The Advanced Magnet Lab is enabling here-to-fore unachievable magnet configurations which unlock the magnet supply chain outside of China and free the world from critical rare earth elements.
Magnets are at the heart of products like motors and generators, which are in turn used in virtually every sector of society – energy, manufacturing, medical, consumer products, and transportation and are a critical component in defence weapons and vehicles (land, air and sea). Today, the magnet industry is dominated by China, which has an abundance of magnet rare earth elements (REE) materials, esoteric manufacturing knowledge, low-cost labour, and low environmental standards. Breaking such a ‘high barrier to market entry’ necessitates new thinking and a new and more innovative approach, which can replace the current Chinese approach to their control of the magnet market.
A 2022 report from the U.S. Department of Energy reports that China dominates all of the major stages in the supply chain.
This includes rare earth mining, separation and processing of individual rare earth oxides, metal refining and 92% share of annual global magnet production, the stage with the highest added value.
The Advanced Magnet Lab, Inc. (AML), located in Melbourne, Florida, is working to onshore critical magnet production and break China’s stranglehold over this critical capability. AML’s breakthrough innovations are unique in that they dramatically improve the Chinese technologies that commercial and defence industries currently rely on by enabling magnets with non-critical REE, more efficient manufacturing, and superior performance in an environmentally cleaner and sustainable way with less energy consumption.
Legacy to state-of-the-art
Establishing a domestic supply chain resilience requires a new approach that addresses the entire magnet supply chain: Materials, magnets, magnet manufacturing, magnet configurations, and magnet-based products. Moving from legacy to state-of-the-art, from incremental to transformational, requires a radically new and all-inclusive technology platform. A technology that rethinks how magnets should be designed, manufactured and applied. An approach that is not limited to ‘block’ magnets. An approach that ‘thinks out of the box/block’ applies an efficient design and manufacturing process to achieve the optimum performance and cost for a specific magnet-based product.
The legacy (conventional) approach evolves incremental improvements in magnet material compositions to increase magnet performance, such as raising the operational temperature. This requires complex manufacturing processes and critical REE to improve the operational performance of a magnet in demanding applications such as electrical machines (motors and generators). This incremental approach is the wrong approach. What if it were possible to reduce or eliminate critical REE with revolutionary magnets from a single new technology platform?
The legacy approach
The conventional legacy approach to magnet manufacturing is archaic. There has been virtually no improvement in manufacturing. Magnets are first produced in blocks, then cut into small piece-part magnets. They are limited in shape, size, and single-direction magnetisation. For motors, the largest magnet market, designs require dozens, hundreds, and sometimes thousands of magnets in the motor’s rotor assembly. Having strong magnetic fields, the assembly of the magnets to optimise the motor’s performance is complex, dangerous, and costly.
A new approach
A new approach opens up new design space freedom for engineers, resulting in unforeseen magnet solutions. Gone are magnet blocks, replaced with magnet configurations, which replace the antiquated legacy approach with state-of-the-art magnets, enabling improved performance and lower-cost magnet-based products. State-of-the-art opens up new choices for magnet material compositions. Compositions which are leaner or free of REE. What if it was possible to have an all-inclusive approach in a single technology platform which disrupts the magnet supply chain to break China’s dominance of the magnet REE industry? AML has done this with the PM- Wire™ Technology Platform.
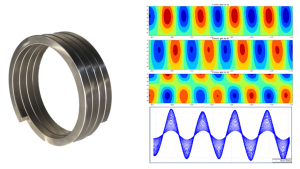
What is state-of-the-art?
AML has developed PM-Wire, a novel approach for the design and manufacture of magnets which improves performance and lowers the cost of magnet-based products while addressing the global desire to reduce dependency on China and REE. PM-Wire is an ideal approach for manufacturing magnets. It uses a ‘wire-like’ manufacturing process for creating unrealised shapes where all the critical process parameters for the magnet materials can be adjusted and precisely maintained/controlled.
What is the PM-Wire impact?
PM-Wire ‘checks all the boxes.’ It impacts all aspects of the magnet supply chain, from raw materials to the final end-use product, such as an electrical vehicle motor. While the value proposition varies by application, the overarching benefits are impressive and impactful.
Materials
PM-Wire is a ‘materials enabler’ that improves the end-use product performance of existing sintered alloy compositions. It also enables non-sintered alloys with less complexity and lower manufacturing costs than sintered magnets, non-critical REE magnets, and the ‘holy grail’ of all magnets – 100% REE-Free.
Configurations
PM-Wire enables long lengths and unique shapes such as rings and helixes. The manufacturing process and proprietary magnetisation of the shaped magnets provide precise and continuous control of magnetic field orientation. One product configuration is PM-360™. In this PM-Wire configuration, AML’s proprietary process yields an almost perfect sinusoidal, continuously changing magnetisation along the full length of a straight, ring or helical magnet. This here-to-fore unachievable type of magnet is a motor designer’s dream design solution. In the example below, 2,750 conventional magnets are replaced by eight PM-360 helixes.
Manufacturing
PM-Wire’s magnet manufacturing process provides high-rate, high-yield, high-quality, less labour and vastly lower-cost capital equipment compared to conventional block magnets. AML’s first manufacturing line can produce PM-Wire magnets at a rate of between 4-6m a minute. To put that into perspective, a magnet having a dimensional cross-section of 4 cm x 4 cm would require less than six production lines to produce 20,000 mt/annum of magnets. Such volume would consume the entire production capacity of the US Mountain Pass rare earth mine, one of the world’s largest REE deposits. Manufacturing lines are low-cost, automated, flexible, easy to scale and can be strategically co-located for supply chain partners or end-user customers.
Enabling non-sintered magnets
Non-sintered magnets, commonly known as bonded magnets, require a bonding agent to bond the magnet powder into a ‘monolithic’ block magnet. This limits the magnet performance due to a percentage of the magnet volume occupied by a bonding agent. This significantly reduces the density, which has a direct impact on magnet performance. Magnet reliability and longevity of bonded magnets are reliant on the magnet material and coatings for structural integrity and corrosion resistance. Furthermore, like sintered magnets, they are limited in shape, size, and single-direction magnetisation.
PM-Wire enables non-sintered magnets for higher performance and higher value applications, which are unachievable with bonded magnets. Three inherent PM-Wire manufacturing attributes contribute to enabling non-sintered magnets.
- Maximum powder density by replacing the bonding agent with a metal containment jacket.
- Magnet powder performance by compressing to a specific powder’s optimum density.
- Magnet magnetisation using proprietary methods enables single-piece Halbach arrays (sinusoidal continuously changing magnetisation), which replace conventional north-south pole topology.
Additionally, PM-wire magnets are virtually unbreakable and corrosion-proof. As a result, PM-wire non-sintered magnets can compete in performance and cost with sintered magnets in the end-use application, even for the most demanding high-performance motors, such as those used in electric vehicles and aero propulsion.
PM-Wire enables non-sintered magnet alloys, including neodymium iron boron (NdFeB), samarium iron nitride (SmFeN), iron nitride (FeN), and manganese bismuth (MnBi).
State-of-the-art at a fraction of the cost
How does the cost of PM-Wire compare to the legacy approach? There is no comparison! One extraordinary example is a PM-Wire electric vehicle retrofit solution. In collaboration with the U.S. Oak Ridge National Laboratory, one of the world’s premier research institutions, ~2,750 NdFeB thin and brittle sintered (NdFeB) magnets arranged as Halbach arrays are replaced with eight non-sintered PM-360 single-piece helical magnets.
The solution provides:
• Equivalent performance (torque and efficiency)
• Eliminates the need to actively cool the motor rotor
• Significantly reduced part count that simplifies rotor assembly
• Yields a fraction of the cost compared to sintered complex Halbach array design
PM-Wire market adoption
How is a legacy market responding to such a radical change from legacy to state-of-the-art, from Block to PM-Wire? The response from the commercial and defence industry is a ‘technology pull.’ Engineers quickly get an impression of the potential design solutions using PM-Wire in the electrical machine market.
- A US defence contractor engineer leaves an excited voicemail: “I am looking at a brochure that says PM-360 is better than a Halbach array.” Months later, a programme was initiated, and the relationship is now three projects deep
- A U.S. Department of Energy-sponsored programme for electric aero propulsion approved a switch from sintered magnets to non-sintered magnets.
- US defence and aerospace company and their U.S. Department of Defense sponsor approved replacing sintered magnets with non-sintered magnets for a defence application.
- Global 2000 heavy industries company has qualified AML non-sintered magnets as a solution for high RPM electrical machines.
- Automotive companies have recognised PM-Wire as an enabler for REE-Free electric vehicles.
- Bonded magnet powder and bonded magnet manufacturing companies are collaborating for PM-Wire magnets to open up new and very large markets for their non-sintered powders.
How to unlock product design limitations – at no cost
Incorporating PM-Wire into existing or new product designs is straightforward. AML uses unique experience in combination with proprietary design and optimisation software for electrical machines and other magnet-based products/applications.
AML’s process integrates all the required customer specifications into its proprietary multi-objective software MOEM™. MOEM provides the full design optimisation space, including solution trade-offs that consider differing materials and PM-Wire configurations. All aspects of the product design and performance are considered, all at no cost to the customer.
MOEM software uses a combination of 2D FEA and analytical equations to model, design and calculate motor performance. The models are fully parameterised and can be used to analyse radial and axial flux machines for different stator and magnet configurations. The model is fast and accurate and outputs 50+ variables like torque, power, losses (resistive, core, windage and eddy), inductance, resistance, mass, volume, etc. Using the above tool, we perform Monte Carlo design space exploration, which helps in the process of finding design solutions that meet the design requirements from a space of design points. The software integrates all the required customer specifications into MOEM, which provides the full design optimisation space, including solution trade-offs considering differing materials and PM-Wire configurations.
PM-Wire™
Imagine a Magnet Industry Without Limitations
Materials
Enabling less critical REE and non-REE alloys
Magnets & Manufacturing
High-rate, high-yield, high-quality, low CapEx
Magnet End-Use Product
Improving the performance and lowering the cost of the end-use product
Design solutions range from rotor retrofits where AML replaces, plug-and-play, the customer’s current rotor magnet configuration with one or more of AML’s magnet configurations. One example is an industrial motor where AML’s patented PM-Axial™ curved magnets replace conventional surface-mounted north-south pole magnets. Using the same magnet alloy and no change to the motor stator, AML’s solution significantly improves design performance and ease of assembly.
- Halbach array performance
- 50% increase in operating temperature
- 50% reduction in rotor overwrap thickness
- 20% reduction in mass by removing the iron
Please note, this article will also appear in the 19th edition of our quarterly publication.