Heat pipe heat exchangers (HPHE) designed by partners at ETEKINA are shaping the waste heat recovery systems of the future.
In early February 2022, the cost of carbon reached record highs, with figures for a ton of carbon dioxide emissions reaching €95. Following this, the pollution penalty decided by the European Union’s Emissions Trading Systems has decreased. However, carbon costs remain tens of Euros higher than previous trading prices at a time when natural gas prices are also extremely high. As a result, the ETEKINA project has been set up to design three heat pipe heat exchanger (HPHE) units to generate a novel waste heat recovery system.
The effect for waste heat recovery projects, such as ETEKINA, is profound. As Mark Boocock, Managing director of Econotherm UK, highlights: “Rising gas prices and higher carbon costs are significantly driving the demand for waste heat recovery, worldwide.
“Energy projects that were struggling to get signed off in the past are now flying through and we are also seeing a greater focus on environmental governance in many businesses. We have seen many global companies implement waste heat recovery in existing facilities whilst also mandating it in new facilities – this is a great time for projects such as ETEKINA.”
Three heat pipe waste heat recovery systems
Boocock has been involved with ETEKINA from its conceptualisation, working closely with the project’s Scientific Coordinator, Professor Hussam Jouhara, from Brunel University London. Jouhara led the design of the project’s three heat pipe waste heat recovery systems, with Boocock and Econotherm colleagues manufacturing and installing the systems at Fagor Ederlan’s aluminium alloy production line in Spain, the SIJ Metal Ravne steel works in Slovenia, and ceramic production plant, Atlas Concorde, in Italy.
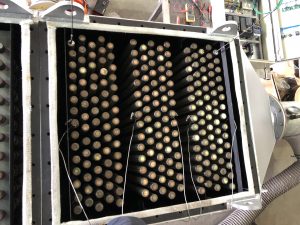
ETEKINA’s initial target was to recover 40% of the waste heat in the exhaust streams at each company facility – four years on, all sites have exceeded in this goal. “With all three heat pipe systems, we have installed more than one megawatt of power,” highlighted Jouhara. “Following our success, we are now fully handing over to Econotherm, which will be able to replicate these systems all over the world.”
Constructing lab-scale HPHE units
A critical part of the ETEKINA project was to initially develop three lab-scale, heat pipe heat exchanger (HPHE) units at Brunel, to validate HPHE models and to also serve as test-beds for the full-scale units that would be installed at the three sites in Spain, Slovenia, and Italy.
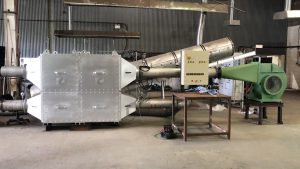
Jouhara and his colleagues devised general thermal models for the heat exchangers, while also carrying out additional modelling to optimise the units’ complex designs. These models were tested on the lab-scale units.
For example, computational fluid dynamics was applied to model exhaust gas flow at the Atlas Concorde ceramic production plant in Italy. This ensured that any heavy particles remained suspended in the gas as it flowed through the system.
“If gas flow was to stagnate inside the heat exchanger, these heavy particles could be deposited, accumulate and eventually block the system,” explained Jouhara. “So, we developed some innovative designs [to avoid particle deposition] and tested these in the lab-scale system.”
During their early modelling and test period, the engineers also realised that even if these particles remained suspended during gas flow, they would still attach to the pipe walls when exhaust temperatures dropped below a certain level. As a result, they added easy access inspection doors to the final system so particles could be removed during regular maintenance.
“We were able to validate this design [with the doors] in-situ at Atlas Concorde, which was amazing,” commented Jouhara. “The lab-scale units ensured any early hiccups were picked up.”
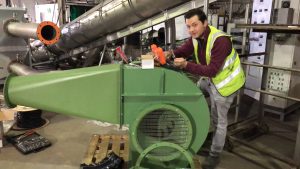
The lab-scale units are highly scalable and will be instrumental in the future development of more heat recovery installations around the world. What is more, they can be utilised to help ensure the final system will not impact on a facility’s existing manufacturing processes.
“Implementing a conventional, or non-heat pipe, waste heat recovery system can bring many benefits, but there is always the risk that it may interfere with manufacturing – any gains will be quickly lost if a heat exchanger failure interrupts production,” said Boocock. “But if you look at our three installations – these are invisible to production processes but have had a huge impact on energy consumption and efficiency.”
More ways in which to recycle waste heat
Looking to the future, the lab-scale units will be critical to the future HPHE system design. Jouhara and Boocock are currently implementing this knowledge, and the many lessons learned during ETEKINA projects, to other HPHE projects.
Whilst at the Atlas Concorde ceramic production plant, the engineers noted large quantities of water condensation being created, which they realised could be recovered to further reduce energy consumption and increase energy efficiency levels.
The EU-funded project – iWAYS – has since launched to develop heat-pipe based technologies for industrial processes, to recover water and heat from exhaust streams.
“I see ETEKINA as being the parent-project of iWAYS, and we are now pushing our technologies further to recover the latent heat and recycle the water from the exhaust streams at Atlas Concorde and other facilities,” concluded Jouhara. “So you see, our success story does not stop with the products we developed at ETEKINA – we are now pushing these to the next level and will bring drastic change to the waste heat recovery systems of the future.”