Matthew Belcher, CEO and founder of HEMSPAN®, outlines the importance of adopting sustainable building materials, such as hemp and timber, to reduce carbon emissions, conserve resources, and improve health and well-being.
Buildings and infrastructure are responsible for 40% of global carbon emissions – a staggering number deserving of more attention. Three-quarters of building and infrastructure emissions stem from energy consumption during operation, and the remaining 25% is attributed to embodied carbon from manufacturing, mining, and construction processes. Achieving green building materials and implementing circularity across supply chains is crucial if we are to mitigate climate change effectively and conserve resources.
Biomaterials are the only way to achieve this, offering a resilient, sustainable, and even climate-positive alternative to traditional materials. Hemp, in particular, holds a wealth of potential. It takes only four months to grow to 12ft and sequesters 9-15 tonnes of CO2 a year per hectare. Recognising the potential of hemp and other sustainable materials, such as fast-growing timber forests, HEMSPAN® has quickly emerged as the leading force in demonstrating how sustainable building practices can be effectively implemented, aiming to address 40% of this problem entirely.
A wealth of benefits
The benefits of natural materials are multilayered, from reducing embodied carbon and toxic chemicals to providing health and well-being benefits for occupants. Using natural materials promotes healthier living and better air quality. They significantly reduce harmful volatile organic compounds, which can be cancer-causing, and create a more peaceful acoustic environment that is more enjoyable to live in.
Sustainable buildings are resilient and perform better in extreme weather conditions. Utilising higher-performing fabric and integrated systems will help maintain comfortable living environments within homes and public buildings while minimising energy usage for temperature control.
In addition, sustainable building considers density and biodiversity in its design. HEMSPAN® believes in designing houses to include open spaces and natural areas, supporting the biodiversity of the development and enhancing the natural environment. This is crucial, as traditional farmland lacks biodiversity due to constant ploughing, resulting in a lack of life.
HEMSPAN® plans to source biomass from local farms located within an hour’s drive of our production facility, benefitting the local farming economy. Hemp offers benefits such as weed suppression and improved soil health, resulting in higher yields for traditional farming rotations. Crucially, this circular system will enhance, not displace, crop production, with hemp serving as an ideal and profitable rotation crop that boosts the production of food crops for years to come.
The foundation of HEMSPAN®
Matthew Belcher has been involved in the clean technology space for six years, focusing on natural composites in various industries like automotive, marine, aircraft, and buildings. He was introduced to the potential for hemp through his work in composite and bio-composite buildings, examining the product possibilities for hemp in construction and the leisure industry.
Combining climate-positive buildings with leisure environments was a catalyst for realising the wide market and potential for climate-positive solutions across various sectors. This led to the launch of HEMSPAN®, assembling a team of experienced business operators and industry partners to develop sophisticated systems for delivering climate-positive buildings. Our goal is to address reliability and viability challenges in the housing and building industry at every stage.
The vision is to seed and grow climate-positive communities globally. While an ambitious task, HEMSPAN® is three years into its journey with some incredible projects alive and under contract. With attention from the UK and global markets, it won’t be long before HEMSPAN®’s materials and technologies achieve a large-scale impact.
BIOHAUS®: Incorporating circularity into infrastructure
The ultimate goal is to make all buildings self-powering. A sustainable built environment uses bio-based feedstocks to create building materials or components for systems that can be deployed on a large scale. At HEMSPAN®, the core focus is on utilising hemp and structural timber to deliver fabrics that minimise energy consumption in buildings. Once the fabric is optimised, technologies such as solar, wind, air source, and ground source energy systems can be explored to provide heating, lighting, and power for buildings.
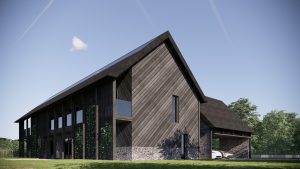
Using this approach eliminates all waste, as materials are recycled not only throughout their lifespan but also within the factory setting. Any leftover materials and trim are recycled back into the initial production process. This means that as the houses are completed and leave the factory, there is no waste.
Our BIOHAUS® system is a comprehensive, sustainable, whole-house system encompassing fabric, design and technologies. Whether it’s one house or 100,000, every component delivered will have a climate-neutral and a climate-positive impact. The BIOHAUS® system sequesters at least 50 tonnes of carbon purely through its hemp element. Factor in the carbon sequestered by timber, and it is clear the potential of these buildings for carbon storage is immense.
Milestones
Several significant milestones have been achieved so far. Securing funding for business development has been a key success as it is vital for any startup. To date, $2.5m has been raised across four funding rounds, enabling considerable growth.
The BIOHAUS® system is now fully developed and has been accredited through the Buildoffsite Property Assurance Scheme (BOPAS). This accreditation demonstrates the highest quality and assurance for systems, specifically for residential and public buildings up to three stories. Achieving this rating unlocks the ability to move into not only residential buildings but also public and multi-occupancy residential buildings, marking an exciting milestone. With the right projects, this scope could be expanded to cover buildings up to 18m or five stories.
The BOPAS accreditation covers us for timber frame construction, surpassing all minimum fire testing requirements and achieving an exceptional two-hour fire rating. Being granted this accreditation and associated fire performance indicates a recognition that the BIOHAUS® system can be and will be a critical part of helping the UK meet housing targets.
Overcoming misconception
There is a prevailing bias against natural materials because of the belief that they cannot perform at the same level as traditional materials. A lack of knowledge, education, and examples of high-performing natural systems drives this misconception. To overcome this, natural materials face must demonstrate their benefits in comparison to traditional materials. HEMSPAN® aims to use its achievements as an example of a high-performing natural system, hoping to increase confidence in the sector. For instance, while PIR insulation provides a thermal barrier, it melts in a fire test, making the building vulnerable in a fire situation. In contrast, HEMSPAN®’s natural systems have proven to be robust, as demonstrated by their fire performance accreditation.
Another challenge is the perception of hemp being associated with the cannabis family, which creates a negative bias. There should be no barrier to the cultivation of industrial hemp and its use in construction. It is important to promote the use and benefits of industrial hemp, as well as to highlight the difference between industrial hemp and the kind of cannabis used in both medical and recreational settings.
At this early stage of development, biobased solutions don’t have the scale of materials such as gypsum boards, mineral wool insulations, and PIR insulations. Over time and with a vertically integrated approach, it will be possible to deliver cost parity with conventional construction methods while reducing whole-life carbon emissions by a huge margin. However, scale is everything, and companies like HEMSPAN® and others in this space need to grow quickly if they are to have such a transformational impact.
Striking a balance
Historically, the prevailing approach to housing has been to maximise density, resulting in concrete and tarmac jungles with minimal green spaces.
There is a balance to be struck in creating sufficient housing and prioritising environmental and lifestyle concerns. However, if we are to meet climate targets and effectively reduce emissions, this cannot compromise climate-positive standards.
Modular and offsite construction plays a pivotal role in reducing waste, enhancing efficiencies, and expediting home construction. It’s imperative to acknowledge the challenges associated with traditional trades and the diminishing training opportunities, which pose a risk to the preservation of crucial skills. Finding a balance between upholding these skills and transitioning to more efficient building methods within controlled factory environments is of utmost importance.
The main challenge lies in cost, which is a significant hurdle for the construction industry. Only through implementing sustainable solutions on a large scale can this cost challenge be effectively addressed, perpetuating wider adoption.
A considerable amount of farmland is currently non-productive due to the pressure on farmers to reduce inputs like pesticides and fertilisers, and this significantly impacted food production. There is an opportunity here to tackle both issues.
By releasing farmland for new housing and increasing yields through the cultivation of hemp and other fibre crops, biodiversity can be improved, food production can be maintained or even enhanced, and a higher standard of living can be offered for new homeowners in a more eco-friendly and diverse setting. This is the type of balance we should be striving for.
Improving regulation and legislation
The wider construction sector needs to address the issue of embodied carbon and consider embracing natural materials in some form. Natural solutions can replace most construction elements within a building project, and where the use of concrete is unavoidable, low-carbon concrete products are available.
The UK Government’s priorities have shifted since the election, and it is encouraging to see a stronger emphasis on environmentally focused approaches to developing new housing. Given the significant demand for new homes in the UK, the government must uphold a focus on sustainability and drive progress in this area. The 2025 Future Homes Standard, though making some efficiency improvements, fell short of expectations. As building regulations evolve, the hope is that sustainable buildings will be subject to greater incentives, ultimately forcing the costs of conventional construction materials up with penalties for the overuse of carbon-emitting products.
HEMSPAN® has been involved in a large project for 2000 houses that aim to be truly transformational in terms of its approach to design, density, and sustainability. Currently, in the early stages of planning and collaboration with the local authority, this project is certain to attract the interest of the new government, allowing them to showcase that homes can be built differently at scale.
Looking ahead
The homes we build must be climate-positive, locking up carbon during construction rather than emitting it and operating with zero energy consumption.
Achieving climate-positive communities and rolling out widespread sustainable housing should not be a distant prospect, nor just a trend. HEMSPAN®’s breakthrough project will demonstrate this. Fundamentally, there are two key components: A large scheme showcasing a new revolutionary model for house building and bio-based building technology that will make this scheme a reality. This must be a comprehensive effort involving collaboration with local authorities, the government, social housing providers, and more to leverage the impact of this scheme and establish a blueprint for sustainable development in the UK.
Please note, this article will also appear in the 19th edition of our quarterly publication.