Dr Carlos Ziebert, Head of the Calorimeter Center at Karlsruhe Institute of Technology, discusses the centre’s innovative calorimetric methods to increase the safety of batteries in the renewable energy sector.
The market for lithium ion-batteries (LIB), for the utility-scale energy storage (UES, see Fig. 1) and for small-scale stationary energy storage, is increasing rapidly. UES can provide different grid services, such as peak shifting, peak shaving, or frequency control and can improve overall power system efficiency and grid stability. The most common small-scale battery-based stationary energy storage systems are solar batteries, which are photovoltaic systems on the roof of family houses coupled to a battery storage solution in the basement, the garage (see Fig. 2), or the living room (see Fig. 3). They allow surplus solar power to be stored for later use.
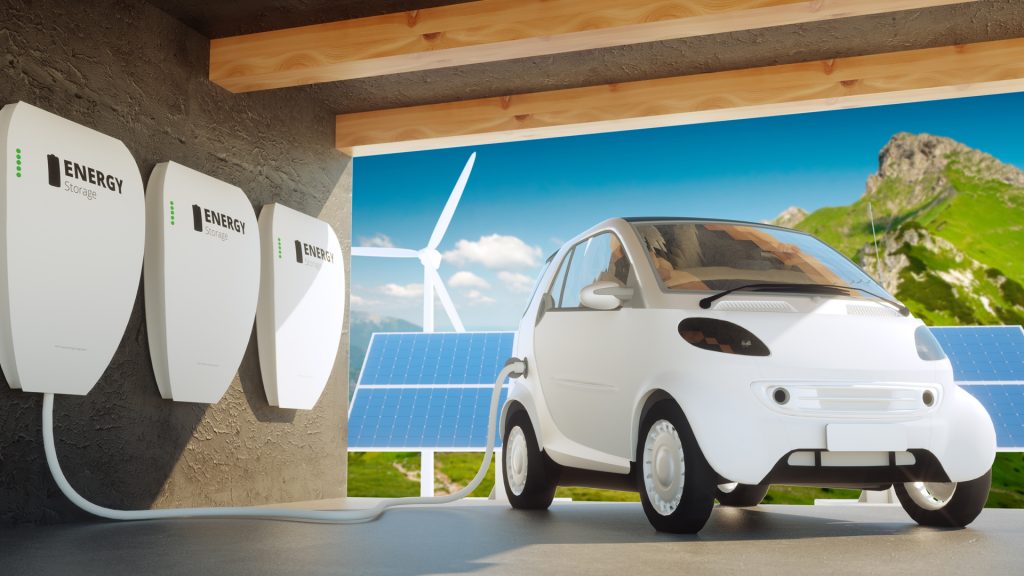
The most important market drivers for both applications are the increasing penetration of variable renewable power sources such as solar and wind, and the dramatic reduction in prices for LIB. LIB technology is by far the leading choice for new projects globally. The primary factor driving continued price declines for LIB is the rapidly growing capacity of global battery manufacturing, which increased from 3 GWh prior to 2015 to currently around 190 GWh. Since 2015, 10 new factories have started production.
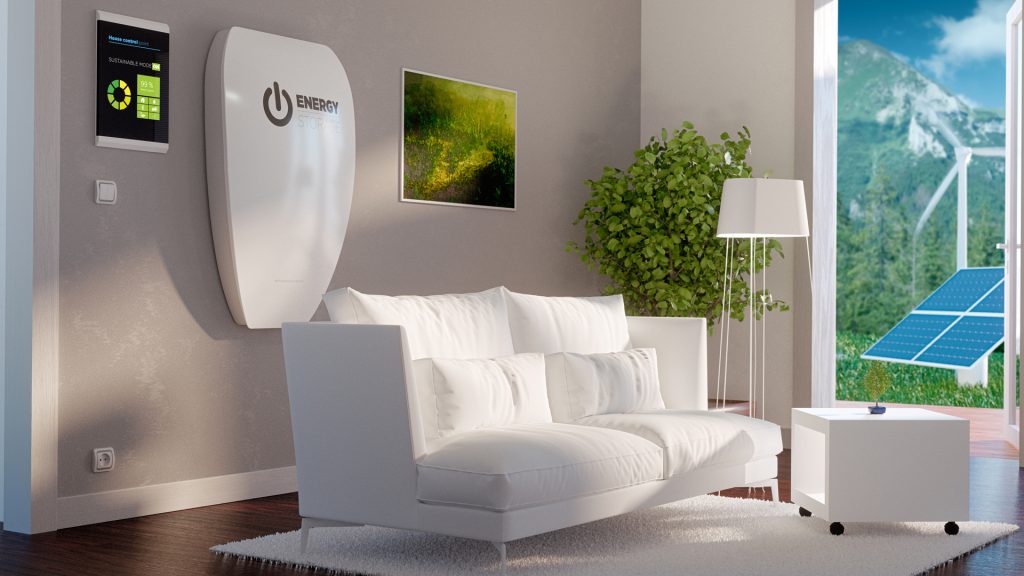
Safety issues
Safety issues have a major influence on consumers’ and utilities’ willingness to adopt current lithium-ion battery technology for stationary storage in the renewable energy market. This is because an uncontrollable temperature increase (so-called ‘thermal runaway’) can cause the battery to ignite or even explode, with a simultaneous release of toxic gases. Such a worst case is, of course, extremely undesirable for batteries applied in both UES and solar batteries.
Indeed, since August 2017, 23 energy storage system fires have occurred in South Korea resulting in system losses valued at over US$32m. A report from their fire investigation committee concluded that some of the root causes for the fires included a lack of protection against shocks, faulty installation practices, and control systems that were incompatible with some components. However, the common practice of charging the LIB from close to 0% to 100% and then discharging it again in the same range on a daily basis has also caused the cells to suffer from a high stress level and accelerated ageing. This severe load profile is common to storage systems coupled to wind and solar farms to shift the output to higher demand periods. Thus, safety and ageing tests are becoming particularly important in developing improved safety strategies and safety systems for battery storage in the renewable energy sector.
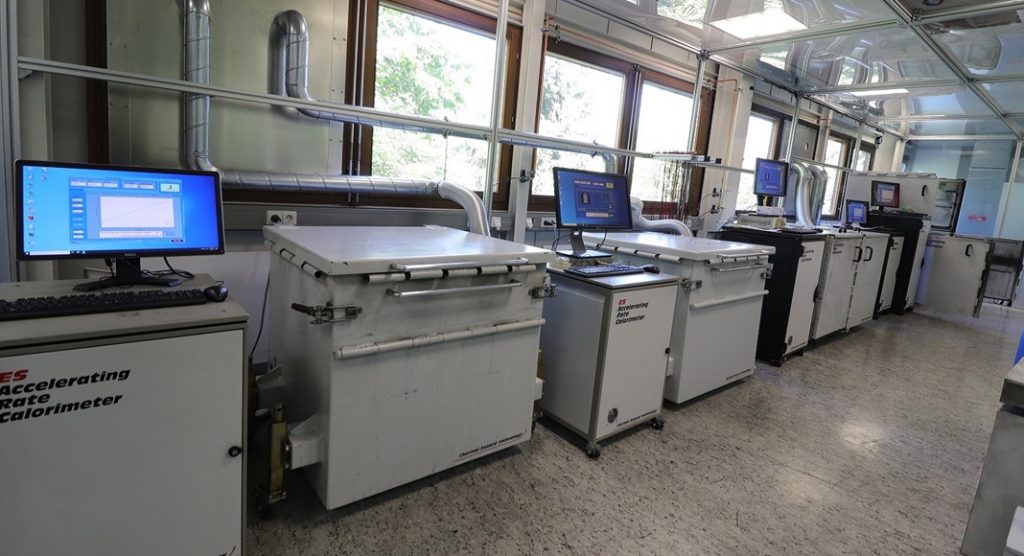
Thermal propagation studies in battery calorimeters
Safety testing is one of the main activities in the IAM-AWP Calorimeter Center that was founded in 2011 and currently operates Europe’s largest Battery Calorimeter Laboratory with six Accelerating Rate Calorimeters (ARCs) of different sizes – from coin to large pouch or prismatic automotive format (see Fig. 4). These robust battery calorimeters enable the evaluation of thermodynamic, thermal, and safety data for LIB on cell and pack level under quasiadiabatic and isoperibolic environments for both normal and abuse conditions (thermal, electrical, and mechanical).
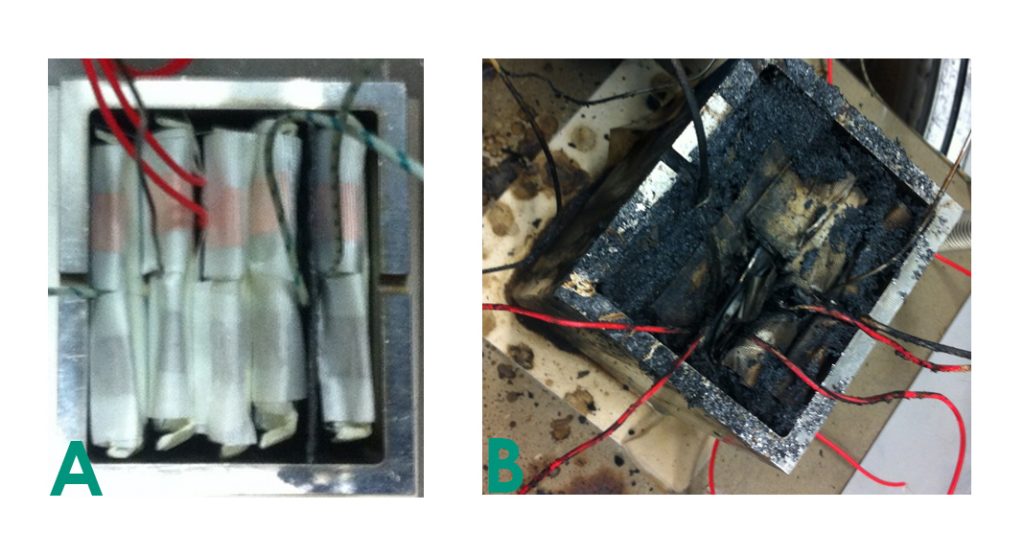
While the chances of an individual cell failing and starting a fire is extremely small (just one in several million), large UES systems can have 10 million or more lithium-ion cells packed into a small space. If just one of these cells fails and adequate safety measures are not implemented, a cascading effect called thermal propagation will almost certainly lead to a large-scale fire. This means that the thermal runaway propagates from one cell to the neighbouring cells, leading to the complete destruction of the module or pack (see Fig. 5).
Adequate safety measures include heat protection barriers between cells to prevent cascading fires, adapted control and monitoring systems, and proper ventilation of the potentially explosive gases. Using the setup shown in Fig. 5a, which consists of a metal box with a lid, mimicking a battery box for the largest ARCs, it is possible to study the thermal runaway propagation in small battery packs in order to develop and qualify suitable heat protection barriers. A heater mat is attached to one of the cells to initiate its thermal runaway by overheating. In front of the last cell to the right, the heat protection barrier material to be tested is installed and the time is measured until the thermal propagation reaches the last cell.
Many different material approaches have already been tested in our laboratory with the aim of finding the best solution for a certain application and cell type. Fig. 5b demonstrates a typical example for a destroyed battery pack after a thermal propagation test with an unsuitable heat protection barrier.
Safety studies of aged cells for second life applications
The increasing number of electric vehicles (EV) that are needed to decarbonise the transport sector brings the recycling and repurposing of EV batteries increasingly into the focus for many EV and battery manufacturers. Both strategies are needed in order to account for the limited raw materials resources.
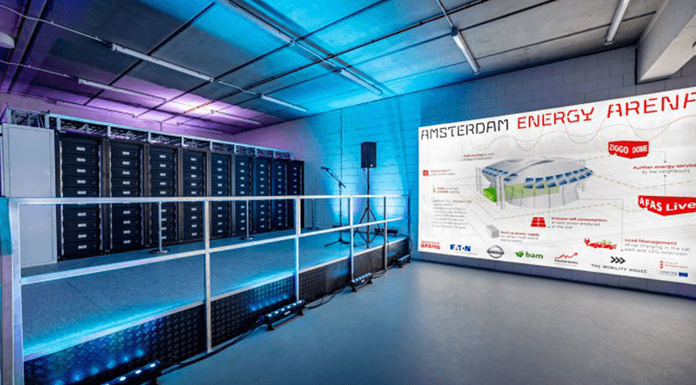
Repurposing means that used EV batteries that still retain up to 80 % of their initial capacity could still serve in other storage applications, which gives them a second life and increases sustainability. A prominent example is the Johan Cruijff ArenA in Amsterdam, Netherlands (see Fig. 6), where a three MW/2.8 MWh storage system made of battery modules from the equivalent of 148 Nissan Leaf battery packs was installed. The stadium also has a solar installation with 4,200 solar panels that can feed power to the battery system. This leads to a more reliable and energy efficient supply and contributes to a stable Dutch energy grid. In order to use batteries in such second life applications the following questions concerning their safety must be addressed:
- Does the cyclic and calendar ageing affect the safety level?
- What parameters need to be characterised after first life in order to decide which batteries can serve in a second life?
- What parameters need to be intensively monitored to ensure a safe second life?
The influence of ageing on the safety level is quantitatively determined by performing electrical, mechanical, or thermal abuse tests on the ARCs when the cells have reached a certain state-of-health (SOH) after being cycled for a certain time or after storage under defined temperatures and state-of-charge (SOC). A SOH of 80% means that 80% of the initial capacity is still available. The cells with several attached thermocouples are inserted in the calorimeter chamber (see Fig. 7), which has heaters and thermocouples in the lid, bottom, and side walls in order to follow and track the different stages of self-heating that occur during the abuse scenario which can include, for example, overcharging, penetration by a nail, or overheating.
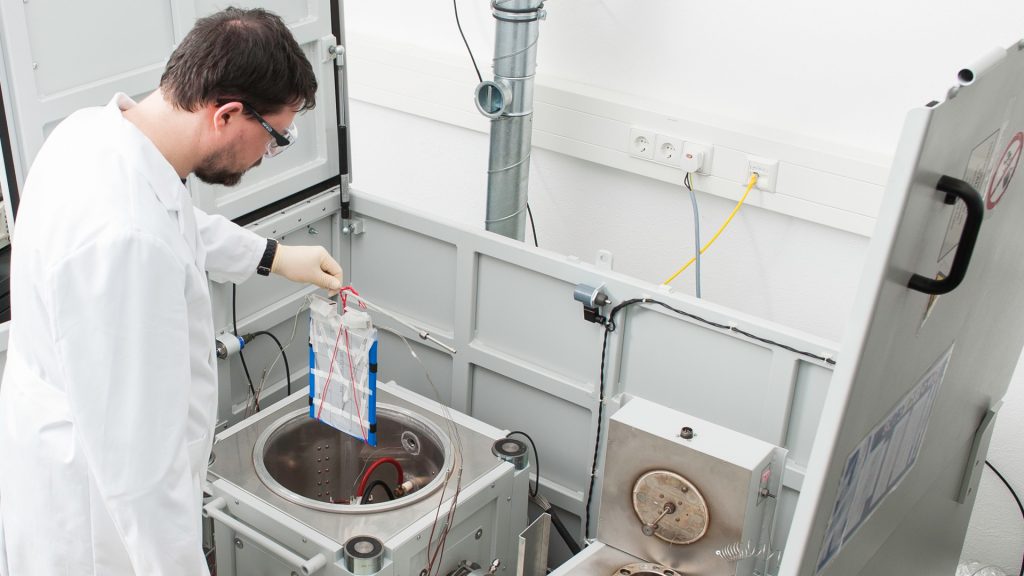
Currently, there remains a lack of publicly available data that would allow for a statement to be made on how the safety level is affected when it reaches a certain SOH in a certain type of cell. In the scientific literature there are examples for both cells that become more unsafe with increasing age and others where the decreased capacity leads to higher safety level. Therefore, tests in battery calorimeters are extremely valuable in order to find criteria and parameters that can help to decide which cells are suited for second life applications.