Biofuels and other biochemicals based on lignocellulosic biomass and municipal solid waste are part of the solution of the future.
As the price of CO2 emissions continue to rise sharply, forerunner companies are already creating their decarbonisation strategies and looking for alternative feedstocks. Lignocellulose and municipal solid waste as well as waste plastics are new possibilities for sustainable, low carbon transportation fuels and other chemicals. All of them are critically needed to secure supply of crucial materials.
Pyrolysis and gasification of plastic waste
Pyrolysis and gasification, the main technologies of chemical recycling, allow us to recycle plastic waste which is otherwise incinerated or sent to landfill. The advantage of chemical recycling is that it can be used for mixed post-consumer plastic waste streams – when mechanical recycling is not an option.
With these recycling processes, a new feedstock avenue is opened to the petrochemical industry. The use of plastic waste as an alternative feedstock represents a completely new business opportunity.
Plastic waste is still an untapped resource for industries. Although plastic packaging waste recycling rate in Europe is already nearly 40%, we must look for new recycling alternatives.1
In Europe, approximately 30 million tons of post-consumer plastic waste was collected in 2018, of which 12 million tons was used for energy recovery and approximately 7.2 million tons was sent to landfill.
“Ideally, the plastic we left uncollected, landfilled, or burned could be used as feedstock for the industry to make various products,” says Senior Scientist Muhammad Saad Qureshi from VTT.
During pyrolysis, impurities are removed from the plastic waste and is converted into valuable feedstock for oil refineries and petrochemical plants for making fuels, chemicals or plastics for example.
Pyrolysis involves using heat and anoxic conditions to break down plastic waste into valuable hydrocarbons in the form of liquid, waxes, and gases.
Gasification is another method of chemical recycling. The main product of gasification is synthesis gas (syngas, CO and H2) which can be further processed into a variety of final products like gasoline, diesel, methanol, synthetic methane and chemicals.
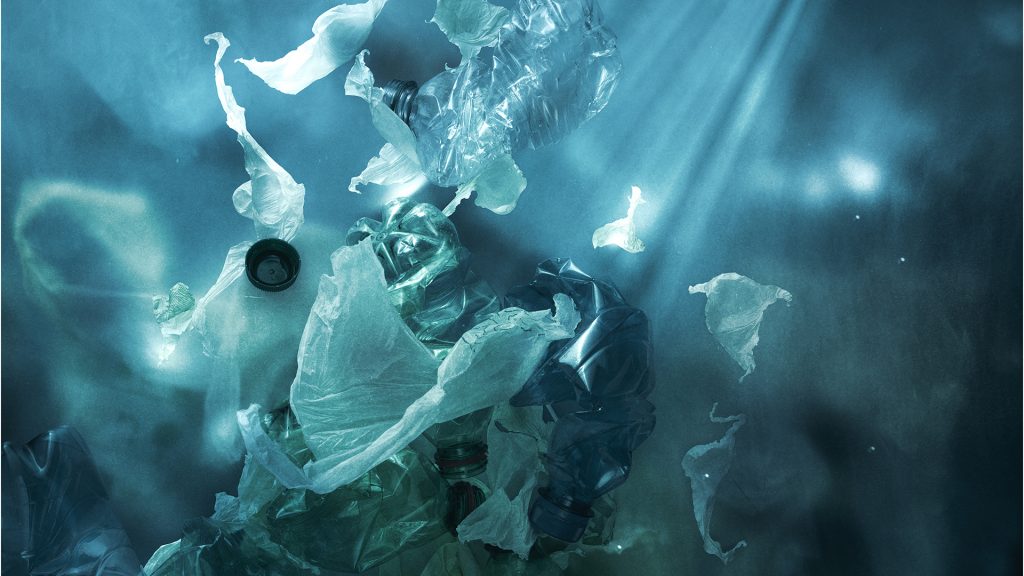
What can one do to optimise the whole value chain from waste to products?
First and foremost, the efficiency of collection, monitoring, and sorting needs to be improved to produce more suitable feeds to target products. “The target here should be the integration of mechanical and chemical recycling methods,” says Senior Principal Scientist Anja Oasmaa, VTT.
However, for plastic waste-based pyrolysis products to become a reality in industrial scale, ardent development in technologies, value chains, and supporting legislation is needed.
Hybrid technologies: from waste and biomass to fuels
The production of alternative liquid fuels can be realised by using biomass and municipal solid waste as feedstock and by combining gasification, electrolysis, and integrated production.
“Around 30% of oil-based fuels can be replaced with fuels from biomass or municipal solid waste. We can double or triple the potential if we combine gasification and electrolysis and create double-integrated processes,” says Senior Principal Scientist Esa Kurkela from VTT. His estimate is that centralised refineries could utilise millions of tons of sustainable feedstock annually. This requires that oil refineries get rid of oil utilisation.
VTT has got the overall concept for combining the technologies. “The process starts with gasification followed by robust gas cleaning. Our specialty is catalytic reforming technology. It increases the conversion efficiency compared to other technologies,” describes Kurkela.
The gasification can be done with VTT’s method at relatively low temperatures thanks to the catalytic reforming technology. In the reformer, gases can be transformed into syngas, which can be processed directly into transportation fuels.
“We can increase the efficiency of the biomass or waste conversion to high-quality fuels quite dramatically, 30-40% compared to conventional gasification-based technologies”, says Kurkela. The process is similar for all feedstocks.
Municipal solid waste is cheap and its importance is growing. According to the estimate of ETIP Bioenergy, a potential 44 million tons of MSW could be available in the EU in 2030.
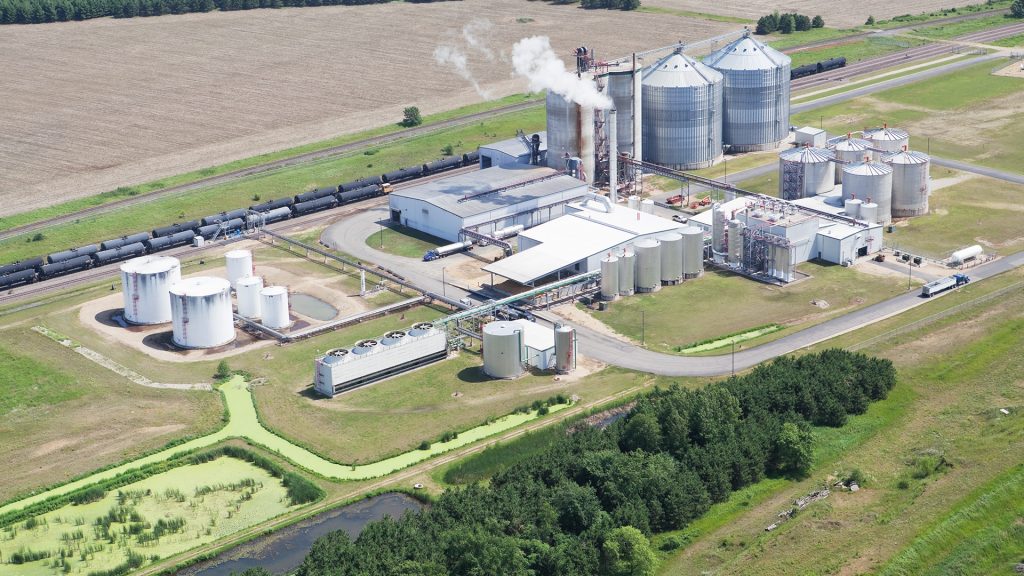
Lignocellulose for biofuels
How about using cellulose and hemicellulose – the carbohydrate components of lignocellulose – as a raw material for biofuels? Today, the technologies for utilising the biomass are ready for upscaling at VTT.
Enormous quantities of organic wastes, which are lignocellulosic, are generated annually. These wastes represent a valuable resource for areas with agricultural-based economies. Small-sized wood and residues from forestry have high potential because they cannot be used as timber in construction. Furthermore, straw and leftovers from rice cultivation could also be used.
There are two ways to produce biofuel from lignocellulose. In thermochemical conversion, lignocellulose is decompressed in high temperatures into its components which can then be re-assembled into fuels or chemicals. The main methods used in decompression are pyrolysis and gasification. The second way is to use enzymes and microbial cells in the conversion of biomass.
“We can engineer microbial cells to get the products we want, for example platform chemicals which can then be reformed into fuels and chemicals,” says Research Professor Merja Penttilä, VTT.
Biomass requires efficient pre-treatment for enabling efficient biotechnical production of various biochemicals. “We have studied many alternatives like alkaline, acid, and organic salt. In principle, we are at a stage where we can go further to large-scale production,” Penttilä says.
The complex processes needed to convert biomass into fuels and other chemicals happen in bioreactors. They support biologically active environments where chemical processes can occur. “From the technological perspective, we can go at least to the demonstration-scale biorefineries to further optimise the process,” Penttilä explains.
What are the pros and cons of each feedstock alternative of the future? If you are interested in learning more, please take a look at VTT’s white paper.
References
- www.plasticseurope.org/application/files/5716/0752/4286/AF_Plastics_the_facts-WEB-2020-ING_FINAL.pdf
Please note, this article will also appear in the eighth edition of our quarterly publication.