Hans Fredrik Wittusen, CEO of Blastr Green Steel, outlines how the company’s low-CO2 steel will contribute to reducing harmful carbon emissions.
Steel is the world’s most important engineering and construction material. It is used in buildings, infrastructure, tools, ships, trains, cars, bicycles, machines, electrical appliances, and weapons.
However, steel production is also a major source of greenhouse gases, so reducing CO2 emissions in the steel industry is central to tackling climate change. Currently, the industry is responsible for more than 9% of global carbon emissions.
Blastr Green Steel, a Norwegian steel producer, is creating an integrated, decarbonised, and scalable value chain for ultra-low-CO2 steel production. Blastr’s production method will eliminate up to 5.8 million tonnes of CO2 emissions per year, compared to conventional production methods.
Digital Editor Megan Traviss spoke to Blastr’s CEO, Hans Fredrik Wittusen, to discover more about the concept of low-CO2 steel and how steel producers can facilitate this change in the industry.
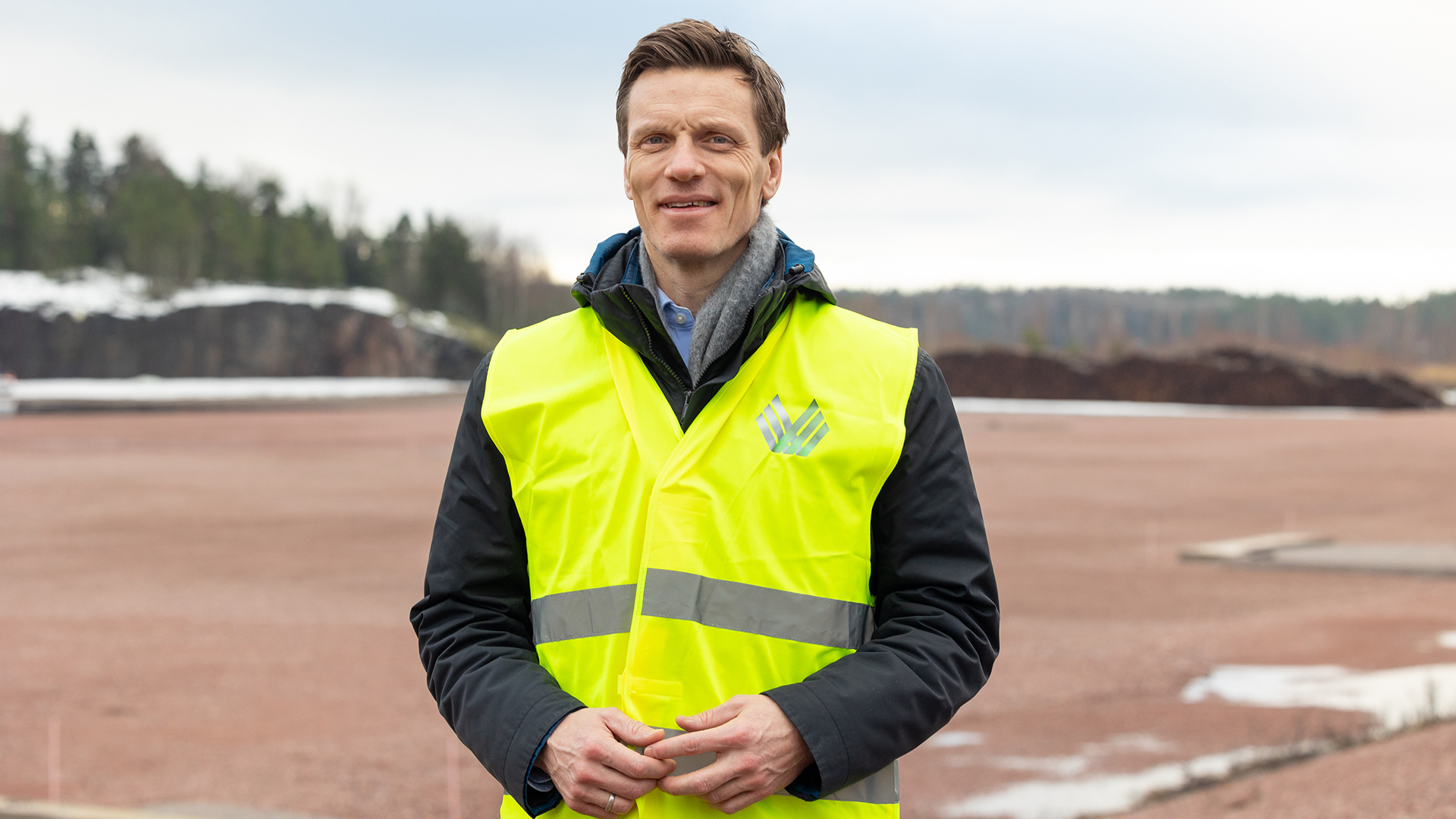
Can you start by explaining the company’s background and outline its key aims and objectives?
The company is two years old today. It started as a project in spring 2021 to explore the opportunity to set up a value chain for steel production.
Utilising the latest technologies, our aim was to produce low-carbon (CO2) steel. This idea was driven by three main objectives.
The first is the immense carbon footprint that the global steel production represents today, which is 8-10% of CO2 emissions. Only the cement industry rivals the steel industry in terms of a single supply chain creating such a huge amount of CO2 emissions globally.
Therefore, the people behind Blastr were driven by finding ways to have a significant impact on CO2 abatement.
In the steel industry, there are a range of technologies and production methods that are proven to significantly reduce steel production’s CO2 footprint. In short, the technology exists, but it isn’t being implemented fully by traditional players.
Blastr has Norwegian origins, and our neighbouring country Sweden has two companies, H2 Green Steel and Hybrit, with similar green steel projects. Two years ago, these companies were gaining recognition for building a steel value chain from scratch. This became inspirational to the people behind Blastr, who wanted to see if this was something that could be done in an even better way than the Swedish alternatives.
After this, the key aims and objectives became clear. We wanted to set up an integrated value chain for steel all the way from the iron ore raw material, producing direct reduction pellets as feedstock for the steel plant.
Blastr wanted to do this with the best technology available to get the lowest CO2 footprint possible. Initially, the aim was to reduce Scope 1 emissions from steel production by 95%.
What is the definition of green steel?
There is actually no definition. However, there are a multitude of green steel projects in the world and all steel producers are working on green steel projects.
The most basic definition is steel that is produced with a lower CO2 footprint than the current, conventional methods. With conventional methods, using fossil fuels like coal and oil produces high CO2 emissions. For each tonne of steel produced, this method emits 2.6 tonnes of CO2, if one counts scope 1, 2 and 3.
With ‘green steel’, we don’t know exactly how much of that steel is green as the definition hasn’t been captured yet. Therefore, we need transparency on how low of a CO2 footprint can be achieved with these production schemes.
The term we have coined for our project is ‘ultra-low-CO2 steel’. For Blastr, ultra-low means reducing emissions from 2.6 tonnes of CO2 by 90% to about 300kg of CO2 across scopes one, two, and three.
Could you outline some of the challenges associated with the transition into low-carbon steel?
As mentioned before, the technology to do this already exists. Therefore, it’s not a matter of needing to develop new technology that must go through testing, piloting, and proving the concept.
There is a huge demand for low-CO2 steel. From a regulatory standpoint, there are no specific requirements or rules. The automotive sector, in particular, has a huge demand and is willing to pay a premium on low-CO2 steel. If the demand is there, and the technology is there, then what is the problem?
The challenge is two-fold. One challenge is that current steelmakers are very slow in their transition. They have legacy assets, existing production lines, and huge capital expenditures.
However, there has been too little regulatory pressure to reduce these footprints. So they keep producing without the economic incentive to make this transition because it’s an extremely costly transition for them. There is no tweaking involved – they have to decommission their whole plant structure and build new ones from scratch.
The main challenge is the lack of access to fossil-free energy. To reduce the CO2 footprint, there needs to be fossil-free energy alternatives. Even if / when the current steel makers set up these new technologies, they still don’t have access to clean energy. This means they still won’t be able to reach ultra-low.
These issues always lead to discussions about how we can solve them.
In the Nordics, we have hydropower, wind, solar, and nuclear providing fossil-free energy. However, this is not always the case across the rest of the world. For the whole world to transition to green, ultra-low-CO2 steelmaking, you need to believe in a substantial buildout of hydropower and wind, which is probably not physically realistic, or there needs to be a resurgence in nuclear energy.
What changes are needed to accelerate the transition to low-carbon steel and how is Blastr supporting this?
Having verified that these technologies exist, it’s obvious this transition is necessary.
The new players that don’t have legacy assets can be agile and quick in scaling up these existing technologies. So players like Blastr, H2 Green Steel, and Hybrit are willing to build these up from scratch and take the lead, which satisfies the huge demand for green steel.
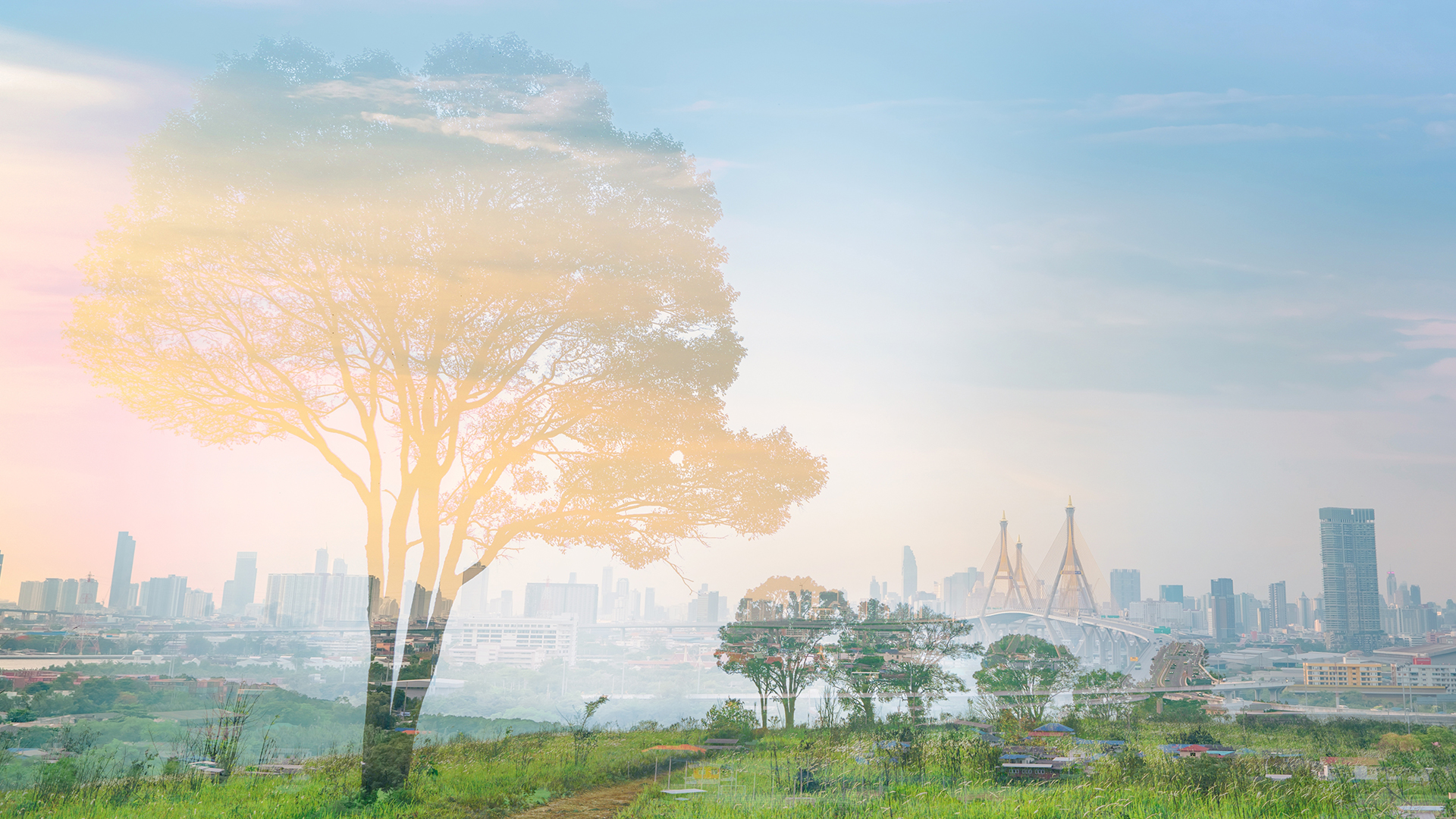
H2 Green Steel is planning five million tonnes, which is a substantial volume and will have an immediate impact. The steel we will produce and the CO2 reduction associated with this is as much CO2 that is emitted from private automobile transport in a country like Finland or Norway. It will have a huge impact.
There also needs to be more pressure on steel companies to follow suit and make these changes quickly. There is some movement on the regulatory side. For example, carbon taxes will be hitting steel producers increasingly after 2026 as free allowances are removed, meaning they will incur higher costs associated with the production of high-emission steel.
What do you see as the key success factors for producing ultra-low-CO2 steel?
Firstly, we need stable access to some critical inputs at competitive cost levels and in large quantities. For these technologies to work, large amounts of hydrogen need to be used, and it needs to be produced with fossil-free energy.
There also needs to be stable access to raw materials going into the steel production. There are two different streams. There’s iron ore and scrap steel, which both go into production. There are huge volumes in the market, and the demand is going to keep rising as this transition unfolds.
For players like us, it’s a critical success factor to capture those inputs in a sensible way through contracts and partnerships. This enables us to produce low CO2 steel at a reasonable cost.
Another success factor is infrastructure. There are several logistics, such as the shipping and freight of millions of tonnes of raw materials and products. They need to be transported by ship to be effective, and ports have to be ice-free. We’re operating in the Nordics because of the fossil-free energy sources but, because of the climate, we need to make sure the ports are ice-free. There are a lot of details on the logistical side, which amount to potentially very high costs if they aren’t solved correctly.
To set up this integrated supply chain, Blastr is seeking to own and operate the different pieces of the puzzle. Sourcing iron ore and producing DR-pellets is the first step. Then, in terms of steel production, we want to produce our own hydrogen to secure the hydrogen supply.
We have an integrated strategy entailing substantial capital expenditures and many things that we need to put in place. But we believe that this strategy is key to assuring our customers and investors that we will be able to produce high-quality steel at low costs for several decades.
What can we expect from Blastr in the near future?
Over the next two years, we are designing the setup of these different parts of the value chain. They are huge projects, which require around €5-6bn in investments.
We are designing, planning, and getting permits, aiming to have a final investment decision in 2025. Expect a lot of announcements from Blastr about the key agreements needed to put these into place. Suppliers expect investment decisions to be made within around two years.
To deliver on these plans, we want to build the organisation and get the best people for the job. Hopefully, we’ll be able to make those types of announcements over the next two years to really accelerate the project.
Is there anything else you’d like to add?
There are many players and stakeholders that share Blastr’s drive and ambition. Politicians, authorities, grid operators, technology suppliers, and end customers all want their footprints to be reduced.
This creates a high probability that this will succeed, and then it’s up to companies like Blastr to put all these pieces together and execute it.
However, it’s really inspiring to work with great partners and stakeholders. Over the next year, we’ll be bringing more investors on board, and, hopefully, we can be clearer about the key partners that are also on board.
Please note, this article will also appear in the fourteenth edition of our quarterly publication.