The Institute for Applied Materials – Applied Materials Physics (IAM-AWP) at the Karlsruhe Institute of Technology (KIT), Germany, is home to Europe’s largest battery calorimeter laboratory.
With six Accelerating Rate Calorimeters (ARCs, Thermal Hazard Technology) of different sizes used in combination with cyclers, the team led by Dr Carlos Ziebert evaluates quantitatively the thermodynamic, thermal and safety data for Lithium-ion cells on the material, cell and pack levels for both normal and abuse conditions (thermal, electrical and mechanical). Lithium-ion cells are the electric energy source which powers our tablets and smartphones, our electric vehicles and our daily lives in the 21st century.
Thermal propagation
The development of safe cells is of utmost importance for a breakthrough in the electrification of transport and stationary storage, because an uncontrollable increase in temperature of the entire system (so-called ‘thermal runaway’) can cause an ignition or even explosion of the battery with simultaneous release of toxic gases. If a single-cell thermal runaway occurs, the next step is to prevent the propagation of the thermal runaway from one cell to the neighbouring cells – known as thermal propagation – or at least extend the time until thermal propagation to five to 10 minutes. This should give the passengers in an electric vehicle enough time to escape or to be rescued by emergency services. The large scale ARCs are well suited for studying thermal propagation.
Materials qualification setup for thermal propagation mitigation
Ziebert and his team have developed a new setup at the Calorimeter Center to allow the development and qualification of suitable countermeasures, such as heat shields or phase-change materials. This setup consists of a metal box which mimics a battery box and which is put into the calorimeter chamber. Four pouch cells are installed in the box and equipped with thermocouples that are connected to the ARC software. A heater mat is attached to cell 2 and the material to be tested is installed between cells 3 and 4 and below the lid (Fig. 1). With the help of the heater mat, cell 2 is now heated up to initiate its thermal runaway. Fig. 2 clearly shows that the thermal runaway instantaneously propagates to cells 1 and 3. However, DEFENSOR MULTIFLEX®, the improved heat shield material from HKO Group which was tested in this example, is able to delay the thermal propagation to cell 4 by nine minutes. The ‘cold side’ temperature on the top of the lid stayed below 80°C during the whole test, whereas temperatures of up to 850°C were reached inside the battery box.
A global technical regulation (GTR) on electric vehicle safety currently being developed by all relevant stakeholders is set to include provision for thermal propagation. There is still a lot of discussion and ongoing research in order to determine the best initialisation method, which could become a standard. We hope that the research in the Calorimeter Center will help to make progress in this field.
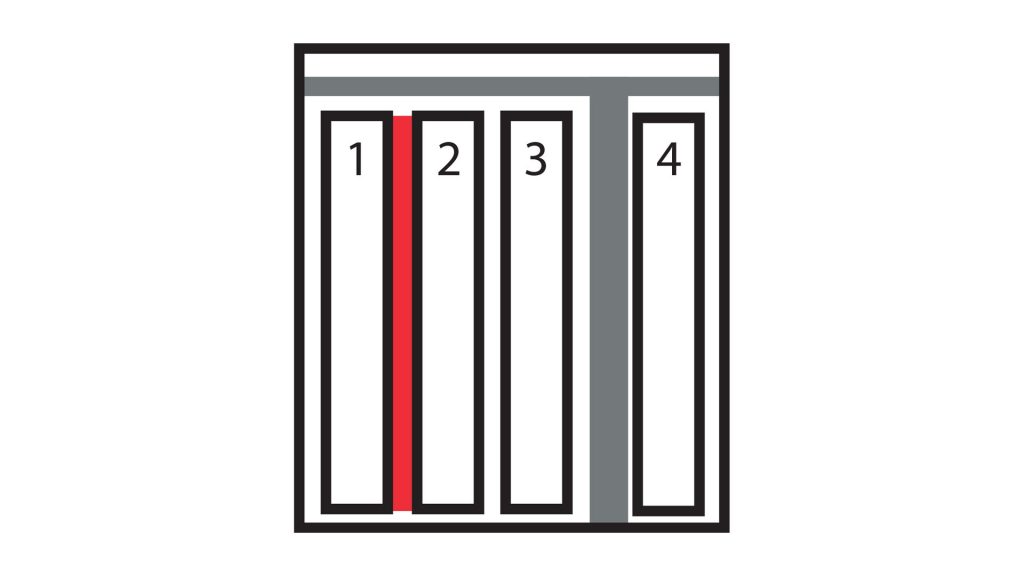
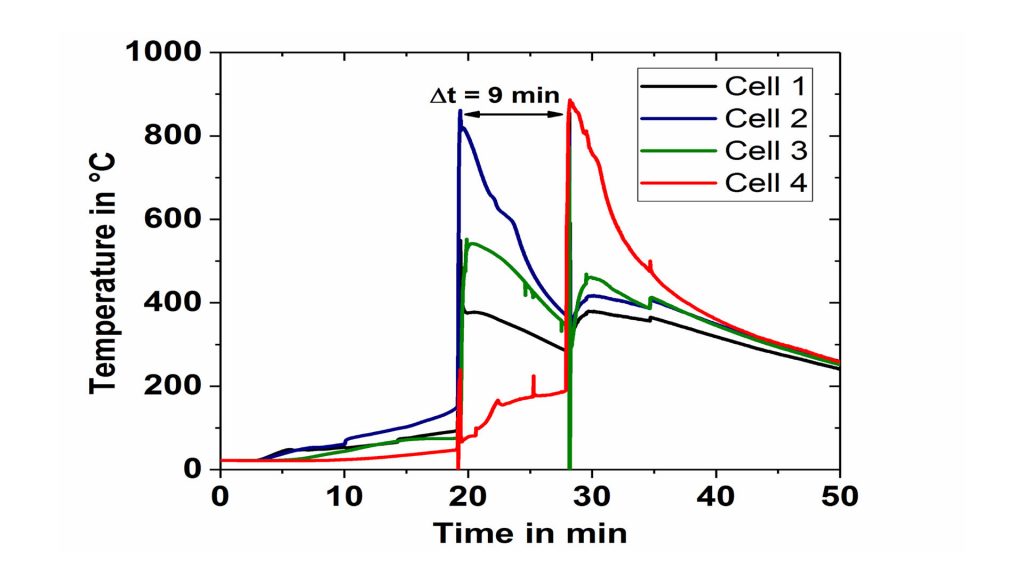