GREEN14’s plasma technology facilitates greener, cheaper silicon production for solar, semiconductors, and batteries.
GREEN14, a startup established in 2021, is poised to modernise silicon production. The Sweden-based firm aims to decarbonise and reshore silicon production for semiconductors, battery electrodes, and solar cells within Europe and the US, reducing emissions by up to 95%. Currently, about 90% of silicon production is concentrated in China, but GREEN14’s innovative approach seeks to change this dynamic, positioning Europe as a key player in the field.
GREEN14’s focus
The company’s focus is not just on shifting the geography of production but fundamentally altering the production process itself. Traditionally, producing pure silicon from silicon dioxide involves a carbon-intensive process, using an electric arc furnace at high temperatures, followed by the Siemens process in which refinement takes place. These methods are both energy-intensive and release significant amounts of carbon dioxide through direct and indirect emissions. This is similar to the shift from outdated iron production methods using blast furnaces, which the green steel movement aims to modernise. GREEN14 aims to overhaul silicon production entirely by making it greener and cheaper than competitors with the added benefit of a transparent supply chain.
The company’s technology drastically reduces the operating cost by up to 50% and the embodied carbon by up to 95% in the silicon production process by implementing a novel method that eliminates direct carbon dioxide emissions and dramatically decreases energy requirements. Up to 80% of the embodied emissions come from electricity in the main process, therefore, reducing energy consumption in the value chain will reduce emissions and the cost of production.
Moreover, moving the production to markets with large shares of renewable electricity allows for a significant abatement of carbon emissions. This approach positions the company to be competitive in the European, US, and global markets outperforming traditional methods in both cost and sustainability.
GREEN14’s patents also apply to 16 of the materials listed in the EU’s Critical Raw Materials Act including copper, cobalt, and titanium. The company aims to produce silicon and silane (silicon gas) for the solar, semiconductor, and battery markets while its business model is to licence out its plasma reduction-refinement (PRR) technology where the processing of high purity metals is concerned. Copper is a large market to which it could licence its technology. For example, hydrogen plasma reduction refinement can be used to form ultra-pure copper from a mixture of copper oxide and recycled copper.
Company tools and assets
A key component of GREEN14’s strategy is the use of Artificial Intelligence (AI) to expedite research and development. The company applies reduced-order modelling wherein AI neural networks are applied to computational models to significantly accelerate the development process. This AI-driven approach enables the company to quickly iterate and improve its technology, reducing both the time and cost typically associated with R&D in the silicon production industry.
The raw material for GREEN14’s process is quartz, which is abundantly available. This is processed with hydrogen in the form of plasma. The emissions of GREEN14’s operations are minimised through the use of green hydrogen – hydrogen produced with renewable electricity – but its emissions are not tied to the use of such low-emission hydrogen. Hydrogen is used in relatively low amounts in the process: Less than 10% by weight per kilogramme of silicon. To be optimal, sites with available renewable electricity for industry is essential for the startup’s base of operations. Sites in the EU, US, India, and Australia are being considered for GREEN14’s first factory.
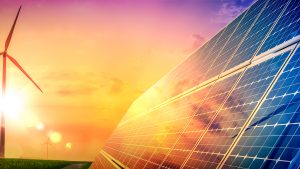
The company’s pilot plant, under construction with the collaboration of KTH Royal Institute of Technology in Stockholm, is expected to initially produce up to five kilogrammes of silicon per hour, with plans for a larger demo plant capable of producing up to 100 kilogrammes per hour. This scaling up is not just a demonstration of the technology’s viability but a stepping stone to larger production efforts in the EU in line with the Critical Raw Materials Act. Silicon is classified as a critical raw material within this new piece of Brussels legislation, as it is a key factor in semiconductors for computing and renewable energy devices, including solar panels, batteries, and wind turbines.
GREEN14’s technology development is not without its challenges. Scaling up plasma metallurgy to industrial levels, particularly where megawatt-scale equipment is required, faces significant limitations due to the limited number of suppliers capable of producing such high-powered plasma equipment. This can lead to longer lead times for equipment procurement and potentially higher costs due to the lack of competitive pricing. The dependency on a few suppliers also poses risks related to supply chain disruptions. To address this, GREEN14 is working closely with several suppliers of plasma equipment, and investing in the development of alternative plasma generation technologies. Furthermore, the limitations in science around modelling plasma, especially in the context of plasma metallurgy, form a crucial area of ongoing research. Plasma behaviour is incredibly complex and dynamic, making accurate modelling a difficult task. GREEN14 prioritises its in-house simulations for optimising its patent pending processes and works to integrating this progress with its AI development roadmap.
Interestingly, GREEN14’s technology also encompasses the recycling of silicon. Retired solar panels, which degrade over time, can be reintegrated into the company’s silicon production process. This circular approach not only reduces waste but also maximises the utility of existing materials. The waste from silicon wafer production, known as kerf, is also well suited to be integrated into the process. The recycling of solar modules and silicon kerf have presented challenges to date with respect to their integration in the silicon value chain.
Upgrading silicon production technology
In the realm of battery technology, GREEN14’s silane – a by-product of their silicon production process – addresses significant supply constraints. Silane, a gas consisting of a silicon atom and four hydrogen atoms, is a preferred material for silicon-based battery anode manufacturers. Major American scale-ups such as Sila Nanotechnologies Inc. and Group14 Technologies Inc. require increasing amounts of silane for their next-generation battery electrodes as well as European scale ups such as Leyden Jar. This shift from traditional graphite anodes to silicon-graphite anodes is expected to enhance batteries’ efficiency and storage capacity by 30%, meeting the automotive industry’s demands for faster charging electric vehicles.
The installation of such silane plants facilitates these next generation anodes, as there is currently significant under-supply of silane for such technologies. The inclination of customers to adopt green silicon varies significantly between industries, primarily driven by the proportion of embodied energy or emissions that silicon contributes to the final product. In the solar panel industry, where silicon constitutes up to 50% of the embodied energy, the impact of switching to green silicon is much more pronounced. This substantial contribution means that using green silicon can dramatically reduce the overall carbon footprint of solar panel production. Customers in this industry, who are typically more environmentally conscious and invested in sustainable solutions, are likely to view the switch to green silicon as a critical step towards achieving their environmental goals. Furthermore, the solar panel industry’s inherent focus on sustainability aligns well with the adoption of green silicon, making it an attractive option for both manufacturers and end-users.
In contrast, the scenario in the computing industry presents a different dynamic. Silicon accounts for only about 8% of the embodied emissions in computing devices, positioning it as a less impactful factor in the industry’s overall carbon emissions. Consequently, the motivation for customers to switch to green silicon in the computing industry may be less compelling. However, supply chain security ought to influence this industry more, given the critical nature of semiconductor devices. In this sector, the focus tends to be more on performance and cost-efficiency rather than on the environmental impact of components, but transparent and secure supply chains are becoming more apparent.
The future for GREEN14 looks promising as it aligns with the global shift towards more sustainable and efficient manufacturing processes. The company’s innovative approach of producing in the silicon market while licensing for other markets, combined with its strategic utilisation of AI in R&D, positions it not only as a pioneer in green technology but also as a key player in the global effort to reduce carbon emissions in industrial manufacturing. With its pilot plant set to operationalise and plans for expansion underway, GREEN14 is on the cusp of leading a significant shift in how silicon is produced, setting new standards in both environmental sustainability and cost-efficiency.
Please note, this article will also appear in the seventeenth edition of our quarterly publication.