beginnings in the early 1990s, where energy density was limited to ~90 Wh/kg. Chemistry changes and dramatic advancements in manufacturing have pushed energy density up to an average of ~250 Wh/kg in commercially available products. In three decades, the amount of ‘fuel in the tank’ has almost tripled and this played a significant role in the legitimisation of the EV beyond the confines of golf carts and small, urban runarounds. No longer are electric vehicles held to less than 100 miles, they are capable of 272 miles in the case of Tesla’s Model 37 and up to 516 miles in the Lucid Air Grand Touring.8 But still, the chemistry is available to push these ranges higher, breaching the 300 Wh/kg ceiling and reaching into the 400-500 Wh/kg regions and beyond.
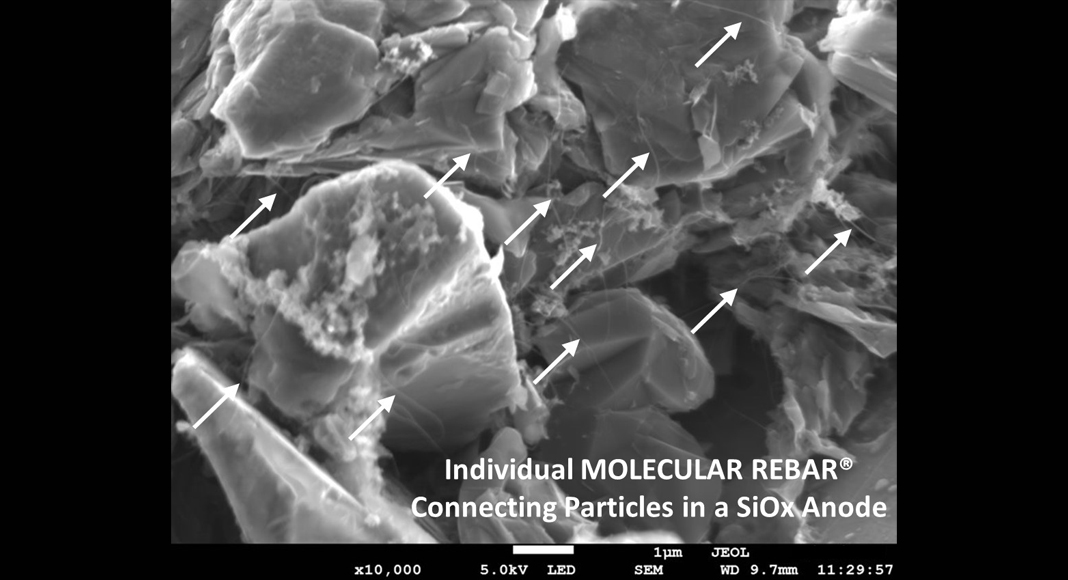
Silicon offers ten times the energy density of traditional graphite, but at a significant toll. Interaction with lithium ions forces the silicon particle, typically micron scale or smaller, to swell to 300% of its original size during charging, before collapsing and often disintegrating into smaller pieces which deplete the cell of electrolyte. MOLECULAR REBAR controls this process by reinforcing the binder, to permit the graphite matrix surrounding the silicon to withstand neighbouring materials’ expansion without delaminating from the current collector (Fig. 3). Although other nanomaterials attempt this role with varying degrees of success, it is MOLECULAR REBAR which sets the bar for nanotubular-based reinforcement. Compared to off-the-shelf aggregated MWCNT, de-aggregated and purified MOLECULAR REBAR offers a 100% improvement to cells containing 20% silicon (>280 Wh/kg, in an optimised system). BDS’ higher aspect ratio offerings, converted to MOLECULAR REBAR from a SWCNT starting material, offer even greater performance in the same system, and a 25% improvement over comparable, but poorly de-aggregated and formulated, off-the-shelf SWCNT (Fig. 4).
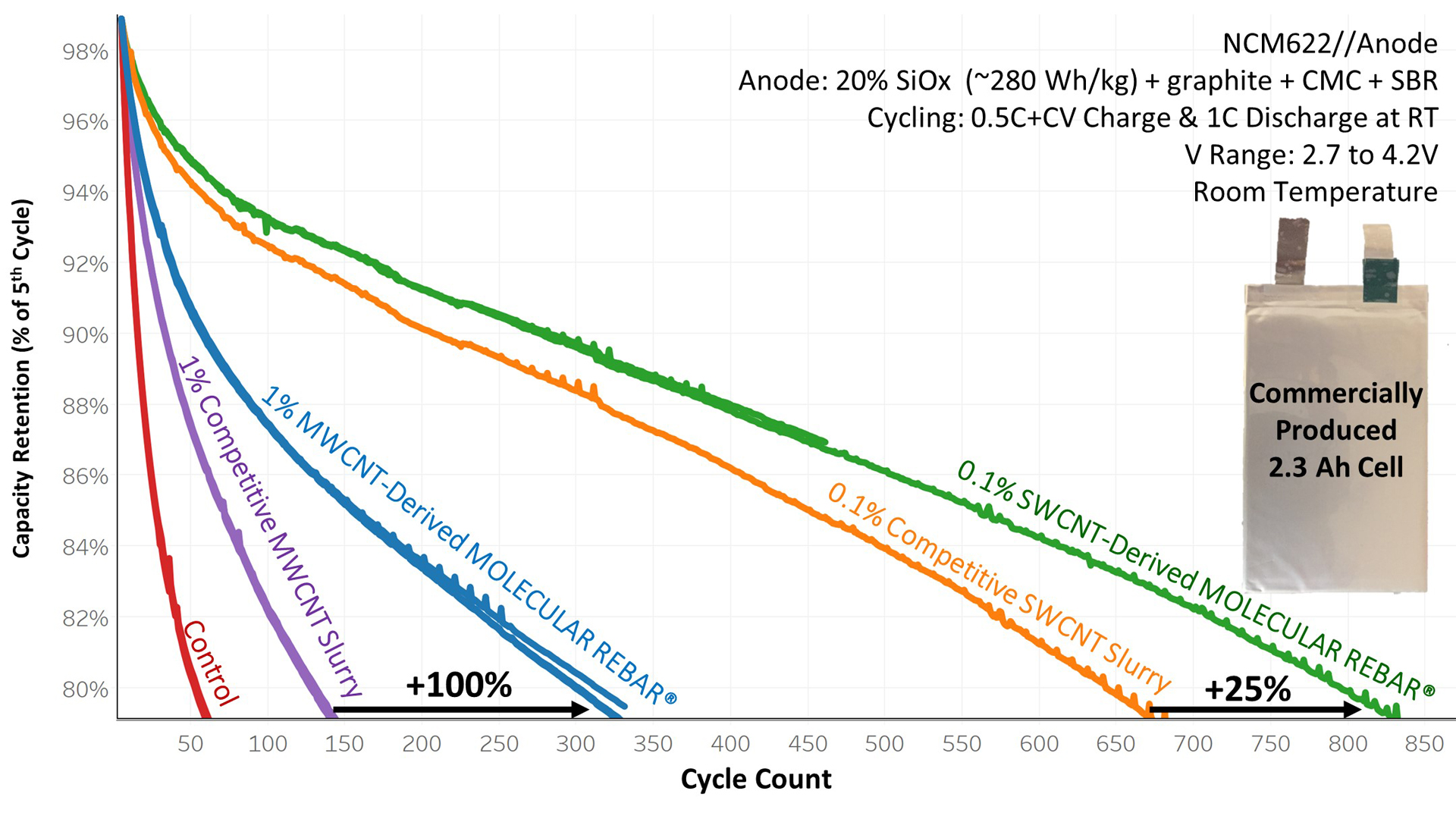
Black Diamond Structures and the MOLECULAR REBAR revolution
Black Diamond Structures, LLC (BDS) was formed in 2014 to develop and commercialise MOLECULAR REBAR technology for the energy storage sector. BDS works closely with battery manufacturers to deploy solutions into their products, helping to develop the next generation of world-class batteries. BDS’ primary research labs and manufacturing facility are in Austin, Texas, with sales teams positioned globally. The current BDS lithium and lead battery client base is over 165 companies strong, representing around 18 countries. We actively participate in global energy storage conferences, consortium-led research workgroups, specification setting committees, and regulatory compliance meetings.
MOLECULAR REBAR products provide four distinct advantages over alternative nanotube materials:
De-aggregated
Firstly, BDS formulations comprise over 95% de-aggregated, separated nanotubes. In their as-synthesized, raw form, nanotubes cluster into large intractable structures composed of thousands of interlocking nanotubes akin to a cotton ball straight from the bud (Fig. 5). These structures fail to transfer the strength and electrical properties theoretically intrinsic to the nanomaterial into the end matrix and instead perform more like standard carbon, often being used at similar loadings. By ‘ginning the cotton’, through converting the raw material into individualised MOLECULAR REBAR nanotubes, we produce a material which more uniformly integrates with the matrix. This unleashes the full performance of the nanomaterial at fractions of the loadings of other products. Although others attempt to offer detangled nanotube products to the market, none have been found that reach the dispersion quality or degree of separation as our patent-protected products in the as-shipped form, or the end matrix (i.e., in an NMC cathode).
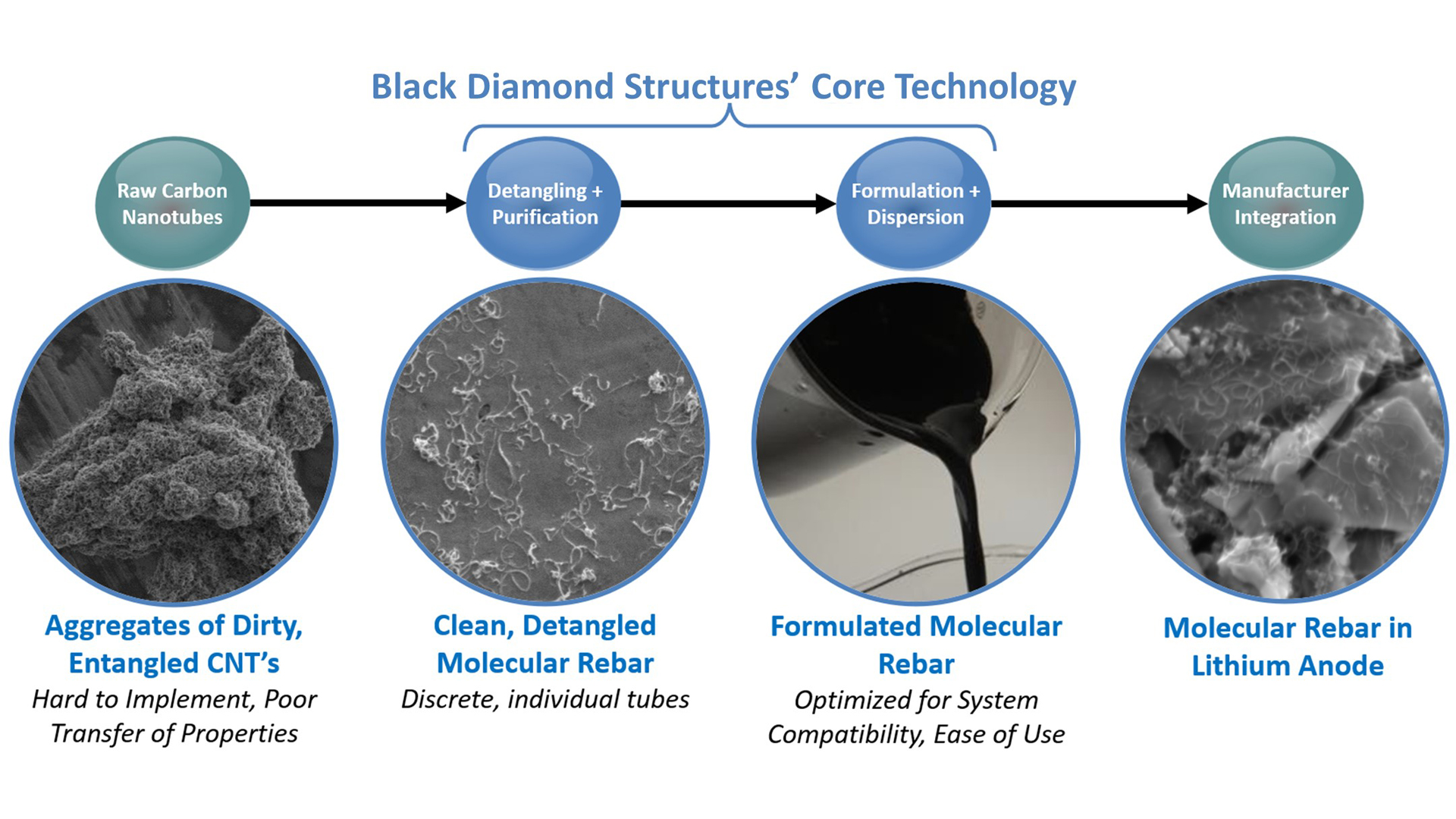
Clean
In the aggregated, raw form, carbon nanotubes sequester significant amounts of residual catalyst metals and carbon feedstocks. Thanks to our chemical and mechanical process, these impurities are almost completely removed, resulting in a substantially purer product of over 99% MOLECULAR REBAR. A purer product elicits less unintended side-reactions and allows for lower loading levels to accomplish similar performance since a higher percentage of our product is ‘active’ and not non-nanotube contaminants.
Functionalised, formulated
When needed, MOLECULAR REBAR products can be more easily functionalised with chemical groups than their as-synthesized nanotube precursors, thanks to their detangled nature which exposes more of the individual tubes’ surface for chemical attack. The ability to manipulate MOLECULAR REBAR’s interaction with its matrix, other surfaces, and elements provides additional customisation routes which ensure maximal performance in almost any system. Our chemists provide MOLECULAR REBAR products in typical solvents, at high active material content, with a best-in-class shelf-life of over 15 months.
Consistent quality and easy to use
MOLECULAR REBAR products are manufactured in an ISO 9001:2015 certified facility to the highest of quality standards. Our processing results in a highly uniform materials structure with tight length distributions and premium purities. All Black Diamond Structures’ products are tried and tested in BDS cell building facilities to develop optimal orders of operation, loading levels, and compatibility with typical industrial machinery. MOLECULAR REBAR additives are designed to be dropped into any process, with minimal capital expense, and maximum returns.
Rising to meet the great nanotube need
Black Diamond Structures, LLC is working with dozens of US-based companies, many with a global footprint, who are in various stages of development and commercialisation with our products. Some of these will be released as soon as 2023.
Our existing manufacturing site has a capacity of approximately 100 MT, enough to fulfill the needs of around 40 GWh of anode manufacturing. This will not be enough. To meet our 2025 projected demands, additional capacity must be built, and the process of site selection and planning for our next facility which will house carbon nanotube manufacture, MOLECULAR REBAR conversion, and product formulation on the same site has begun.
The new facility will boast an unrivalled nanomaterial production capacity in North America: 1,000 MT multi-walled MOLECULAR REBAR and 150 MT single-walled MOLECULAR REBAR. These volumes will support our current evaluation partners and customers while providing significant additional capacity for the emerging North American battery supply chain.
The U.S. Department of Energy is aware of around 365 GWh of battery capacity coming online over the next four to five years in North America, with more gigafactories being announced almost weekly.9 Large and small cell manufacturers are partnering with OEMs to joint venture on the plants which will power the electrification of America (for example, Ford Motor Company and SK Innovations; General Motors and LG Energy; Volkswagen and 24M Technologies). The scale and speed of this build-up will allow the US to take dramatic steps towards its Energy Independence by loosening its ties to foreign cell suppliers and by building a strong, internal supply chain, following in the footsteps of the EU who began similar operations as part of their Horizon 2020 Initiatives.
The re-electrification of America will not be cheap, but well-timed and targeted government funds will soon flow from the Bipartisan Infrastructure Bill4, providing over $14bn to support the growth of the North American Battery Supply Chain, the cell and EV production capability, and the charging infrastructure to support the new load. As our nanotubes are as fundamental to the performance of advanced lithium-ion batteries as the lithium itself, BDS intends to access a portion of these funds to provide the industry with the homegrown, clean, de-aggregated nanotube products it needs to build its cells. If the ~365 GWh capacity was dedicated to energy-dense, high-rate capable EV battery cells, it would require around 6,000 MT of de-aggregated carbon nanotubes, and Black Diamond Structures aims to supply. With our partners, we will bring the world’s best nanotube synthesis technologies together with the world’s best de-aggregation and formulation processes to fulfill the enormous unmet need for locally manufactured nanomaterials in the US. The facility will be centrally located within a soon-to-be-built 25-60 GWh battery park near at least ~150 GWh of additional demand.
Beyond energy storage
MOLECULAR REBAR has found uses in medical applications at BioPact Ventures, LLC, electronic applications at ElecNano, LLC, 3D printing technologies at MechNano, LLC, and internally at Molecular Rebar Design, LLC, in coatings, rubber compounds, and composites.9
Molecular Rebar Design, LLC, owns more than 120 patents across its application spaces in various jurisdictions. Black Diamond Structures, LLC, are the exclusive licensees of Molecular Rebar Design’s prolific patent portfolio in the Energy Storage space. There are four layers to our shared Intellectual Property portfolio:
- Use of MOLECULAR REBAR material (granted through to 2037);
- Use of formulations comprising nanomaterials with MOLECULAR REBAR-like properties;
- Use of MOLECULAR REBAR formulations in various intermediates, such as battery slurries; and
- Use of MOLECULAR REBAR in various applications spaces, such as batteries.
Molecular Rebar Design LLC’s extensive IP prevents others from using de-aggregated, clean, and/or functionalised or formulated nanotubes matching the physical description of our MOLECULAR REBAR in a variety of applications. With the use of nanotubes being increasingly prevalent in the energy storage field, it is unsurprising that Black Diamond Structures, LLC, has already uncovered examples of infringement in store-bought batteries and will pursue licensing actions against the offenders, under the advisement of several well-respected legal offices.
The right material, in the right place, at the right time
MOLECULAR REBAR is a critical component for the high-rate capable, energy dense cells vital for the growth of the emerging EV industry in North America, and beyond.
Our products offer best-in-class performance at fractions of the loadings of competitive material thanks to our focus on de-aggregation, formulation, and integration into the final matrix. All are protected by composition of matter patents, application patents, and formulation patents.
We intend to dramatically increase our capacity over the next two to three years to bring clean, de-aggregated nanotube synthesis and manufacture to North America on a scale capable of addressing the incredible unmet need for these materials in the Li-ion battery supply chain.
References
1 M Kane, “BMW Electrification Roadmap: 25 Plug-Ins By 2025” May 2019
2 C Randall, “Daimler to exclusively introduce EV platforms from 2025” July 2021
3 T Krisher, “Ford: Electric vehicles to be 40% of global sales by 2030” May 2021
4 Congress, “www.congress.gov” 15 Nov 2021
5 P Crompton, “BEST Mag,” Energy Storage Publishing Ltd., August 2021
6 DataM Intelligence, “Carbon Nanotubes Market Size & Growth | Forecast 2022, 2029”
7 Tesla, 2022
8 Lucid Motors, 2022
9 Molecular Rebar Design, 2022
Please note, this article will also appear in the tenth edition of our quarterly publication.