Antifouling paints cause the spill of biocides and microplastics in our oceans. Finsulate prevents this deliberate and unnecessary pollution with its eco-friendly antifouling wrapping solution.
As soon as a vessel or yacht gets into the water, mussels, algae and other organisms start to attach. This growth increases the drag of the vessel, resulting in higher fuel consumption and lower top speeds. To prevent this, vessel owners use toxic antifouling paints. These paints kill all marine life. Furthermore, the huge amount of toxic copper that is released causes dramatic effects on precious corals. The regrowth of corals is decimated by copper because the coral larvae die. On top of this, the paint itself is also slowly released into the oceans. Annually, 50 million litres of paint particles end up in the seas. This amount of microplastics equals roughly 10-20% of the total plastic soup. This level of pollution requires the immediate adoption of eco-friendly antifouling solutions.
Finsulate provides a solution that prevents both pollution and growth. The concept of using a wrap instead of a paint is revolutionary, however, and it takes time to convince conventional commercial marine business of its effectiveness. Nevertheless, in the area of yachting, Finsulate is already taking off.
Biofouling
Fouling is the process whereby bacteria, microalgae, and subsequent larger organisms such as mussels, barnacles, and seaweeds attach to the hull of a ship. This process can take just weeks or even days in high fouling areas like the Caribbean. In colder water, it normally takes some months for growth to become fully developed, and in cold water during the winter, nothing much happens at all.
This variety in fouling conditions in addition to the variety in the amount that ships move, makes prevention in all conditions a challenge: fouling mainly occurs when a ship is idle. As such, commercial container vessels that sail 100% of the time are less susceptible to fouling compared to yachts that are idle 95% of the time.
Pollution
Regardless of the conditions, 99% of the vessels and yachts around the world are using toxic antifouling paint. Depending on the sailing conditions and frequency, the paints are more or less successful. All cases have one thing in common, however: the leaching of paint particles and biocides into the oceans.
The annual consumption of antifouling paint worldwide is over 100 million litres. The purpose of the paint is to dissolve slowly in the water and, as a result, spread biocides that kill all marine life in the surrounding area. Concentrations of copper in the paint can reach 40% for commercial marine vessels. In yachting, the copper concentrations are lower, but they are combined with several persistent organic biocides. Annually, the use of antifouling paint leads to:
- The evaporation of 50 million litres of solvents (mainly xylene and toluene);
- The deposition of 25-50 million kg of biocides; and
- The leaching of 25-50 million kg of paint particles, all micro- to nano plastics.
Prohibition by law mainly focuses on the biocidal elements of the paints. Several states, including areas like Sweden, The Netherlands, Washington State (US) and California (US) have already put stricter laws in place. Achieving such legal prohibition takes time, and that is not necessarily just because of the legal process, but also the strength of the lobbying on the part of the paint producers. Indeed, these multinational companies can stall the legislation process for years. California is the best example of this: a first Bill was ready in 2012, but it took until 2018 for it to come into force.
Though it is logical to focus on the biocidal element of the paints due to the fact that the biocides are detrimental to things like coral reefs (as pointed out, for instance, by Steven Victor in the Marine Pollution Bulletin in 2005 and Claire Bennett in New Scientist in 2003), the effects of the dissolving paint cannot be neglected.
In a general sense, there is a societal emphasis on preventing plastic spills, and yet annually 25,000-50,000 tonnes of paint particles are deliberately released into the oceans via antifouling paints. This is no different to walking onto the shore and pouring the paint directly into the water which, of course, would be a crime. And yet, when it comes from paint dissolving from a ship hull, nobody seems to care. To put this into perspective: annually, these microplastic paint particles amount to roughly 10-20% of the total amount of plastics in the ocean which, apparently, society is concerned with preventing.
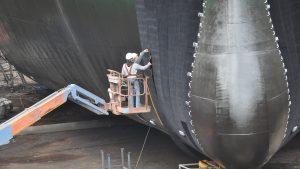
Alternatives
Several alternatives to antifouling paints are getting ready for the market. The paint producers have taken the lead with silicone-based alternatives, which are sometimes also applied as a wrap. The general concept is to make a surface slippery so that fouling cannot attach. Though conceptually this is a perfect solution, in practice things are a little different.
After a long development process, the materials are still quite vulnerable to mechanical damage, and application is critical. In addition, there is ample evidence (such as that provided by Professor Rittschoff at Duke University, North Carolina, who has published several scientific articles on the subject) that toxic compounds are continuing to leach from these paints, the most prominent candidate of which is organotin. This group of compounds has been banned by the International Maritime Organization (IMO) as a biocide since 2008, and yet the big paint producers now claim they need it to include it as a catalyst. Organotin compounds are indeed known as a catalyst for silicone polymer curing. However, these catalysts are normally added in very low concentrations. Interestingly, in all of the silicone-based paints, the concentration is at least 10 times higher than would be deemed logical, and the amounts are close to or even above the limits that the IMO has set for biocidal use.
Finsulate – The Sea Urchin Principle
One alternative to all of these toxic approaches really stands out. The Finsulate team has taken a completely different approach by looking at Nature. In Nature, many organisms use spines to protect themselves: from the spines of a hedgehog to the thorns of a rose, the principle is the same. Finsulate mimics these spines in what it terms ‘the sea urchin principle’. The team has created an artificial spiney surface with very fine hairs that stand out vertically from the surface. To create this surface efficiently and to fit in with the docking schedules of vessels, Finsulate has developed this skin as a self-adhesive wrap. Based on the continued development and the subsequent granting of the patents, Finsulate inventor Rik Breur was given the award of European Inventor of the Year by the European Patent Office in 2019.
Finsulate – in practice
Finsulate is not just an academic concept; it is already being widely applied. About 500 yachts and several commercial vessels are already sailing using Finsulate, some of them for six years, meaning that the claim of a five-year lifetime has already been surpassed. Indeed, as the materials are all durable, there is no reason to expect a lifetime shorter than 10 years, and further developments are already take place to obtain a lifetime of 20 years or more in order to meet the demand of offshore wind industries who hope to be able to increase the lifetime of wind turbines.
Application is carried out by certified installers that can either be shipyard personnel or trained wrap-installers who conduct installations on a daily basis on other objects.
Of course, there have been teething problems but, overall, 99% of clients are happy with the performance. Furthermore, while the growth rate was low in 2020 due to COVI9-19-related lockdowns which occurred during the maintenance season (March-May), the outlook for 2021 is good. With European legislation getting stricter in 2022, it is almost a given that the uptake of Finsulate will be significantly boosted in the years to come.
Rik Breur
Managing Director
Finsulate BV
+31 850653470
info@finsulate.com
www.finsulate.com/en
www.linkedin.com/company/finsulate
Please note, this article will also appear in the fourth edition of our new quarterly publication.