The EASI-STRESS project aims to revolutionise industrial residual stress management in metals by developing commercial services within advanced characterisation.
Every year, millions of tonnes of steel are wasted from over-dimensioning of metallic structures in the energy, construction, and transport sectors. There are many good reasons for reducing steel consumption: in part, it will save material cost, but also because it will significantly reduce global CO2 emissions since steel production accounts for 9% of the global emissions. One reason for the overconsumption of steel is lack of residual stress control.
This article delves into the intriguing world of residual stresses, exploring how the EASI-STRESS project, along with the services offered by the project partners, is revolutionising residual stress management within the industrial landscape. This captivating scientific journey has the potential to enhance component designs, improve product performance, and shape the future of materials engineering.
The presence of residual stresses can be a critical factor in component failure, for example, stress corrosion cracking and fatigue fracture. Residual stress levels can be difficult to determine correctly and are instead treated as a ‘known unknown’ parameter. In industry, you either choose to live with the risk of cracking and increase your maintenance load, or you exaggerate the safety factors and use more material than necessary. The presence of residual stresses can be flipped to an advantage if the direction and magnitude can be controlled. Tensile stresses, where the material is pulling itself apart, are generally regarded as detrimental, whereas if the direction of the stresses can be changed to compressive, the material is instead pushing on itself, delaying crack development and increasing product lifetime. This is especially relevant when wanting to counter stress corrosion cracking and fatigue.
Even with conservative or exaggerated safety factors, residual stress induced fatigue fractures are prevalent in critical failures, as evident from the 147 registered failures related to residual stress in the ASM Failure Analysis Database™ in 2016.1 These failures have been identified as either fatigue fractures or stress corrosion cracking.
These stresses are of critical importance across various industrial sectors, including transportation and energy. However, scientists can directly determine bulk stresses non-destructively through the use of neutrons and x-rays, without causing any damage to the materials. Historically, there has been a barrier between industrial needs and the state-of-the-art academia research on residual stresses, a barrier that is being overcome with the assistance of EASI-STRESS and other initiatives.
The European EASI-STRESS project
In the fascinating realm of materials science, a groundbreaking Horizon2020 project called EASI-STRESS is set to revolutionise the way companies approach stress-control in their components and products. The partners behind EASI-STRESS have estimated that residual stress management could enable 15% material savings. However, to reduce safety issues and save material, new measurement techniques for determining the residual stress levels must be validated in industrial settings and implemented into quality systems. By making bulk residual stress measurements more readily available and efficient, this project aims to optimise component designs, reduce material usage, and even accelerate time-to-market by qualifying new materials and processes more efficiently.
During the project’s ongoing research, we acquired valuable data from residual stress measurements on newly developed benchmarking round-robin samples. The samples are carefully examined using multiple neutron and synchrotron instruments, as well as relevant laboratory techniques. The results have undergone a meticulous comparison with modelling data, providing valuable insight into the accuracy and reliability of the measurements. Both destructive and non-destructive techniques have been validated against each other, highlighting the suitability of the different methods on different types of samples.
In the past, industrial developers faced challenges in utilising advanced characterisation tools such as synchrotron x-rays, or neutron diffraction-based non-destructive residual stress analysis. Data comparability and harmonised protocols were lacking, making it difficult to ensure reproducibility and traceability. However, the EASI-STRESS project is overcoming these obstacles by establishing European-wide standards and harmonised operating procedures, leading to improved data comparability and greater confidence in measurements.
To further contribute to advancements of residual stress management in the industry, project partners the Danish Technological Institute (DTI) and CETIM, now offer commercial residual stress measurement services. This brings practicality and accessibility to the field, providing companies with accurate and reliable measurement and consulting solutions to address the challenges of residual stresses in metals.
The EASI-STRESS benchmarking study
Early in the project, EASI-STRESS identified and produced a series of benchmark samples with the aim of comparing the new measurement protocols based on synchrotron x-ray and neutron diffraction with more wide-spread state-of-the-art techniques. The benchmark samples had increasing complexity to prepare the consortium for the challenges faced when measuring real industrial components. The benchmark samples thus represent different industrially relevant materials and manufacturing methods.
The steel flexures (Fig. 2, left) were the simplest system chosen since they have a well-defined stress state, as the stress is mechanically applied after manufacturing. This process is even straightforward to simulate numerically. The additively manufactured steel arches (Fig. 2, middle), produced by laser powder bed fusion, introduces very steep temperature gradients, fast cooling, and several thermal cycles during the manufacturing process, resulting in a more complex stress state in the final product. Finally, aluminium castings (Fig. 2, right) experience uneven cooling and solidification rates, presenting the most complex stress state due to the manufacturing process.
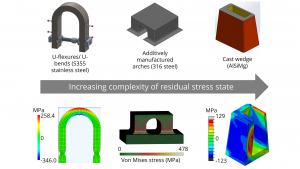
Several measurement methods have been compared for each sample to find the most suitable method for measuring the residual stresses, while considering geometry, resolution, and the desired information. The most common method for assessing the residual stress levels in an industrial component is to extract them from numerical modelling. Hence, the measurements have also been compared to simulations results to validate the models. Numerical modelling is a powerful tool, but the complex nature of residual stress and materials containing multiple phases and phase transitions during manufacturing, means that validation of said models is necessary for accurate predictions.
Selected results from the benchmark samples are presented in Fig. 3, showing how the different measurement methods compare to each other. In Fig. 3 top, synchrotron- and neutron-diffraction based residual stress results have been compared to two different modelling approaches, highlighting important discrepancies. Synchrotron- and neutron-diffraction yield comparable results, however synchrotron XRD has a higher resolution and therefore more detail in the stress distribution. The two modelling approaches appear to overestimate the stresses at certain positions, indicating that the models should be optimised.
In the cast component (Fig. 3 bottom), neutron diffraction was compared to a combination of the destructive methods of hole drilling and contour mapping. These methods measure the stresses by removing material and observing the subsequent deformation as the stresses are re-distributed due to the stresses in the removed material. The resolution of the destructive methods does not seem to be sufficient to map the details of the stress distribution. There is also a difference in the measured magnitude of the stresses.
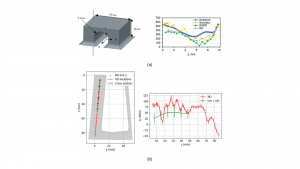
These discrepancies can be explained by different physical phenomena and highlight the inherent complexity of residual stress measurement and basic assumptions of the different methods, bringing into the light the need for best practice guidelines and standardisation. This is something that is addressed in EASI-STRESS, as it is a fundamental necessity for providing reliable residual stress measurements as a service to industry.
Extracting best practices for stress measurement
There are several obvious considerations to make before measuring residual stress in metal components and these can significantly limit the available options:
• The desired information depth;
• The optimal resolution;
• Non-destructive versus destructive; and
• The relevant direction of stress
The benchmark studies made the participants especially aware of mistakes that are easy to make when performing residual stress measurements. A fundamental practice should be to compare results of at least two independent methods of measurement if the exact value of the residual stress is of interest. Regarding the destructive methods, it would be beneficial to compare with a non-destructive method, the most commonly available being laboratory X-ray diffraction. If any mechanical deformation is introduced when removing material, which is an essential process to observe the stress relaxation, the residual stress state has been changed and the measurement is therefore not meaningful anymore.
The project deliverable D2.22 3 outlines best practices for comparing and validating results from different residual stress measurement techniques as well as comparing them to predictions from finite element analysis (FEA). The report stresses the need for standardised approach taking into consideration the different geometric boundaries over which stresses are averaged for each technique. Overall, the report brings to light the multifaceted nature of residual stress measurement and provides a comprehensive overview of best practices for comparing and validating results from various techniques and FEA.
Establishing harmonised measurement procedures
For measurements performed at synchrotron- or neutron-facilities, some very important considerations must be made, as measurements can vary significantly depending on the exact procedure. These measurements are diffraction based, where the interatomic lattice spacing, d, is measured using Bragg’s law: 2 d sin=λ, where θ represents the diffraction angle and λ the wavelength of the x-rays or neutrons (Fig. 4).
Thus, the lattice spacings are used as ‘internal strain gauges’ since changes in the lattice spacing can be attributed to the presence of residual strain if certain assumptions are made.
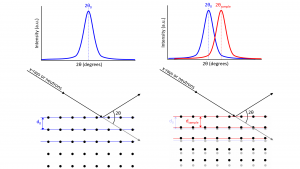
To measure the strain, which is then used to calculate the stress, using these techniques, a so-called d0 sample is required. This is a sample to measure a reference value of the un-strained lattice spacing. Therefore, a representative sample with zero residual stress is required. The d0 sample is commonly obtained by cutting a small piece of an identical specimen. The piece should be small enough for all the stresses to be relaxed. As alloying elements can affect the lattice spacing drastically, (for example the presence of carbon in steel will expand the lattice), the chemical composition of the d0 sample must be identical to the actual specimen. Furthermore, the chemical composition must be identical in the exact position of the residual stress measurement. For that reason, it was found for samples that have a heterogenous chemical composition, such as carburised samples, and samples manufactured via laser powder bed fusion, a powder or single d0 sample was not sufficient. Instead, great success was found with manufacturing ‘combs’ with each leg acting as a d0 reference throughout the thickness of the specimen.
The data format and treatment procedures were also found to be widely different from facility to facility, and even different between instruments at the same facility. As part of EASI-STRESS, the data and metadata formats are in the process of being harmonised among participating facilities in NeXus, which is an extended data format for neutron, x-ray, and muon science, developed with the aim to become an international standard4. This new NeXus Stress application includes the meta data (material, instrumental) and reduced data (fitting results) necessary to enhance traceability and a data treatment significantly more accessible. A dedicated software SOFT-AIS (Analyser for Industrial Stress) with focus on strain and stress calculations and user friendliness and will trivialise the previously time-consuming data treatment.
Residual stress standardisation
EASI-STRESS has opened a working group on diffraction (WG10) under the CEN Technical Committee 138 on non-destructive testing, with the aim to develop official standard documents for residual stress measurement. Standards already exist for residual stress measurement using laboratory-based X-ray diffraction5 and neutron diffraction.4 6 The EASI-STRESS standardisation effort is focused on developing a technical specification (TS) with the title ‘test method for determining residual stresses by synchrotron X-ray diffraction.’ In late 2023, the draft document will be circulated to all European members of CEN for approval. The Technical Specification is an official guideline and acts as a pre-cursor to a standard. CEN TC 138 will also decide whether the work towards a real standard shall commence, but this is beyond the scope of EASI-STRESS.
Launching an industrial service
The wide-spread value of EASI-STRESS for industry will be realised with the launch of an industrial service as an open innovation test bed. The partners DTI (DK) and CETIM (FRA) already perform residual stress measurement services for industrial clients based on their in-house laboratory equipment and, based on the learnings from EASI-STRESS, they have now added semi-standardised synchrotron and neutron measurement services to the service offer.
The transformation of neutron and synchrotron x-ray experiments from scientific tools into industrial service is achieved by resolving and developing the following areas:
- Establish reference samples based on the EASI-STRESS benchmark samples;
- Develop measurement protocols based on the EASI-STRESS standardisation work;
- Providing auxiliary services, e.g. metallographic sections, mechanical testing, modelling; and
- Enabling more accurate price and time estimates
If the internal competence levels at the companies is sufficiently high, they can also engage directly with the partner facilities in EASI-STRESS: ILL (neutron, FRA), ESRF (x-rays, FRA), Hereon (x-rays/neutrons, GER) and EK (neutron, HUN).
Finally, the academic partner in the project, the University of Manchester, offers research-driven industrial collaborations in the area of residual stress management.
In conclusion, EASI-STRESS is nearing the end of the project period, but the industrial service and exploitation of the new methods is just beginning.
Acknowledgements
The EASI-STRESS Work Package leaders are acknowledged for providing input to the article: Matthew Roy, University of Manchester; Ennio Capria, ESRF; Sandra Cabeza, ILL; Fabien Lefebvre, CETIM and Marc Thiry, Hereon. EASI-STRESS has received funding from the European Union’s Horizon 2020 research and innovation programme under grant agreement No 953219.
References
- Fairfax, E J, Steinzig, M (2016). A Summary of Failures Caused by Residual Stresses. In: Bossuyt, S, Schajer, G, Carpinteri, A, (eds) Residual Stress, Thermomechanics & Infrared Imaging, Hybrid Techniques and Inverse Problems, Volume 9. Conference Proceedings of the Society for Experimental Mechanics Series. Springer, Cham.
- Matthew Roy, in preparation
- Matthew Roy, et.al., EASI-STRESS Deliverable 2.2: “Best practice guidelines”
- Mark Könnecke, et al. (2015), The NeXus data format, J. Appl. Cryst. 48, 301-305 doi:10.1107/S1600576714027575
- EN 15305:2008 “Non-destructive Testing – Test Method for Residual Stress analysis by X-ray Diffraction”
- ISO 21432:2019 “Non-destructive testing – Standard test method for determining residual stresses by neutron diffraction”
Please note, this article will also appear in the sixteenth edition of our quarterly publication.