With unique properties, nickel will be crucial to the clean energy transition. We take a look at how nickel mining can power a range of green technologies and how the industry is ensuring sustainability within the sector.
First identified in 1751 by Swedish chemist Axel Cronstedt, nickel is the fifth most common element on Earth, with a concentration of 80 parts per million in the Earth’s crust. It is a hard, ductile, and malleable metal that is a good conductor of heat and electricity. Products containing nickel have more strength at high and low temperatures and have greater toughness and corrosion resistance compared with other materials. This makes nickel vital for various applications.
Approximately 69% of nickel produced is used to manufacture stainless and heat-resistant steels, due to its strength and resistance to corrosion and high temperatures.1 Roughly 15% of nickel is used in other steel and non-ferrous alloys, which are often used in specialised industrial, aerospace, and military applications. Around 3% of nickel is used in batteries for electronics, and in batteries for portable equipment and hybrid cars, and about 2% is used for catalysts, chemicals, and dyes.1 The material is also used in medical devices and cordless power tools.
Nickel is now playing an increasingly important role in the clean energy transition, with the material being used in lithium-ion battery (LIB) chemistry for powering electric vehicles (EVs), and in renewable energy storage.
Nickel’s role in the clean energy transition
The world is headed for a 3.2˚C temperature rise if drastic action is not taken to reduce emissions. If temperatures continue to rise at their current level, more instances of extreme weather will occur which will have devastating impact on the planet. The world must halve emissions over the next decade and reach net zero carbon emissions by 2050 in order to limit global temperature rises to 1.5˚C.
Clean energy technologies will be the primary solution to the climate crisis. In 2020, energy demand from oil, gas, and coal fell by 5% relative to the previous year because of the COVID-19 pandemic.2 Alongside this, the energy demand from new energy systems, such as renewables, remained constant.
Nickel is required to facilitate the successful deployment of new energy technologies. With unique properties which make it vital to numerous applications, nickel is used in many clean energy technologies, such as batteries for electric vehicles (EVs) and energy storage. Some emissions-reducing technologies may only require small amounts of nickel, but that small quantity still plays a critical role.
Batteries for EVs
Nickel is present in many battery technologies and, currently, high nickel-based LIBs are the technology of choice for EVs as they offer the highest energy density on the market. Energy density is a priority for original equipment manufacturers (OEMs) because it defines the range per charge that a vehicle can drive. The cost of the battery is also crucial because the EV must be affordable to the general consumer. As well as providing higher energy density, LIB cathodes which contain nickel make batteries smaller and lighter. Using nickel therefore results in a more efficient EV, enabling a longer driving range.
Over the past decade, a mix of nickel, cobalt and manganese or aluminium oxides (NMC/NCA) has been the best technology, and will be the batteries of choice for EVs for the foreseeable future. It has been reported that the LIB sector will continue to move towards high nickel NMC, which has more than an 80% nickel cathode.3 The current estimates of LIBs with high nickel NMCs are 8%, and that figure is expected to rise to nearly 50% by 2030.3
Batteries for storage
Modern battery technology allows for electricity generated by wind turbines or solar panels to be stored and used only when required. As sun and wind power cannot be sourced on demand, batteries must be deployed to capture energy and release it when it is needed. The dominant technology is lithium-ion (Li-ion), as a result of the long history of Li-ion in the consumer electronics market and the recent investments into the Li-ion industry. Global suppliers of LIB cathode material are increasing production capacity of nickel-manganese-cobalt (NMC), with a typical ratio of 33% for each element.4
Mining and processing
Currently, the world’s nickel resources are estimated at almost 300 million tonnes, with Australia, Indonesia, South Africa, Russia, and Canada accounting for more than 50% of global nickel resources.5 Known nickel reserves and resources have steadily grown, due to an increase in knowledge of new deposits in remote areas, and improved nickel mining, smelting, and refining technologies enabling lower-grade nickel ore to be processed. It is also suspected that there are considerable nickel deposits in the deep sea, as significant amounts of nickel are found in manganese nodules, located on the deep-sea floor. With developments of deep-sea nickel mining technologies, access to these resources will be facilitated in the future.
Nickel-containing ore is mined in more than 25 countries globally, and is found in sulphide and laterite-type ore deposits. In 2020, Indonesia was the highest nickel producer, with Indonesian mines producing approximately 760,000 mt of nickel.6 The Sorowako Mine, located in South Sulawesi, Indonesia, was the largest nickel mine of 2020, producing around 71,000 tonnes of nickel.7 Global nickel production has been forecast to grow at a compound annual growth rate (CAGR) of 3%, reaching 2,730.6 kt in 2025.8
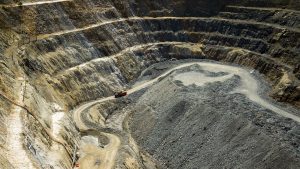
Nickel mined from lateritic ore is mined from various depths beneath the surface, and sulphidic ore is mined underground. To extract nickel from the lateritic ore, conventional roasting methods are used, removing moisture. The nickel oxide is then separated by a reduction furnace, which in turn reduces the chemical-filled water. This metallurgical process results in a 75% pure form of nickel.9
The extraction process of nickel from a sulphidic ore requires a different method, which currently includes both flash and electric smelting. The ore is placed in a furnace which contains pre-heated oxygen, causing the iron and sulphide to oxidise resulting in 45% nickel.9 At the final stage, oxygen is injected into the molten bath, eliminating remaining traces of iron and sulphide.
Through further refining, using the fluid bed roasting technique, a 95% form of nickel can be obtained.9
Reducing carbon footprint in the nickel sector
Although clean energy technologies rely on metals and minerals that are unavoidably energy intensive to produce, the IEA has stated that the climate advantages of these technologies remain clear. However, more still needs to be done to reduce the carbon footprint of nickel production.
So far, Nickel Institute member companies have reduced their GHG emissions from nickel production by approximately 9%. This is set to rise even higher as Nickel Institute member companies have committed to reducing their carbon emissions through implementing a range of solutions, ensuring that their processes are made less carbon intensive.
Recycling and recovery
Recycling nickel will help reduce carbon emissions, as nickel-containing products, such as stainless steel, are designed for long-term use. Nickel and nickel-containing alloys can be returned to their original state or can be converted to an equally valuable form. For example, nickel-containing stainless steel scrap from recycled batteries can be turned into new stainless steel and nickel. Amongst all metal recycling, nickel recycling has one of the highest efficiencies, as approximately 68% of all nickel available from consumer products is recycled and begins a new lifecycle and 15% enters the carbon steel loop. 17% still ends up in landfill, however.10
Every year, a colossal amount of electronic waste (e-waste) is produced, with over 53 million tonnes produced in 2020 alone. Currently, only about 10 million tonnes of e-waste is truly recycled. There is nickel in e-waste, and in the circular economy, it is necessary that we recover as much as we can.11
Each nickel producer involved in recycling has its own processing route for e-waste. It starts with pre-processing, as e-waste contains a number of plastics, ceramics and other non-metallic materials that have a separate path. Steel in appliances can be magnetically separated out and sent to steel mills for direct recycling. Circuits and whole mobile phones can also be shredded into small pieces to assist the separation process. Some companies will have a separate recycling line for the various types of batteries, the supply of which for recycling is expected to increase rapidly as EV batteries come to the end of their life. Pyrometallurgy (high temperature), hydrometallurgy (dissolution in acids), or sometimes both processes, are involved in the recovery of copper, nickel, and the precious metals.
As nickel has outstanding properties and has a high recycling efficiency, it can re-enter the economy following the end-of-life of nickel-containing products. Nickel and nickel-containing stainless steel demonstrate how primary materials can contribute to a circular economy.
References
- https://nickelinstitute.org/about-nickel-and-its-applications/properties-of-nickel/
- Clare Richardson, https://nickelinstitute.org/blog/2021/october/nickel-and-net-zero/
- https://nickelinstitute.org/media/8d926a8a54d694a/2021-review-ni_energizing-batteries-v3.pdf
- Dr Parvin Adeli, https://nickelinstitute.org/about-nickel-and-its-applications/#01-nickel-properties
- https://nickelinstitute.org/about-nickel-and-its-applications/#mining
- https://www.statista.com/statistics/264642/nickel-mine-production-by-country/
- https://www.mining-technology.com/marketdata/ten-largest-nickels-mines-2020/
- https://www.mining-technology.com/comment/nickel-output-2021-indonesia-philippines/#:~:text=Global%20nickel%20mine%20production%20is,19%20related%20lockdowns%20and%20restrictions
- https://www.agiboo.com/nickel/
- https://nickelinstitute.org/policy/nickel-life-cycle-management/nickel-recycling/
- Gary Coates, https://nickelinstitute.org/blog/2022/january/mining-electronics-waste/