Innovation News Network spoke to Oana Penu, Director of the InnoEnergy Skills Institute, about the current green skills gap and how the Institute will assist in reducing this shortfall.
The InnoEnergy Skills Institute is at the forefront of addressing the European green skills gap. With a bold mission to elevate the global workforce for a clean energy transition, the Institute harnesses insights gained from its partners and aligns them with the industry’s evolving demands.
To learn more about the work of the Institute, Jack Thomas, Managing Editor at Innovation News Network, spoke to Oanu Penu, Director of the InnoEnergy Skills Institute.
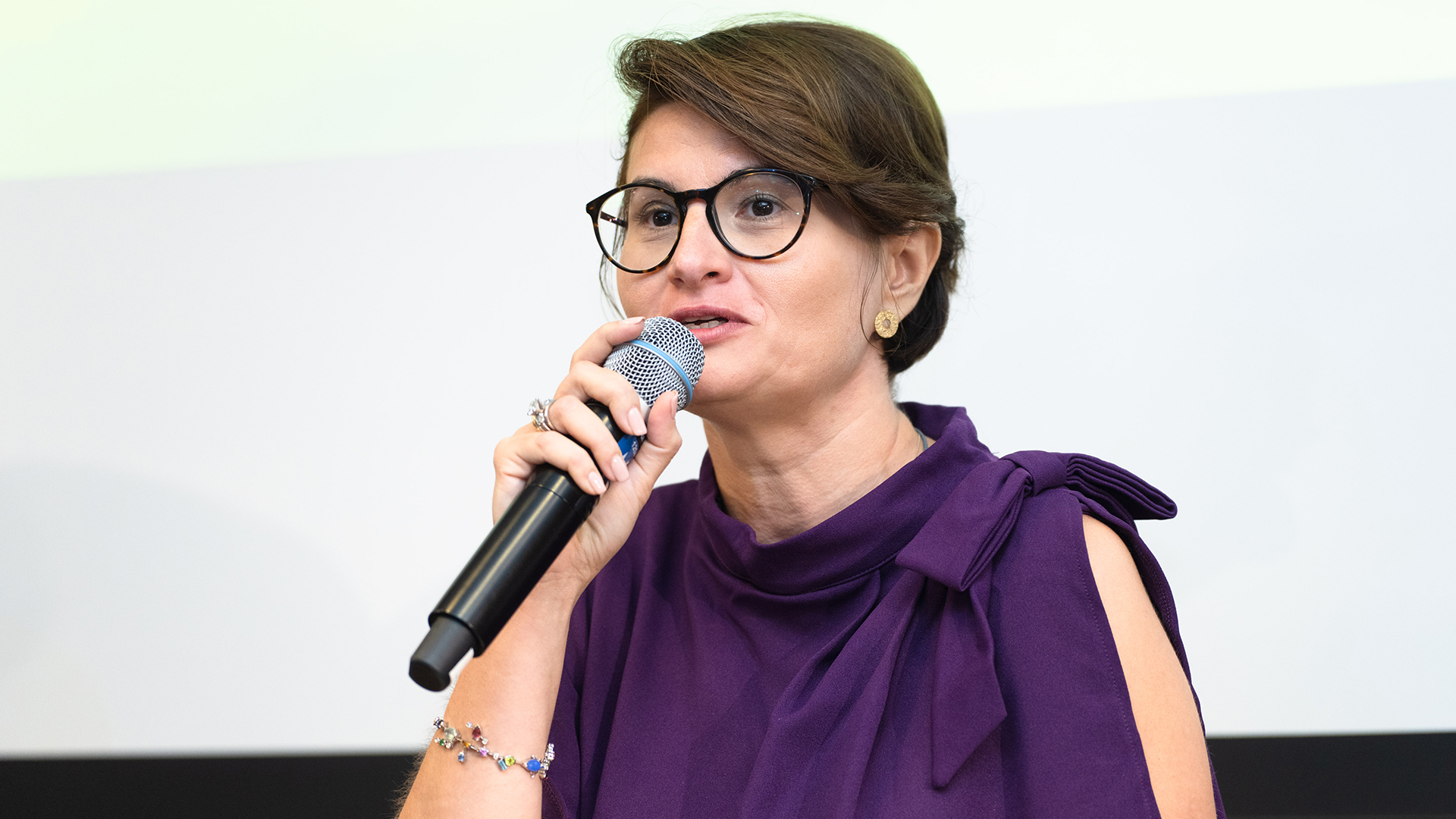
Please can you provide an overview of the InnoEnergy Skills Institute and its mission to address the European skills gap?
The InnoEnergy Skills Institute is a solution to one of the major bottlenecks identified in the transition to a net zero economy – a lack of skilled workforce.
Our vision is to not only elevate the European workforce but to uplift the global workforce for the energy transition. We are determined to equip the global workforce with the needed skills and competencies for a sustainable economy.
We have know-how from our education partners and the needs and demands of our industry partners. When this is put together, it can be put forward to the people helping to accelerate the energy transition, ensuring they have what it takes to facilitate this change.
Since launching in April, how has progress been so far?
So far, the InnoEnergy Skills Institute is gaining significant interest. The Institute is built on the success of the European Battery Alliance Academy, which started in 2019.
During COVID-19, there was a huge transformation in the education sector with the emergence of online learning, AI, AR, and VR applications. This transformation has been accelerated by demand from the industry side.
We have also seen that the demand experience in the battery world, where until now we have upskilled and reskilled over 40,000 people, is similar in other industries, like the solar and hydrogen industries.
What is the current shortfall we’re facing, and is there enough time to get enough people trained to meet these targets?
We are currently having a so-called four-pressure situation. The first pressure we have is the volume of workers required.
According to a report from the World Economic Forum, 18 million new jobs will be created that do not exist today. Comparing this figure to the active population in Europe, you can see that we are falling short.
The second driver is time: 2030 in industry standards is tomorrow. Regarding the battery value chain, we must reskill and upskill 800,000 people by 2025. Comparatively, this is an hour in industry time.
You must create learning experiences to enable rapid catch-up of the new skills and competencies that are needed. With that being said, for most basic jobs in the industry, people need between two and four months to perform properly.
Automation is also important – we need to understand the impact of technology on the job roles and the workforce we have today.
Another force is that skills are concentrated in different agglomerations. The new agglomeration where skills are needed does not necessarily match areas where you have workers.
For example, there are a lot of workers in the automotive industry in Central and Eastern Europe and the north of Italy because that’s where the automotive clusters are. The Gigafactories, however, tend to be in the Nordics, Germany, and France, where you have people with slightly different competencies.
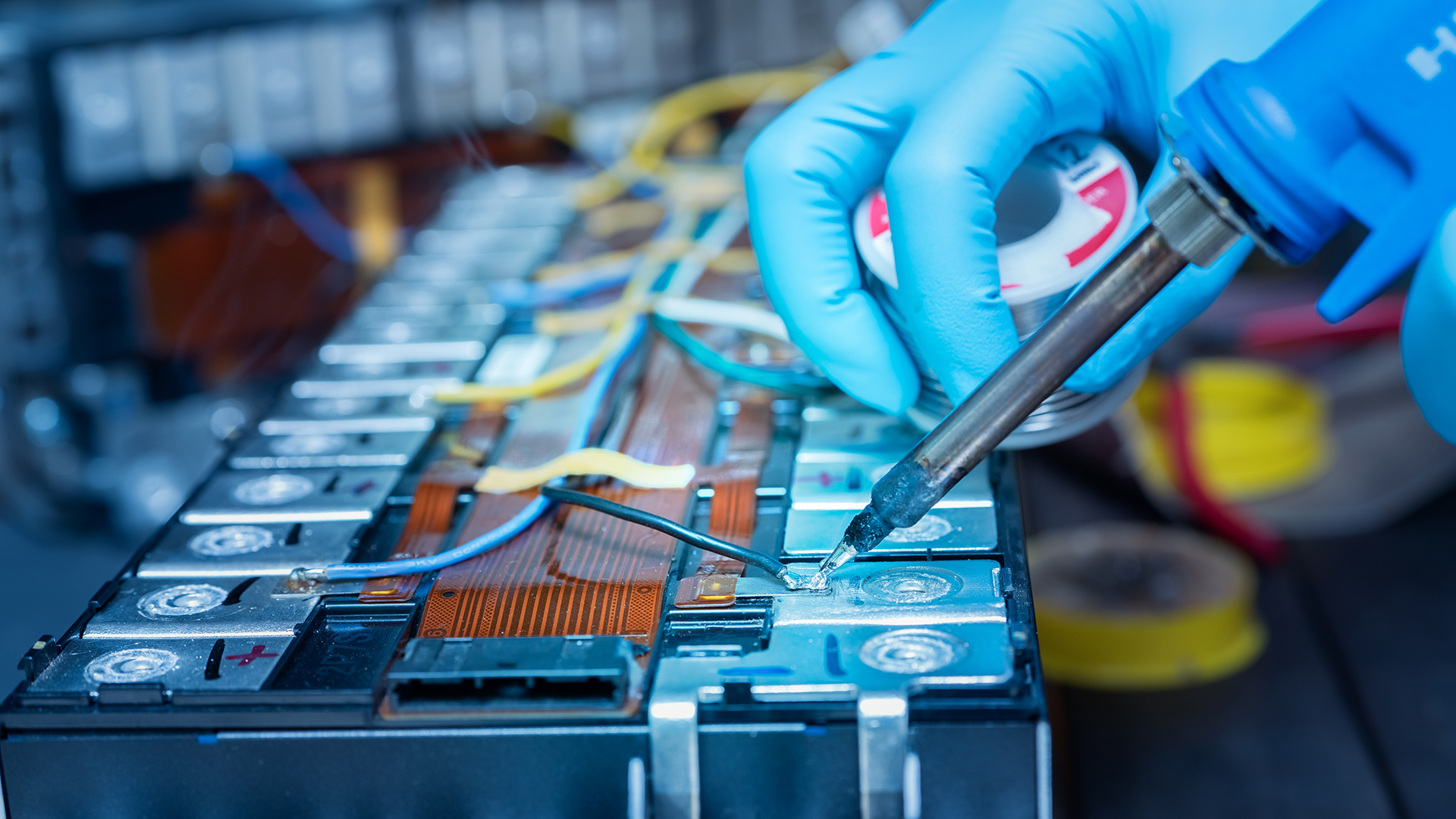
Therefore, how do you ensure that the people in traditional automotive areas remain employed and relevant to industry, and how do you bring a skilled workforce to the emerging European areas?
Europe is a specific focus area because, across the continent, we do not have social mobility. In Europe, especially in blue-collar industries, people tend to stay where they have started their careers.
Language is another challenge in Europe. Especially when we talk about blue collars, work has to be translated into their own language, and that is expensive and time-consuming.
Lastly, the current education system is not equipped to address these challenges. I think the education system is great, and it is doing the right things, but it’s simply not capable of providing the workers with very intensive two to four months of training.
That is where the InnoEnergy Skills Institute comes in. We have customised learning experiences that equip people with the needed skills to perform the required job.
At the end of this, we also offer them credentials and accreditations recognised at the European level.
Could you explain more about the unique training of the Skills Institute? Are there flexible options to help people get into green careers?
We aim to do two things through our solution. First, we want to increase the employability of a worker. On one side, we want to ensure that the worker remains relevant to the evolving industry.
Conversely, we want to assure the employer that that person has the needed competencies and skills to ensure productivity.
These aims are matched through our skilful solution that starts with assessing the situation.
First, we want to see what the needed critical job roles are. For this, we have a tool called the Skills Compass. The Compass is a report generated by a tool that mines the internet and human resources databases. From this information, it creates a customised report for a need of a given enterprise.
In this report, we identify critical job roles based on the briefing we have received. Then, we define these job roles with the competencies and skills needed for them and levels of proficiencies based on this.
We then create what we call a learning journey.
For example, if you want to be an EV technician, we create a learning journey with both an online component and face-to-face in a lab. For this learning journey, we offer several courses from our library.
Today, in the library, we have 500 hours of unique content on the battery value chain, solar, and hydrogen. By the end of next year, we want to have 1,200 hours of unique content.
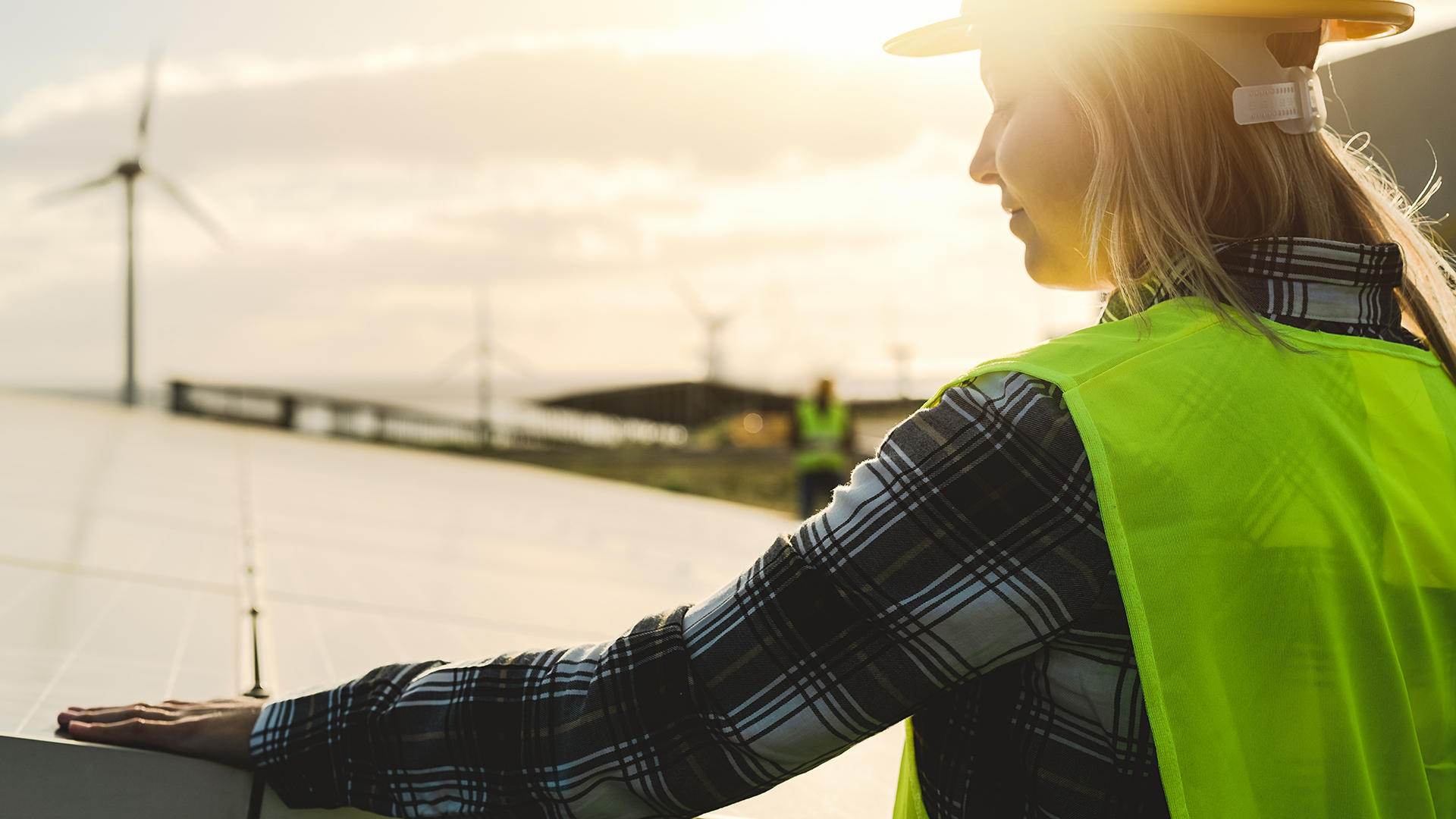
We have learned to create content that matches the job roles that are needed.
The learning journeys have clear objectives and outcomes and can take from six weeks to six months.
If the exam is passed at the end of the course, a certificate is offered, which is valid at the European level.
At the InnoEnergy Skills Institute, we offer a unique solution to a particular issue. An extra service that we provide is that learning journeys are created on what is relevant to the person.
The focus of the Institute is on blue-collar workers in particular. This is because white collars are highly educated, proficient in English, have very high mobility, and know how to find their own way of learning.
In Europe, most of the time, blue-collar workers are trapped in their region, facing significant language barriers. They are at the mercy of their employer, hoping for a solution.
We need to empower those people to capitalise on the skills that they have, putting them on successful paths for the future. Without this, there will be a huge social impact through forced early retirement.
How important is the ManpowerGroup InnoEnergy Skills Institute partnership in filling the battery value chain shortfall?
Manpower comes at the problem from the demand side – they know what the industry needs. They let us know what skills and competencies are needed to fill that role.
The InnoEnergy Skills Institute puts on courses to give people the identified skills.
The partnership coordinates supply and demand, accelerating the creation of paths for people navigating the clean energy transition.