Discover the new, more sustainable electric car battery recycling technique that has been developed by a team from the University of Toronto.
With electric car sales surging worldwide, the demand for metals essential to battery technology is also substantially increasing. Professor Gisele Azimi, of the University of Toronto Engineering’s Laboratory for Strategic Materials, has developed a novel technique that could help secure a supply of critical metals by altering the current method of electric car battery recycling.
This new process, proposed by Azimi and her team, is a more sustainable method to mine for critical minerals, such as lithium, cobalt, nickel, and manganese. The team will recycle these metals from lithium-ion batteries that have reached the end of their useful lifespan.
How does the new technique differ from conventional battery recycling methods?
PhD candidate Jiakai (Kevin) Zhang, the lead author on a new paper recently published in Resources, Conservation and Recycling, explained that conventional processes for electric car battery recycling are extremely energy intensive. One of the processes is based on pyrometallurgy, which uses high temperatures and produces greenhouse gas emissions. The other process is based on hydrometallurgy which uses acids and reducing agents for extraction, producing wastewater that needs to be processed and handled.
The new electric car battery recycling technique instead uses supercritical fluid extraction for metal recovery. This technique separates components from each other by using an extracting solvent at a temperature and pressure above its critical point. This is the point where the solvent adopts the properties of both a liquid and a gas.
Zhang then used carbon dioxide as a solvent to recover the metals, which were brought to the supercritical phase by increasing the temperature above 31°C and the pressure up to seven megapascals.
Advantages of the new electric car battery recycling technique
The new process matched the extraction efficiency of lithium, nickel, cobalt, and manganese to 90% when compared to the conventional processes. Azimi and her team also showed that their electric car battery recycling technique used fewer chemicals and generated significantly less secondary waste. In the new method, the main source of energy released came from the compression of the carbon dioxide.
Azimi stated: “The advantage of our method is that we are using carbon dioxide from the air as the solvent instead of highly hazardous acids or bases.
“Carbon dioxide is abundant, cheap, and inert, and it’s also easy to handle, vent, and recycle.”
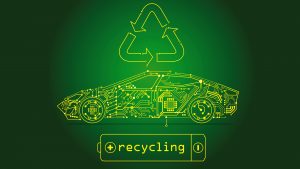
Supercritical fluid extraction is not a new process, since the 1970s it has been used to extract caffeine from coffee beans. The team has used previous research on this process to recover rare earth elements from nickel-metal-hydride batteries.
However, this is the first time that this process has been used to recover metals from lithium-ion batteries.
“We really believe in the success and the benefits of this process,” stated Azimi.
The next steps
“We are now moving towards commercialisation of this method to increase its technology readiness level. Our next step is to finalise partnerships to build industrial-scale recycling facilities for secondary resources. If it’s enabled, it would be a big game changer.
“If we recycle existing batteries, we can sustain the constrained supply chain and help bring down the cost of electric car batteries, making the vehicles more affordable.”
Canada is committed to a mandatory target that requires 100% of new light-duty cars and passenger trucks sold in the country to be fully electric by 2035. This is part of Canada’s target to reach net-zero emissions by 2050.
For this target to be achieved, the country needs to increase its supply of critical metals, which are already high in cost.
“We are about to reach a point where many lithium-ion batteries are reaching their end of life,” said Azimi.
“These batteries are still very rich in elements of interest and can provide a crucial resource for recovery.”
By recycling electric car batteries, these critical materials can be supplied at a lower cost, and the need to mine raw ore, which comes with environmental and ethical concerns, is reduced.
The current life expectancy of electric car batteries is between ten and 20 years, but most car manufacturers only provide a guarantee for eight years or 160,000km. When electric car batteries reach end of life, metals can be recovered from them through recycling. Currently, this does not happen, as many electric car batteries are discarded improperly, ending up in landfills.
“If we keep mining lithium, cobalt, and nickel for batteries and then just landfill them at end of life, there will be a negative environmental impact, especially if corrosive electrolyte leaching occurs and contaminates underground water systems,” said Zhang.
The team’s new electric car battery recycling technology, therefore, provides a more sustainable way to recover metals, subsequently assisting the electric vehicle revolution, and the global transition to clean energy.