Advancing our understanding of the degradation caused by hydrogen can provide the scientific and technological knowledge needed to improve hydrogen storage and transport.
Led by Professor T A Venkatesh at Stony Brook University, a multi-disciplinary team of academic researchers, from three programmes (Materials Science and Engineering, Mechanical Engineering and Chemical Engineering) across three institutions (Stony Brook, Stanford and MIT), are teaming up with national laboratories, industry and utility partners in an important project on hydrogen funded by the United States National Science Foundation to optimise hydrogen storage and transportation.
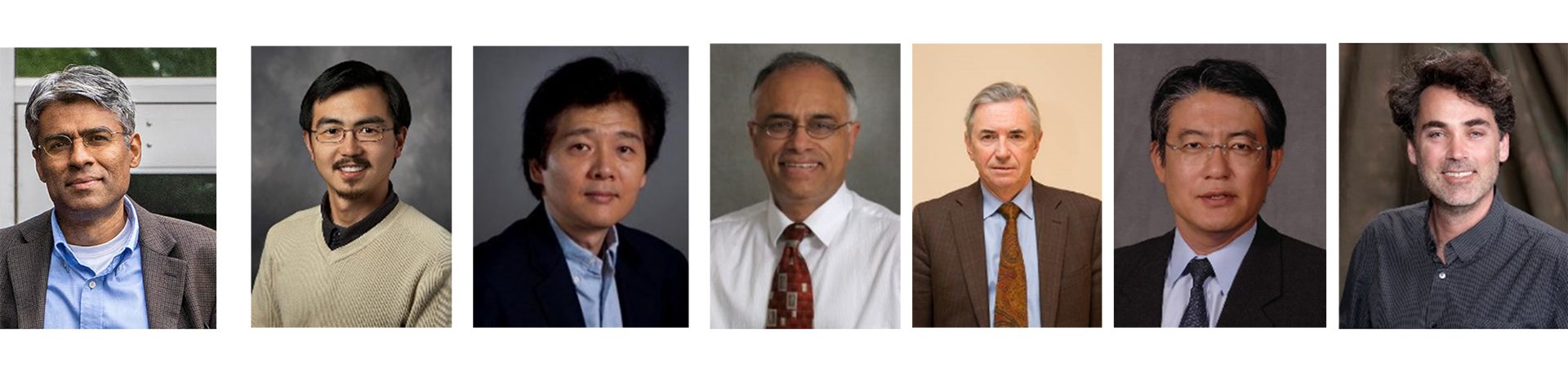
The promise of hydrogen
Hydrogen, a carbonless fuel with water as its combustion product, is the ultimate clean fuel to address environmental CO2 management. Hydrogen is a flexible energy carrier and has been identified by the U.S. Department of Energy (DOE) as being able to “enable resiliency of the power generation and transmission sectors, while also aligning diverse multibillion dollar domestic industries, domestic competitiveness, and job creation.”
The attributes of hydrogen are compelling. It can be stored in compressed or liquefied form and in adsorbed storage systems. It can be blended with pipeline natural gas and this capability makes the gas distribution networks a potential asset for the transportation and storage of large amounts of renewable power production using hydrogen. In addition, hydrogen has the potential to store more dispersed renewable energy, at a lower cost, than traditional methods such as electrochemical batteries. This energy can then be used to generate electricity with fuel cells, power fuel cell hybrid electric vehicles (EVs) and to heat or cool buildings. With the promise of a green hydrogen economy now closer to reality than it has ever been, the US and Europe have taken lead roles in road-mapping and catalysing the development of appropriate infrastructure that can support and sustain the promise of hydrogen. The H2@Scale programme of the DOE estimates the economic potential of hydrogen to become a $1tr economy by 2050.
Future plans of utilities
From the perspective of utilities, what is not known today is:
• The magnitude and limits or the expected cost profiles to produce, store, and distribute hydrogen using the growing gas infrastructure; and
• Technology enhancements and investment required for new infrastructure and energy service equipment to effectively enable hydrogen to be a competitive option for the long-term storage and distribution of renewable energy.
A study by the RAND Corporation concluded that “If hydrogen emerges as an important fuel in the power or transportation sectors, regulators will be faced with decisions regarding competitive access to hydrogen distribution networks and also distributed generation access to the electric grid. These would be important considerations for natural gas utilities contemplating speculative investments (not covered by regulated rate recovery) in hydrogen production and distribution.”
Current understanding of materials issues and mechanisms in the hydrogen embrittlement field
To realise the promise of the hydrogen economy, materials issues associated with hydrogen storage need to be well understood. Hydrogen degradation (HD), including embrittlement (HE), is recognised as a complex metallurgical phenomenon which combines chemical and physical processes that ultimately degrade the metallurgically designed toughness of an alloy, ultimately compromising hydrogen storage capabilities. Not all alloys are susceptible to HD, but gas pipeline steels and pressure vessel steels are susceptible to spontaneous failure in the field. Adding hydrogen to natural gas or replacing natural gas with hydrogen in the pipelines requires analytical understanding of the issues which may lead to HD and to develop the correct strategy to eradicate or at least significantly lower the risk of HD.
Several efforts have been made worldwide to characterise the influence of hydrogen on the mechanical properties of potential pipeline and pressure vessel materials. With insights from experiments, several mechanisms have also been proposed to explain the phenomenon of hydrogen embrittlement that principally include processes that reduce surface energy, resulting in hydrogen-enhanced decohesion, processes that interact with dislocation movements resulting in hydrogen-enhanced localised plasticity and, more recently, processes that involve interactions with vacancies resulting in hydrogen-induced nano-void formation, growth and coalescence leading to fracture.
When steels that have hydrogen trapped in them are subjected to pulsating stresses, as can be observed in pipelines near the compressor stations which pump up gas pressure to facilitate faster movement of gases, they can also exhibit significant susceptibility to damage due to fatigue. A common theme that emerges from the analysis of fatigue crack growth data of pipeline materials obtained by several researchers is that the fatigue crack growth rate (da/dN) (as a function of the crack driving force, ∆K) displays two unusual characteristics (as seen in Fig. 1).
There is high sensitivity to the presence and concentration of hydrogen at lower crack driving force (∆K) regime. There is also relatively lower sensitivity to hydrogen and microstructural features at higher ∆K regime. Consequently, the hydrogen effect on crack extension rate (da/dN) is fully manifested only above a certain threshold value of the driving force ∆K.
While some suggestions have been made towards correlating the observations with the hydrogen diffusion and fatigue load frequency, the controlling mechanisms are still not well understood.
Multi-disciplinary team
In order to obtain a fundamental understanding of the degradation caused by hydrogen, an academic team with expertise in modelling across multiple length-scales from atomistics and dislocation dynamics (Dr Cai), to crystal plasticity (Dr Dao) and continuum/structural length scales (Dr Nakamura and Dr Venkatesh), and expertise in experiments on indentation, fatigue and fracture (Dr Venkatesh and Dr Dao), corrosion science (Dr Clayton) and in scaling up technologies for decarbonisation (Dr Mahajan) is working together with scientific collaborators from National Laboratory (Dr San Marchi, Dr Renovich and Dr Zhou), and a gas utility (National Grid) on this important project.
Key questions and hypotheses
The team has hypothesised that the controlling mechanisms for hydrogen-induced damage under fatigue conditions occur in the plastic zone around the crack tip, over a length scale of about one to ten microns, which is too small for continuum theory to be predictive and too large for atomistic simulations to handle by brute force. This project will close the knowledge gap at the mesoscale, through a tightly coupled experimental-computational programme.
The team will:
• Develop a multi-scale modelling platform, informed by and integrated with experiments, to accelerate the pace of understanding and discovering fundamental knowledge related to the mechanisms of hydrogen embrittlement, particularly under fatigue-loading conditions; and
• Enable the faster deployment of hydrogen-resistant materials and microstructures in the energy transportation sector as it transitions from the transport of fossil fuels, such as natural gas, to hydrogen-based renewables.
At a fundamental level, this study will advance the current knowledge of crack tip processes that contribute towards damage initiation and propagation under fatigue loading, as the material transitions from a relatively ductile material (without hydrogen) to a relatively brittle material (with hydrogen). Central to the understanding of damage accumulation and progression due to cyclic loading in hydrogen environments is the understanding of:
- Kinetics of hydrogen adsorption and dissociation at the material surface in the presence of impurities, diffusion, interactions with trapping sites and propensity for hydrogen gas and/or hydride formation inside the material;
- Mechanics of dislocation level activities – activation, multiplication, movements, interactions, pileups, cross-slips, and persistent slip band formations; and
- Mechanisms of fracture processes such as micro-void creation, growth, and coalescence.
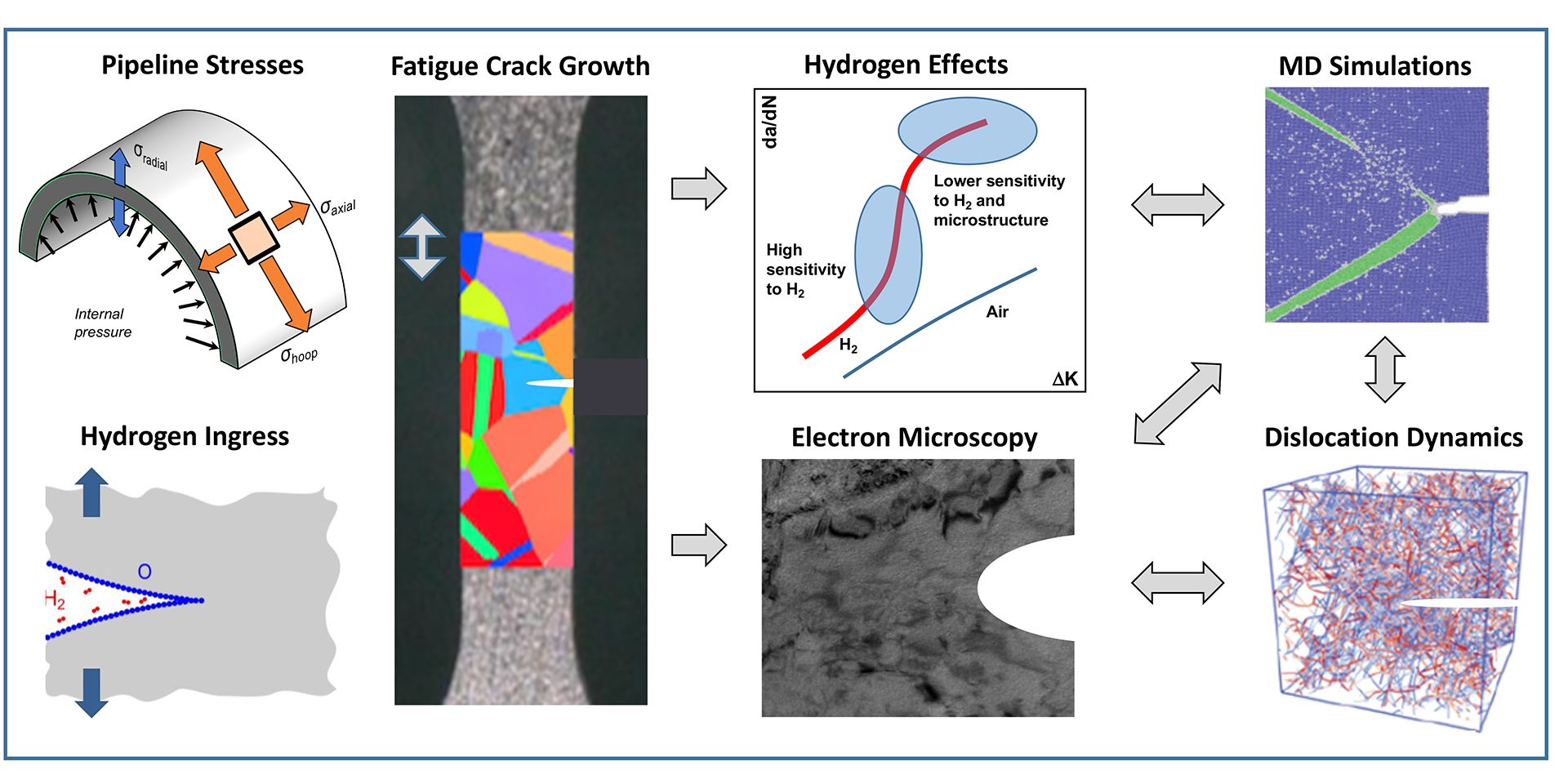
While each of the above mentioned three aspects have been recognised as being independently important for influencing the mechanical behaviour of materials in hydrogen environments, the novelty of this study lies in the consideration of key elements from these aspects – i.e., kinetics of hydrogen diffusion and chemistry of hydrogen interactions with the mechanics and mechanisms of plastic deformation and fracture, in an integrated manner, from the atomistic level to the continuum level.
As the phenomenon of hydrogen embrittlement has posed intriguing challenges for researchers for several decades, this study is designed to provide key insights on an important piece of the puzzle in the hydrogen embrittlement field (i.e., crack initiation/propagation), which would contribute towards the development of comprehensive frameworks for:
- Microstructural design for developing materials with enhanced hydrogen damage resistance; and
- Structural life prediction for hydrogen storage and transportation infrastructure.
New insights on large-scale hydrogen transport
The current natural gas pipeline system consists of gathering, transmission, and distribution lines, each with varying materials, in-service age, operating conditions, and equipment size. Hydrogen blending is expected to take place in both transmission and distribution lines that connect commercial and residential end users. Pressure reduction is one of the drawbacks that hydrogen blending brings to the cost dynamics of blended gas transport. In general, more energy is needed to transport the blended gas (compared to pure natural gas) to deliver the blended gas of comparable energy density at the appropriate flow-rate conditions to the end users. Computational fluid dynamics (CFD) models are being built to assess the effects of hydrogen concentration and flow boundary conditions on the blended gas flow characteristics and the projected energy costs associated with the transportation of methane-hydrogen gas blends. The CFD analysis has shown that, by modifying the pressures and flow rates, the increased cost of transporting hydrogen can be mitigated.
Preliminary studies in hydrogen blending have demonstrated that end-use appliances, such as modified engines, oven burners, boilers, stoves, and fuel cells, can be designed to have good compatibility with hydrogen-blended fuels where the blend volume fraction of hydrogen is typically around 20% or less. However, in considering higher blend concentrations of hydrogen in the natural gas – hydrogen mixtures – the advantages of hydrogen as a non-carbon energy carrier need to be balanced with safety concerns of blended gas during transport, such as overpressure and leakage in pipelines, hydrogen embrittlement issues and energy costs for transportation.
Please note, this article will also appear in the twelfth edition of our quarterly publication.