Stephen Gifford, Chief Economist at The Faraday Institution, discusses the importance of the UK in establishing a domestic lithium-ion battery recycling industry.
As the UK transitions to a greener economy, establishing a domestic lithium-ion battery recycling industry becomes increasingly crucial. This is highlighted in the Faraday Institution’s recently published Faraday Insight 20, which provides an overview of the global recycling market’s scale, the primary recycling processes for batteries, and the economic dynamics of battery recycling, focusing on the complexities of maintaining recycled material value. It also examines advancements in the UK and European recycling sectors, exploring both the opportunities and challenges for the UK to emerge as a prominent hub for battery recycling.
Gifford spoke to Innovation News Network to provide further insights on the report and outline the trajectory of the UK’s recycling landscape.
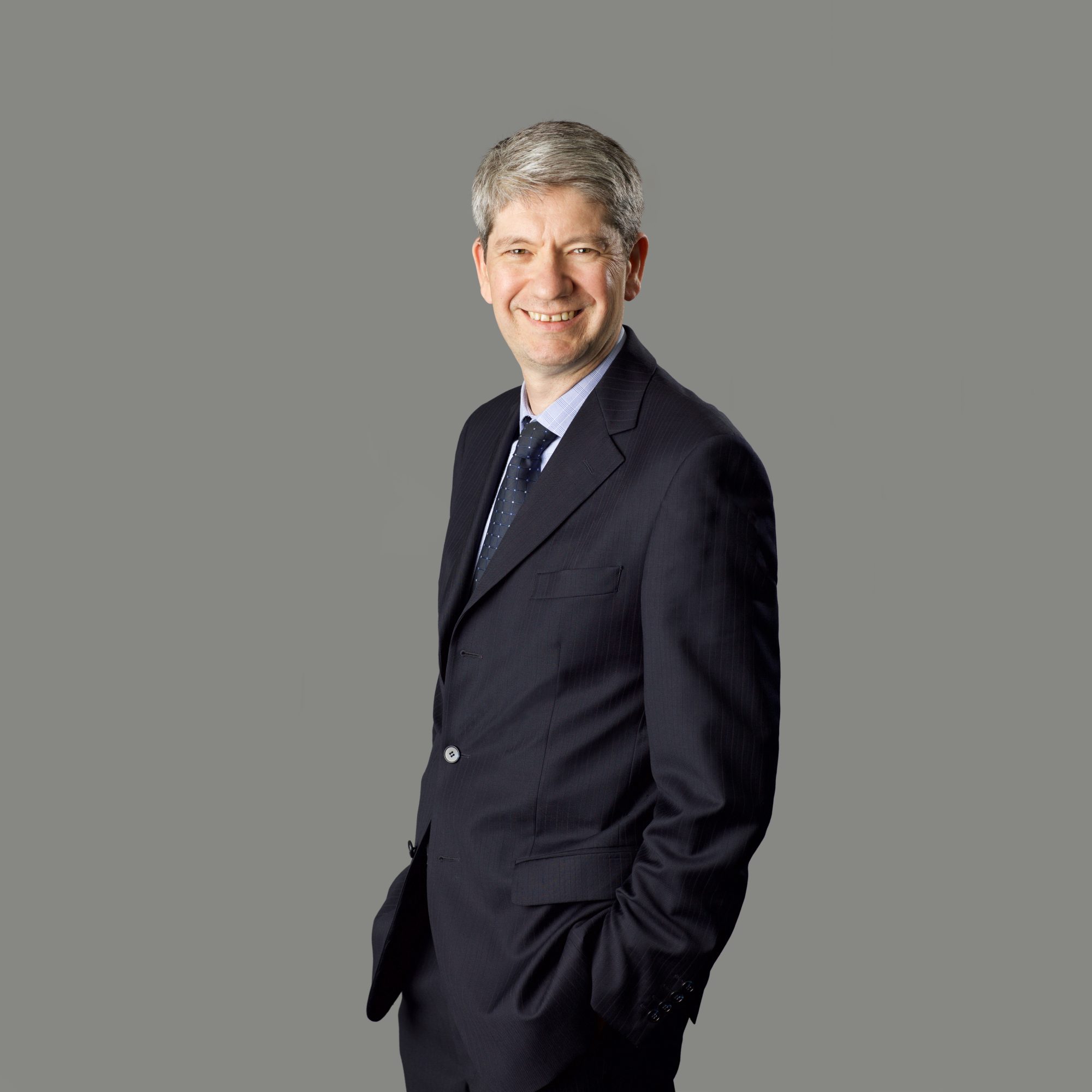
Motivations behind establishing a domestic lithium-ion battery industry in the UK
Establishing a domestic lithium-ion battery recycling industry in the UK would create a circular battery economy, reducing dependency on importing critical materials such as lithium, graphite and cobalt. It would lower carbon emissions, reduce environmental costs, and reduce the need to mine virgin raw materials around the world, as well as mitigate the risks associated with global trade disruptions seen during the pandemic and energy crisis.
Developing and implementing advanced lithium-ion battery recycling technologies and processes will ensure the consistent and efficient treatment and management of used materials, leading to increased efficiency, a reduction in costs and the development of a resilient and sustainable supply chain. Globally, recycling could supply 39% to 57% of the lithium, cobalt and nickel demand for batteries by 2040.
There is a danger that many of the environmental gains from the transition to EVs will be lost if the UK fails to manage the increasing volumes of electric vehicle (EV) lithium-ion batteries at the end of their useful life. Recycling is just one part of a circular economy strategy for batteries, which can also be reused or repurposed before material recovery or disposal. Reuse and repurposing are often preferred to retain processing value.
Risks to the UK from outsourcing recycling to other countries such as China
Outsourcing recycling abroad poses several risks to the UK, particularly the potential vulnerability to supply chain disruptions, which could arise from geopolitical tensions, trade restrictions and logistical challenges. Dependence on external lithium-ion battery recycling facilities will also increase UK firms’ exposure to fluctuations in global commodity prices, policy changes in other nations and different environmental and safety standards.
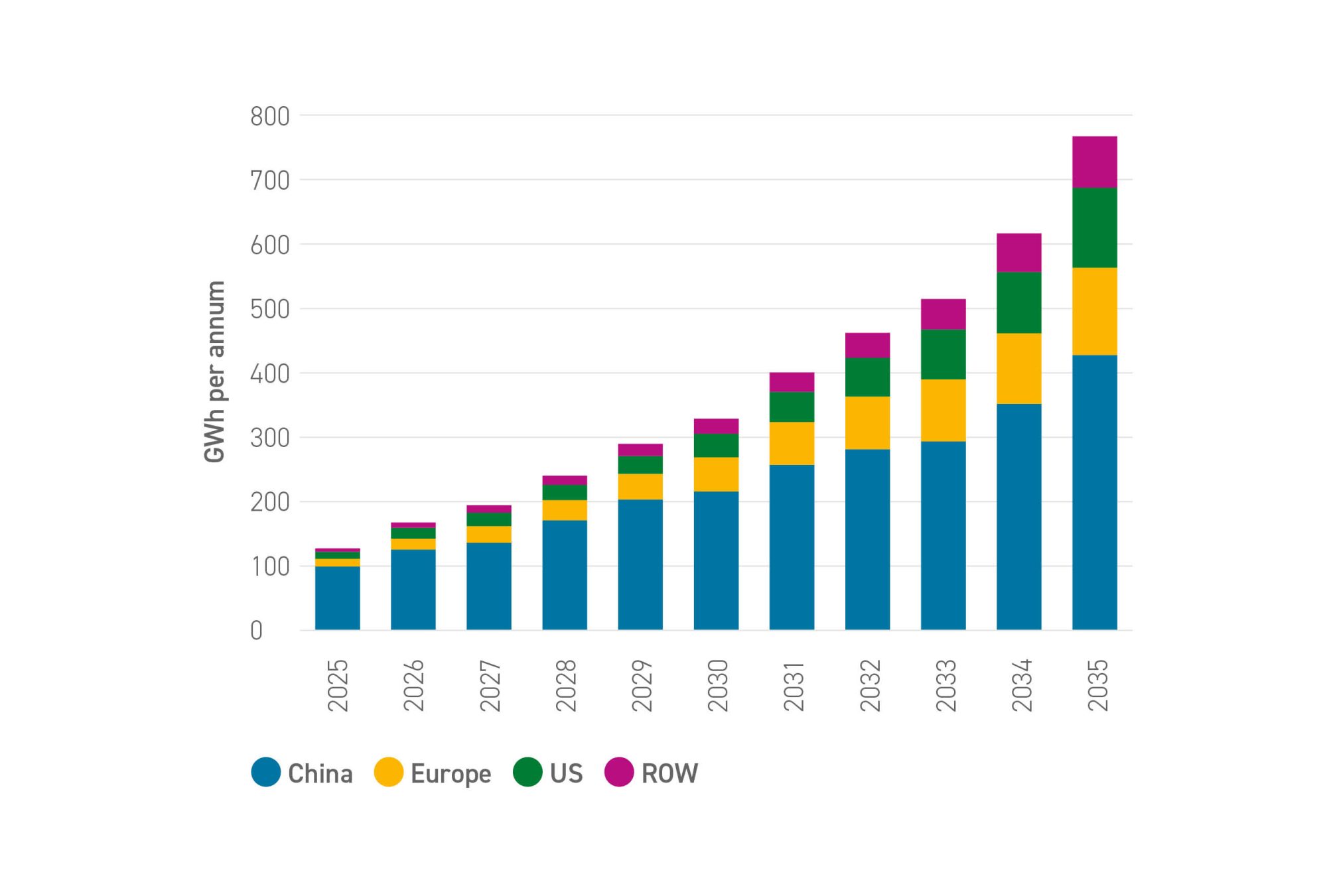
Above all, relying on foreign recycling capabilities will almost certainly delay or even prevent the development of the UK’s own recycling infrastructure and the creation of a closed-loop system. It could also put the 100,000 metric tonnes per annum of lithium battery recycling capacity already existing or announced at risk.
UK’s progress in recycling this significant volume of batteries
The UK is making progress but is not fully on track to handle the significant volume of EV batteries reaching end-of-life in the 2030s. Currently, the UK has six publicly announced pre-treatment plants and three black mass treatment plants, but most capabilities are still either in planning stages or operating on a pilot scale. There is still time to develop a UK industry as recycling volumes are anticipated not to increase sharply until the mid-2030s, driven by end-of-life EV batteries.
Because the current volumes of end-of-life EV batteries are low and because of the many uncertainties involved in the commercialisation of recycling, government intervention is necessary to help establish the first EV battery recycling facilities in the UK. Indeed, the UK government has recognised the need for a domestic recycling industry and supported various R&D initiatives to scale up technologies. However, extensive legislative and policy changes are needed to match the expected demand, including streamlined permitting processes and incentives that support second-life applications and regulations to ensure the safe handling of lithium-ion waste streams.
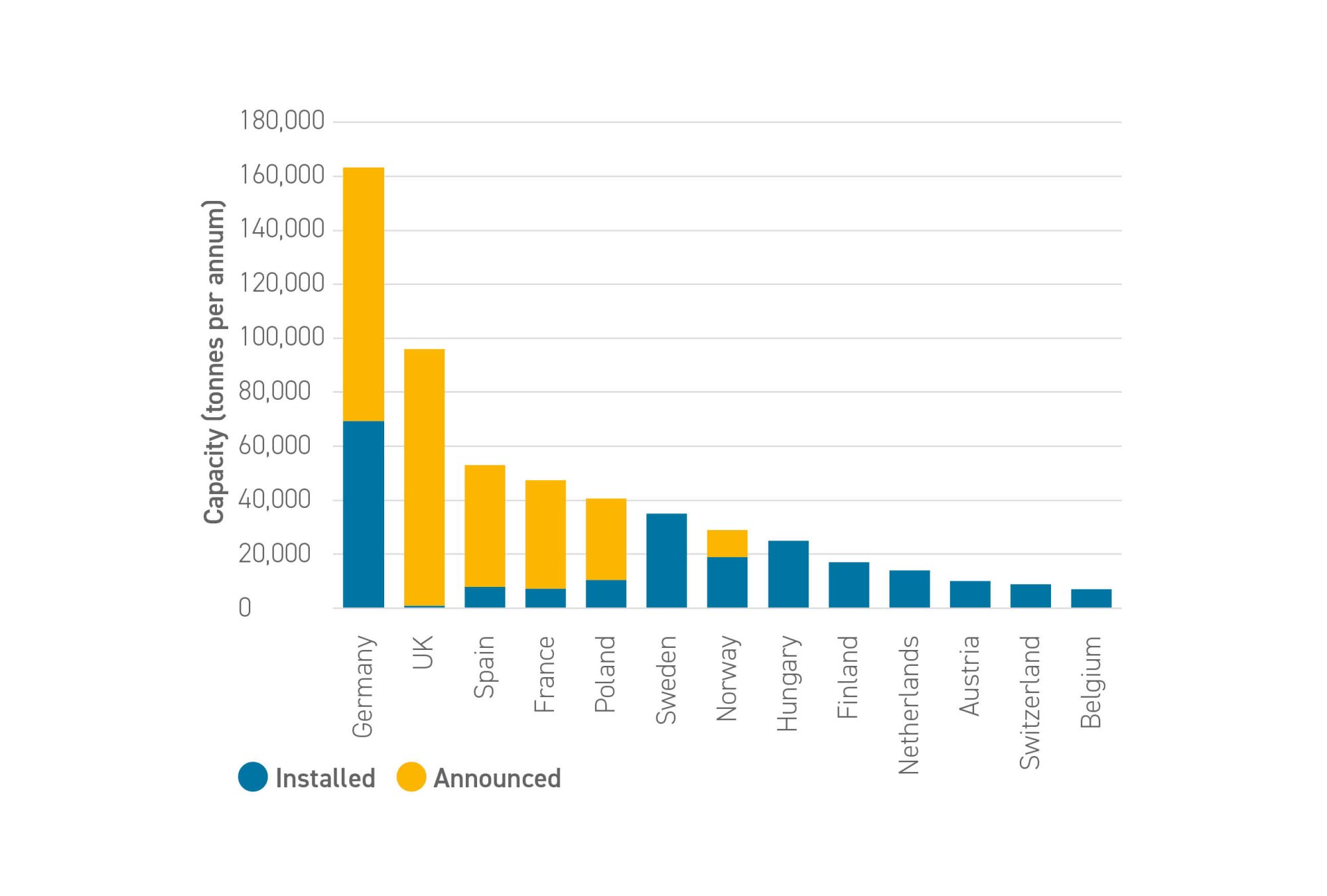
Key battery recycling technologies
Creating a domestic recycling industry in the UK will likely require a combination of three technologies: pyrometallurgy, hydrometallurgy and direct recycling. Each method has distinct advantages and challenges:
- Pyrometallurgy, while this is a mature technology that is capable of processing mixed waste streams, has lower lithium recovery rates and high energy requirements. It is a relatively simple process with short reaction times and a lower consumption of concentrated acids than hydrometallurgy. Coupled with a large treatment capacity and scalability, it has matured into a widely adopted recycling process.
- Hydrometallurgy offers higher recovery rates and less energy use but involves complex chemical processes. The process delivers a high recovery rate of over 98% for copper, nickel and lithium. The release of volatile organic compounds and highly corrosive hydrogen fluoride, however, poses a safety challenge, which has been a hurdle to widescale industrial development.
- Direct recycling, still in its early development stages, promises high material recovery but faces challenges in scaling and adapting to various cell chemistries. Direct recycling would have numerous benefits such as retention of economic value, lower environmental impact due to the absence of harsh chemicals and the need for fewer downstream processing steps.
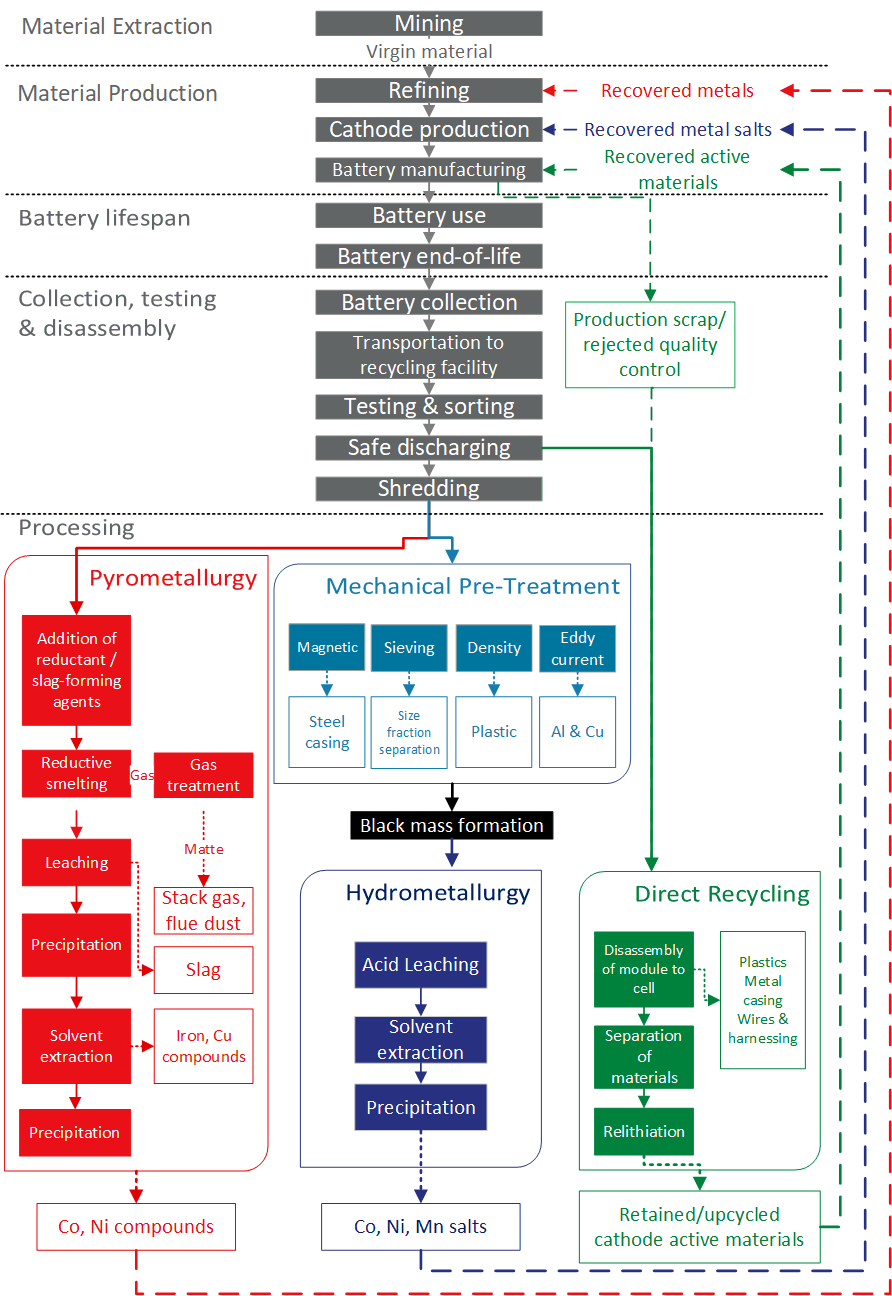
A combination of these technologies will allow the UK to leverage the strengths of each method, ensuring efficient and cost-effective recycling processes that can handle diverse battery chemistries and designs.
Importance of expediting planning and approval processes
Expediting planning and approval processes are crucial for the UK to scale up its recycling projects in time to meet future demand. Streamlining the environmental permitting process, including obtaining planning permission and battery treatment operator permits, is essential. Delays in these processes could become a bottleneck, hindering the timely development of necessary recycling infrastructure. Improved alignment and understanding between industry and permitting agencies could expedite these processes, ensuring that safety standards are upheld while efficiency is improved.
Developing skills and the role of automation and AI
To establish a lithium-ion battery recycling industry in the UK, it is crucial to develop a skilled workforce. Current UK capabilities are mostly in the planning or pilot stages and in similar operations such as electronic waste and precious metal recovery. Skills in handling, management and transfer of lithium-ion waste streams will need to be improved.
Automation and AI could enhance the efficiency and safety of battery disassembly and recycling processes, providing a quicker, safer and more accurate method for scaling processes. Current research is exploring the possibility of automation and advancements in artificial intelligence, and it is rapidly progressing to enable batteries to be sorted based on visual characteristics, including size, colour, and geometry, which can improve throughput and profitability. Delivery of these technological improvements will require skills in handling advanced equipment and understanding AI applications.
Importance of design for recycling principles and standardised battery designs
‘Design for recycling’ refers to the strategy of designing battery packs, modules and cells to optimise recyclability and minimise waste. This provides automakers, manufacturers and recyclers with a consistent framework to simplify and safely dismantle cells at their end-of-life. This focus on consistency in pack design across manufacturers and countries could significantly reduce the time and costs of recycling. Automation could potentially reduce the cost of recycling a Nissan Leaf battery pack from US$ 0.64 per kg to US$ 0.02 per kg.
New batteries are increasingly being designed with second-life applications in mind, such as applications that support grid-based energy storage systems, load-shifting, peak-shaving, and energy backup for intermittent renewable power generation. Second-life batteries provide an alternative through repurposing, reconditioning and reuse, offering cost-effective solutions for grid storage.
Standardisation and universal labelling could enable the automatic sorting of batteries into distinct groups based on structure or chemistry. The International Dismantling Information System (IDIS) database provides manufacturer-specific safety information and end-of-life dismantling information. This could be expanded beyond conventional lead-acid batteries to encompass lithium-ion battery testing, discharging and dismantling for recycling.
Integration of an IDIS-like database within a battery passport system could further enhance transparency by disclosing the battery’s history, composition, origin and guidelines for safe handling and recycling. Extended producer responsibility regulations that support a move to a circular economy model are also crucial, ensuring the safe and effective reuse of EV batteries and imposing increasingly robust recycling targets.
Changes to regulation and policy needed to maximise UK recycling
The importance of battery recycling has been recognised in the recently published UK Battery Strategy and supported via a number of R&D initiatives. To further strengthen the UK’s position in the global recycling market and enhance supply chain resilience, additional research and policy changes are needed to maximise recycling technologies, including:
- Research to improve recycling technologies, focusing on new direct recycling methods and enhancing material recovery;
- Enhance recycling processes for more efficient recovery rates and reduced environmental impacts;
- Expand research on second-life applications, focusing on feasibility and safety for EV batteries;
- Adopt design for recycling principles to standardise and simplify battery designs, improving disassembly efficiency;
- Develop initiatives to encourage battery reuse and repurposing;
- Provide financial support to recycling facilities and incentives for SMEs and startups;
- Develop strategy and policy to reduce reliance on imported raw materials and spur UK battery supply chain innovation; and
- Strengthen domestic capabilities to handle future end-of-life EV battery designs and chemistries.
Establishing a UK-based lithium-ion battery recycling industry is crucial for creating a resilient, sustainable and secure supply chain. It will help secure the supply chain for raw materials needed for EV battery production and ensure sustainable management of used materials. Currently, recycling is labour-intensive and costly, influenced by battery chemistry, commodity prices and recovery efficiency. Developing advanced recycling technologies and processes will increase efficiency, reduce costs and foster a circular domestic battery economy. Overall, scaling up the UK recycling industry will require the construction of large-scale recycling plants, research and innovation and supportive government policies.