A novel power generation system, being developed by the Colorado School of Mines, targets both radically lower cost (<1000 $/kW) and ultra-high efficiency (70%-LHV) using hybrid solid oxide fuel cells for commercial applications up to 1 MW.
High temperature, ceramic-based, solid oxide electrochemical technology continues to advance for both power and hydrogen production applications. There is a growing need for high-efficiency dispatchable power generation technologies supplied with carbon-neutral fuels to mitigate curtailment of renewables.
Pressurised, hybrid solid oxide fuel cell (SOFC) systems fuelled with hydrogen, biogas, or renewable natural gas can generate clean power at ultra-high efficiency. The Colorado School of Mines and its partners are developing a novel hybrid stationary power system comprised of an intermediate temperature (600°C), metal-supported solid oxide fuel cell integrated with a high-efficiency stationary engine and novel balance-of-plant (BOP) equipment. In collaboration with Colorado State University, and Kohler Power Systems, the technology development effort aims to drive both radically lower capital costs (<$1000/kW) and ultra-high electric efficiency (>70%-LHV) at distributed generation scales of 125 kW.
The market opportunity for distributed generation in domestic US markets is greater than 200 GW in capacity and estimated at roughly $300bn, with global markets exceeding 1 TW. Distributed generation markets in the US often chart a difficult path for various technologies due to volatility in both gas and electric grid pricing which strongly influences the overall economic value proposition. However, new market forces related to supporting electrification of the transportation sector, renewable energy (RE) firming of regional grids, and reduced net carbon emissions are incentivising the need for flexible, high efficiency power generation from zero-and low-carbon fuels.
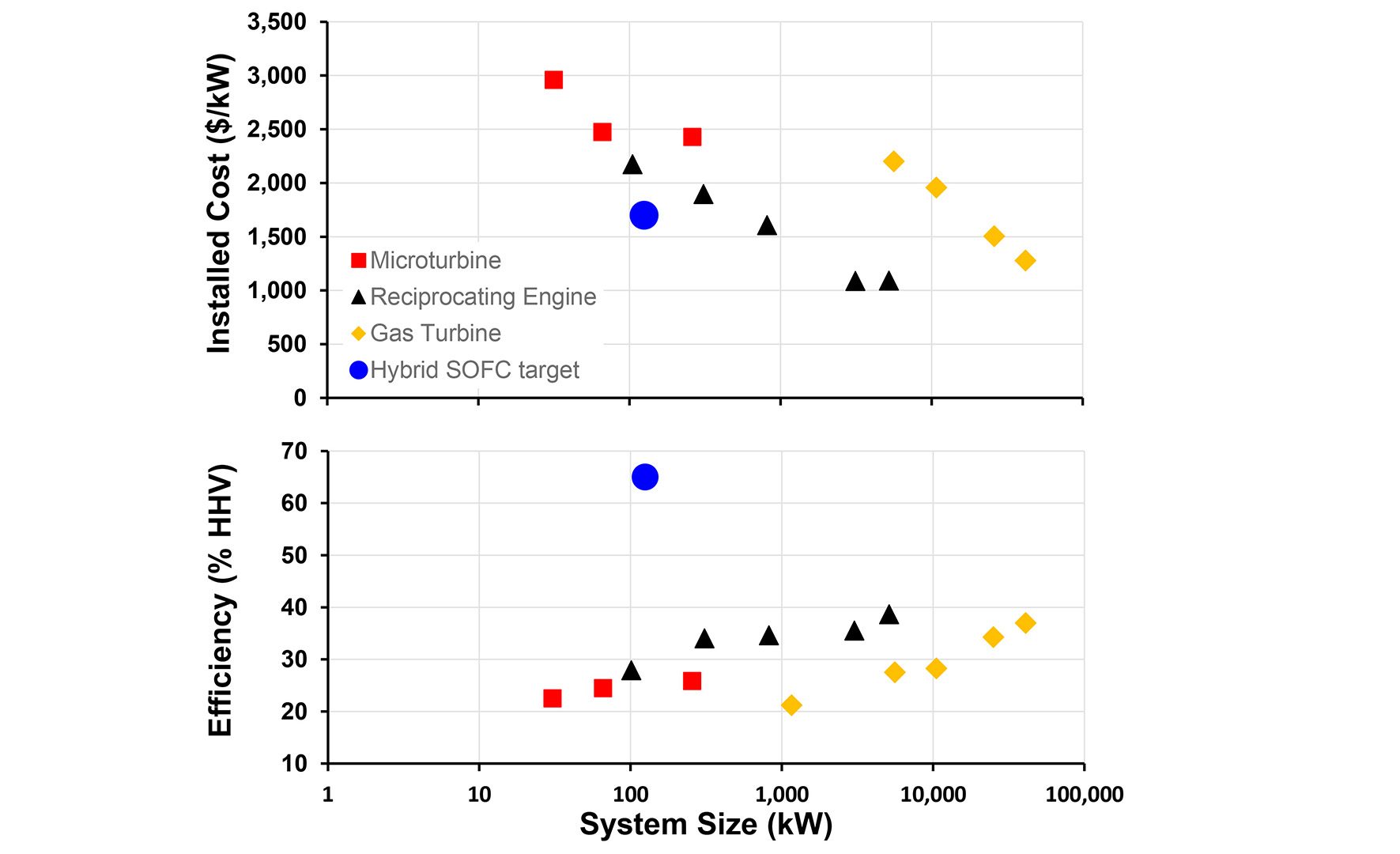
Fig. 1 illustrates some of the size, efficiency, and cost characteristics for existing technologies in distributed power applications. A gap in the availability of high efficiency, low-cost generator availability in the 1-10,000 kW capacity range at costs less than 2,000 $/kW and efficiencies greater than 50% is absent in current generator product portfolios. Furthermore, given the ramping requirements associated with electric-grid-demand characteristics for high penetration renewables (e.g. duck curve), robust, dynamic distributed generators would help fill the need for RE firming.
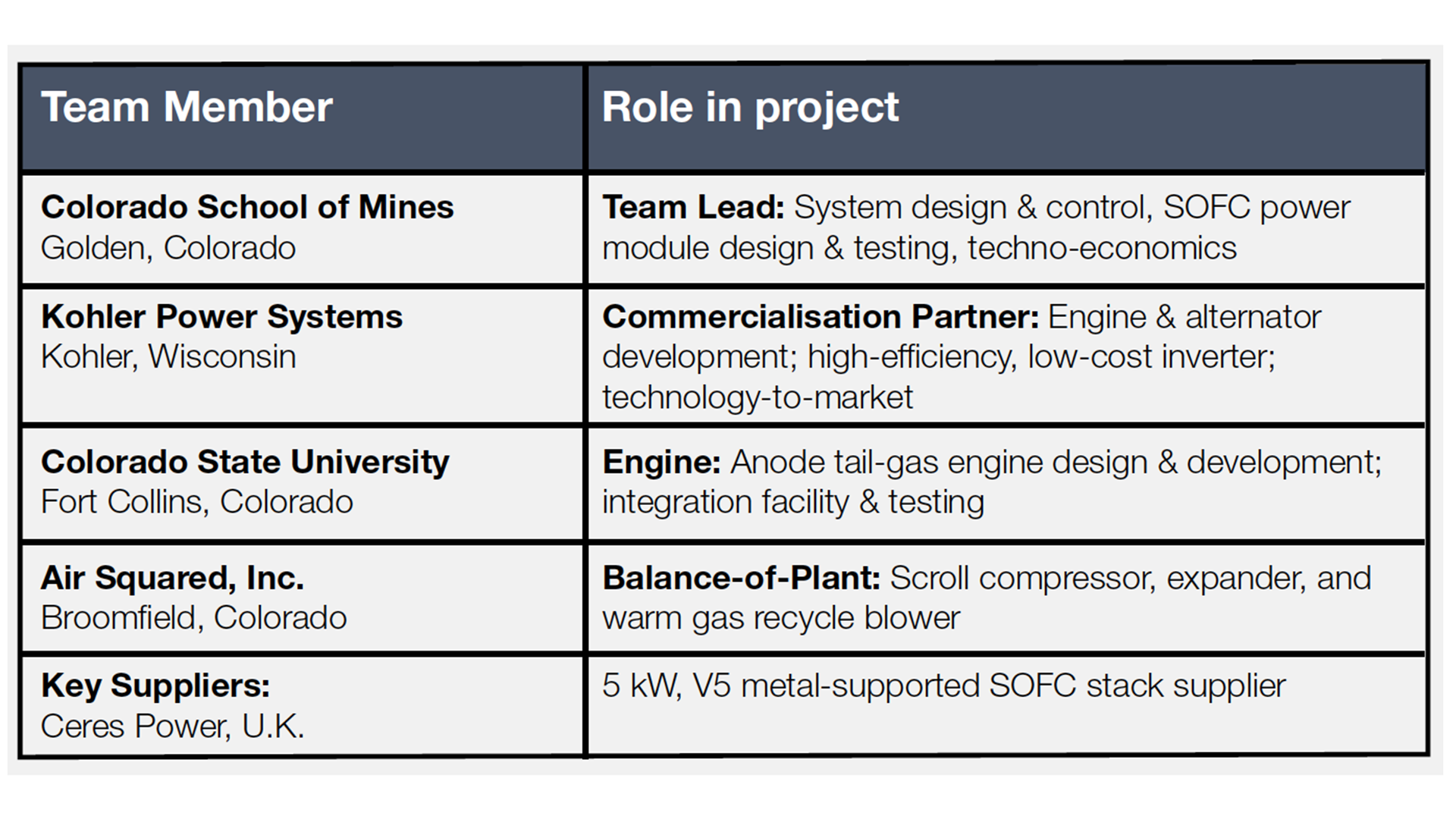
The project team (Table 1), led by the Colorado School of Mines (Mines), is in year three of a five-year development effort funded by the U.S. Department of Energy’s ARPA-E INTEGRATE programme.
How hybrid systems are integrated
A high-level schematic (Fig. 2) illustrates the integration approach of the novel hybrid system, which features robust, low-temperature SOFC technology and advanced internal combustion (IC) engine design. The custom-designed, turbo-charged IC engine will produce power from the unreacted fuel in the SOFC exhaust, and will be used to drive a novel compressor that supplies pressurised air to the fuel cell. An electric generator will also be driven by the IC engine to utilise excess mechanical shaft power. The system will export AC power to the electric grid using novel stack/power-conditioning integration and an innovative, low-cost DC-to-AC inverter technology.
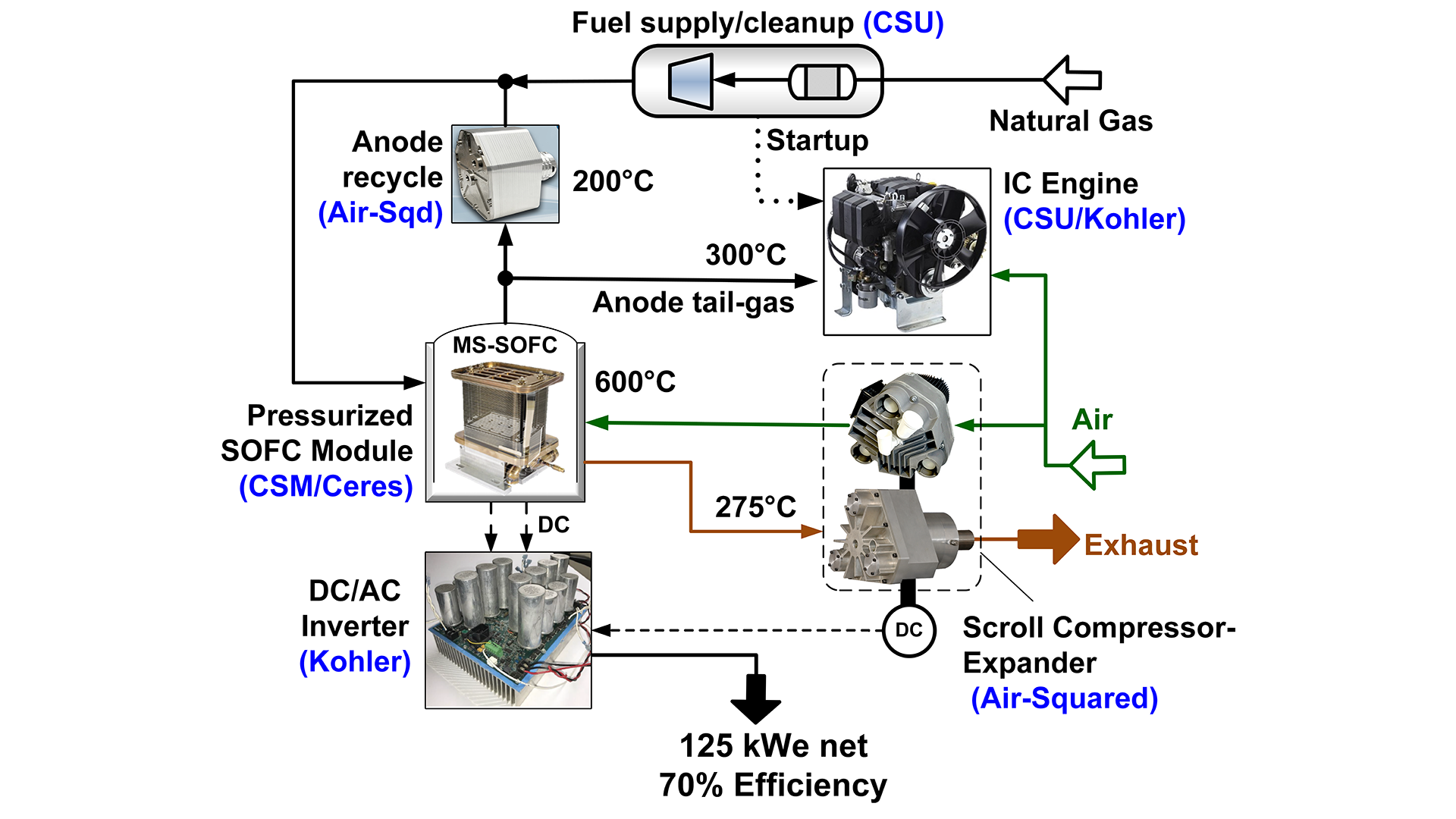
The heart of the system under development features Ceres SteelCellTM metal-supported SOFC technology from Ceres.3 The lower cell operating cell temperature and high degree of internal reforming enable excellent thermal management and effectively reduce air preheater duty by >60% over more conventional SOFC systems operating near 800°C. Pressurisation of the system facilitates an increase in stack power density and lowers plant footprint. Overall, the SOFC stack represents >85% of the total power output of the system. A modified, gasified-diesel engine converts the residual chemical energy in the anode tail-gas to shaft power, which drives auxiliaries and produces net additional power. In addition, because the engine is fuelled by a mixture of hydrogen and carbon monoxide, a simple engine after-treatment for achieving low engine emissions (NOx, CO) is possible.
The central component of the system is the packaged, multi-stack power block. The power block is comprised of three 30 kW multi-stack module (MSM) assemblies that are packaged together (Fig. 3 – right). Each 30 kW multi-stack module is built from four Ceres 5 kW SOFC stacks that are arranged together as an insulated, thermally and electrically integrated subassembly (Fig. 3 – centre) that is fully replaceable. As the fuel cell stacks are pressurised, they operate more efficiently and up to 7.5 kW can be extracted from a typically rated 5 kW stack. Thus, a total of 12 fuel cell stacks are employed in the ~100 kW power module to be hybridised with a bottoming spark-ignited, internal combustion engine.
Balance-of-plant hardware development is critical to overall system efficiency
A low-speed, shaft-coupled, positive displacement compressor and expander is under development by Air Squared Inc. First generation prototypes have been designed, fabricated, and tested as separate components. The compressor is derived from the P34 scroll compressor technology previously developed for proton exchange membrane fuel cell systems in onboard fuel-cell-powered bus applications. Liquid-cooled, second-generation units have been designed with displacements near 1600cc and target performance of 76% isentropic efficiency when operating at pressure ratios near 3.3 bar.
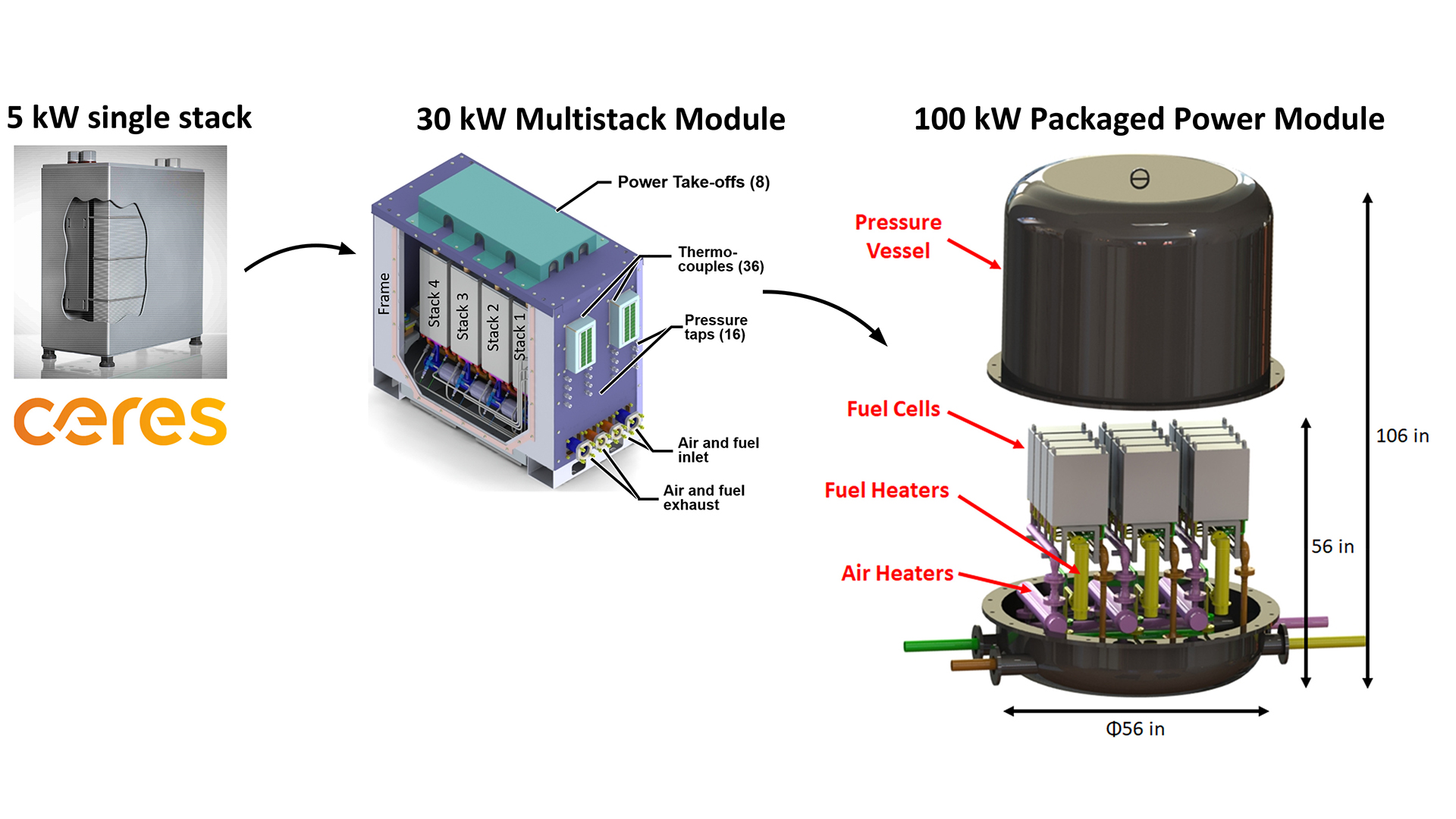
Kohler Power Systems (KPS) is developing a high efficiency, three-phase inverter system leveraging several unique aspects of the application. The inverter will provide power regulation (baseload operation) export limiting (peak shave) and islanded (voltage / frequency control) operational modes. The inverter logic will include multiple modes of operation to facilitate operation as standalone, parallel-to-the-grid, or as part of a microgrid. The inverter will be connected line-neutral and will produce 277/480VAC at 60Hz. This will provide equivalent or better performance to a line-line connected inverter while operating in parallel with the grid, providing superior voltage regulation and current imbalance capability to an islanded load.
Prototype development on a sub-15 kW unit has demonstrated proof-of-concept performance. The design features SiC wide-bandgap switches that enable higher speed switching with lower conduction and switching losses, a smaller output filter and transformer-less operation. The amorphous iron cores result in lower cores losses with high saturation levels that allow for compact design and reduced winding losses. Using test data and inverter models for full-scale prototype performance estimation, an efficiency exceeding 98% is possible across load ranges of 33% to 100% design capacity as shown in Fig. 4. Mass produced CapEx is estimated at < 90$/kW.

Engine design specifications that will allow the engine to achieve ≥35% efficiency based on the incoming fuel LHV (anode exhaust) have been a significant aspect of tail-gas engine development. The design specifications were established from a combination of experimental data and engine modelling efforts. Test data from 1-2L engine experiments were used to validate both in-cylinder combustion and GT Power models, and then the models were exercised to explore a range of design engine parameters to determine the optimal design specifications. Specifically, key parameter sweeps related to percent mass fraction burned, engine speed, and equivalence ratio. The final test varied the equivalence ratio from 0.7 to 1.1 while maintaining the power at 12.5 kW and utilising the optimal speed and crank angle location identified from previous model runs. The efficiency increased dramatically while sweeping the equivalence ratio from stoichiometric to fuel lean, increasing from 28% up to 33.9% at an equivalence ratio of 0.75.
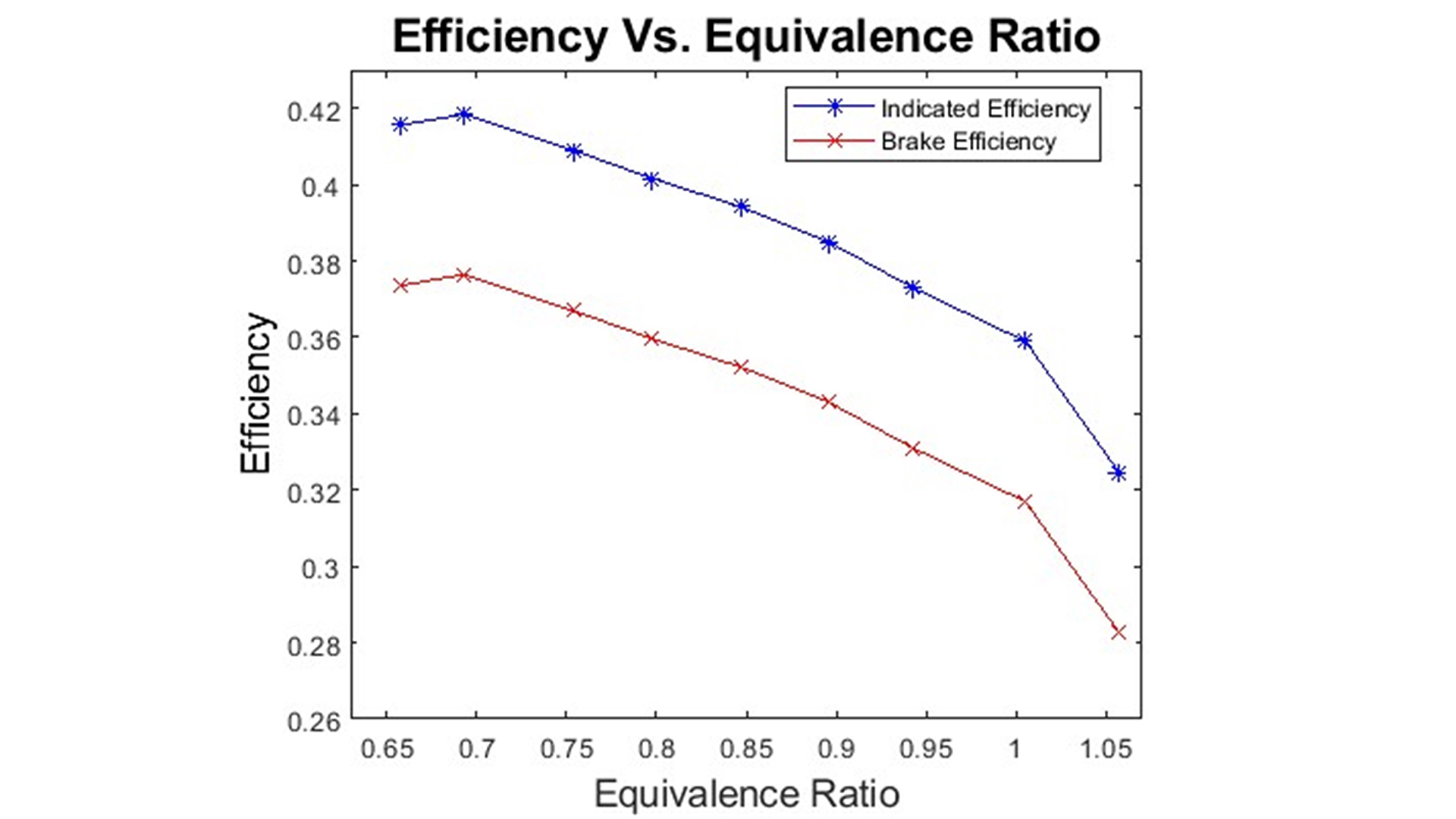
It should be noted that the observed 33.9% efficiency represents the engine brake efficiency accounting for supercharger pumping power requirements. If pressurised engine air is instead supplied by the main system scroll air compressor, the engine brake efficiency exceeds 38%. With establishment of the final engine configuration, the prototype unit has been built and is undergoing testing at CSU.
Unique test facilities are being applied to develop the technology
Mines has established unique test capabilities that are being used for pressurised testing of electrochemical stacks in the sub-kW to 50 kW range for both power production and hydrogen generation. Fig. 7 illustrates the hardware in one of the laboratories at the Colorado School of Mines in Golden, Colorado, where the 30-kW MSM sits within a four-foot diameter pressure vessel (10 bar rated) and surrounding balance-of-plant equipment is being assembled. Another operating Mines test facility has a three-foot diameter pressure vessel for testing of electrochemical stacks in the 100 W to 10 kW range.
In addition to small and large stack testing, the full-scale 100 kW hybrid SOFC-Engine power generation system will be tested in a new facility at Colorado State University. Subsystem testing will begin in autumn 2022, with full system testing starting next year.
While the demonstration test facility has a large footprint for technology evaluation in a laboratory setting, the expected footprint for commercial versions of the hybrid system are much smaller, as shown in the concept of Fig. 7.
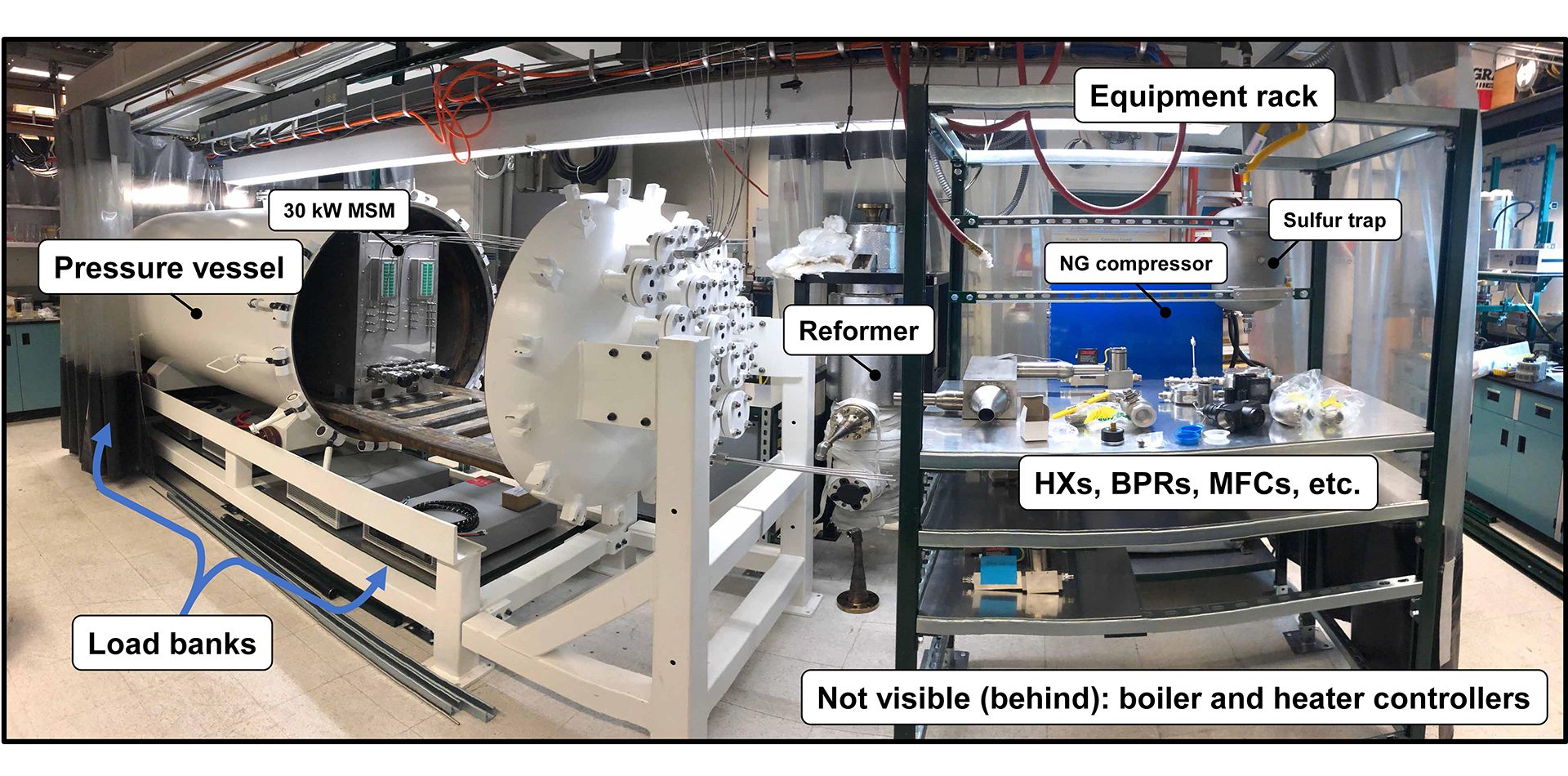
Techno-economic potential of hybrid SOFC systems
The hybrid system design is targeting capacity ranges from 125 kW to 1 MW using 125 kW building blocks. The estimated installed system price in mass manufactured quantities is between 1,800 to 2,000 $/kW, with O&M costs ranging from 0.025 to 0.035 $/kWh depending on stack replacement and BOP servicing requirements. An average efficiency over plant life of 65% is expected with potential for an additional 15-25% thermal efficiency in hot water recovery configurations. Table 2 summarises the comparison versus other DG technologies.
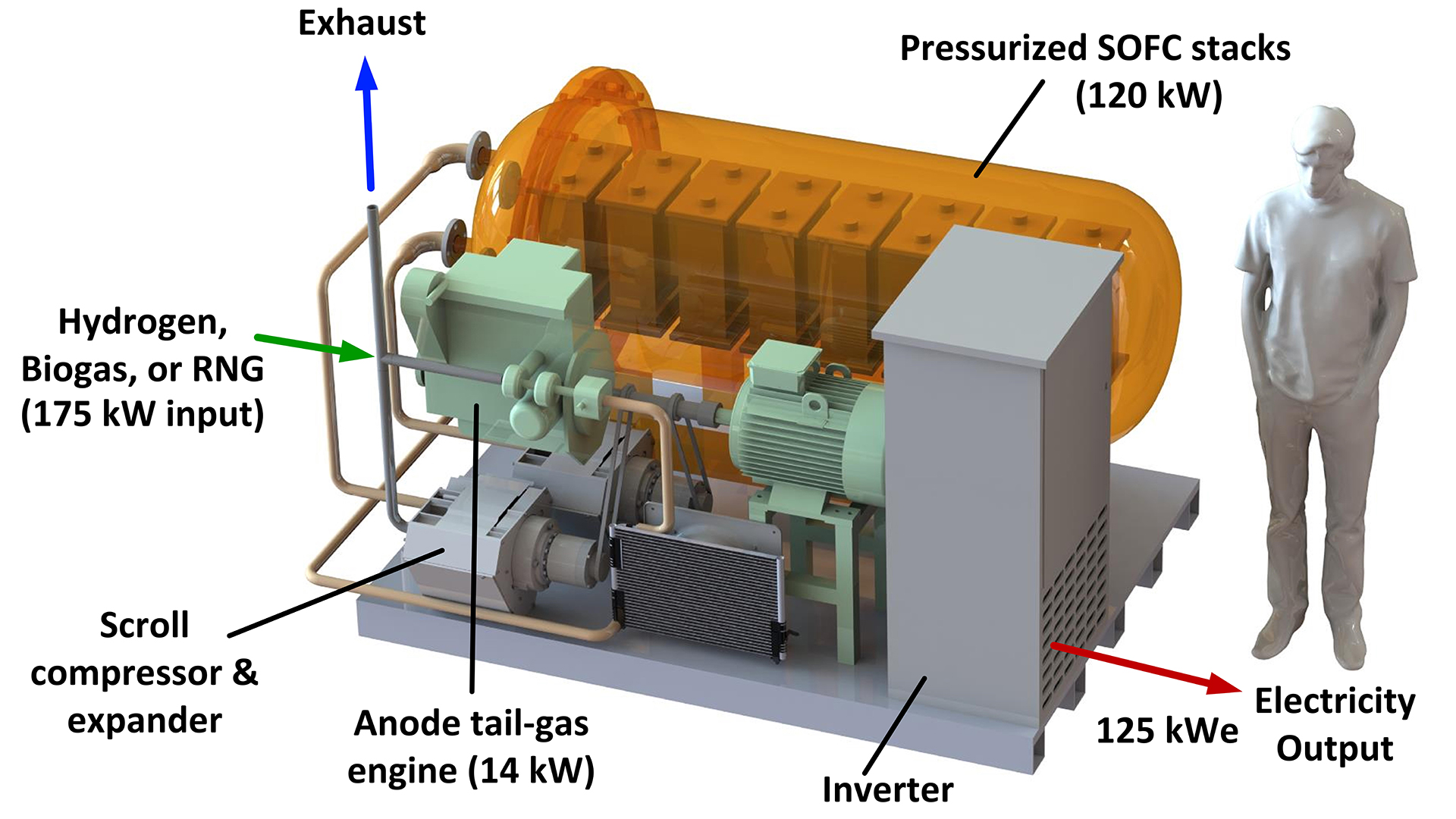
A competitive assessment of hybrid solid oxide fuel cell-internal combustion engine (ICE) systems configured for combined heat and power (CHP) in commercial building distributed generation (DG) applications has been performed. The hybrid SOFC-ICE systems were evaluated against microturbines, internal combustion engines, and generic SOFC systems using the REopt Lite webtool developed by the National Renewable Energy Laboratory.7 The tool recommends optimal (i.e. minimum life cycle costs) technology sizing and dispatch of hybrid renewable energy systems (RES) and CHP systems for commercial building retrofit applications. A study to quantify the economic potential of these novel hybrid SOFC systems relative to other conventional CHP system types was made. DG applications including large hotels, supermarkets, and data centres were evaluated and compared. While the comparative results of the analyses are strongly dependent on the CapEx and OpEx assumptions, the fuel cell systems modelled with the given costs and performance traits of Table 2 always resulted in higher relative savings than conventional generation and RES-only systems for the given scenario. These analyses reveal SOFC systems as the most cost-effective solution of all the CHP options in buildings with lower thermal-to-electric ratios.
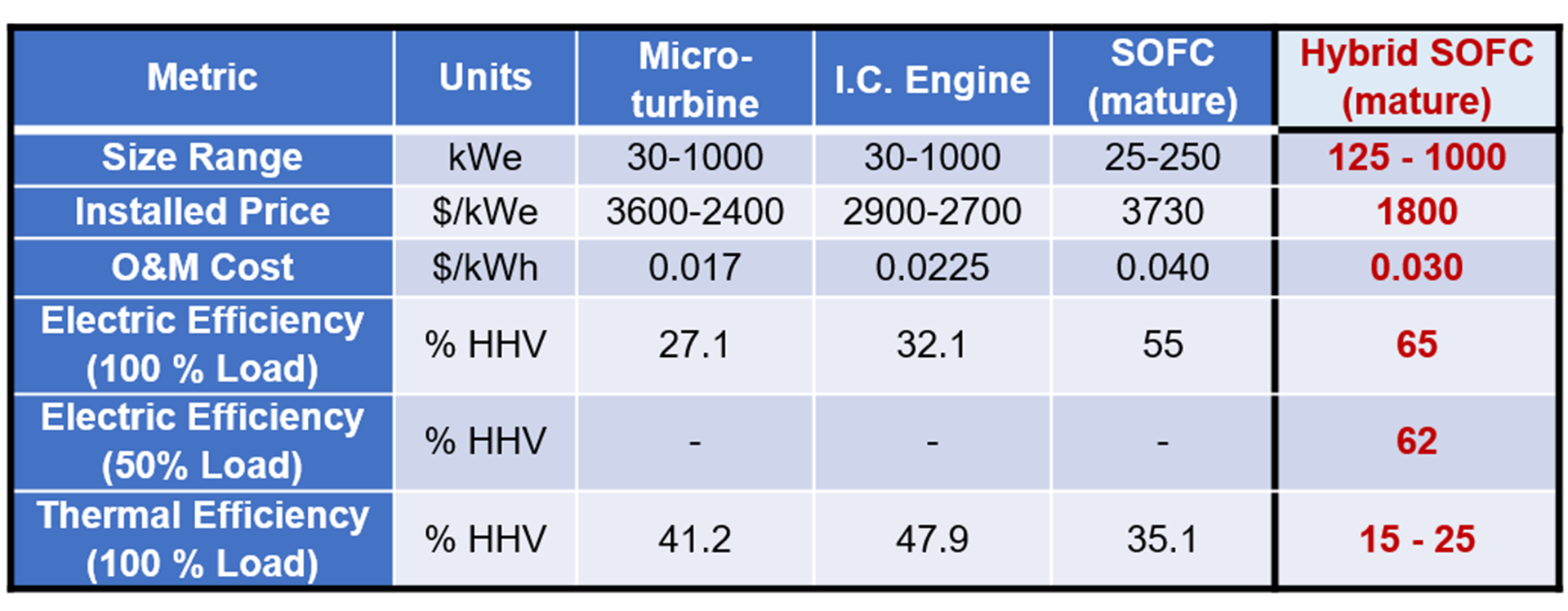
The estimated lifecycle savings are upwards of 30-40% for several sites and our findings are that the hybrid SOFC systems serve as the most cost-effective option for instances when a suitable site with low thermal-to-electric ratio pursues a DG installation. Further hybridising SOFC systems with renewable energy systems (photovoltaics with batteries) lowers the overall lifecycle savings of the combined system, but improves the economics of renewable energy systems deployed without SOFC systems. As our commercialisation partner, Kohler will look to move this system into production after the technology is de-risked via successful field trials.
Acknowledgements
The authors thank the U.S. Department of Energy ARPA-E INTEGRATE programme office for funding under award number DE-AR0000954.
References
- U.S. DOE ARPA-E REBELS Funding Opportunity Announcement, Nov (2013)
- R J Braun, E Reznicek, C Cadigan, N P Sullivan, R Danforth, T Bandhauer, S Garland, D Olsen, B Windom, B Schaffer, Development Of A Novel High Efficiency, Low Cost Hybrid SOFC/Internal Combustion Engine Power Generator, SOFC-XVI, Japan, ECS Transactions, (2019)
- S Mukerjee, Development Progress of Ceres Power’s Steel Cell technology, Electrochemical Society, presentation, SOFC-XV, Glasgow, Scotland, (2015)
- Battelle Memorial Institute, Manufacturing cost analysis of 100 kW and 250 kW fuel cell systems for primary power and combined heat and power applications, prepared for the U.S. Department of Energy under contract #DE-EE0005250 (2016)
- B D James and D A DeSantis, “Manufacturing Cost and Installed Price Analysis of Stationary Fuel Cell Systems,” (2015)
- “Catalog of CHP Technologies,” Environmental Protection Agency (2017)
- K Anderson, D Olis, B Becker, L Parkhill, N Laws, X Li, S Mishra, REopt Lite User Manual, Tech. rep., National Renewable Energy Laboratory (2021)
Please note, this article will also appear in the twelfth edition of our quarterly publication.