Element 1’s compact and efficient hydrogen generator technology offers affordable, onsite and on-demand hydrogen production.
Located in Bend, Oregon, US, Element 1 Corp is a global leader in the development of methanol-to-hydrogen generators for affordable, on-site, and on-demand hydrogen production. Drawing on more than 140 years of experience in hydrogen generation, hydrogen purification, and fuel cells, the technical team at Element 1 has achieved the most compact and highest-efficiency hydrogen generator available today.
The Element 1 approach
Recognising that manufacturing hydrogen is not difficult but transporting hydrogen (compressed or liquid) is expensive and challenging, the approach used by Element 1 is to convert a mixture of methanol and water into high-purity hydrogen at the point of use. The product hydrogen meets or exceeds ISO 14687-2019 purity specifications for low-temperature polymer electrolyte membrane (PEM) fuel cells as well as compressed hydrogen for dispensing into onboard storage cylinders for fuel cell vehicles. Typical product hydrogen purity is >99.997% hydrogen with <0.2 ppm CO (dry basis). The impurity is methane at <30 ppm, and there is about 40 ppm to 70 ppm water vapour.
With three product models scaling from 4kg of hydrogen per day up to 390kg of hydrogen a day, an Element 1 hydrogen generator operates using a highly efficient thermochemical process and achieves energy efficiency of up to 84%, resulting in low hydrogen cost at the point of use. For example, with methanol priced at $400/metric ton, the cost of the produced hydrogen is less than $3/kg of hydrogen. Required electrical power is negligible, less than 1 kW at maximum hydrogen output on the largest hydrogen generators, or about 0.1 kWhrs/kg of hydrogen delivered to the user. This is 500 times less electrical power compared to typical water electrolysers.
Moreover, even the larger hydrogen generators are small in physical size, and fully self-contained. For example, the M/L18 is rated to deliver 235kg of hydrogen a day, and it is only 879mm (W) by 2,080mm (D) by 1,380mm (H), making it practical to install onto a vehicle (e.g., medium-duty or heavy-duty truck) or maritime vessel. The M/L18 hydrogen generator pairs well with a nominal 140 kW to 150 kW fuel cell module (the L designation indicates stationary applications, and the M designation indicates mobility applications).
The L18 and its larger variants are also showing potential for distributed electric power generation (primary and backup) for applications, including battery electrical vehicle (BEV) charging stations, data centres, commerce, off-grid developments, temporary or transportable power, and critical infrastructure. All these applications benefit from the ease and low cost of transporting liquid methanol using existing infrastructure that was developed for distributing petroleum fuels (gasoline, diesel, aviation fuel).
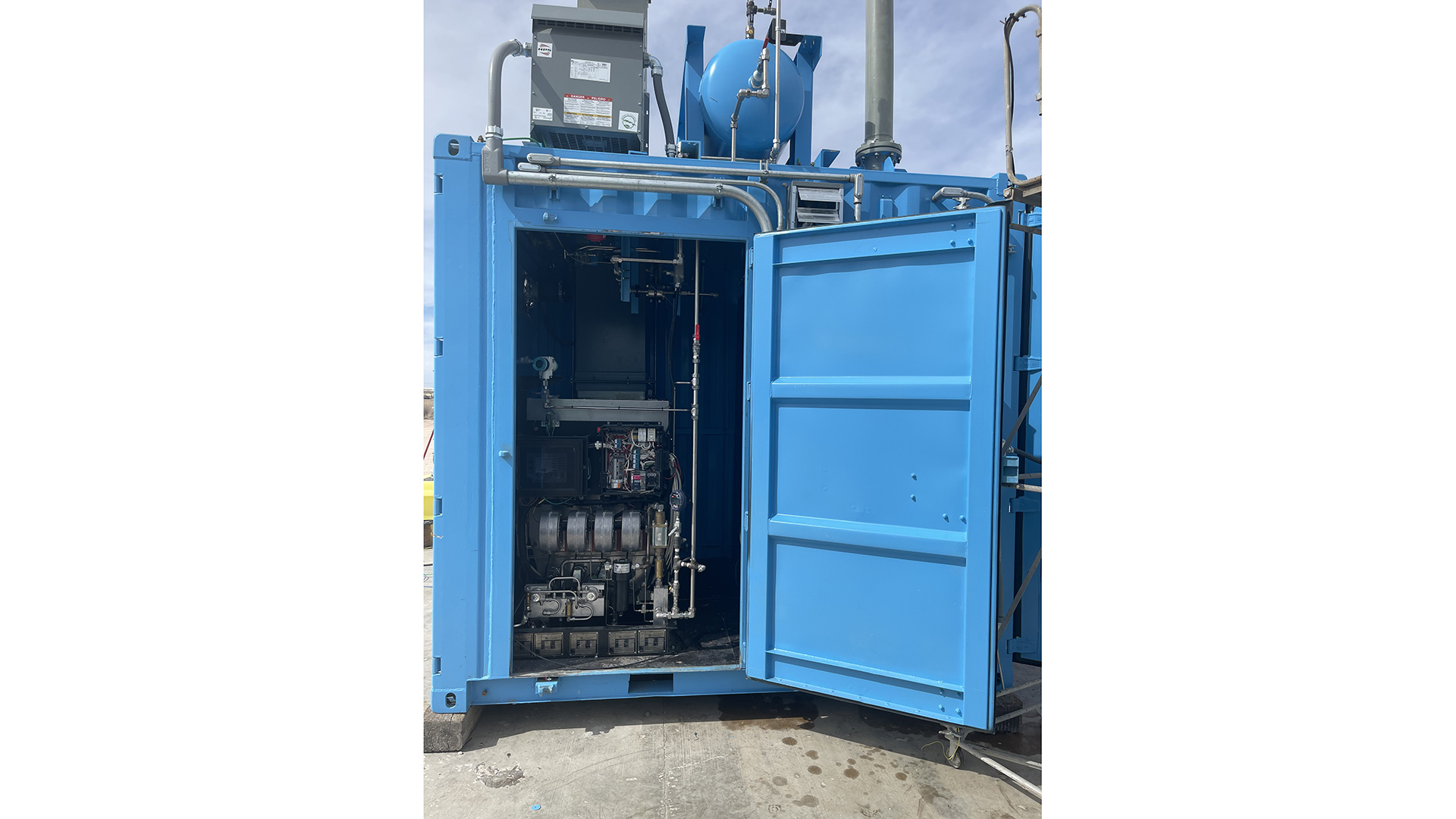
Offering optimum power
The architecture of the self-contained electrical power generation product is straightforward, with only minor differences for a conventional fuel cell power hydrogen generator utilising a supply of compressed hydrogen. Fig. 1 is a 3D model of a demonstration system at Element 1 used for charging electric cars (see also Figs. 2 and 3). The major components are installed within a modified ten-foot shipping container and include one L18 hydrogen generator, one PowerCell PS200 fuel cell module, and a Zinc Five nickel-zinc battery bank (96 kWhrs). Power electronics and cooling (for the fuel cell) are external.
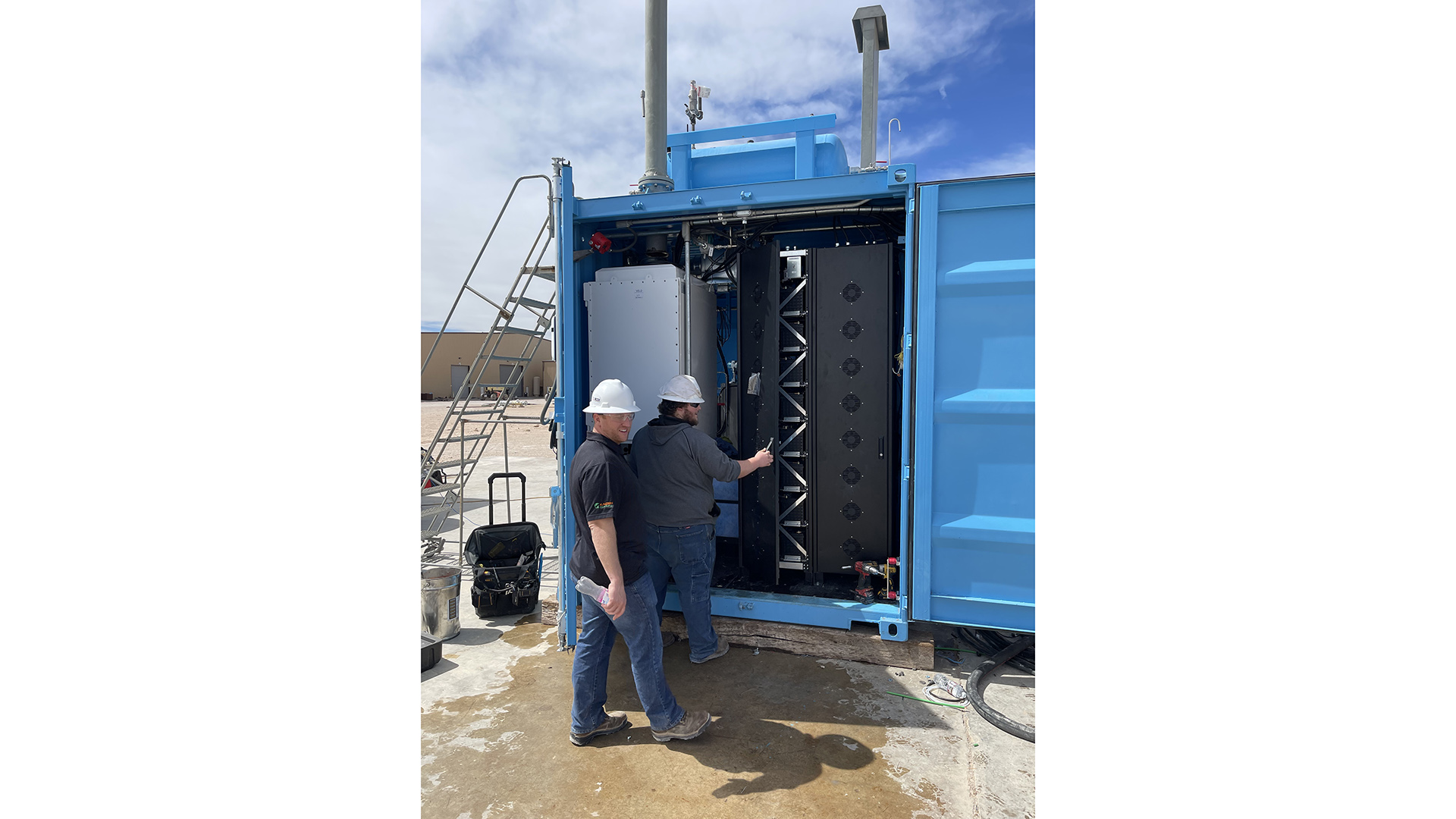
At the maximum rated hydrogen output for the L18 (235kg of hydrogen per day), the fuel cell module will net about 143kW. This is more than enough power to operate the three Level 2 BEV charging cables, plus the Tesla Level 3 charging cable, all at the same time. To demonstrate the full capability of the power generator, it is also equipped with a 480 VAC / three-phase output representative of power required for many building applications. The nickel-zinc battery chemistry was selected over lithium-ion batteries due to the inherent safety of nickel-zinc batteries – they will not undergo thermal runaway and combust.
This demonstration electrical power hydrogen generator is designed to operate in conjunction with the electrical grid or completely independent of the grid. Higher power outputs may be realised by placing multiple hydrogen generators and multiple fuel cells into a single enclosure. A standard 20-foot shipping container is sized appropriately to hold sufficient modules to generate about 450 kW of regulated electrical power.
Environmentally friendly
As mentioned, the methanol-to-hydrogen process is thermochemical in nature rather than electrochemical. Consequently, there is a combustion exhaust stream. However, the exhaust is very clean with respect to regulated emissions, with no sulfur oxides (SOx), no nitrogen oxides (NOx), and no particulate matter (PM). Carbon monoxide emissions are very low at < 1 g/kWhr. Furthermore, if renewable methanol is used as the feedstock, the carbon intensity will be very low or even negative with most types of biogenic renewable methanol (Fig. 4), achieving both environmental benefits as well as contributing to energy security. According to the Methanol Institute, there are more than 80 renewable methanol projects underway globally that are projected to produce more than eight million metric tons of green methanol annually by 2027 (this is in addition to the currently 35+ commercially operating renewable methanol plants worldwide).
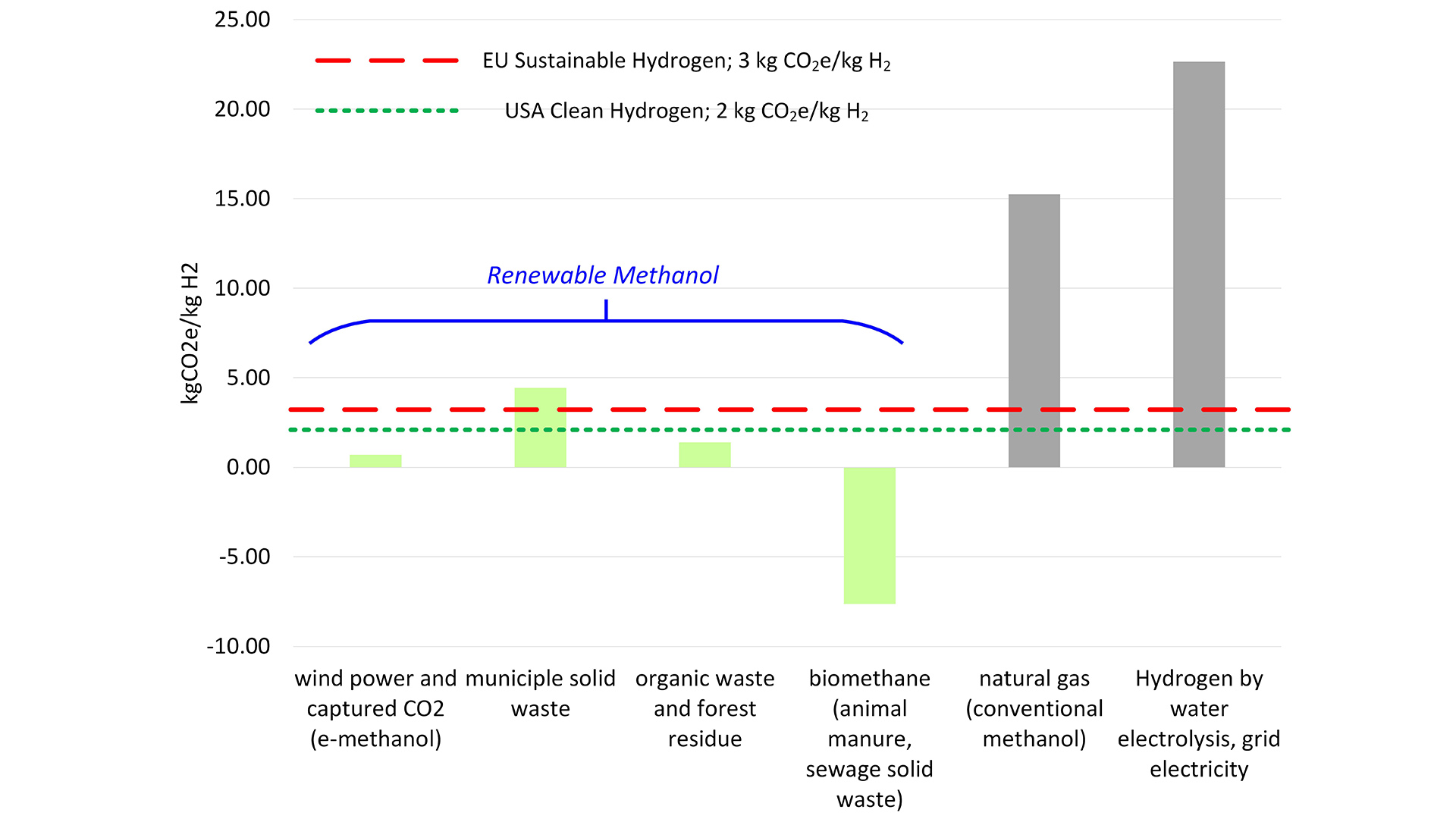
The design of the methanol-to-hydrogen generator (at any scale) is such that we have a unique opportunity to economically capture carbon dioxide far more economically than attempting carbon dioxide capture from the exhaust gas. Removing carbon dioxide from the emissions, even partially, will reduce the carbon intensity of conventional ‘grey’ methanol, and can drive the carbon intensity of hydrogen from renewable methanol into strongly negative numbers.
The hydrogen-depleted waste-gas stream inside the hydrogen generator (rejected at the hydrogen purifier) contains more than 80% of total carbon emissions as carbon dioxide. Plus, this gas stream is at elevated pressure (240 psig to 290 psig) and its composition is 45-50% carbon dioxide. Element 1 and Aramco have been engaged in a joint collaboration programme since 2021 to evaluate the engineering and economics of applying carbon capture to this waste-gas stream. We are now beginning to procure components and plan to assemble the first prototype system scaled to a 235kg hydrogen per day machine before the end of this year.
Although carbon capture is not practical for all commercial applications, it does make sense in certain cases (such as maritime applications and larger stationary hydrogen generation and distributed electrical power) where the captured carbon dioxide has market value or can be economically sequestered.
In summary, producing high-purity hydrogen economically at the point of use with the methanol-to-hydrogen generator leverages the attractive characteristics of hydrogen as an energy-dense and renewable fuel, while largely mitigating the storage and transportation challenges that are preventing hydrogen from achieving widespread utilisation in both stationary and mobility applications.
Please note, this article will also appear in the fourteenth edition of our quarterly publication.