Driven by green targets and improved efficiency, the manufacturing industry is navigating the complex landscape of the transition to more sustainable practices.
As the manufacturing sector stands at the crossroads of innovation and sustainability, industry leaders are increasingly recognising the imperative to adopt environmentally responsible practices.
The implementation of these practices is not merely a response to regulatory pressures but a strategic move towards enduring efficiency and market relevance. Sustainable manufacturing demands a nuanced understanding of material selection, energy efficiency, and waste reduction, and the adoption of such measures often necessitates the integration of advanced technologies and redesigning of traditional processes.
However, as manufacturers embark on this journey, they encounter a complex web of challenges and opportunities. This landscape is particularly evident when considering the transition from conventional coatings that contain potentially harmful substances, such as PFAS, to more eco-friendly alternatives. The implications of this shift are vast, touching on aspects of product quality, operational costs, and long-term environmental impact.
Undoubtedly, the discourse on sustainable coatings is not only a matter of compliance but a critical reflection on the future of manufacturing in a world increasingly attentive to ecological concerns. How the industry navigates these waters may very well define its role in shaping a sustainable economy and the well-being of our planet.
Implementing sustainability
In the realm of manufacturing, companies are increasingly adopting sustainable technologies and practices, such as energy-efficient equipment, pollution control systems, and comprehensive waste management strategies, to mitigate their environmental impact and enhance operational efficiency. The integration of energy-efficient processes is a cornerstone of these efforts. Manufacturers are replacing traditional lighting with LED alternatives and deploying real-time energy management systems to monitor and reduce power consumption. Transitioning to renewable resources like solar and wind power also plays a critical role in powering operations with a smaller carbon footprint.
Moreover, waste reduction strategies are being implemented to minimise the volume of waste generated. Practices such as closed-loop recycling systems allow materials to be reused within the production cycle, reducing the need for virgin resources and lowering waste disposal costs. Composting and responsible e-waste management are other facets of a robust waste management plan that contribute to a more sustainable manufacturing process.
A sustainable supply chain is essential for extending sustainability beyond the factory walls. Manufacturers are assessing the environmental practices of their suppliers, favouring those who demonstrate a commitment to sustainability. Green procurement policies are adopted to ensure that purchased goods have the lowest possible environmental impact throughout their life cycle.
Production optimisation techniques, including lean manufacturing principles, are applied to streamline operations and reduce unnecessary resource use. Emphasising equipment maintenance ensures machinery operates at peak efficiency, minimising energy consumption and reducing downtime.
The dangers of PFAS
While sustainable practices in manufacturing are on the rise, concerns persist regarding the use of PFAS coatings and their associated risks to both human and environmental health. PFAS, or per- and polyfluoroalkyl substances, are a group of chemicals widely used for their water and stain-repellent properties in various products, including coatings for cookware, textiles, and industrial processes. However, the durability that makes PFAS valuable also contributes to their persistence in the environment, leading to significant disposal concerns.
The environmental impact of PFAS coatings is far-reaching. These substances can leach into soil and water systems, causing contamination that is difficult to remediate. This contamination poses a threat to ecosystems and can compromise drinking water sources, leading to bioaccumulation in wildlife and humans. Health risks associated with PFAS exposure include developmental issues, immune system disruption, and potential links to certain cancers. Adverse effects on human health are particularly troubling, given the widespread use of these coatings and potential exposure through inhalation or ingestion.
Regulatory challenges arise as scientists and lawmakers work to understand the extent of PFAS-related risks and how best to control their use and disposal. As awareness of these issues grows, manufacturers face reputational risks if they continue to rely on PFAS coatings. Consumers and investors are increasingly holding companies accountable for the sustainability and safety of their products, which includes the avoidance of harmful substances.
A competitive alternative
Sustainable coatings are emerging as viable alternatives to PFAS-based options, offering comparable performance with a significantly reduced environmental footprint. These eco-friendly alternatives are engineered to provide the necessary durability, resistance, and finish that manufacturers require while also addressing the growing concerns about the environmental and health impacts associated with PFAS compounds.
In terms of performance comparison, sustainable coatings are designed to meet the stringent demands of various industries. They have been found to offer:
- Resistance to chemicals and corrosion
- Longevity and durability comparable to PFAS-based coatings
- Aesthetic qualities such as gloss and colour retention
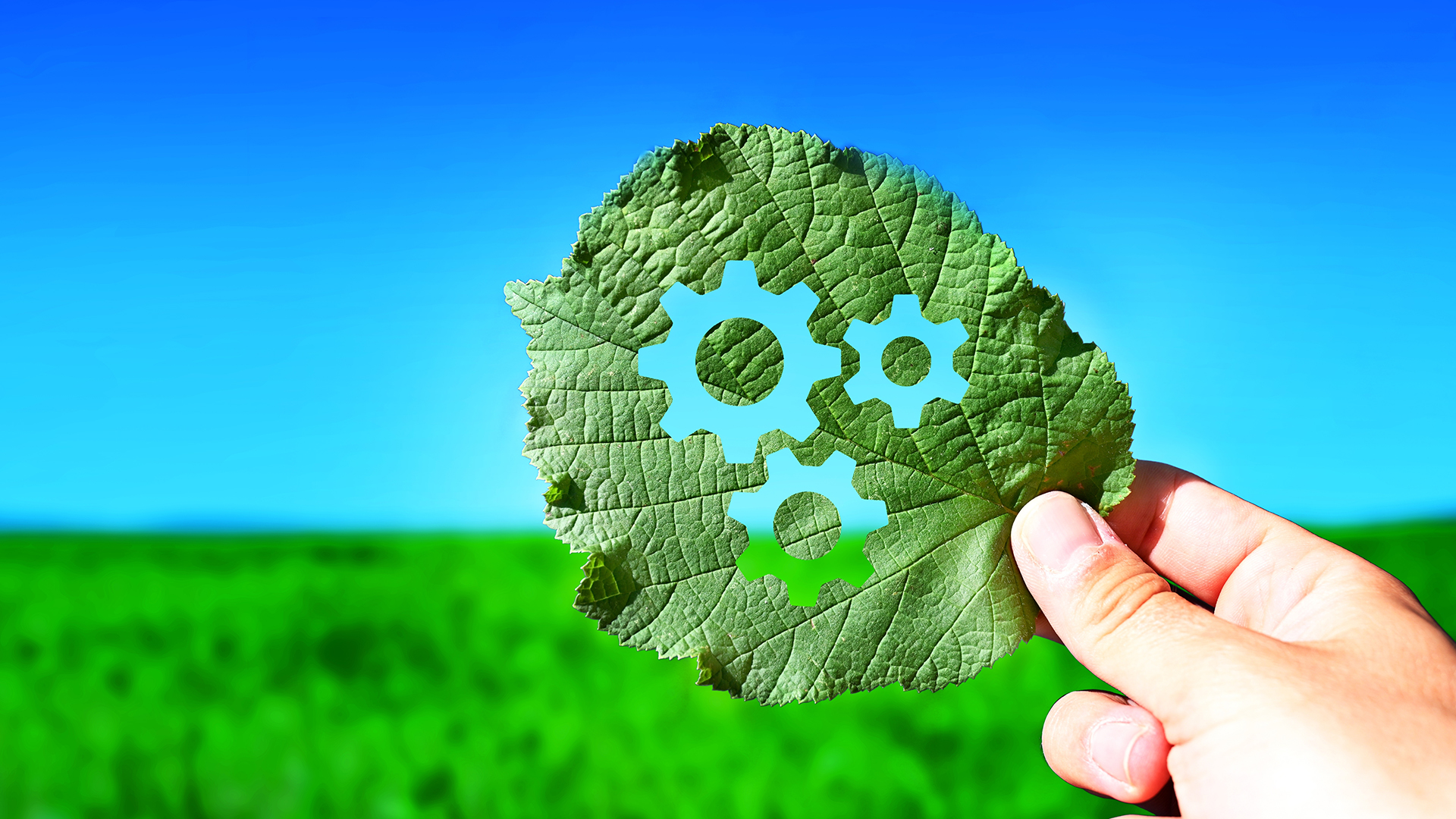
When considering the environmental impact, sustainable coatings have several advantages that contribute to their sustainability benefits:
- Eco-friendly materials
a. They utilise non-toxic, biodegradable, or renewable materials that have a lower impact on ecosystems
b. Reduced emissions of volatile organic compounds (VOCs)
c. Absence of persistent pollutants like PFAS
d. Decreased bioaccumulation potential in wildlife and humans - Efficiency analysis
a. Sustainable coatings often require less energy to produce and can be applied efficiently, reducing waste
b. Advanced water-based formulas that reduce energy consumption during application
c. Improved transfer efficiency, minimising overspray and material waste - Recycling and waste reduction
a. These coatings are designed to be recycled or broken down more easily at the end of their life cycle
b. Facilitating the recycling of coated products
c. Supporting a circular economy by enabling materials to re-enter the production cycle
Manufacturers that adopt these sustainable practices not only lessen their environmental impact but also stand to improve their compliance with regulatory standards and enhance their brand reputation among consumers who prioritise sustainability.
Reducing our dependency on PFAS
Recognising the importance of mitigating environmental concerns associated with PFAS, several initiatives are underway to develop and promote the use of sustainable coatings in manufacturing. These initiatives blend research efforts, industry collaborations, and regulatory actions to reduce the environmental impact of coating technologies.
To encapsulate the ongoing efforts, the table above highlights key initiatives focusing on sustainable coatings.
Investments in research initiatives form the backbone of this movement, with scientists and engineers seeking to create coatings that match the performance of PFAS-based options while being environmentally benign. Industry partnerships are vital in this endeavour, as they facilitate knowledge exchange and accelerate the adoption of innovative solutions. Together, they are exploring closed-loop systems that enable the recycling and reuse of coating materials, significantly reducing waste.
Regulatory guidelines are evolving to address concerns over PFAS, guiding manufacturers towards sustainable practices. Collaboration with agencies ensures that the developed coating technologies not only meet performance standards but also align with environmental regulations.
Through such initiatives, the manufacturing sector is poised to embrace a more sustainable future, limiting the repercussions of PFAS on the environment while maintaining the efficacy of coating applications.