Latrobe Magnesium demonstrates a world-first, environmentally sustainable patented hydromet/thermal reduction process to produce magnesium metal and other valuable commodities from magnesium-rich waste feedstocks.
Located 150km southeast of Melbourne, Australia, Latrobe Magnesium (ASX: LMG) have completed the construction and commissioning of its 1,000 tonne-per-annum, Stage 1 demonstration plant, successfully producing environmentally sustainable magnesium oxide from fly ash – a waste product from brown coal power generation.
World-first magnesium production technology
Latrobe Magnesium’s patented hydrometallurgical extraction/thermal reduction technology is the only process capable of extracting magnesium from brown coal fly ash, and ferro-nickel slag tailing feedstocks.
Converting nearly 100% of this unwanted waste into saleable products, this low-emission process produces magnesium metal, a critical mineral, and the following valuable by-products:
• Supplementary cementitious material (SCM)
• Silica
• Char
• Iron oxide
• Agricultural lime
Latrobe Magnesium’s patented processes not only halve the operating cost of traditional magnesium and cement production methods, but reduce carbon emissions by as much as 60% compared to the industry average. Our patented process produces no further downstream tailings, ensuring environmental sustainability.
Latrobe Magnesium (LMG) has an agreement with Energy Australia Yallourn W power station to supply its Australian operations with industrial fly ash. Even with the brown coal power stations slated closure in 2028, LMG believes there will be enough fly ash provided over the next four years to supply this feedstock for a 20-year commercial plant.
Staged expansion pathway
With the recent completion of the demonstration plant’s magnesium oxide strategy, whereby the project successfully produced magnesium oxide, an intermediate product for customer sales, prior to the production of magnesium metal; the Stage 1 construction continues to progress with installation and commissioning of the remaining equipment necessary to produce magnesium metal and SCM, using industry proven thermal reduction processes.
Latrobe Magnesium’s Stage 2 project, a 10,000 tonne per annum full-scale commercial plant, will have a 20+ year life and help promote industry growth and create job opportunities in the local and regional communities. With offtake distribution agreements at minimum floor prices already signed to sell the majority of its magnesium into North, Central and South American and Caribbean markets, LMG can operate at globally competitive costs due to a US anti-dumping duty of 141% payable on magnesium imports from China.
Société Générale, a multi-national corporate and investment bank with market-leading experience in structuring, advising, and financing mining and downstream metals production projects, both in Australia and globally, has been mandated as Sole Coordinator, Structuring Bank and Lead Arranger in respect of financing LMG’s Stage 2 commercial plant project.
By carefully preselecting a range of strategic suppliers across equipment, technology, construction, freight, and automation industries, Latrobe Magnesium is set to dramatically improve project efficiency and the speed in which technical outcomes are achieved.
These strategic suppliers will have direct input into the forthcoming completion of the Stage 2 Definitive Feasibility Study (DFS) to ensure a Final Investment Decision (FID) is made by the year end of 2024. This will guarantee that intellectual capacity will directly influence and optimise the ultimate design of the plant and attain a high level of accuracy in estimating the total installed costs, used in subsequent project phases.
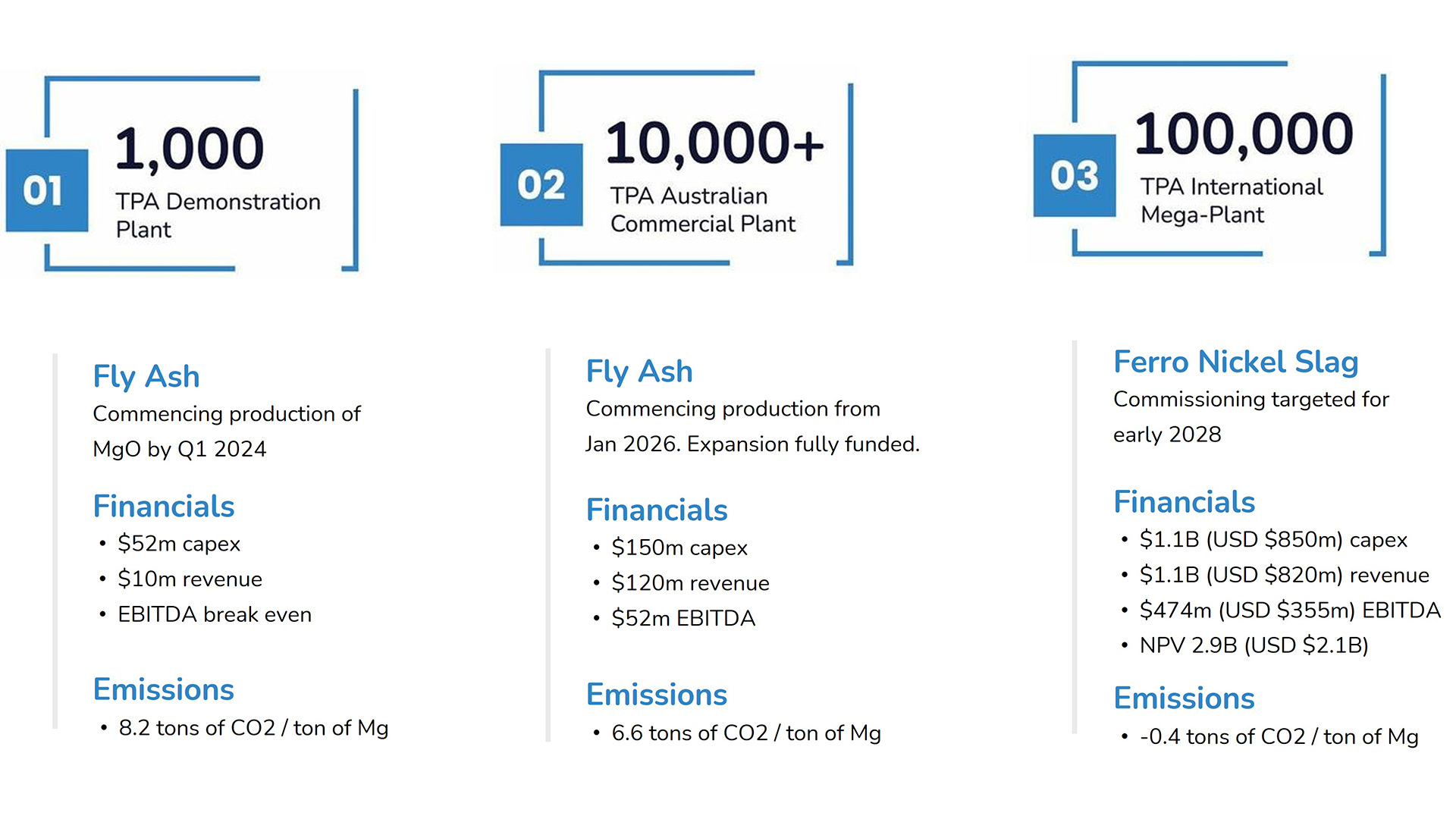
With a partially completed Pre-Feasibility Study (PFS) with global firm Bechtel, LMG’s Stage 3 is the development of a 100,000 tonne per annum international mega scale plant using ferro nickel slag feedstock. Targeting net-zero emissions to support the rising global demand for magnesium which is reaching approximately one million tonnes per annum and projected to double over the next few years, LMG has started the process to secure suitable land for the project, close to port facilities and reagent suppliers.
The projects’ location is the Samalaju Industrial Park, in the state of Sarawak, Malaysia due to the availability of sufficient hydroelectric power generation for magnesium metal to be produced with zero net emissions on a life cycle analysis basis.
Latrobe Magnesium have signed a binding Memorandum of Understanding (MoU) with Société Le Nickel (SLN), for the supply of 450,000 tonnes per annum of ferro-nickel slag over 20 years, as its feedstock for LMG’s 100,000 tonnes-per-annum operations.
Magnesium: A critical metal
With the continuous quest for weight reduction across a wide array of industries, magnesium alloys are among the most promising materials for technological development.
Magnesium is the lightest of all structural metals. With its unique blend of low density, high specific strength, stiffness, high electrical conductivity, high heat dissipation, and absorption of vibrations, magnesium is an excellent candidate to support a variety of industries.
Magnesium has the best strength-to-weight ratio of any commonly used structural metal; it is stronger and 75% lighter than steel and 33% lighter than aluminium.
Currently, the majority of primary magnesium production takes place with the Pidgeon process in China (which is energy and carbon intensive). With 85% of the world’s magnesium being supplied by one country, Latrobe Magnesium’s projects will create industry diversification and see LMG become the first producer of magnesium in Australia.
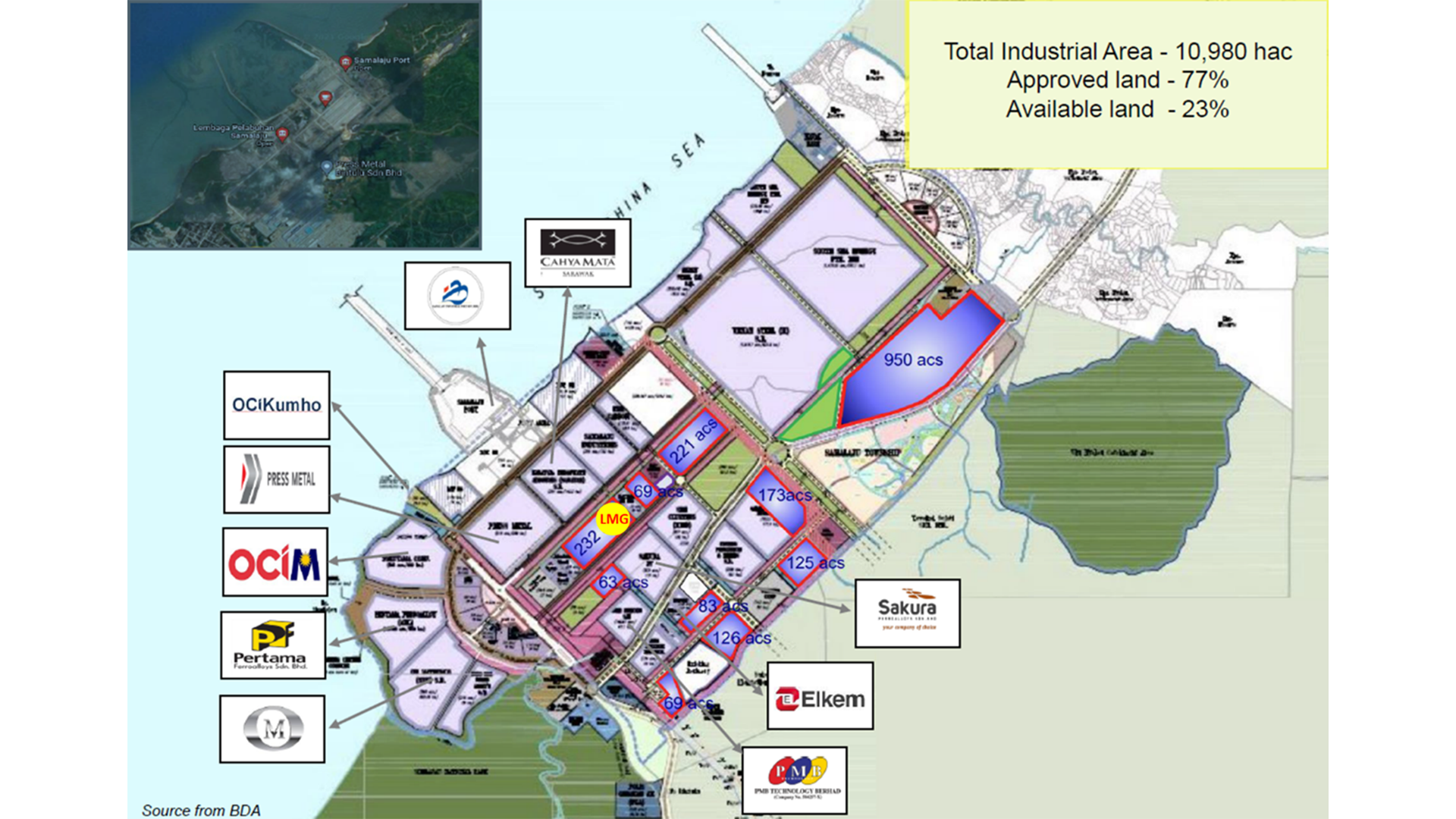
Magnesium metal can be shaped into any form, using a variety of techniques. Its unique properties and exceptional versatility make it an ideal choice for various applications, across multiple industries, such as:
• Aerospace and defence
• Automotive
• Medical and healthcare
• Electronics
• Power tools
Magnesium is ideal for the emerging electric vehicle (EV) market — extending driving range and improving efficiency by offsetting the weight of heavy batteries.
David Paterson said: “A vehicle chassis made from lightweight materials such as magnesium or aluminium alloys can reduce its weight up to 50%.”
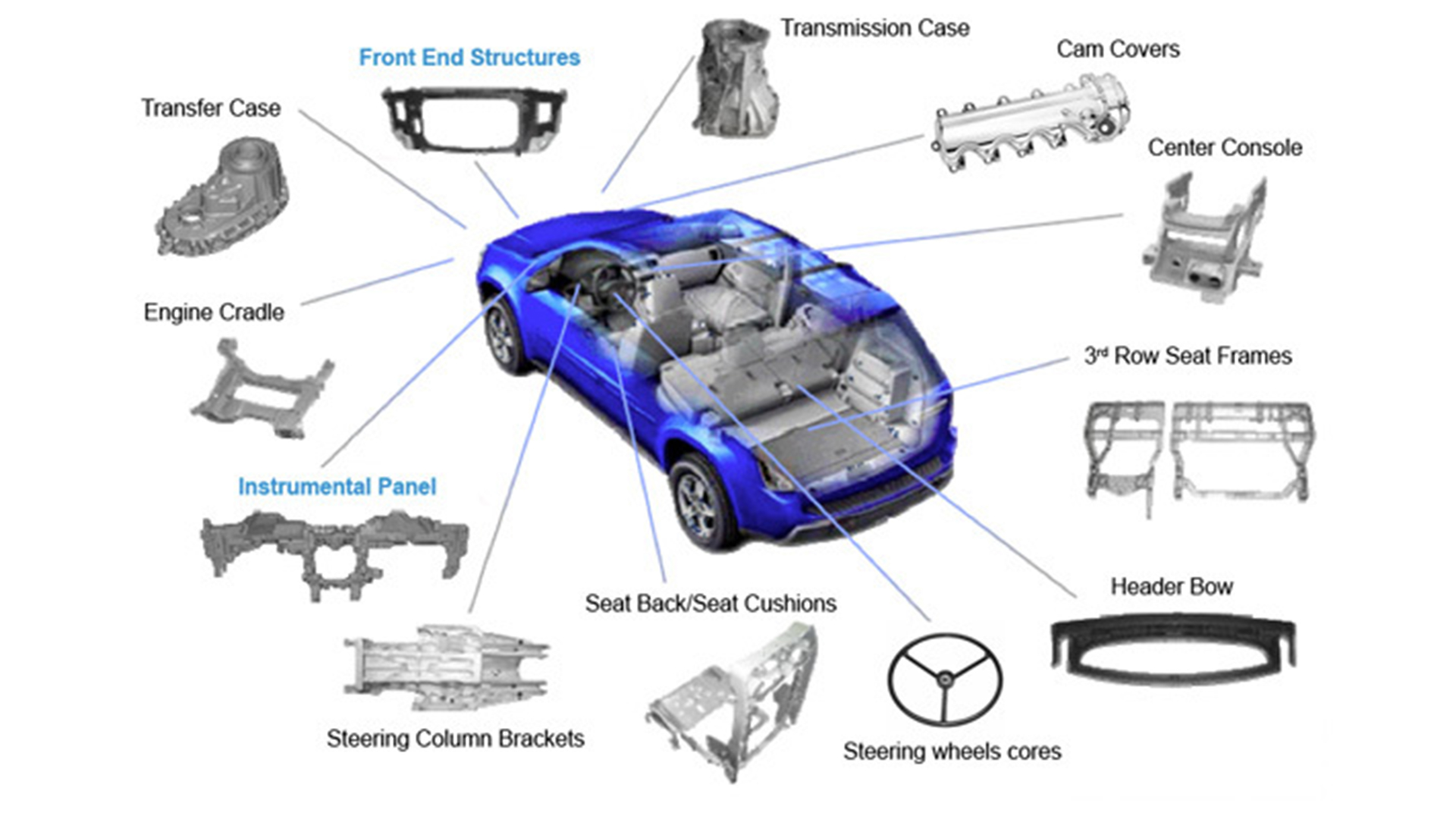
Magnesium is recyclable, holds a lower carbon footprint than aluminium, and enables lower greenhouse gas emissions over a products life cycle through light-weighting and increasing durability.
Magnesium is also desirable in the manufacturing of power tools and electronic devices. With its non-hazardous, non-toxic properties, it is placed at the forefront of cutting-edge bioresorbable medical applications.
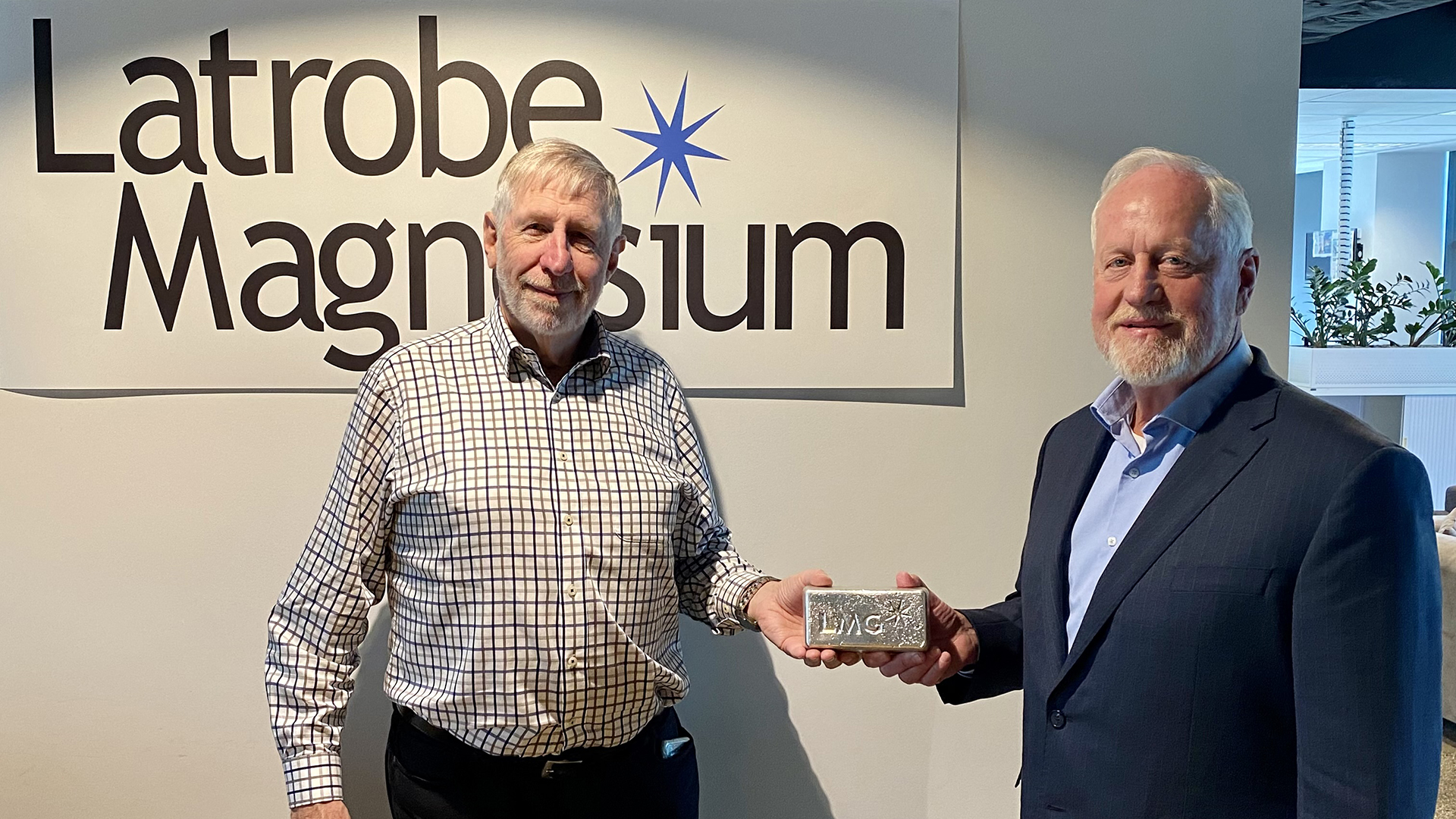
The potential of magnesium is endless, with scientists pioneering new rechargeable aqueous magnesium batteries that provide an environmentally friendly, safe, low-cost energy alternative.
Magnesium is not only a critical mineral in Australia but for trade partners such as the US, UK, Europe, and Japan, and is essential to business and industry.
Latrobe Magnesium’s projects are leading the way for metal production without environmental degradation. We contribute to a circular economy by recycling waste resources into a critical metal, and transitioning to a low carbon, sustainably responsible future.
Please note, this article will also appear in the 18th edition of our quarterly publication.