FRACTION develops a novel integrated biomass biorefinery approach to maximise the purity and quality of cellulose, lignin and hemicellulose, demonstrating their upgrading into high-added-value products.
The conversion of lignocellulosic (non-edible) biomass is a promising alternative to replace petroleum as feedstock to produce carbon-based products. The biggest challenges to implementing a biomass biorefinery that can compete with petroleum refineries have been related to the economics of the biomass-derived processes and not to technical limitations or the quality of the products achieved.
To improve the economics of a biorefinery, we need to achieve the complete utilisation of the biomass feedstock by getting value from all the components despite their different chemical structures, i.e. cellulose, hemicellulose, and lignin.
To meet this goal, an efficient fractionation technology that simultaneously maximises the yield of each component without decreasing their value is necessary, so they can be upgraded separately according to the best technology for their individual structure, and this is what we are doing at FRACTION, funded by Bio-Based Industries Joint Undertaking (BBI JU).
FRACTION’s biomass refinery process
The first step of our process is done at the Institute of Catalysis and Petrochemistry (ICP-CSIC), a Spanish public research institute. We obtain our biomass from Stora Enso, a Finnish pulp & paper company (wood chips from different hard and soft wood, bagasse and old corrugated cardboard). To fractionate, we use a solvent mixture of water and gamma valerolactone (GVL), an organic chemical derived from biomass, so we do not need to dry or grind the biomass before processing, eliminating pre-treatment steps and saving a lot of energy and money.
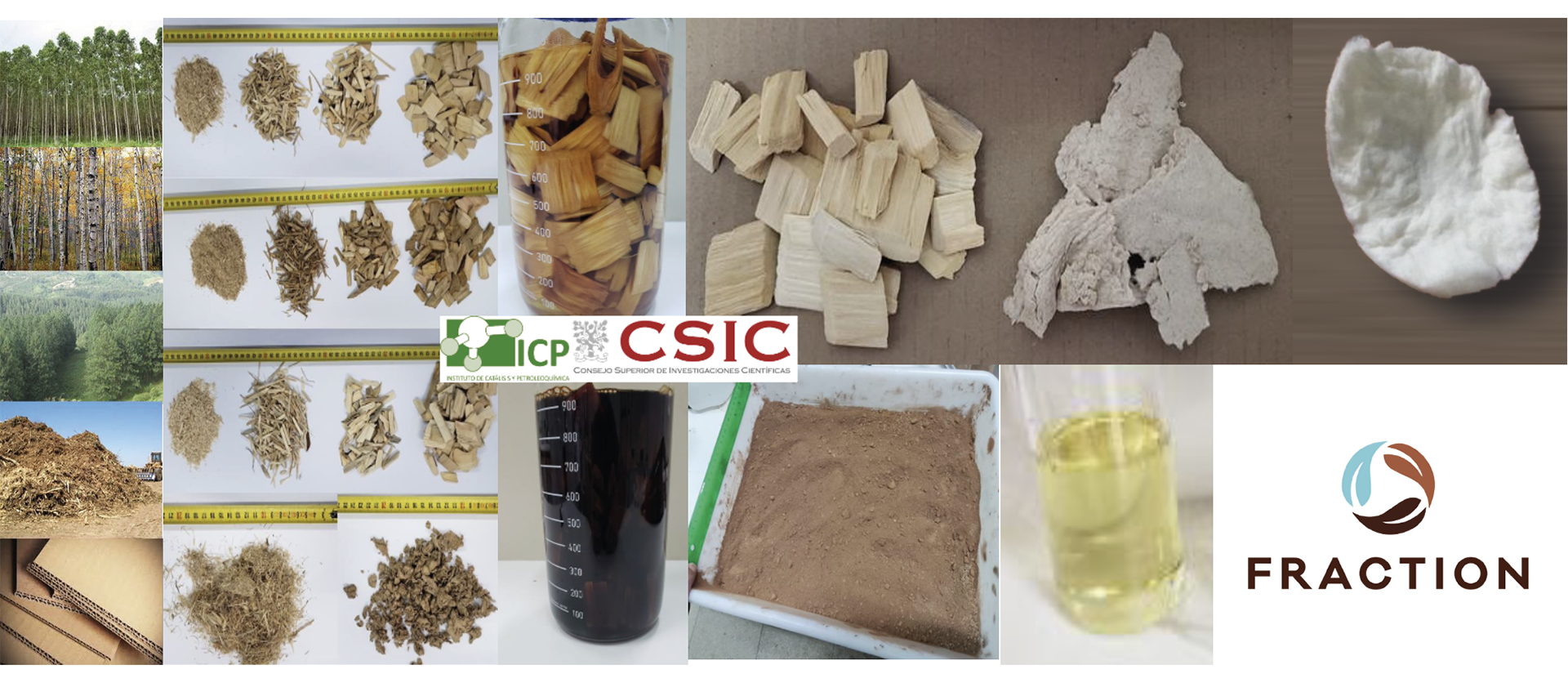
Using an organic solvent has disadvantages, such as the need to recover and recycle it.
However, in the case of GVL, these are outweighed by the advantages. When we add GVL, the hydrolysis reaction, which separates hemicellulose and lignin from the cellulose of the biomass, is faster than in pure water. So, we can work at milder conditions and thus solubilise hemicellulose and lignin without damaging them or the solid cellulose that is left behind.
At ICP-CSIC, we can solubilise >90% of the hemicellulose and the lignin, leaving solid cellulose with >93% purity and >90% yield. We can also work at high biomass loading (>20 wt%), which allows us to reduce solvent use and improve the economics of the process.
In the next step, we separate the lignin from the hemicellulose. The lignin we produce is high purity (>97%). The third fraction of the biomass contains hemicellulose, a heterogeneous polymer composed of C5 and C6 sugars. In our process, this stream only needs to be concentrated before transforming into furfural, a versatile chemical building block with high yields (>80%).
To demonstrate the value of cellulose, hemicellulose, and lignin, we are developing several new downstream conversion technologies at FRACTION to synthesise and validate novel building blocks. Hereby, we cover the whole value chain, from biomass to final products, including end-of-life options and techno-economic evaluations.
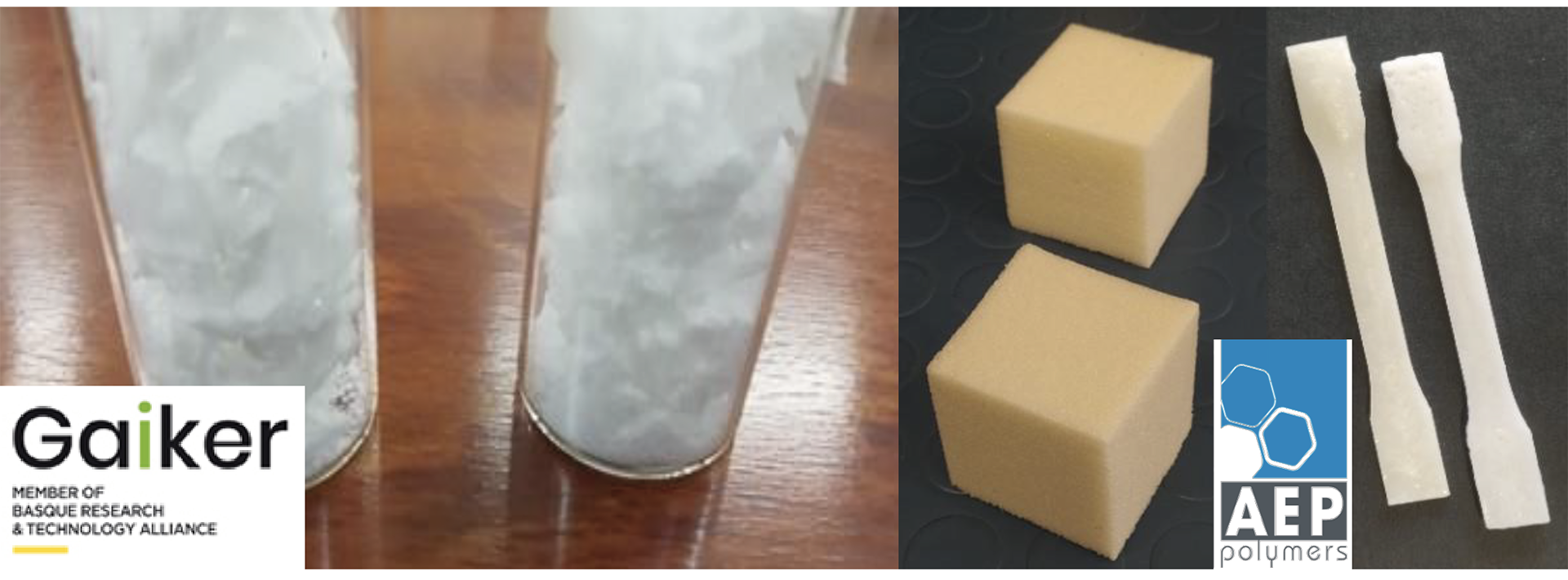
Demonstrating value
Stora Enso has demonstrated that the cellulose pulp produced can be bleached to full brightness and is evaluating further upgrading strategies to produce high-quality dissolving pulp, for example, for textile products.
Spanish RTO FUNDACION GAIKER produces poly (alkylene succinate)s that can be used for coatings and adhesives. As feedstock, it uses succinic acid, coming from the oxidation of furfural, and 1,5 pentanediol, coming from furfural hydrogenation, both catalytic reactions being studied at ICP-CSIC.
Italian SME AEP Polymers is also working on valorising the furfural stream by developing multifunctional polyols, acrylates, and methacrylates. Its work focuses on developing components for formulating acrylic coating, polyurethane foams, and adhesives, while maximising the bio-based content of these products.
An alternative for the valorisation of hemicellulose is being studied at the Rey Juan Carlos University (URJC). Its focus is on biomass, of which hemicellulose is rich in C6 sugars instead of C5 and thus has low potential as feedstock for furfural production. After separating the sugars from the GVL solvent as concentrated aqueous solutions (>150 g/L of sugars), URJC can produce α-hydroxy esters that can be used as green solvents or building blocks for other molecules.
The university has demonstrated that this transformation can also work with C5-C6 sugar mixtures, allowing valorisation through this pathway of different hemicelluloses.
Another option is the isomerisation of the C6 sugars to fructose. URJC has developed a process based on the isomerisation-glycosidation of sugars, allowing alkyl ketoxides to produce high yields (>90%). This fructose is used by Swiss SME AvaBiochem to produce HMF and FDCA, a molecule that is used to produce polyethylene furoate (PEF), an equivalent of the PET used to make most plastic bottles.
The third stream, lignin, has attracted a lot of attention lately, as its valorisation is key for the economic success of any biomass biorefinery. At FRACTION, RTO VTT in Finland is working on the hydrogenolysis/solvolysis into monomers and low molecular weight products that can further be used in resin synthesis.
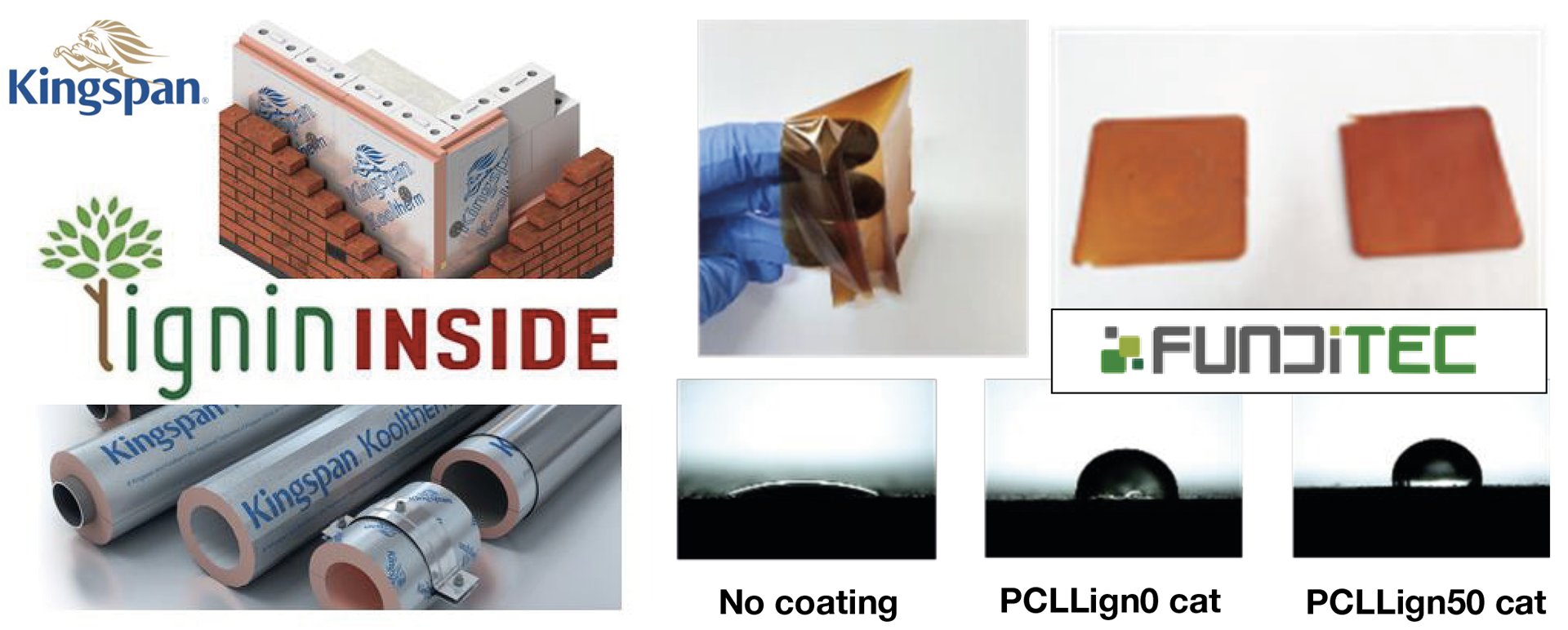
Another possibility to valorise the lignin is the catalytic oxidation to high-value molecules such as vanillin, which Spanish RTO FUNDITEC is studying. The company is also working on synthesising lignin-based polyurethanes for coatings, adhesives and elastomers, which can have antimicrobial, anticorrosion, and other beneficial properties such as changing the hydrophobicity of coatings.
Finally, Kingspan Insulation, one of the five operating divisions of Kingspan Group, a world-leading manufacturer of insulation solutions for the building envelope, pipe and ducting services, district heating and cooling, as well as custom moulded packaging solutions, is using the lignin to increase the sustainable content of end products.
At FRACTION, we valorise lignin into a biobased replacement for phenol, a monomer used for manufacturing phenolic resins before curing and expanding them to phenolic insulation foams, traded as KOOLTHERM®.
Besides demonstrating the technical feasibility, project partner IFAU is doing a market assessment to design the strategy for commercialisation. To validate the environmental benefits of implementing this biomass biorefinery, GAIKER and URJC are working on the sustainability of the process and end-life of the products, while PROCESS DESIGN CENTER BV is working on the techno-economic evaluation. More information about implementing the dissemination & communication activities can be obtained from CLIC.
This research was funded by the Biobased Industries Joint Undertaking (JU) under the European Union’s Horizon 2020 research and innovation program under grant agreement No 101023202. The JU receives support from the European Union’s Horizon 2020 research and innovation program and the Bio-based Industries Consortium.
Please note, this article will also appear in the sixteenth edition of our quarterly publication.