The Construction Scotland Innovation Centre is driving transformational change across the construction industry
The construction sector plays a significant role in the UK economy, employing over 9% of the workforce. Yet, when it comes to innovation and modernisation it often falls behind other sectors. In 2016, Mark Farmer’s hard-hitting review of the UK construction labour model warned that the sector must ‘modernise or die’. He challenged the industry to ‘to do things differently’ and to reduce its reliance on building in the same way that it had for decades.
The industry-led Construction Scotland Innovation Centre (CSIC) aims to drive that transformational change and deliver economic impact.
Its CEO Stephen Good spoke to the Innovation Platform’s Managing Editor Michelle Gordon about championing innovation within the sector.
How is CSIC driving transformational change across the construction industry and why is it important to do so?
‘Innovate or die’ was the clear message for the construction industry set out in the 2016 Farmer Review of the UK construction sector, being last but one in the ranking of sectors for digital modernisation and advancement. CSIC was set up to change this as one of seven publicly funded innovation centres tasked with using innovation to deliver economic benefit for Scotland.
Since its beginning in 2014, CSIC has worked on more than 300 projects, creating almost 4,000 jobs and more than £1bn of revenue for the Scottish construction industry.
CSIC defines innovation as ‘change that unlocks new value’. One of CSIC’s most valuable assets is its connected ecosystem of collaborators focused on driving positive change that would otherwise be impossible in silos. By linking together businesses, university experts, the public sector, and the economic development networks, its industry-led team supports a culture of innovation that drives transformational change across the construction industry.
The centre’s work revolves around creating new products, business models, and services; collaborating with industry to find solutions to key challenges; giving industry access to advanced equipment at its world-class innovation factory; and connecting and engaging networks through a rich events and educational programme.
Our state-of-the-art Innovation Factory was the UK construction industry’s first dedicated digital manufacturing, prototyping, and future skills centre of excellence. It is home to a wide range of product development, manufacturing, robotics, and visualisation equipment and can be accessed by companies in the sector or used together in collaborative R&D projects led by the CSIC technical team.
Taking inspiration and learnings from other automated industries, equipment housed in the 35,000 sq ft facility includes the UK’s only vacuum press for the production of cross laminated timber, robotics, virtual and augmented reality equipment, an insulation line, an offsite manufacturing line, and various other enabling equipment and digital tools.
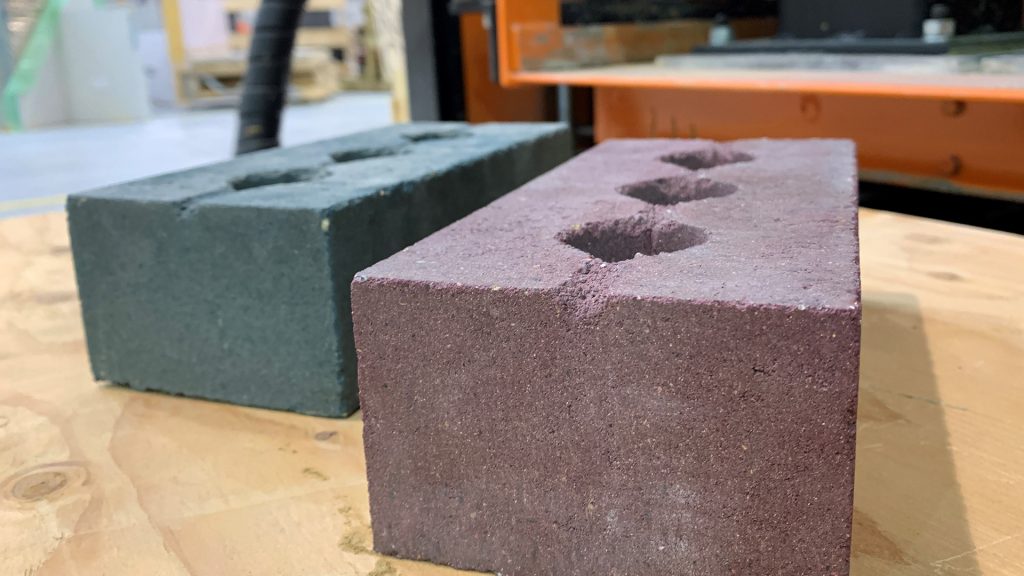
Talk me through some of the key R&D projects/innovations around sustainable materials that CSIC is supporting and the potential impact of these projects?
Project: K-briq: The sustainable brick
- Developing/upscaling a new sustainable brick that is made from 90% recycled building materials – specifically plasterboard, old brick and stone;
- No cement is used and it is unfired, so emissions are significantly lower; and
- The project with CSIC assessed the feasibility of the K-briq and readied it for commercial use. It included a pilot production, testing and optimisation, and building a demonstration structure with ongoing monitoring.
Impact:
The K-brick has 1/10th of the emissions of standard clay-bricks, is two times stronger than ‘common bricks’ (N/mm2), more durable and costs 47% less to produce.
Future implications:
It opens up the opportunity for construction to move towards building with sustainable and recycled materials with virtually no downside.
Project: Multiply
- CSIC manufactured the first ever hardwood Cross Laminated Timber panels in the UK as part of the award-winning project MultiPly;
- Led by the American Hardwood Export Council, MultiPly created an innovative structure to showcase hardwood CLT in modern construction. The project combined an accessible sustainable material – American tulipwood – with modular design; and
- The structure’s 111 tulipwood CLT panels were manufactured at CSIC’s Innovation Factory in Blantyre: the only facility with an industrial scale CLT vacuum press in the UK.
Impact:
The structure has been showcased around Europe and won various awards and highlights the potential that CLT has in the Scottish market.
Future implications:
Ultimately, the project confronted two of construction’s challenges: the need to build more housing and the demand to combat climate change. The ultimate aim for CSIC is to manufacture CLT using homegrown timber and this project is a major stepping stone towards that goal.
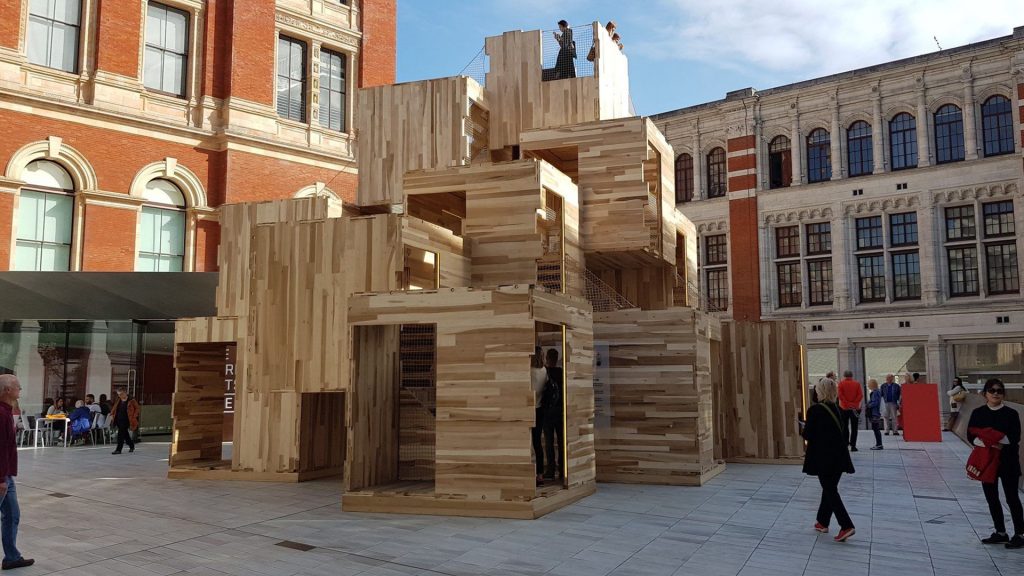
Project: COP26 CLT demonstrator unit
- The project will see the manufacture of the first Scottish-sourced cross laminated timber (CLT) and nail laminated timber (NLT) housing unit – including wall, roof, and floor;
- Using the UK’s only vacuum press at CSIC’s innovation factory in Hamilton; and
- The CLT and NLT superstructure is set to be complete by the end of the year
Impact:
It will be showcased at next year’s COP26 UN conference on climate change in Glasgow, and has the potential to be the catalyst for mainstreaming the use of Scottish-sourced CLT.
Future implications:
Among the benefits, using more home-grown timber is expected to significantly lower costs for the construction industry – figures suggest a reduction of up to 10% compared to imported. CLT can cut carbon emissions through reduced transportation and open new markets to the UK-based timber sector.
Project: Integra House
- The CSIC supported the development of a low-cost sustainable house – the Integra House – for Sylvan Stuart’s affordable and sustainable rural housing project; and
- The second part of the project tested blown-in woodfibre insulation at the CSIC’s Innovation Factory, which consists of finely shredded wood shot into thick wall cavities. It is made from sustainable wood that does not contaminate or pollute.
Impact:
Each Integra house would store between 2-3 tonnes of woodfibre, capturing 1000-1500kg of CO2 and meeting heat transfer levels at passivhaus energy standards. It also reduces material waste as, unlike PIR board, it has no off-cuts.
Future implications:
Blown-in woodfibre insulation would be new to the Scottish construction industry. Although already used in parts of central and northern Europe, this would be a pioneering technology in Scotland.
Project: Energystore
- Testing Energystore’s Superbead technology in Scotland’s pre-1919 dwellings;
- Expanded polystyrene beads (EPS), a kind of bonded bead insulation placed inside wall cavities, was used; and
- The technology allowed pre-1919 dwellings to be retrofitted less invasively and more effectively through small holes in the wall which are covered after fitting.
Impact:
The beads were found to lower heat transfer an average 63% in pre-1919 dwellings, upgrading energy ratings of analysed dwellings and capturing an average 750kgCO2/year per home.
Future implications:
The beads have a high resistance to heat loss when bonded with adhesives, and their effectiveness at reducing CO2 makes them very helpful in the journey to net zero – especially in the central belt of Scotland where tenements that are difficult to retrofit and prone to heat loss are so prevalent.
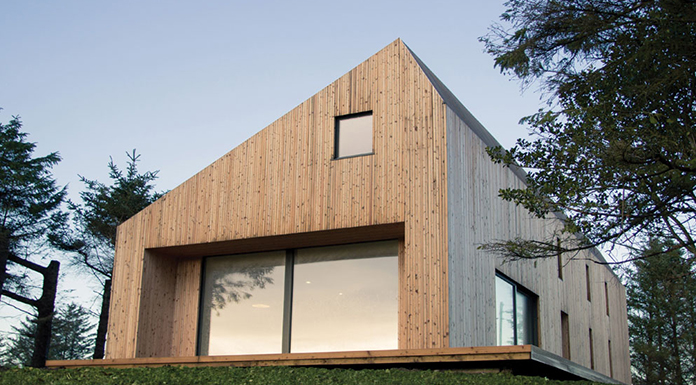
What implications does the research outlined above have for the future of the construction industry and the way in which our built environment is shaped?
These projects will help to build a stronger circular economy, through less waste and more recycling/reusing, with viable recycled building materials. There will also be more homegrown resources being used in Scotland, with a greater emphasis on homegrown timber and CLT.
The retrofitting of more existing homes with novel insulation methods will help to reach ambitious and challenging net zero targets
What will be the key areas of focus for CSIC over the next five years?
Meeting net zero carbon targets with a focus on the following areas:
Culture change and skills
Products and processes don’t innovate themselves. It is people who drive change. New ways of doing things though, need new skillsets. Progress in offsite and modular construction will require electricians to modify their skills and knowledge to work in these environments.
The industry has the opportunity to work with Scotland’s world-class universities and colleges to develop the skills of our future workforce. So, from apprentices to university students to those working in industry at all levels, CSIC offers access to a range of skills and knowledge programmes to equip the sector with the required expertise.
The sector’s image problem also needs to be addressed if we are to attract the right talent. This is another area of focus for CSIC, promoting the opportunities we provide for all other sectors, the benefits we bring to society, the value we create, the communities we empower, and the global challenges, like climate change, that we will solve.
Digital Transformation in the Construction Sector
The industry will benefit from the long-term approach to integrating and scaling up the very best tried and tested digital, manufacturing and enabling technologies that already exist, whilst continuing to innovate where there are gaps in knowledge and new solutions are still required, to create a digital ecosystem fit for the future.
Accelerating industrialisation
The move to offsite and industrialised construction is improving efficiencies and quality across the industry.
Building sustainably
Finding new products, processes and materials that will support our built environment to achieve net zero carbon.
Stephen Good
CEO
Construction Scotland Innovation Centre
+44 (0)141 212 5250
info@cs-ic.org
Tweet @CScotIC
www.cs-ic.org
Please note, this article will also appear in the fourth edition of our new quarterly publication.