Sari Rautiainen, Senior Scientist at VTT, proposes a new circular approach to PEF plastics: from citrus peel to plastic bottles.
Fossil-based polyethylene terephthalate (PET) plastics are widely used in packaging and plastic bottles, amongst other things. While plastics have many benefits in food packaging, they also cause major environmental issues such as plastic pollution and carbon emissions. In order to tackle these problems, fossil-based PET plastics could be replaced by bio-based polyethylene furanoate (PEF) plastics with a lower carbon footprint. This shift, however, requires new, efficient methods. VTT has created an alternative route for producing PEF-plastics from food waste streams. Circularity and high yield are the major benefits of this novel technology.
Our current habits of using, consuming, and discarding plastics have created huge global challenges and major damage to our environment. We need new, sustainable solutions and technologies to tackle these issues.
Plastic packaging is one of the fields that most urgently requires a shift towards more sustainable solutions. Both eco-conscious consumers and policymakers are pushing for more sustainable packaging. The EU strategy focuses on achieving 100% recyclability, reusability, or compostability of packaging materials by 2030.
A shift towards bio-based materials
VTT has identified the shift to bio-based materials made from sustainable feedstocks as one of the main paths towards the circular economy of plastic packaging. Currently, most plastic packaging materials are made from fossil feedstocks, and these materials are typically not circulated.
Replacing these fossil-based materials with alternative bio-based materials made from renewable feedstocks can significantly reduce the carbon footprint of packaging. Together with solutions that enable effective recycling and enhance biodegradability, these bio-based materials can take the circular economy of packaging to a new level.
PEF – a 100% bio-based alternative to PET plastics
Research has been conducted on the possibility of manufacturing bio-based PET plastics, but without commercially viable results. PEF plastics are a 100% bio-based alternative to PET plastics, with enhanced characteristics.
Replacing fossil-based PET with plant-based PEF polymers can lower the carbon footprint of the end products by 50%. PEF also provides superior mechanical and barrier properties. When applied to food packaging, this means longer shelf life for food products.
Traditionally, PEF plastics are manufactured using edible glucose and fructose as feedstock. VTT’s novel technology provides a circular approach: it uses food waste streams as the feedstock to produce PEF plastics.
FDCA: an essential building block for PEF plastics
PET plastics use terephthalic acid in the production of polyesters, while PEF plastics substitute this by bio-based 2,5-furandicarboxylic acid (FDCA) and its esters. In addition to terephthalic acid, PET and PEF both need ethylene glycol as a second monomer, which can be produced from renewable sources.
Traditionally, FDCA is produced in a two-step process starting from edible glucose and fructose with 5-hydroxymethylfurfural (HMF) as the intermediate. The sugar is first dehydrated using an acid catalyst into 5-hydroxymethylfurfural (HMF) which is further oxidised into FDCA. Another option is to use methanol as solvent for the dehydration, producing methoxymethylfurfural (MMF) as the intermediate.
There are two problems related with this common method. First, the raw materials – glucose and fructose – could also be used in the food industry. Thus, this process competes directly with the food chain. This problem could be overcome by using lignocellulosic glucose.
Second problem has to do with the instability of HMF. This intermediate readily reacts further under acidic conditions to produce levulinic acid and insoluble humins. Because of this instability, HMF yields often remain low. Although extensive efforts have been made to suppress the side reactions and enable high yields of the isolated HMF, the inherent instability of HMF makes it a challenging molecule for biorefineries.
VTT’s new route to FDCA
VTT’s chemical development platform has created a unique and highly efficient process for producing FDCA and its esters. This patented technology overcomes the challenges related to the traditional production process of FDCA.
It enables the use of pectin-containing agricultural waste streams as raw material and enhances the circular economies of plastics. Furthermore, it uses C6 aldaric acids as stable intermediates. A stable intermediate does not tend to react further, which is essential for achieving high yields of FDCA.
The first step on this new route is to replace the edible glucose and fructose by sustainable feedstock that does not compete with the food industry. VTT’s process uses food waste streams such as orange peel or sugar beet pulp as feedstock. VTT’s experts on biotechnology have developed and patented technology for producing aldaric acid by the oxidation of galacturonic acid, the main constituent of pectin. With this technology, under-utilized waste carbohydrates can be used as raw material for renewable monomers.
Aldaric acid is a stable intermediate for the production of FDCA. The next step of the process is the dehydration of aldaric acids by solid acid catalysts in butanol or in other alcohol solvent to produce furancarboxylates. Best results are achieved with heterogeneous acid catalysts, e.g. silica-supported sulfonic acid catalysts. The FDCA mono and diesters produced in this process are more easily processable than FDCA in free acid form.
Combining VTT’s patented technologies for producing aldaric acid from pectin and, subsequently, FDCA from aldaric acid, VTT can resolve the entire route from food waste to PEF plastics. This efficient process enables high yields of FDCA up to 80 mol %.
Suitable for high-end applications
The PET market volume is currently over 30 million tonnes annually. Major fields of application are food packaging, plastic bottles, and textiles. PEF polymers can offer a direct replacement for the raw material of these plastics and cut the carbon footprint of the final products by 50%. Furthermore, PEF is a high-performance plastic with some improved qualities compared to PET plastics, mainly superior barrier properties. PEF provides several times better barrier for oxygen, carbon dioxide, and water than PET. When this material is used in food packaging, it enables longer shelf life for food products, helping to reduce food waste.
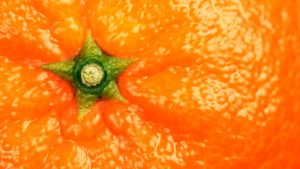
PEF is fully renewable and completely recyclable. PEF bottles can be recycled directly in the PET streams, which is important to the consumers when these products enter the market. This opens possibilities for the industries to reduce waste and to have positive impact on the environment.
While PEF can offer direct replacement to PET plastics, it is not the only material that can benefit from FDCA. FDCA is also rapidly gaining interest as a bio-based monomer for other applications such as polyurethanes and epoxy resins, and the research of other materials goes on.
The next step: upscaling the production
VTT has brought this process for producing FDCA from food waste to pilot production. The production is on a kilo scale and still upscaling. VTT’s unique scale-up infrastructure from laboratory to pilot ensures that this new technology will be brought to a technology readiness level that will allow polymer manufacturers’ easy transition to full scale.
Currently, VTT is looking for industrial partners to upscale the production. In the near future, you may buy orange juice in bottles that are made out of orange peel.
Please note, this article will also appear in the sixth edition of our quarterly publication.