Nickel-based superalloys stand as the vanguard in materials engineering, wielding unparalleled resilience in high-temperature settings—a trait that renders them indispensable across various industrial applications.
When conventional materials like steel or titanium alloys succumb to extreme conditions, nickel emerges as the stalwart, providing robustness and steadfastness.
Their distinctive attributes owe much to specific alloying elements that augment their mechanical prowess.
This piece navigates through the realm of additive manufacturing (AM) concerning these robust nickel-based superalloys, presenting a thorough exposition of their fabrication processes.
Pioneering metallurgical insights
Understanding the metallurgy of nickel-based superalloys within additive manufacturing is pivotal.
These alloys uphold their strength even at temperatures surpassing 540°C, setting them apart from traditional counterparts and earning the title of ‘superalloy’.
The incorporation of alloying elements elevates both their mechanical traits and microstructural stability, which is vital for enduring high stress at elevated temperatures.
A granular metallurgical analysis unveils intricate interactions during the fusion-based AM process, leading to complex phase transformations within parts due to non-equilibrium solidification. This investigation offers valuable insights into controlling these interactions for optimal outcomes.
The microstructural stability of nickel-based superalloys profoundly influences their performance. Grain boundary segregation, where alloying elements concentrate along grain boundaries, can impact an alloy’s resistance to deformation and cracking at high temperatures.
Monitoring any microstructural variations resulting from changes in processing or composition becomes imperative.
Thermal behaviour also plays a pivotal role. The repetitive heating, melting, and cooling during fusion-based AM induce multiple thermal cycles, significantly shaping final characteristics like hardness and tensile strength.
Grasping how these cycles affect the microstructure aids in predicting potential defects or weaknesses before their emergence, amplifying overall efficiency and quality control within AM practices.
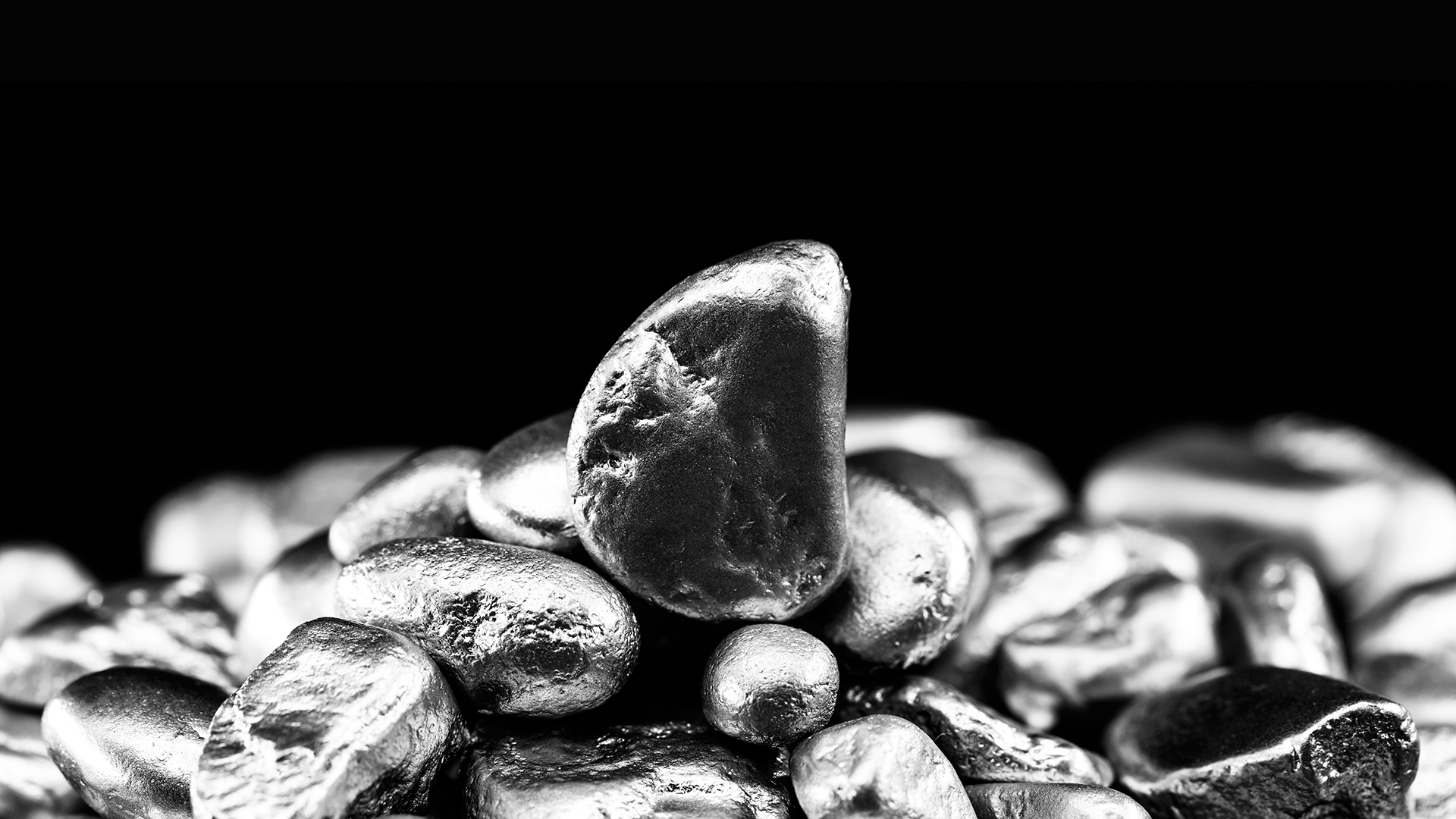
Embracing fusion-based additive manufacturing technologies
Fusion-based AM technologies wield laser or electron beams to trigger rapid solidification, contributing significantly to enhancing alloy properties.
The choice of feedstock, typically in powder or wire form, influences the resultant microstructure and performance attributes. Stringent quality control measures encompass precise process parameters and microstructure analysis, unveiling potential enhancements during production runs.
Post-processing techniques further refine nickel-based superalloys, diminishing porosity, enhancing mechanical properties, and refining surface finish.
The characteristics of powders, encompassing factors like morphology and size distribution, significantly influence processability. Powders with excellent flowability facilitate efficient melt flow into pores, augmenting overall product quality.
Alloy compatibility: Crucial considerations
Alloy compatibility holds a critical role in fusion-based AM. The non-equilibrium solidification process and complex melt flow experienced by parts necessitate thorough weldability analysis.
Understanding phase transformations within these superalloys becomes integral in ensuring structural integrity. Effective management of thermal history alongside strategies for controlling phase transformations optimises material bonding and performance under service conditions.
Deciphering mechanical properties
Evaluating the mechanical properties of nickel-based superalloys proves challenging due to their non-uniform microstructure post-AM processing.
Anisotropic properties, dependent on load orientation relative to the build direction, require comprehensive characterisation.
Traditional testing methods supplemented by advanced techniques like digital image correlation and thermo-mechanical fatigue are imperative for a holistic evaluation.
Simulation and modelling: Crafting precision
Advanced simulation techniques are crucial in unravelling the complexities of AM processes. Capturing transient temperature variations, incorporating Marangoni convection, and accounting for heat source movement ensure more accurate predictions.
These simulations offer insights into compositional effects on microstructure, guiding alloy design specific to AM-processed nickel-based superalloys.
Crafting alloys for the future
Designing alloys for AM-processed nickel-based superalloys demands consideration of composition, microstructural control, process optimisation, and surface finish.
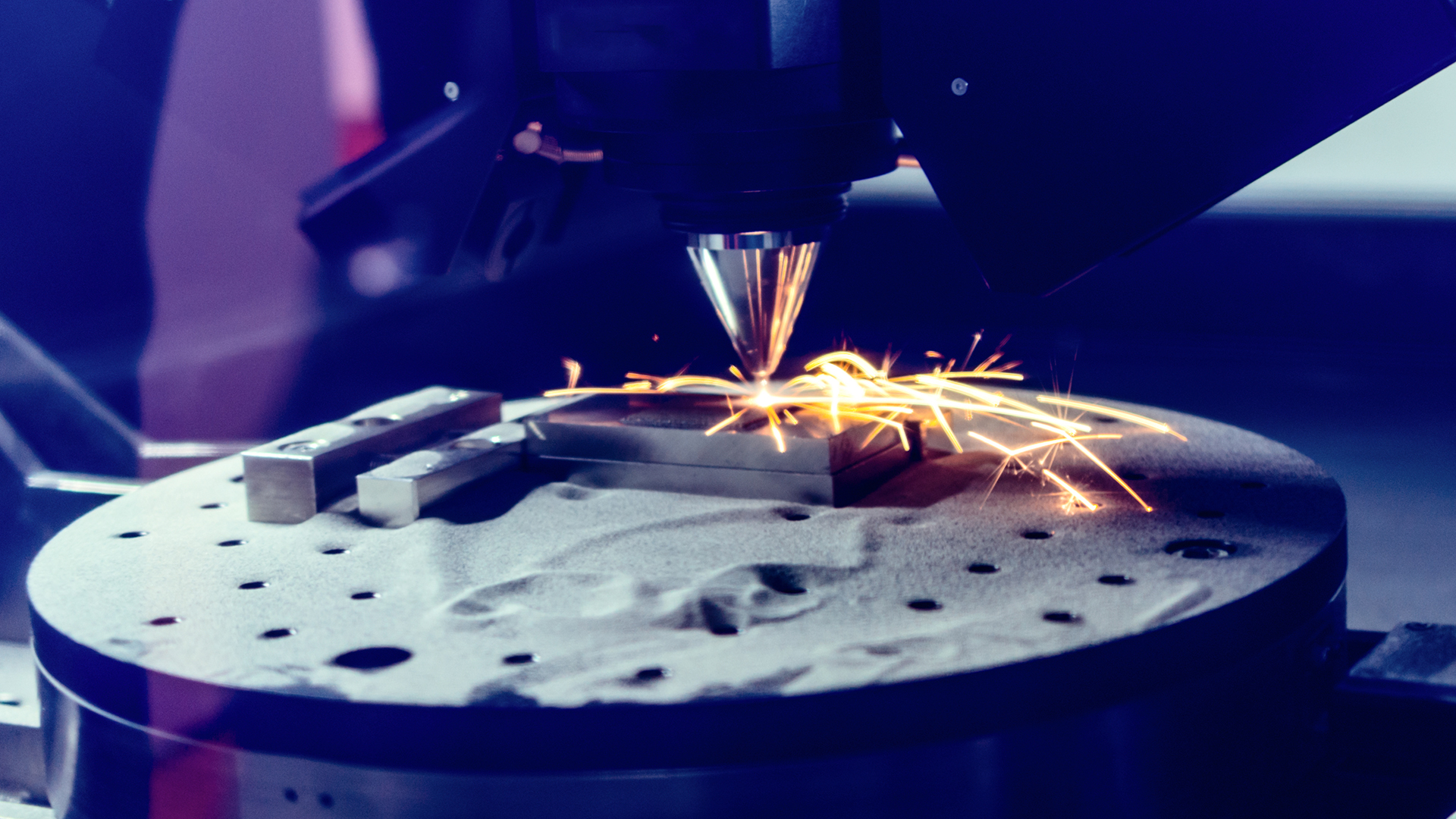
© shutterstock/Nordroden
These integrated factors elevate fabrication and mechanical properties, paving the way for high-performance applications. Continuous advancements in this domain promise further exploration of AM technology’s vast potential.
Charting future research frontiers
Future explorations in this field revolve around advancing process control, mitigating defects, innovating scan strategies, optimising beam profiles, and establishing online process monitoring.
These endeavours not only enhance product quality but also fortify mechanical properties, ushering in reliability, which is crucial for demanding applications associated with nickel-based superalloy components.
In conclusion, nickel-based superalloys, forged through additive manufacturing, stand as the cornerstone of modern engineering prowess, offering unparalleled strength and endurance in the face of extreme conditions.
Their continued refinement and exploration through advanced methodologies promise a future of even greater innovation and utility in high-performance applications.