Sichuan Calciner Technology is employing techniques and processes used in cement engineering to revolutionise lithium extraction around the world.
Sichuan Calciner Technology Co. Ltd (SCT) left its first footprints in cement engineering, cultivating and nourishing the land of engineering design and EPC in 23 countries across the world. Cement engineering and spodumene extraction engineering share the common features of high-temperature calcining and milling, making spodumene extraction a logical next step for SCT.
In 2011, SCT first began engineering spodumene calcining and milling, in which SCT made the ground-breaking practice of transplanting the sophisticated know-hows from the cement industry – such as preheater, grate cooler and pre-homogenisation – into the spodumene-to-lithium industry. Good performances in respect of energy consumption per unit (ton) product and automation have caught the attention of intra-industry players, as this creative practice has injected something never-seen into the traditional spodumene calcining.
Jiangfeng Zhang, Vice President of the Lithium Industry Branch of China Nonferrous Metals Industry Association said: “When SCT stepped into the lithium industry, it brought about so many revolutionary ideas.”
SCT’s expansion into the lithium industry
For over a decade, SCT has been expanding in the lithium industry, with its reach extending across: spodumene calcination to acid roasting, leaching and full-line process design (lithium carbonate and lithium hydroxide) and the engineering of production trains for cathode material, lithium iron phosphate.
SCT has completed fundamental investigations and experiments on the spodumene/lepidolite concentrate from dozens of different lithium minerals across the world in the search for lithium ore characteristics and optimal lithium recovery rate. This is to ensure our clients can be provided with different, targeted process solutions and proprietary equipment packages.
The SCT exhibition room displays a dazzling array of spodumenes, which were gathered little by little. SCT’s engineering experience in lithium extraction technology has been built up in the same way – little by little. For each project, SCT embarked on the study of the physical characteristics of spodumene concentrate, which set up the basis for innovative and distinctive practices made for each project.
In the subsequent commissioning and technical services, a large quantity of first-hand data can be obtained. In this way, the experience from previous projects can be considered and utilised in the next project design. With this continuous summary and persistent improvement, SCT occupies the commanding height of technology and remains excellent and innovative.
Currently, the overwhelming majority of lithium production trains (whether in operation or not) both in China and around the world, are designed by SCT. By the first half of 2023, SCT had completed 61 production trains of lithium carbonate and lithium hydroxide, with more than 30 trains already in operation.
The lithium production trains designed by SCT cover nearly all the lithium material suppliers, including three global top companies, with the total design capacity more than one million tons. This accounts for more than 85% of the overall market share in China and over 60% in the world.
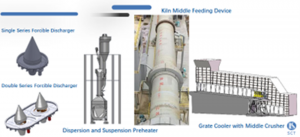
Besides, SCT owns more than 40 National Utilisation Patents and five National Invention Patents. It has been granted the certificate of ‘National High-tech Enterprise’ and titles including ‘Specialised and Sophisticated SMEs of Sichuan’ and ‘National Little Giant Firm of Specialised and Sophisticated SMEs’ among other honours.
In 2023, the spodumene-lithium extraction technology developed by SCT was evaluated as being ‘internationally advanced’ by Sichuan Provincial Technology Transfer Centre.
Successful technology transition into lithium industry
Tianqi Lithium had two production trains in operation before, producing 3,000 tons per annum (tpa) and 5,000 tpa Li2CO3. The trains adopted the traditional hollow rotary kiln (material straightly goes inside and comes out) for material calcining and the water-spray single-cylinder cooler for material cooling. Such an arrangement was inefficient and required improvement.
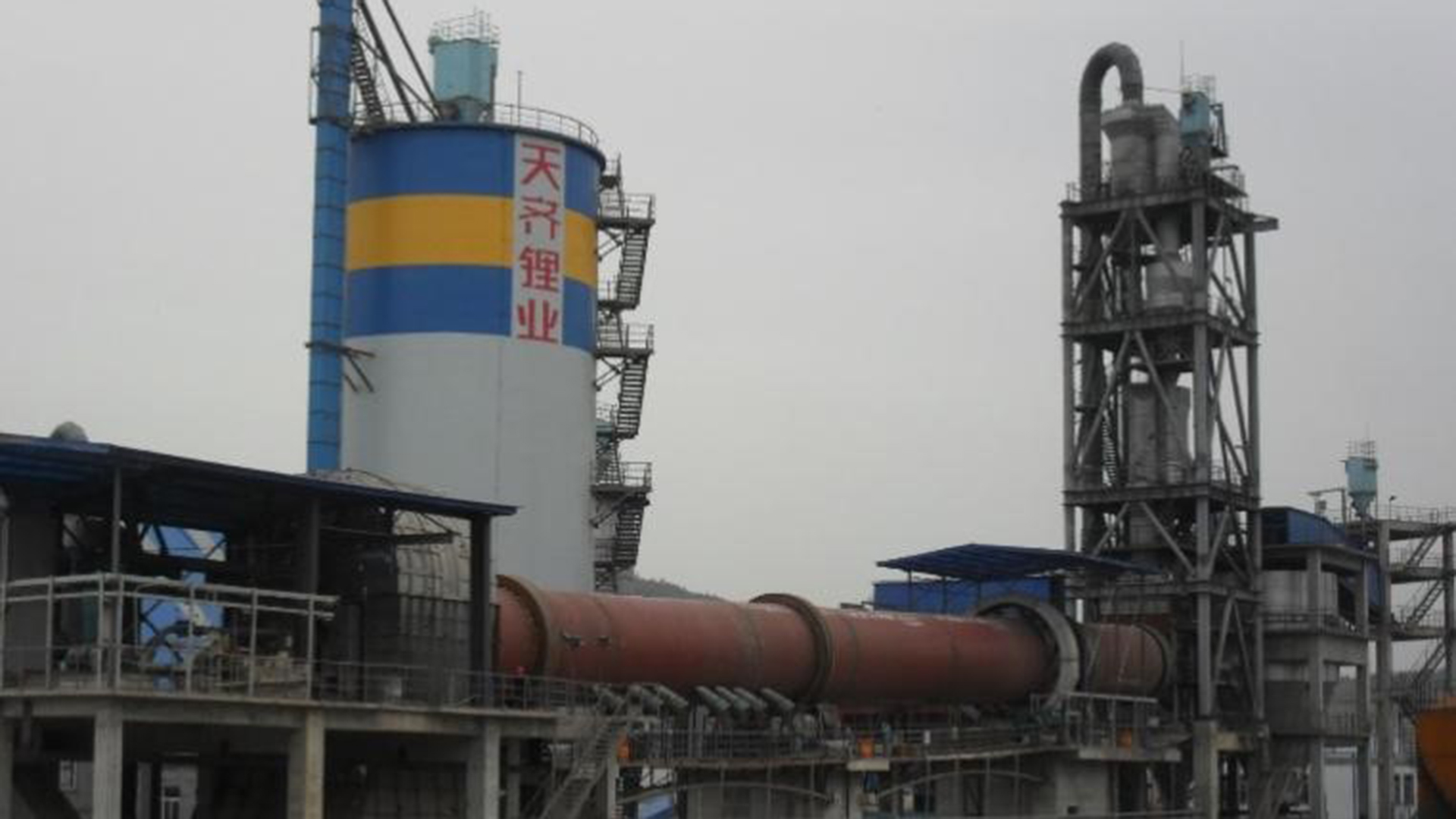
In 2011, SCT took up the engineering, for Tianqi Lithium, of a spodumene calcining facility with a lithium carbonate production train of 20,000 tpa. Here, SCT came up with the pre-homogenisation process for spodumene and raw coal, replacing the overturning, radiating heat exchanging process with suspension heat exchanging, as well as substituting the water-spray and single-cylinder cooler with air-cooling and a fine-powder grate cooler.
The practical performances have verified SCT designs effective by proving that the design capacity was achieved three months after commissioning, with a stable output capacity of 600 tons per day (t/d) for the rotary kiln, and 50% of energy consumption reduced when compared with the old train.
This is the first spodumene calcining project designed by SCT the acquired different experience from cement calcination and the SCT-specialised spodumene calcining process came into birth.
Dedicative commitment in process and technology to achieve product diversification
A lithium extraction project includes two areas – Pyromet and Hydromet. The former is similar to the cement process while the latter is categorised into inorganic chemical technology. What SCT firstly came up with was to transplant the sophisticated cement know-hows into spodumene calcining.
For the acid roasting of β spodumene, SCT developed two types of acid roasters – outer heating and internal heating, which inherited the design embodied in the production trains of Yin Li New Energy, Yahua Lithium, Sichuan Energy Investment and others.
For the project invested by AVZ in Congo (Kinshasa), SCT creatively came up with the process of lithium sulphate crystals that helped reduce the transportation (extremely expensive) costs for lithium ore. The process can not only effectively reduce the carbon emission, but also decrease the product transportation cost with the lithium slag refilled back into mining area.
Starting with the process of lithium sulphate, SCT successfully developed its proprietary solution for the lithium production train by the investigation and combination of the process features practiced in different lithium production trains in China.
Recently, SCT has engineered more than five full-line lithium production trains. SCT broadened the design scope further in the lithium iron phosphate production train in Qujing, Yunnan in China by converting African amblygonite to lithium iron phosphate.
Empirical summary and technological innovation
Different-origin spodumenes vary from each other in terms of physical features and chemical compositions, with moisture ranging from 5-18% and particle size varying from micrometre to millimetre. Therefore, the selection of treatment schemes and main equipment varies from one project to another because different projects will process different lithium ores.
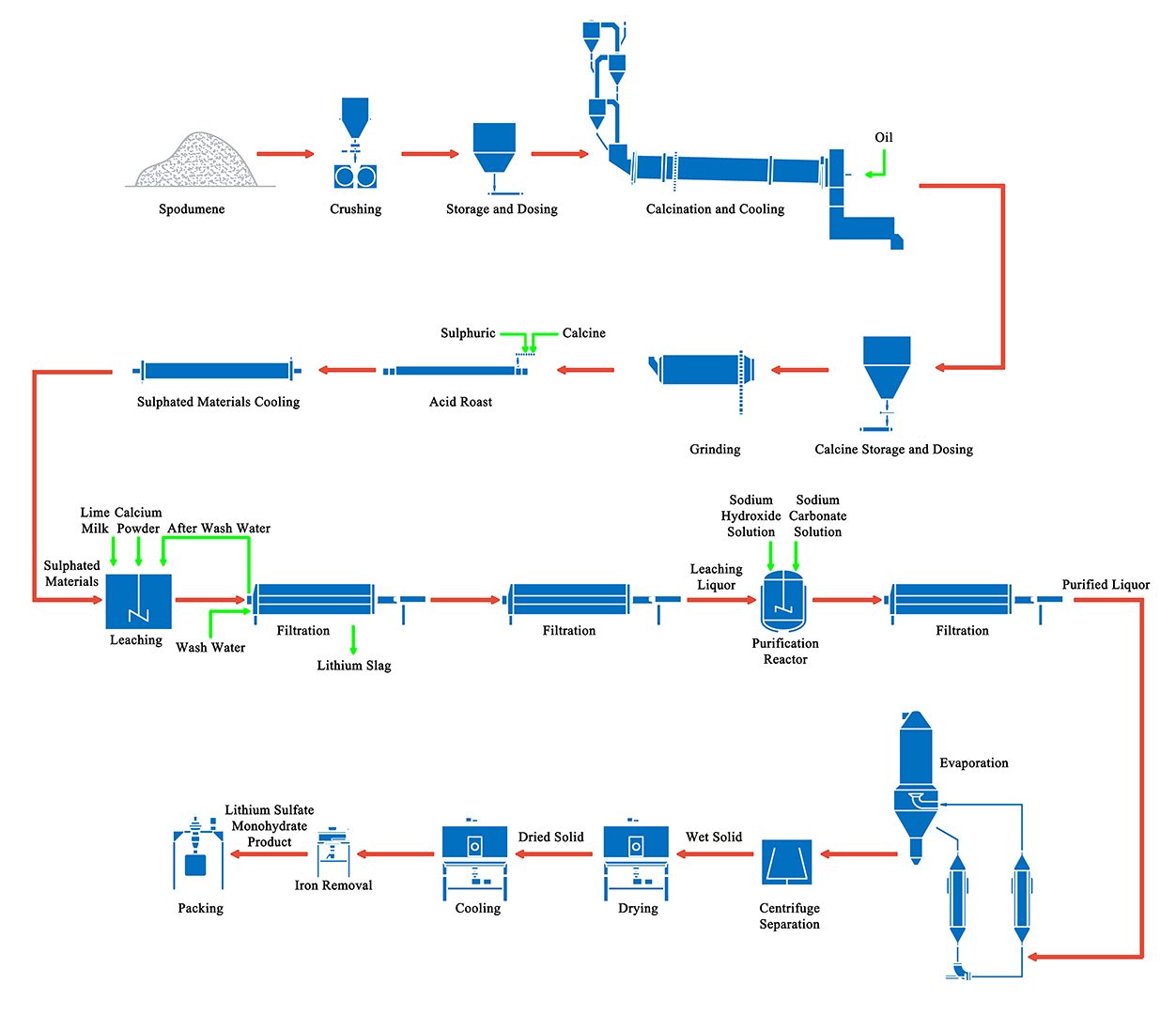
Other than for common-used spodumene and lepidolite, recent years have seen that some lithium ores such as amblygonite, petalite, lithium clay and other types – which require far more complicated processes than spodumene – are being exploited. One African lithium ore may be composed of various ores, meaning that spodumene contains lepidolite and amblygonite, and hinting that the calcining and utilisation of lithium ore will be of higher difficulty.
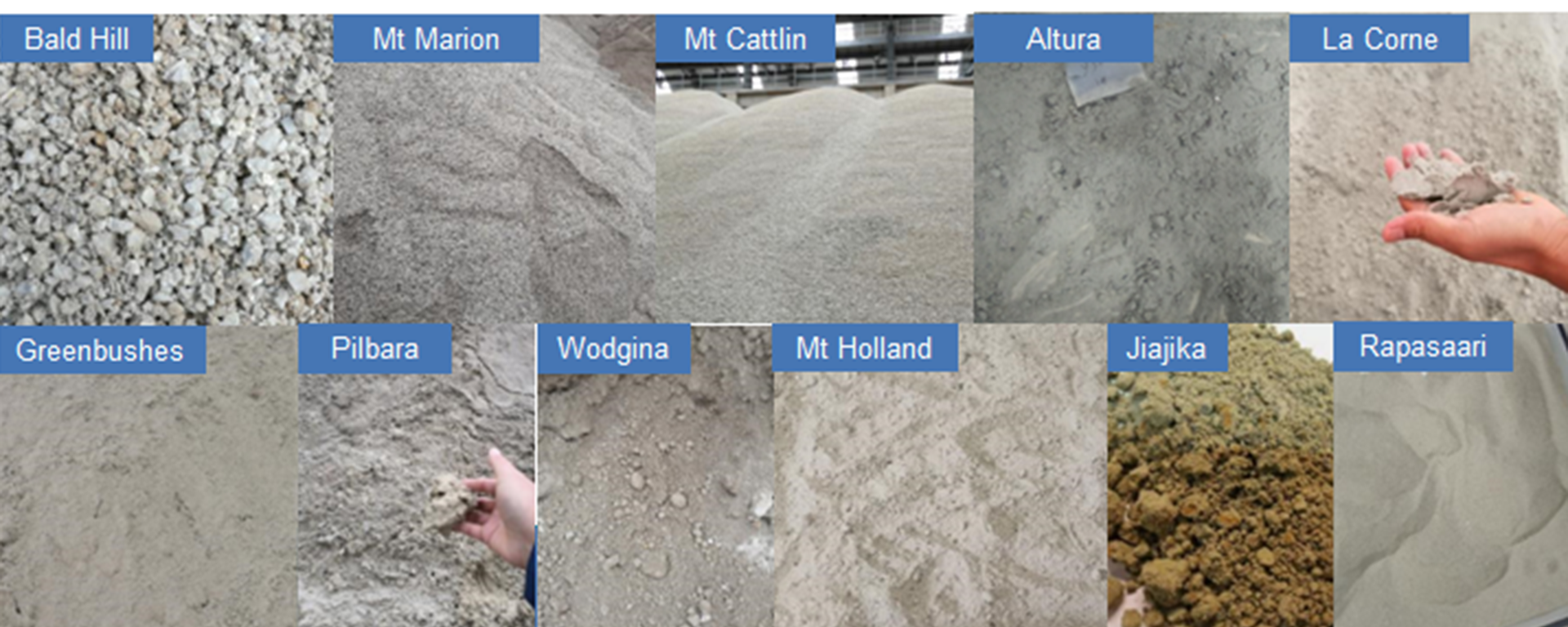
SCT starts the study on raw material characteristics by performing static experiments: Calcining experiments in a small-size rotary kiln and acid roasting experiments so that our clients can be served with optimally proper process design.
The calcining system involves preheating system with multi-stage cyclones, and the quantity of cyclones will depend upon the grade, particle size, and moisture of the raw material.
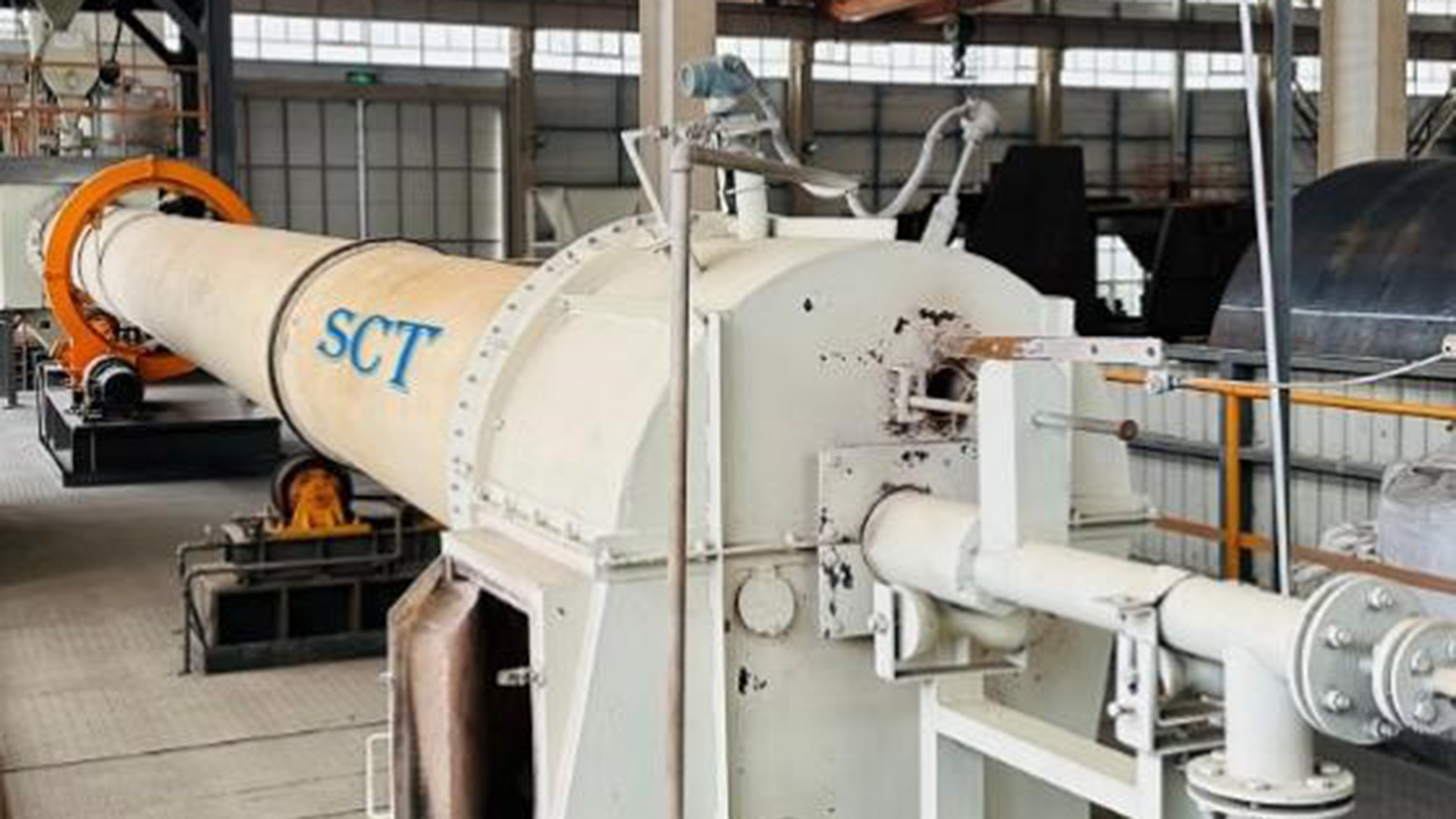
The experiments on different lithium ores will support engineering applications with fundamental data generated in the experiments.
In one project in Hebei, China, when confronted with the caking of high-iron content spodumene in the rotary kiln, SCT set up an intermediate high-temperature roller crusher in the middle part of grate cooler. This allows the caked material to be crushed when passing through this machine before continuing the cooling process at the back end, a configuration that helps to eliminate the occasion where high-temperature material comes out of the grate cooler.
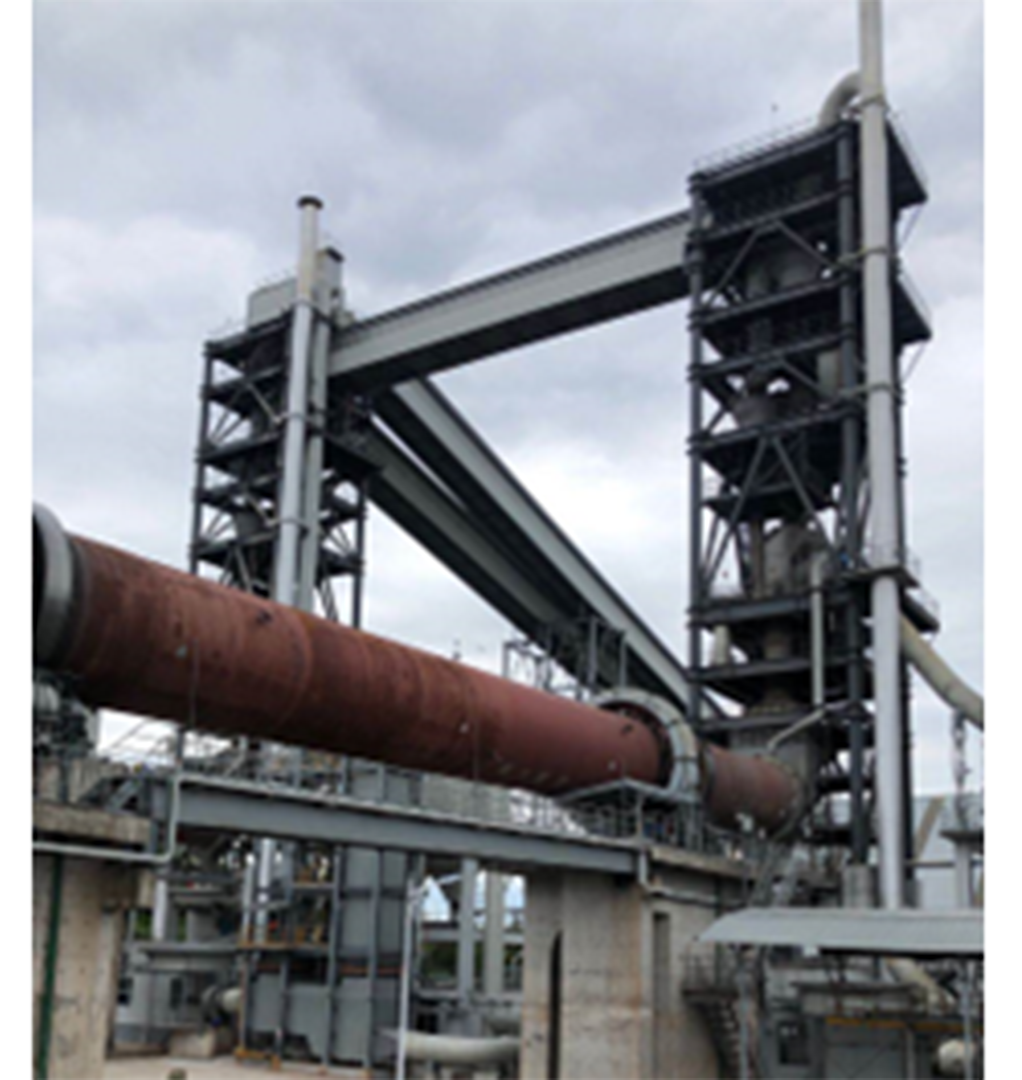
In 2021, SCT performed the first trial operation for the grate cooler with intermediate roller crusher in which the expected performances were achieved. Since then, the intermediate crusher roller has become the standard and necessary option for the extraction engineering of high-iron content and high clay content lithium ores.
SCT’s first overseas project is the ChengTok Lithium Project with two trains, each producing 40,000 tpa and invested in by Chengxin Lithium in Indonesia, featuring the largest calcining kiln for one train in the world, with a capacity of 1,200 t/d.
SCT is currently developing a spodumene conversion solution in which one single rotary kiln can even calcine a certain amount of raw material (spodumene) producing approximately 5-6 tpa lithium products, and this will be applied very quickly in future engineering.
Optimisation and upgrading of lithium production train
Tianqi Lithium acquired the production train with 17,500 tpa lithium carbonate owned by Galaxy Resources Limited in Zhangjiagang. In this train, the design capacity of spodumene calcining system is 15t/h, while the actual capacity is around 9.5 t/h since it’s been in operation.
In the middle of 2016, Tianqi Lithium entrusted SCT to perform the technical upgrading and modification of the old trains. SCT added a suspension preheating system which helped to rise the spodumene feeding temperature from indoor temperature to 300°C.
Additionally, the front end of water-spray single-cylinder cooler was set up with an short section of air heat exchangers so that the temperature of feeding combustion air was raised from 200°C to 600°C.
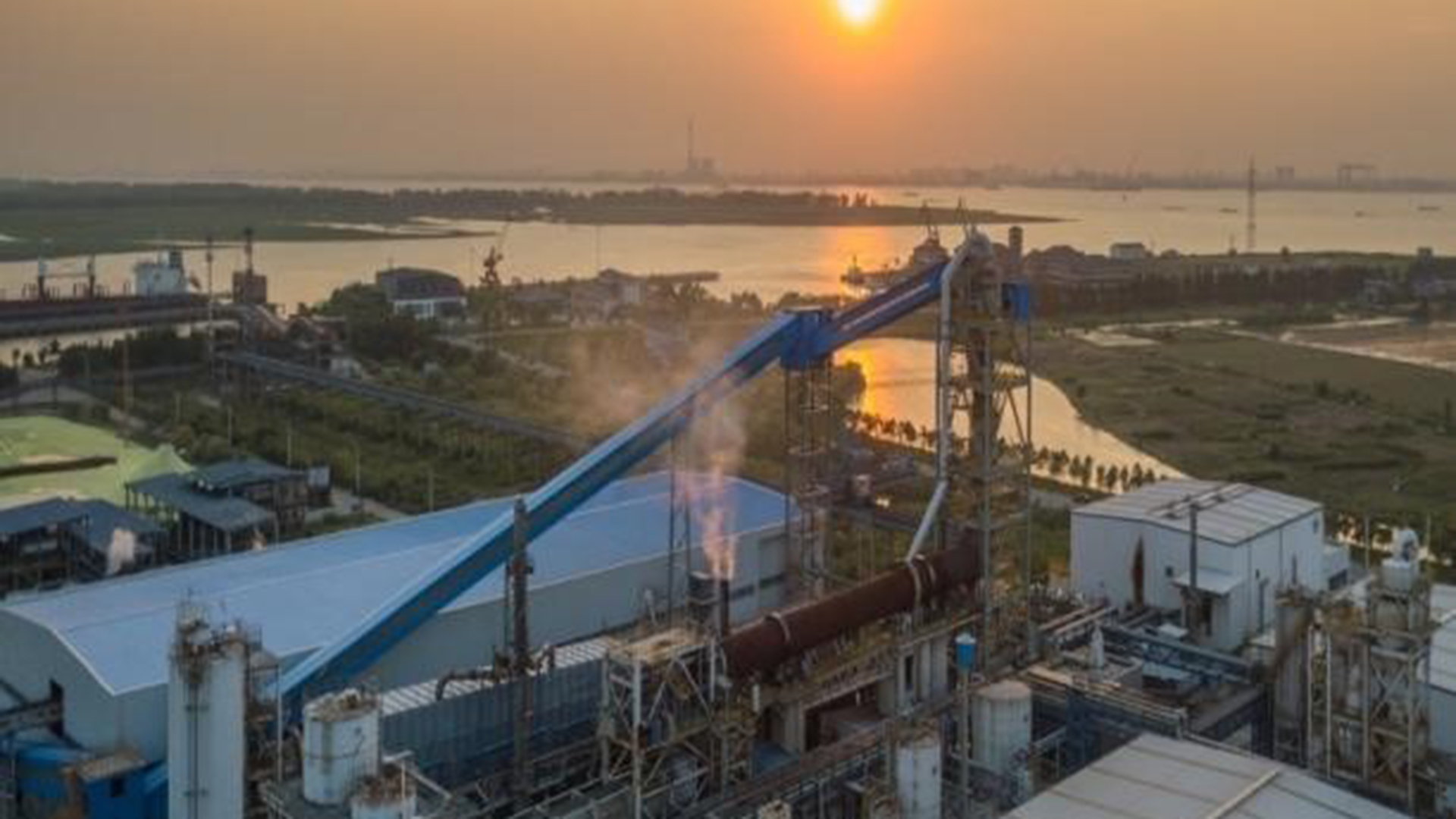
The production capacity for calcining system reached 12 t/h on the third day of its re-operation. The seventh day saw capacity reach 18 t/h, double that of the old trains, with energy consumption per unit ton of spodumene astonishingly decreasing by 35%.
The production and standard satisfaction in this project have greatly enhanced the reputation of SCT in lithium industry, and established the foundations for SCT to be a global leader in pyrometallurgical technology.
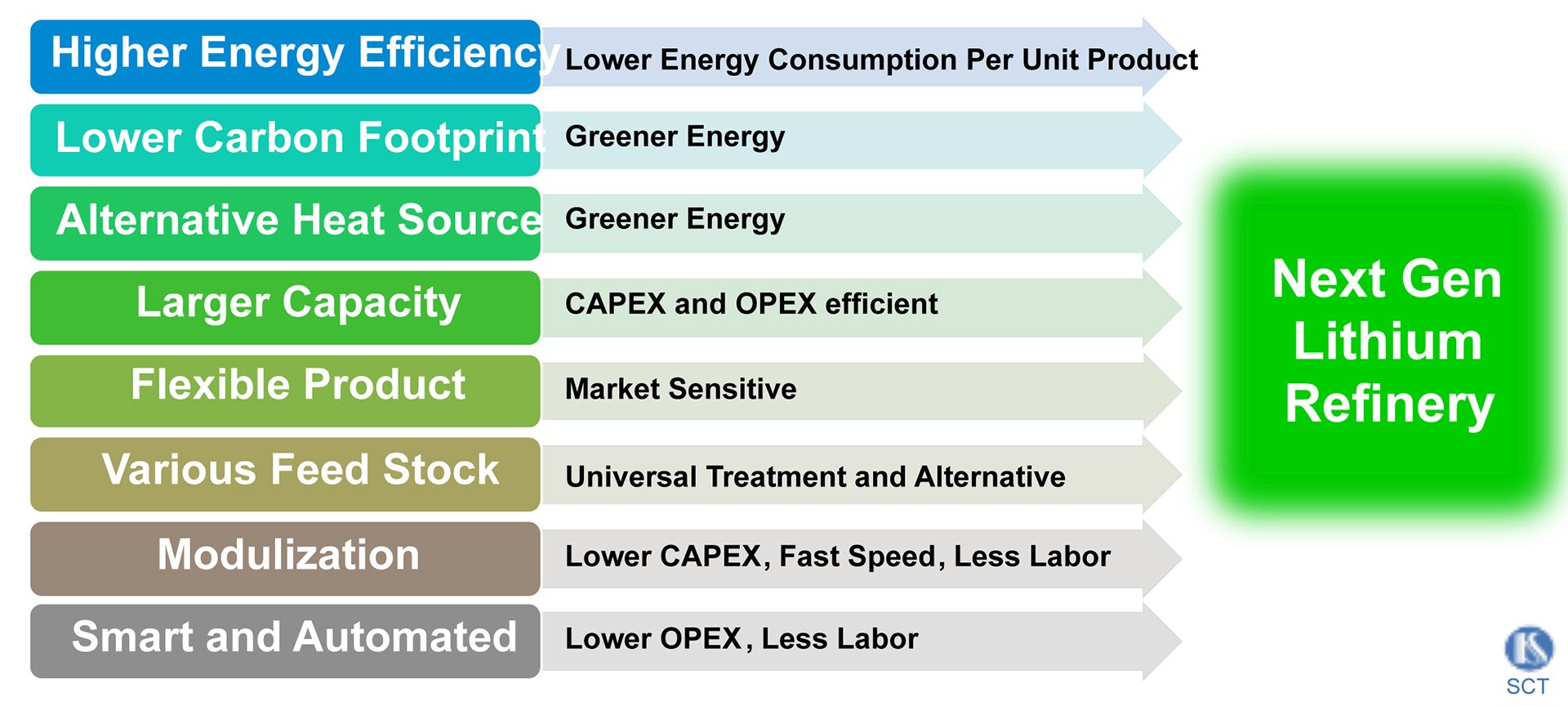
Lithium extraction outlook
Services SCT can provide:
• Spodumene-to-lithium laboratory and/or pilot experiments
• Innovative spodumene-lithium process
• Intelligent management and control for production train and smart laboratory system
• Comprehensive study on the utilisation of lithium slag
• Engineering design, consulting, EP, EPC, EPCM
• Initial Studies: Scoping, pre-feasibility, definitive feasibility
• Various Engineering and Study Reviews
• Full Disciplines Engineering: Basic Design, FEED, detailed design
• Equipment: Engineering, manufacturing, procurement and support
• Commissioning
• Production management and maintenance
• Performance guarantee
• Project diagnosis and upgrades
Please note, this article will also appear in the sixteenth edition of our quarterly publication.