A team of researchers has successfully enhanced the production efficiency of fuel cells with laser machining technology.
The team has used a scanner that allows for laser welding to enhance the efficiency of fuel cells. The scanner can also cut materials for bipolar plates for cells with a thickness of 0.075mm.
These cells, which are crucial components in vessels and aeroplanes, are becoming lighter to improve, which has led to a decline in the thickness of bipolar plates. As the laser machining technology has a thin bipolar plate, the efficiency of these cells can be greatly increased.
A paper detailing the research, ‘Effects of Beam Shape on the Microstructures and Mechanical Properties during Thin-Foil Laser Welding,’ was published in the journal Metals.
Accommodating the demands of fuel cell manufacturers
The researchers focused their attention on demands from fuel cell manufacturers, which require the welding of large-scale thin plates of various forms as well as high-quality cutting at the same time.
To increase the efficiency of fuel cells and meet these demands, they used conventional technology to move the stage and scanner simultaneously.
This succeeded in developing a ‘Top-Lamp’ composite processing machine capable of welding and cutting large areas in various forms by cross-coupling the cutting gas output nozzle to the stage.
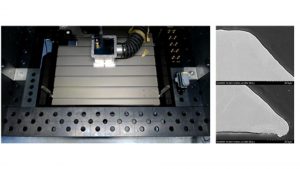
Additionally, the research team developed the function of maintaining machining accuracy. They did this by automatically correcting the work area through the same axle of the scanner and the vision system of the external angle in real-time.
This technology enables the correction of the centre position of the diameter of the nozzle throat and irradiation of the laser beam within 3mm from the diameter of the nozzle. This vastly improves the efficiency of fuel cells.
The researchers have overcome issues with improving the efficiency of fuel cells
Despite the success of the technology, the team did face some issues.
They found it difficult to precisely control the form of the material because of the change in speed caused by acceleration or deceleration at the time of turnaround.
Moreover, because it has been difficult to make corrections to the machining process, it has been necessary to improve the quality of it.
The researchers also faced increased processing times and expenses when increasing the efficiency of fuel cells. As it is not easy to attach cutting gas nozzles to conventional high-speed scanners, it has been necessary to use separate equipment for welding and cutting.
These issues have now been overcome, and the researchers hope that the technology can be used in various industries.
Principal Researcher Su-jin Lee, from the Korea Institute of Machinery and Metals, commented: “The research team is also expecting that the latest technology, developed through international joint research, will be applicable to various sectors.
“The newly developed technology is meaningful in that it can respond to the demands from the fuel cell market for the improvement of machining quality as the thickness of bipolar plates for fuel cells becomes increasingly thinner.”
Overall, the process helps to enhance machining quality by reducing cross-coupling errors through a more precise position correction by the vision system of the scanner. It helps to increase the efficiency of fuel cells through high-speed welding and partial cutting at the same time.