A nuclear technology, molten salt reactors (MSRs), once considered to power aircraft during the Cold War, is now on the cusp of lighting our homes. Here, the University of South Carolina’s Professor Ted Besmann details the concept, history, and future potential of MSRs.
‘Everything old is new again,’ the title of a Peter Allen song, should probably include nuclear energy from reactors fuelled, or simply just cooled, by molten salts. The MSR systems use liquid salts as reactor coolant, instead of the water commonly used in almost all of today’s reactors. Moreover, the fuel for most MSRs (uranium or plutonium) is dissolved in the salt melt, serving as both fuel and reactor coolant. The concept of salt for fuelling/cooling an MSR can be likened to table salt (sodium chloride) heated above the melting point.
History of molten salt reactors
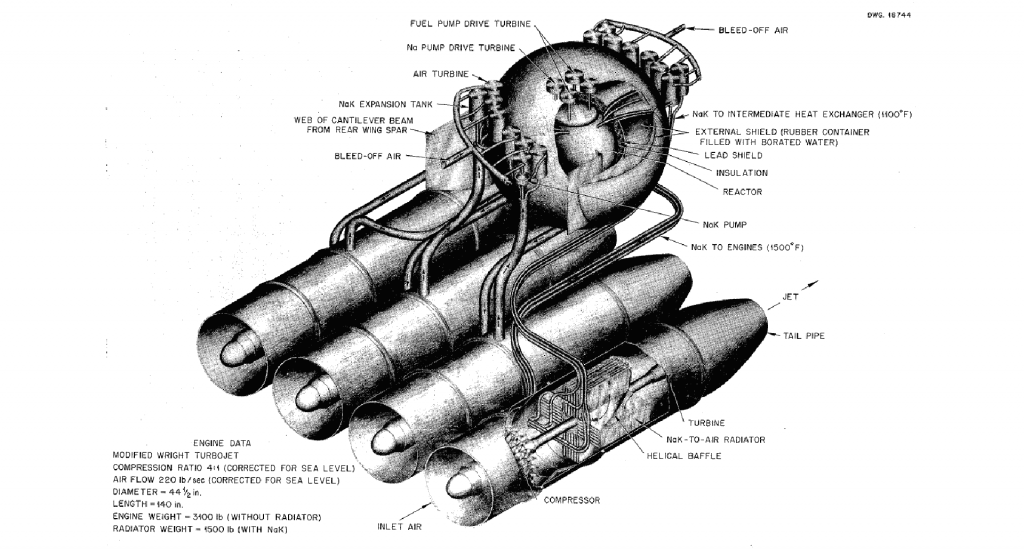
The idea of using MSRs arose in the 1940s when the US primarily relied on its jet-powered bomber fleet to deter the Union of Soviet Socialist Republics (USSR). Intercontinental ballistic missiles (ICBMs) and submarine launch platforms were not yet well developed, leaving bombers as the primary retaliatory threat keeping war at bay. However, the planes could not fly to their targets in Russia and return on a load of fuel, requiring landing in a third country after a mission or engaging in what was, at the time, difficult and risky in-flight refuelling. In response, the US started the Aircraft Nuclear Propulsion (ANP) programme to develop a nuclear-powered aeroplane that could remain in the air almost indefinitely.
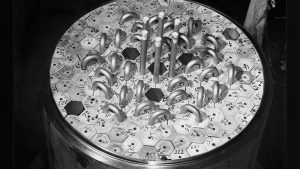
A compact MSR held the most promise for successfully powering a plane, and thus a small system, the Aircraft Reactor Experiment (ARE), was built at the Oak Ridge National Laboratory to demonstrate the concept. In 1954, that first MSR operated with a sustained nuclear chain reaction for nine days, generating a peak power of 2.5 MWt. In the ultimate concept, fission would heat the salt in the reactor core which would then be pumped in a continuous loop to a heat exchanger in the aircraft engines where it would heat entering air, and its expansion would create thrust/and or run a turbo-fan as it exited the back of the engine. ANP was, however, ultimately doomed by the overwhelming issues, including the excessive weight of the shielding needed to protect the crew from radiation.
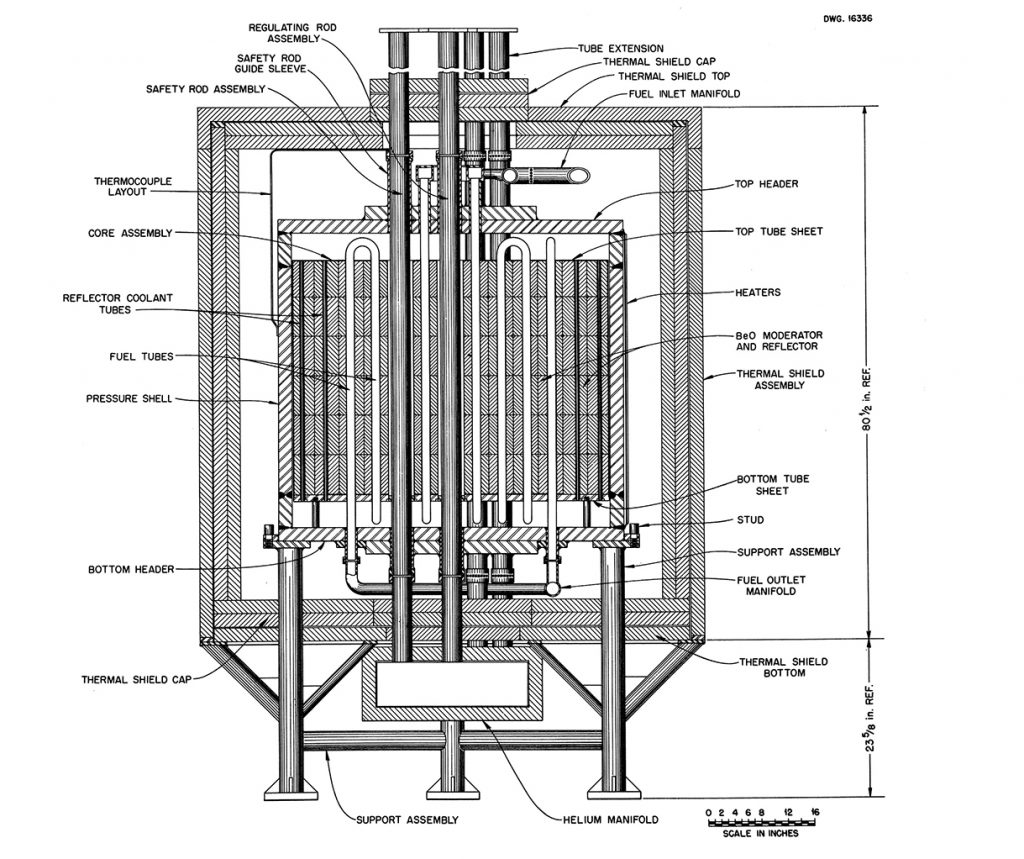
Molten Salt Reactor Experiment
Whilst it failed as an aircraft powerplant, the MSR demonstration excited those involved at Oak Ridge National Laboratory and led then Director Alvin Weinberg to convince the Atomic Energy Commission (predecessor to the U. S. Department of Energy) to fund a power reactor program. From here, the Molten Salt Reactor Experiment (MSRE) was developed, with design beginning in 1960 and construction starting in 1962. The MSRE went critical in June of 1965 and demonstrated the full power of 7.4 MWt in May of 1966 (although it did not include the electricity-producing balance of the plant). The reactor operated with various combinations of 233U, 235U, or 239Pu fluoride fuel dissolved in a lithium-beryllium-zirconium fluoride molten salt solvent.
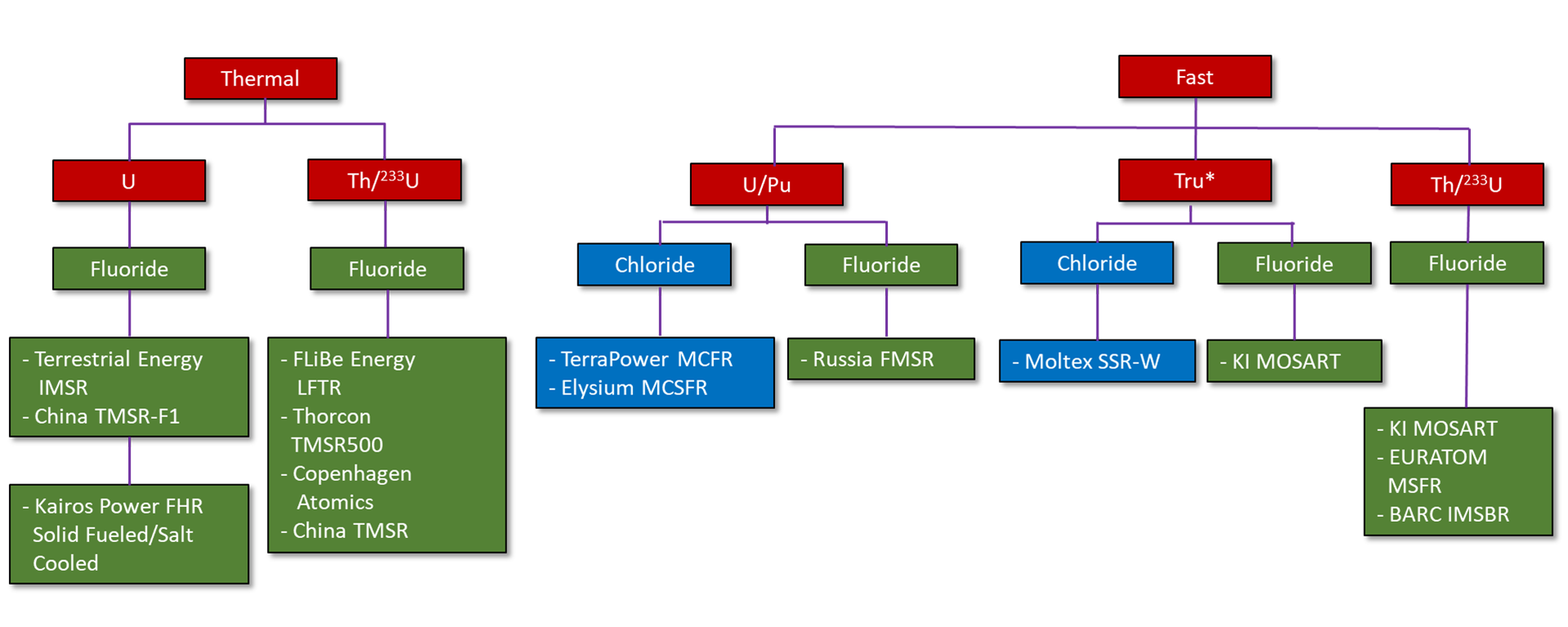
How does an MSR work?
The idea of an MSR is both clever and simple. A salt-cooled reactor replaces water as a heat transfer medium, flowing through an array containing solid nuclear fuel (although the solid fuel material and configuration will generally be very different from current water-cooled reactors). The nuclear-heated salt then transfers the energy downstream in the cooling loop to a heat exchanger to eventually make steam and drive a turbine to generate power. In the fuelled-salt concept, fissile material is dissolved in the salt, which then acts as both fuel and heat transfer medium. It either directly transfers its heat to a non-fuel salt loop or is similarly pumped around a flow loop, continuously entering, and leaving a volume (the core) where a self-sustaining nuclear chain reaction of the uranium or plutonium isotopes is possible. The generated fission heat is transferred to another fluid and produces steam for a turbine.
For thermal reactors, the neutrons that cause nuclear fission need to be slowed from energy at birth of approximately 2 MeV, to energies of a fraction of an electron volt in order to efficiently be absorbed and cause new fissions. This requires the presence of a moderator, such as graphite in or near the core of the reactor, which allows the rapidly moving neutrons to collide with, in this case, carbon atoms and effectively lose almost all of their energy.
MSRs designed as fast reactors do not require to slow the fission neutrons to encourage fission, and thus avoid the need for moderator material. However, the lesser likelihood of fast neutron absorption-caused fission requires higher fissile atom concentrations in the fuel, and thus more highly enriched fuel. Fast reactors also lend themselves to breeding fuel, where neutrons are allowed to be absorbed by the fertile isotopes 238U or 232Th and produce more fuel, 239Pu or 233U. They also generate significantly less long-term radioactive waste products and have been envisioned as potential means for consuming existing waste elements. Again, in the fuelled-salt coolant loop, it is still necessary for the salt to flow through a region where the geometry is such that it limits neutron loss out of the volume and thus encourages a self-sustained chain reaction.
For any reactor, whilst electricity production is of prime interest, there are also concepts where nuclear heat is directly used for industrial processes, including producing hydrogen for fuel or chemical applications.
The history of the industry’s Generation I, II, and III reactors begins in the 1950s, with the first power-producing reactor – the 60 MWe Shippingport Atomic Power Station outside Pittsburgh – followed by the first fully commercial plant – the 110 MWe Yankee Atomic Electric Plant – built near Rowe, Massachusetts. These reactors used ceramic uranium oxide fuel pellets stacked inside vertical metallic tubes spaced in an array that allows water, which is both the coolant and moderator, to flow up past them, absorbing the heat. From those first reactors, the common wisdom has been that the bigger the nuclear plant, the more efficient and therefore more inexpensive the electricity. This concept of ‘economy of scale’ proved to be true early on, with plants reaching the approximately 600 Mwe range, bringing in power at significantly reduced costs. However, as plants rose to 1,000 MWe or more, their outsized components now required specialised forging and assembly, and the need for onsite fabrication, increasing plant capital cost. That, together with the substantial growth in design requirements needed to satisfy safety regulations due to their increased size and the double hit of the extensive reconsideration of nuclear safety after the accident at the Three Mile Island plant in Pennsylvania, condemned the plants to enormous cost overruns and, in some cases, decades-long delays.
Small modular reactors
The past couple of decades have seen the development of the concept of the small modular reactor (SMR), whose size eliminates the need for some safety systems and opens the door to more efficient factory manufacture of the reactor, rather than on-site construction. An added bonus for electricity suppliers is the smaller capital outlay, reducing fiscal risk, and the ability to add capacity in smaller increments; for example, incorporating an individual ~300MWe unit as needed rather than 1200 MWe all at once where the demand for that much power has yet to develop. There are now at least 24 private and national ventures to develop SMRs, with the first prototypes of some expected before the end of the decade. Many of the concepts are MSRs, taking advantage of their compact nature, the simpler configuration in having no solid fuel, and lesser likely safety requirements and the attendant cost.
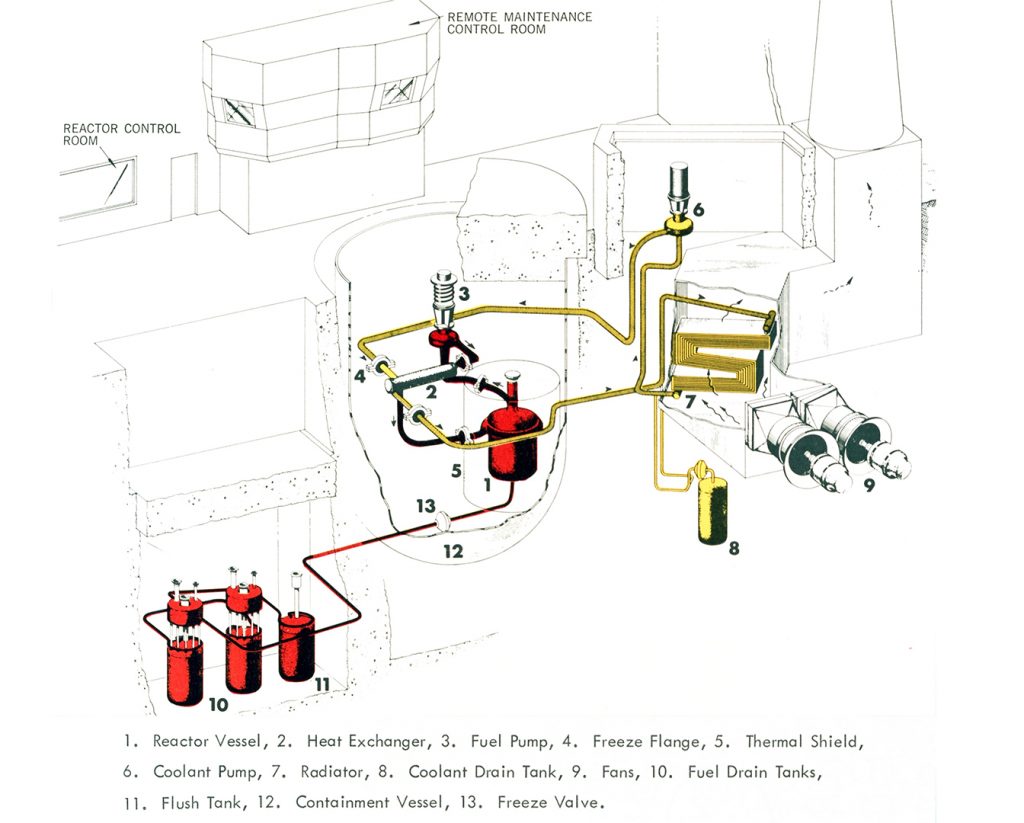
The constellation of MSR organisations and projects can be seen in Fig. 1. Thermal reactors can be fuelled with fluoride salt compositions, and can also breed fuel by allowing thorium salts to absorb neutrons and convert to fissile 233U. Fast neutron MSRs can use chloride or fluoride salts and breed fuel by allowing 238U to absorb neutrons and transmute to fissile 239Pu. Moltex has designs that are focused on neutralising transuranic waste elements produced in reactors which are very long-lived, creating difficulties for ultimate disposal. These isotopes are allowed to absorb neutrons in the reactor, undergoing transmutations that eventually progress to stable (non-radioactive) elements. Elysium Industries intends to utilise used nuclear fuel from conventional plants as their source of fuel. Finally, there are systems that use solid fuel and depend on fluoride salts solely as the heat transfer medium, taking advantage of their benefits over water. Kairos Power intends to use coated fuel particles embedded in graphite spheres as the core, with the salt flowing around the spheres to remove the heat. The particle fuel concept from the 1960s was originally used in prototype gas-cooled reactors, yet now lends itself well to salt-cooled systems.
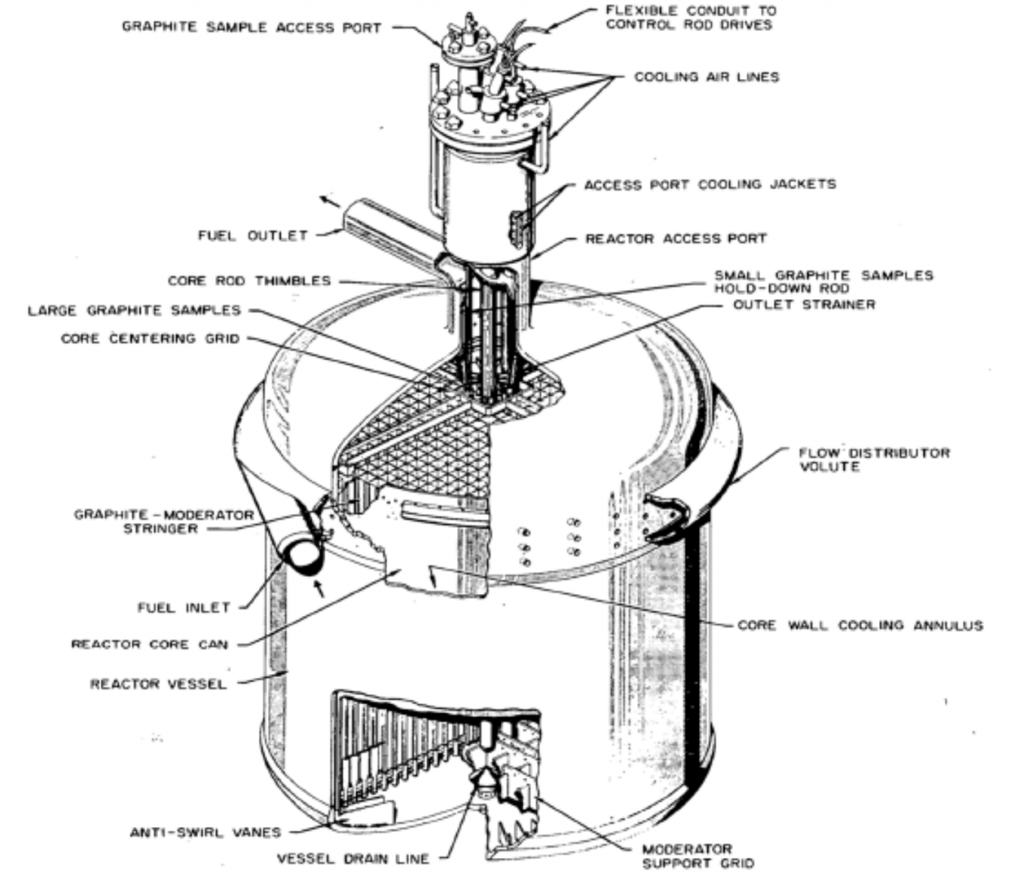
MSR developers recognised the significant advantages of salts as fuel and coolant and are working to match today’s need for reactors of more modest size, simplified safety requirements, and higher efficiency with their advantages of:
- High solubility for uranium, plutonium, and thorium;
- Chemical stability when subject to radiation at high temperatures;
- Being inert (no chemical reactions with air or water);
- Excellent heat transfer and heat capacity;
- Very high boiling points;
- Compatibility with nickel-based structural alloys and graphite; and
- Suitability for using already developed salt-based approaches for processing used fuel.
Fig. 4: Thermal MSR concept with graphite moderator in the core through which the salt flows (Idaho National Laboratory)
One of the greatest benefits of MSRs is that they can operate at near atmospheric pressure, eliminating the greatest safety challenges of water-cooled reactors which must operate at approximately 550°F and thus be kept at 1,000 to 2,200 psi to prevent the water from boiling. This requires the reactor core to sit in a huge, several-inches-thick steel pressure vessel. Any loss of pressure due to a failed valve or loss of active cooling, as occurred during the accident at Three Mile Island and at Fukushima, can allow the fuel rods to not be sufficiently cooled and result in catastrophic melting and possible breach of the protective barriers to radioactive release.
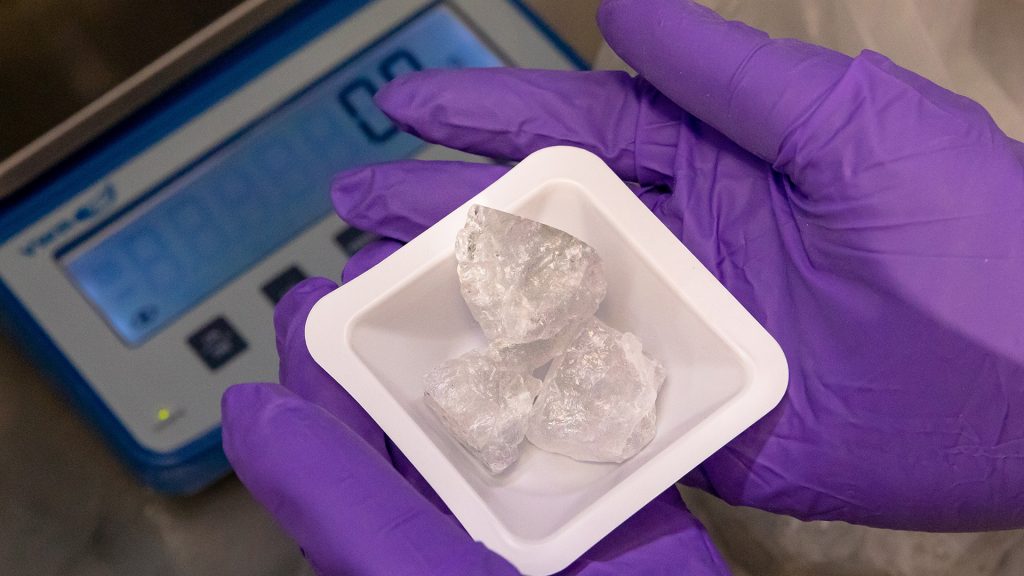
In an MSR, the reactor vessel does not need to be enormously thick as the pressure is low and, for the salt-fuelled systems, the fuel is already a liquid. In an accident, salt can spill from the reactor loop into the surrounding containment structure which would provide cooling, and thus there it would stop. The much less severe reactor accidents possible with MSRs should allow them to operate with substantially less in the way of extra equipment to prevent or mitigate an accident, and thus offer significantly improved economics over the large, water-cooled plants.
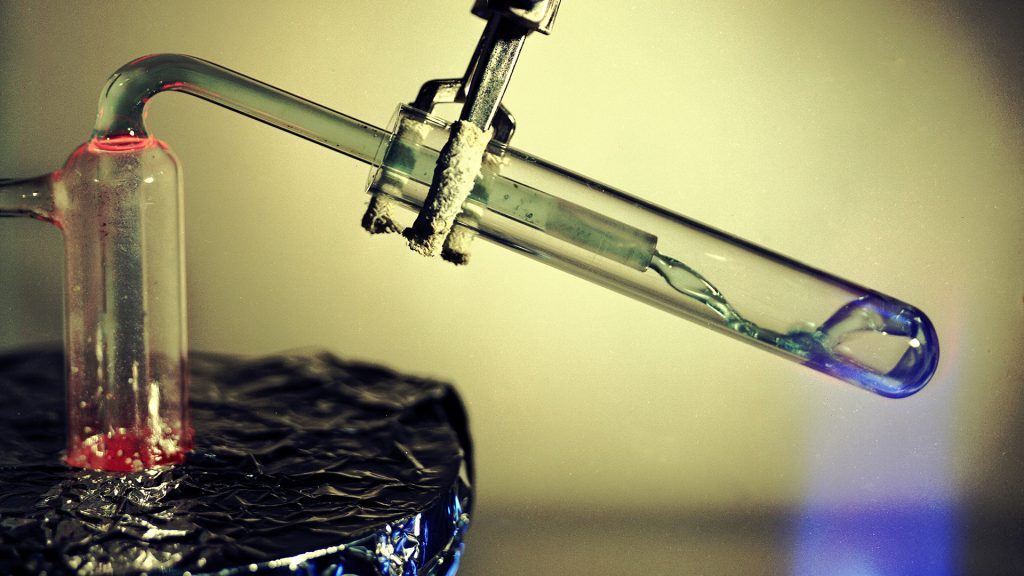
The future of nuclear construction
Small modular reactors, and particularly MSRs, are the next wave in nuclear construction in countries, such as the US, with a mature nuclear industry and modest rates of growth in electrical demand. These new systems, however, face a number of hurdles before they can be commercially deployed, with the first amongst them being licensed for construction and operation. The US Nuclear Regulatory Commission has just now issued the first design approval for an SMR, a water-cooled reactor proposed by NuScale. The licensing process for other SMRs, including MSRs, is well advanced. Yet, there is still a distance to go as the NRC is in the process of modifying its computational tools for accident analysis and considering how to define MSR ‘design basis accidents.’
Another major issue is whether these ventures can successfully construct and operate the units at the projected costs. In addition, the back end of the nuclear fuel cycle needs to continue consideration of either direct conversion of used salt into a nuclear waste form, or processing of the material to recover fissile material and segregate the waste elements.
If nuclear energy is going to be a growing contributor in controlling climate change, we will need a set of power sources that are relatively near-term, economically attractive, essentially inherently safe, and flexible in their use. Molten salt reactors have the potential to meet these requirements, filling a significant niche in the spectrum of technologies we will need to eliminate carbon emissions and move to a sustainable energy future.
Resources
- Status of Molten Salt Reactor Technology, IAEA Report https://inis.iaea.org/search/search.aspx?orig_q=RN:52090830
- GF 2020 Annual Report https://www.gen-4.org/gif/jcms/c_178290/gif-2020-annual-report