Dr Carlos Ziebert, leader of the group Batteries – Calorimetry and Safety, KIT, details the Modelling of Battery Gassing project, examining how calorimetry and thermodynamic modelling help to improve our understanding of battery gassing and the effects on cell ageing and safety.
To guarantee a permanently high performance of lithium-ion batteries (LIB) in long-term operation, the perfect interaction of the constituent components – such as electrodes, electrolyte, separator and current collectors – is required. However, extensive material reactions take place during permanent charging and discharging, but also during the initial battery formation, which can adversely affect the behaviour of the LIB.
The reactions of the liquid electrolyte, and the associated gas formation, play a decisive role in cell ageing and cell safety. These reactions are, therefore, core to the Modelling of Battery Gassing (BattGas) project, which is funded by the German Federal Ministry of Education and Research (BMBF) and belongs to the new battery competence cluster battery usage concepts (BattUse). The BattUse competence cluster has received funding of €20M and aims to foster our understanding of battery behaviour to determine when the second use of battery storage is preferable.
Aims of the Modelling of Battery Gassing (BattGas) project
The Modelling of Battery Gassing (BattGas) project started on 1 October 2020 and is coordinated by the Institute of Applied Materials – Applied Materials Physics (IAM-AWP) at Karlsruhe Institute of Technology (KIT). The two other partners are the Institute for Power Electronics and Electrical Drives (ISEA) at RWTH Aachen University and the Münster Electrochemical Energy Technology (MEET) at the University of Münster.

The aim of the project is to develop electrolyte ageing models in combination with battery models for the early prediction of cell behaviour in the usage phase. The work at the IAM-AWP focuses on two areas.
Firstly, extensive battery calorimetric measurements are carried out on the active materials and the electrolytes as well as on the cells for consistent modelling to better understand the changes and to reveal the decomposition mechanisms of the electrolyte and the simultaneous build-up of gas pressure during cell use.
Secondly, the results of the calorimetric measurements are included in thermodynamic modelling of the electrolyte components, the additives, and the electrode materials with the help of CALPHAD (CALculation of PHAse Diagrams) methods, which are used to calculate phase diagrams and thermodynamic functions that are implemented in the overall model that will be provided by ISEA.
This overall model will finally enable a detailed understanding of the decomposition of the battery electrolyte in the course of battery use and the effects on ageing. In this way, safety can be increased, and the LIB can be operated much longer without disruption, which increases its sustainability. Likewise, by transferring the model to newly developed materials and cells, their time-to-market is shortened, which allows the model to check performance and service life with regard to electrolyte ageing at an early stage.
The work at the IAM-AWP can be divided into work at the material and cell levels. At the material level, calorimetric investigations of the cell components were carried out using highly sensitive Tian-Calvet calorimeters and differential scanning calorimeters. From these measurements, thermodynamic data of the electrolyte components ethylene carbonate (EC) and ethyl methyl carbonate (EMC) were modelled using the CALPHAD method using the Thermo-Calc software. At the cell level, the cells built and provided by the partner MEET were formed and characterised, enabling a calendric ageing study to begin.
Furthermore, electrochemical-calorimetric tests were carried out on cells under isothermal and adiabatic conditions. Fig. 1 above illustrates the different aspects of the project. The work at the IAM-AWP, which contributes to modelling battery gassing, is particularly highlighted here. This allows the influence of gas formation on cell behaviour to be mapped.
Electrochemical and thermal cell characterisation
Pouch cells with a nominal capacity of 5Ah were manufactured by the MEET battery production line and made available to KIT without formation. Three different cell variants were produced, which differ in terms of their electrolyte composition. Graphite is used on the anode side and Li (Ni0.6Mn0.2Co0.2) O2 (NMC 622) on the cathode side. The electrolyte for all three cell types is a mixture of the organic solvents EC and EMC in a ratio of 3:7. This composition without additives represents the reference cell.
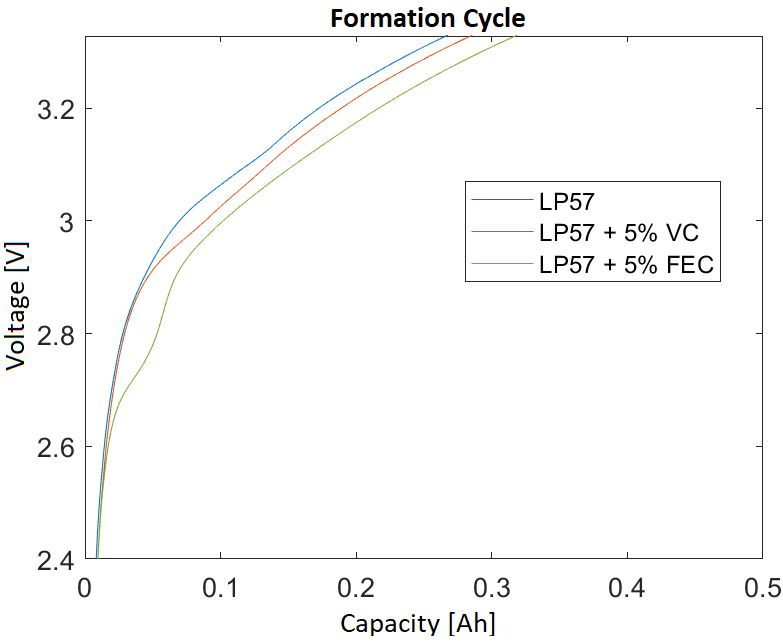
The influence of additives on battery gassing
To investigate the influence of the additives on gas formation, cells were provided with 5 wt.-% vinylene carbonate (VC) or fluoroethylene carbonate (FEC) provided as an additive. At the IAM-AWP, the pouch cells underwent a formation procedure. Fig. 2 shows the formation cycle of one cell of each type. The cycle efficiency was about 80% for all three cell variants. The discharge capacity in the first cycle of the cells with additive was higher than that of the reference cells. This can be explained by the decomposition of the additives instead of the electrolyte. Fig. 2 shows in detail the different voltage curves before the potential limit of 3.0 V is exceeded for the first time. Due to the lower decomposition voltage of the additives, they are decomposed instead of the electrolyte.
After formation, the cells were degassed and resealed to remove the gases that developed during formation from the pouch bag. Gas samples were taken from individual cells and analysed qualitatively in a gas chromatography-mass spectrometer (GC-MS) Perkin-Elmer Clarus 690 Arnel 4019. Using various valves within the GC-MS, the gases are separated after the first column and flushed with the carrier gases argon and helium at specific times to prevent such overlapping. The gas flows are measured separately by two thermal conductivity detectors (TCD).
Furthermore, some of the gases are also measured via the connected mass spectrometer, since molecules with a high mass can be specifically detected here. Products typical of the decomposition of the electrolyte or the additives could be detected. These are CO, CO2, methane, ethane and ethene.
The influence of temperature on battery gassing
After resealing and performing ten charge and discharge cycles, thermal tests were carried out on selected cells to determine the heat capacity using highly sensitive heat flow sensors (HFX) that were attached to the centre of the pouch cell surface. The ambient temperature of the cell was increased in steps of 10°C and the mean heat capacity in the temperature range was determined from the resulting heat flow. Fig. 3 shows the results of determining the heat capacity of a cell in the temperature range from 10 to 50°C. To evaluate these measurements, an evaluation routine was created using MATLAB software.
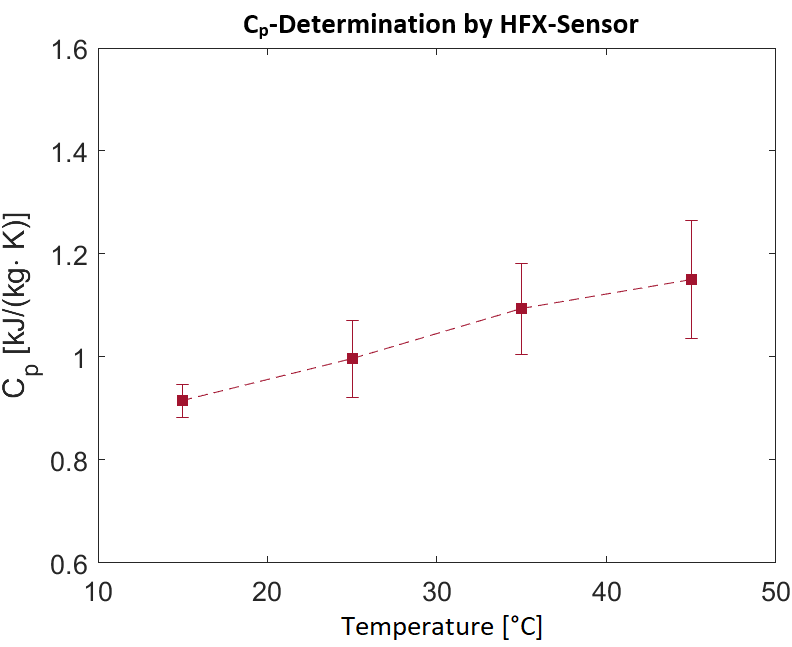
The first isothermal measurements were carried out and cells were cycled in a climate chamber at 25°C with different C-rates (0.2C, 0.5C and 1C). The change in surface temperature during cycling was recorded by thermocouples. In addition, a heat flux sensor was attached to the top and bottom of the cells to determine the heat generated by the cell during cycling.
Thermophysical measurements on cell components and thermodynamic modelling
An intensive literature search for available thermodynamic data was carried out to determine which thermodynamic data are already available for the thermodynamic modelling to be performed. As part of this literature search, it was found that there are only a few published data on the electrolyte solvents ethyl carbonate and ethyl methyl carbonate, some of which contradict each other. The published thermodynamic data, such as heat capacities, are only given for temperatures up to 50°C.
However, as part of the thermodynamic modelling, the electrolyte is to be modelled down to the gas phase, so separate thermodynamic data must be determined for this. For this purpose, experiments using differential scanning calorimetry (DSC) were carried out to determine the heat capacity of the electrolyte components EC and EMC in a wide temperature range. The determined heat capacities agree well with literature data, which were evaluated by NIST.
The determined heat capacity values were incorporated into the thermodynamic modelling using the CALPHAD method. The data was entered into a so-called POP file, which is necessary for the process of creating the thermodynamic modelling. This contains the experimental data on which the thermodynamic modelling is optimised.
Furthermore, a so-called TDB file was created for the thermodynamic modelling, which contains the basic model of the thermodynamic modelling. This also contains the variables adjusted as part of the modelling. These variables were iteratively adjusted as part of the modelling so that the data calculated with the modelling correspond to the literature data as far as possible.
How industry can utilise our methods
The development of new measuring methods for the Tian-Calvet calorimeter and the establishment of a method for determining the heat capacity of cells of any format as a function of temperature has already begun. These methods can be offered to industrial partners as contract measurements immediately after the end of the project and they can be supported in establishing them in their own company.
In principle, the prerequisites are very good for the scientific work to quickly lead to technologically and economically usable results which can be further developed into market-relevant measurement methods within industrial cooperation. This serves both the mission of the cluster BattNutzung (Battery Utilization Concepts) and the innovation pipeline of the BMBF umbrella concept for the German battery research factory.