Dr Myriam Bourgeois, NUCOBAM Coordinator at Université Paris-Saclay CEA, explains how the European project aims for future AM Standard in the nuclear energy industry.
The main aim of NUclear COmponent Based on Additive Manufacturing (NUCOBAM) is to develop the qualification process allowing the use of such a metal Additively Manufactured (AM) components in a nuclear installation. Once qualified, the use of AM will allow nuclear industry to tackle component obsolescence challenges, to manufacture and operate new components with optimised design. This will increase reactor efficiency and safety. These developments will be used for three main applications in three different periods:
- In the short term by the end of the project, NUCOBAM results will be used in existing nuclear power plants (NPP) in order to continue safe operation and optimise maintenance;
- In the mid term, all NUCOBAM achievements will provide high value for nuclear fuel with new possibilities for fuel components design with improved performances and safety; and
- For long term, NUCOBAM results will allow optimisation design of future reactor components (large reactors or small modular reactors (SMR)).
Fig. 1: Laser Powder Bed Fusion technology at CEA with SLM Solutions SLM280HL®
Nuclear component challenge
This project investigates the laser powder bed fusion (LPBF) process to consolidate stainless steel materials for nuclear components of existing light-water reactors (LWR). The conventional degradation mechanisms such as irradiation, thermal ageing, mechanical loadings as well as environmental assisted cracking such as stress strain crack corrosion are examined.
To thoroughly study physical and mechanical properties of the L-PBF stainless steel, four NUCOBAM partners have produced additive manufacturing samples: VTT, AMRC, Laborelec, and CEA (see example of process in Fig. 1). The European consortium, composed of 13 partners, is combining its skills and resources to meet one of the major challenges of nuclear power plant components: the ageing of components, whether through neutron irradiation effects in the core of the reactors or thermal ageing issues for ever longer in-service periods.
Two applications in Stainless Steel (SS) 316L AM (see Fig. 3) were considered for in-service tests:
- Debris filters for fuel assemblies, developed by Framatome; and
- Valve bodies, developed by Ramén Valves.
AM is of great interest for components with complex geometry, such as grids, because it reduces both cost and time compared to conventional manufacturing by material removal.
The debris filter is also especially interesting to study as an in-core component and thus subjected to neutron irradiation degradation.
The AM valve body components are of great interest because they are subjected to thermal and pressure stresses, and have to face the problems of ageing stainless steel alloys during long-term operation.
Once both designs of debris filter and ball valve have been validated, preliminary Additive Manufacturing Process Specifications (pAMPS) have been established.

NUCOBAM objectives
Therefore, NUCOBAM has set itself five technical objectives and one dissemination related objective, as listed below.
Establish a qualification methodology for AM nuclear components to be proposed for standardisation and to be communicated to nuclear design code committees: Nuclear industry and regulators need a reliable qualification and codification process for AM as a base for future components manufacture and use in NPPs.
Develop a Laser Powder Bed Fusion (L-PBF) manufacturing plan that ensures and demonstrates process stability, repeatability and reproducibility that meet nuclear quality standards: Qualification and codification processes have to ensure that AM provides stable, homogeneous and reproducible results in terms of materials performances.
Demonstrate that L-PBF material performance meets qualification requirements: Qualification and codification processes have to ensure that AM provides materials performances in agreement with existing requirements for conventional manufacturing processes.
Demonstrate that L-PBF in-core use case meets its safety-related function and operational requirements (see IBAM in Fig. 4): Safe and reliable operation of AM components in a reactor needs to demonstrate that AM material behaviour under irradiation is consistent with existing field experience and does not undergo any unacceptable degradation.
Assess the operational performance of ex-core AM components regarding safety-related function and operational requirements: Safe and reliable operation of AM components in NPPs needs to demonstrate that AM components meets dedicated functional requirements and that AM material does not undergo any unacceptable degradation.
Disseminate and prepare the exploitation of results with nuclear industries and regulatory bodies in support to codification and industrialisation of AM: High confidence level has to be reached and shared between nuclear industry and regulator for future operation of AM components in NPPs.
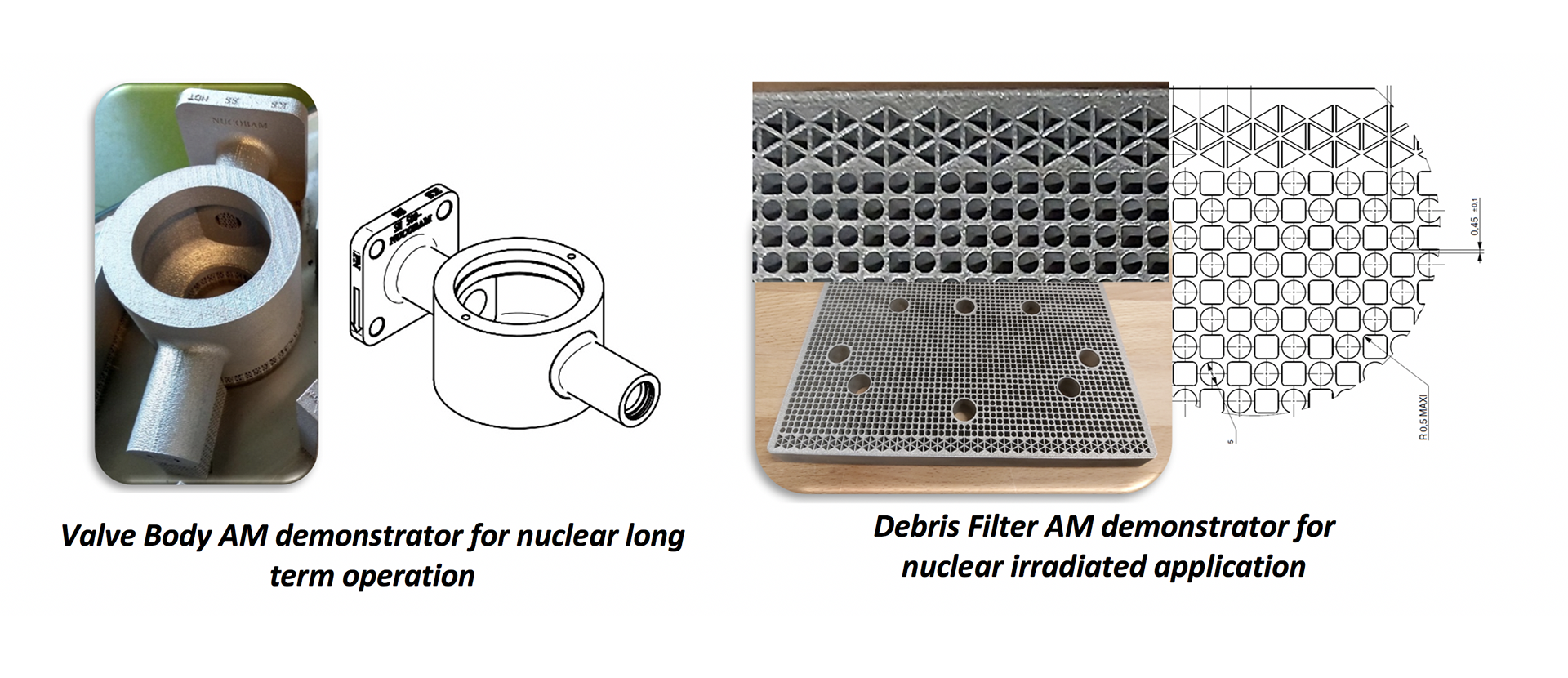
Corresponding demonstrators and associated samples have been manufactured and some of them will be submitted to post-treatment (heat treatment or high isostatic pressure). The results will be analysed and compared with existing approved manufacturing processes by design codes. This work will help to assess the gaps needed to be filled before reaching the objectives of the project, and deduce the main parameters required for specification.
Expected impact on nuclear industry
NUCOBAM will bring major advances, which will benefit to:
- Nuclear industry profitability, both for new NPP design and for existing LWR operation;
- Improve nuclear safety with optimised component design for higher performances;
- Development, qualification, and standardisation of an innovative AM technology; and
- Creation of new manufacturing industry and new employment in Europe.
The partners in charge of the designs of two nuclear components are potential manufacturing industry such as Framatome, Naval Group, and Ramén Valve. These two components will be tested to satisfy the acceptance criteria of nuclear industry. The properties of the 316L SS manufactured by L-BPF process will be studied after irradiation. The Belgium Partner SCK-CEN performed the work to prepare eight capsules named In-pile Behaviour of Additively Manufactured samples (see IBAM capsule design in Fig. 4). The project is particularly ambitious in terms of irradiation: AM Stainless Steel 316L materials will be irradiated to neutrons in the BR2 test reactor as well as in an operating nuclear power plant. The irradiation has started for approximately 18 months.
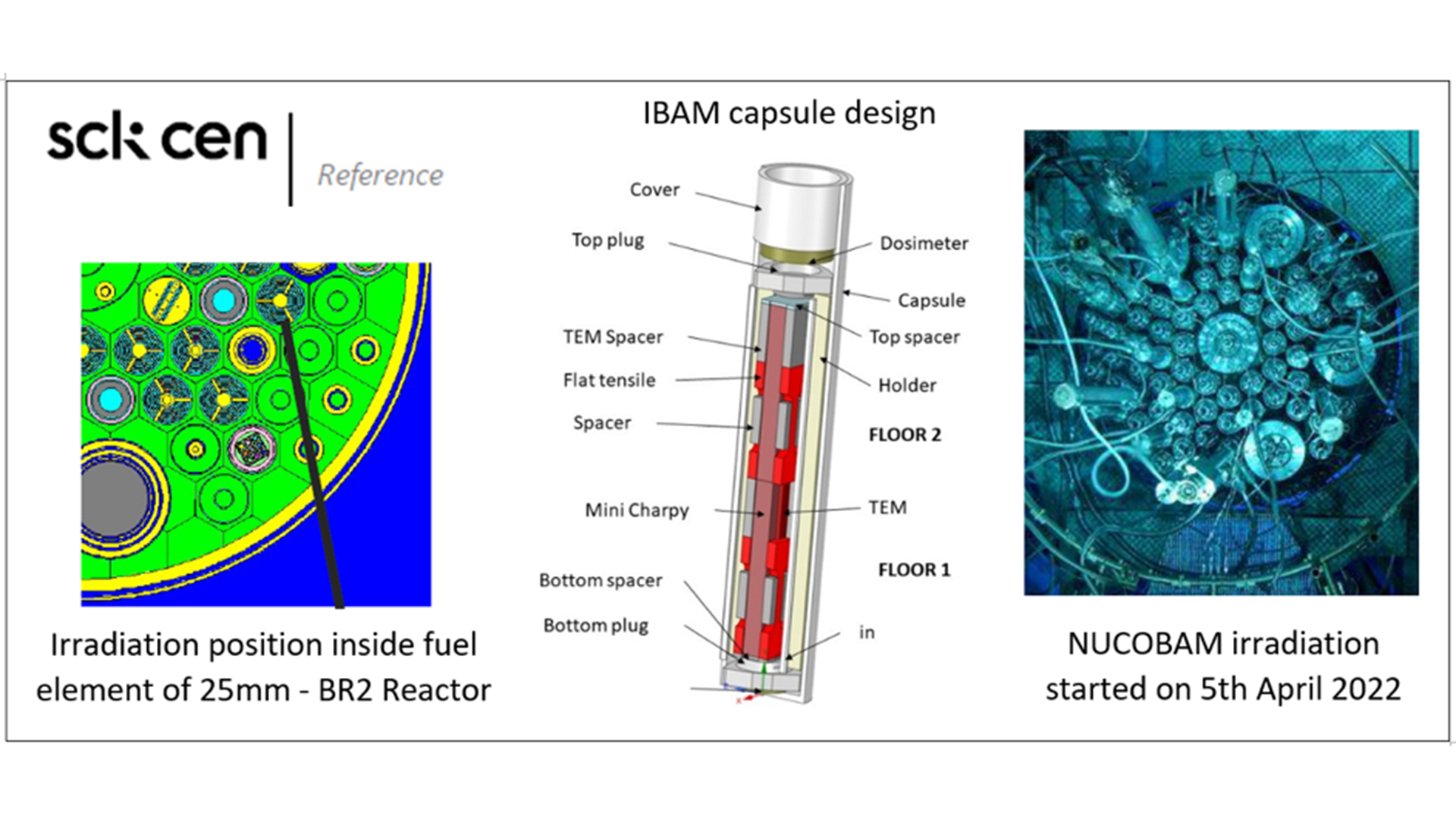
The strategy for acceptance of metal additive manufacturing in the nuclear sector is to implement directly the qualification of the process and component in nuclear design codes and standards, such as the French nuclear code for Design and Construction Rules for Mechanical Components or American standard. The project has defined new quality control methods to ensure stability, repeatability and reproducibility of AM processes.
The qualification method draft has been delivered at mid-term project, and will be completed during the next two years of the project with the results of four main tasks: qualification process, characterisation of L-PBF 316L materials, irradiated material resistance, and nuclear functional pressure tests and thermal ageing tests on component. The backbone of the standard has been defined at an early stage in the project and defined all the required sections to be documented to have a consistent standard harmonised with existing nuclear standard on 316L material (obtained by classical manufacturing and with the new requirements for AM which exist in other non-specific nuclear standards). The objective is to have a ‘pre-codification’ document to propose in the French RCC-M code.
An end user group is constituted of 17 industries from nine countries; nuclear industry experts on materials; additive manufacturing, mechanical assessment, nuclear industry, and codification to promote NUCOBAM work in the nuclear field. It will advertise the partners involved in the preparation of the pre-codification documents.
Obsolescence management of nuclear power plants remains a technical challenge for European asset owners, because original equipment manufacturers (OEMs), who were historically subjected to nuclear quality assurance requirements, may not be willing to maintain their costly nuclear qualification. Most of those manufacturers have disappeared or have left the nuclear sector. The project will help to develop in-depth qualifications for new manufacturers of components and equipment. Metal additive manufacturing has the unique potential to produce near-to-shape components in a one-step manufacturing process, followed by post-processing steps. This unique approach will simplify the fabrication value chain and make it more reactive and effective for the delivery of unique parts. The development of such a manufacturing process could improve the reliability of the material, reduce the sequence of manufacturing steps, develop new, more efficient tools, improve material performance and develop a new component design for new NPP design.
Then, the project will contribute to design components for new NPP design or existing LWR operation for the nuclear industry profitability, and to improve nuclear safety with optimised component design for higher performances.
The project will contribute to creating new additive manufacturing industry and support employment in Europe.
This project has received funding from the Euratom research and training programme 2014-2018 under grant agreement No 945313. The content of this document reflects only the author’s view. The European Commission is not responsible for any use that may be made of the information it contains.