How using a novel process called Hydro-to-Cathode™ battery recycling can result in better performance than batteries made from new materials.
As the demand for greater electrification of vehicles intensifies to reduce overall global carbon emissions and fossil fuel consumption, the power source for these electric vehicles (EVs), the lithium-ion battery has quickly become the critical limitation for further EV adoption, putting battery recycling to the foreground. The sheer number of vehicles and the relatively large size of the batteries combined make the current lithium-ion battery supply chain inadequate and further cost reductions impossible.
In addition, once all these batteries are manufactured and deployed, what happens to them after they are used and reach end-of-life? The disposal considerations for tens of millions of EV batteries, each weighing 400kg or more, obviously requires an efficient global infrastructure to accommodate hundreds of thousands of tonnes of lithium-ion batteries at a time, which currently does not exist. Lastly, lithium-ion battery factories generate a fair amount of scrap – between 6% and 10% of overall production output – which is happening now and must be taken care of.
The overall growth of the lithium-ion battery market is expected to be dominated by the EV sector, driving the vast majority of its growth. For example, in October 2021, North American-based battery manufacturing capacity announcements by companies like Toyota, Stellantis, Britishvolt and others exceeded 140 GWh,1 enough to supply over two million EVs per year. With the proliferation of massive gigafactories to supply this increase in battery demand, supply chain issues are now shifting to the raw materials required to feed all of these factories.
The key elements necessary for lithium-ion batteries include lithium and nickel, cobalt, manganese, and graphitic carbon. While used in other industries, the lithium-ion battery industry is beginning to consume most of the global production of these critical elements and concerns around raw material shortages are rising. Nowhere is this impact more evident than in the price of lithium. Since last year, the cost of lithium has more than quadrupled, from around $6/kg to $25/kg.2
While increased mining is the typical solution to meet increased demand for commodity minerals refined into battery-grade chemicals, it suffers from significant challenges.
Mining has a detrimental impact on the environment, with pollution and contamination of the local region as a common consequence. In addition, new mines take a significant amount of time from discovery of reserves to commercial operation, in some cases over a decade for lithium mines. Lastly, there is a finite amount of resources on this planet, and as easy deposits are exploited, it gets more challenging to mine the deeper reserves.
Extraction of metals from the earth thus demands proper stewardship as elemental resources become more scarce and costly to obtain. There are also geopolitical implications of the location of these critical strategic elements as they are not evenly distributed around the globe. For example, in September 2020, the United States government issued an Executive Order to address the national threat of supply chain reliance on critical minerals from foreign adversaries and specifically calls out battery elements like lithium, cobalt, and graphite.3 Thus, as lithium, nickel, and cobalt are consumed in ever-greater quantities by the lithium-ion battery industry – for economic, environmental and national security reasons – the interest in recycling spent lithium-ion batteries is rising dramatically.
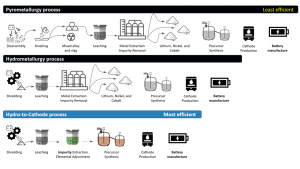
products of lesser value before going into battery manufacturing, while hydro-to-cathode goes straight to synthesis of higher value finished cathode materials
The role of recycling for lithium-ion batteries
Today, most lithium-ion batteries, especially those used in consumer devices, are not recycled due to several reasons, including collection logistics, public awareness, and general inconvenience.
As a result, many small lithium-ion batteries are discarded into general waste and household trash. The consequences of improper disposal of lithium-ion batteries, again mostly from consumer goods, are becoming more problematic.
There are not only environmental contamination and pollution hazards associated with improper disposal but also fire safety hazards. Lithium-ion batteries are dangerous due to the stored energy, resulting in overheating if they are short-circuited. This, combined with the flammability of internal components like the electrolyte, have resulted in hundreds of waste facility fires over the years. For this reason alone, recycling is a far better alternative than disposal in landfill or traditional waste management streams.
However, beyond safety and environmental contamination prevention, preservation and stewardship of the critical elements necessary to manufacture lithium-ion batteries presents a clear economic benefit. As recycled lithium, cobalt, nickel, and other elements are reclaimed and reintegrated into the supply chain, the need for primary mining can be offset. Increased supply and diversity of supply will help reduce price volatility of the commodity materials feeding the lithium-ion manufacturing sector.
Recycled materials also reduce overall carbon emissions and the costs associated with them. As a result, the overall cost of lithium-ion batteries will benefit – roughly 50% of the price comes from the battery materials utilising lithium, cobalt, nickel, and graphite – and subsequently, the cost of EVs can continue to drop, making them more affordable – displacing more and more internal combustion engine (ICE) vehicles which help to achieve global carbon emissions reduction goals.
Finally, from a national security perspective, batteries can be recycled as a strategic minerals concentrator. Domestically-sited battery collection facilities can gather the used EV and other lithium-ion batteries containing concentrated amounts of critical elements. Processing hubs can reclaim and reincorporate these elements back into domestic supply chains for reuse in locally manufactured batteries and EVs. This lowers any country’s reliance on foreign sources of lithium, cobalt, and other key elements and begins to establish a closed-loop battery economy that can be more resilient to geopolitical risks while providing additional benefits, as mentioned previously.
As the industry shifts its output from electronic devices to the burgeoning EV industry, collection and disposal of lithium-ion batteries used in cars, trucks, and other commercial vehicles are expected to be supported by the much better recycling infrastructure already present in the automotive industry. Batteries used in EVs are also hundreds of times larger than those in electronics and cannot be easily disposed of with household waste. They are also much larger than standard 12V automotive lead-acid starter batteries, which sometimes get into general waste streams. Thus, the collection of used EV batteries is expected to be somewhat easier than consumer goods with embedded lithium-ion batteries. Yet after collection, how does a lithium-ion battery get recycled?
How lithium-ion batteries are recycled
The lithium-ion battery recycling process can be classified into three main types – pyrometallurgy, hydrometallurgy, and hydro-to-cathode.
Pyrometallurgy-based recycling of lithium-ion batteries uses a high-temperature smelting process to melt the scrap batteries into a slag and is the oldest type of battery recycling in operation today. This slag goes through a subsequent leaching and dissolution step. The cobalt, nickel and some other metals can then be extracted from the resulting solution. However, pyrometallurgy is energy-intensive and relatively inefficient.
Hydrometallurgy avoids the high energy smelting process and instead relies on shredding the scrap batteries before going into the leaching process of dissolving into the various metals for extraction. Hydrometallurgy is less energy-intensive and more efficient than pyrometallurgy. Still, both result in the same end products – the reclaimed metals are separated, packaged and shipped to battery material manufacturers. These material manufacturers then use these recycled metals to create new battery materials, which then go on to lithium-ion cell manufacturing plants.
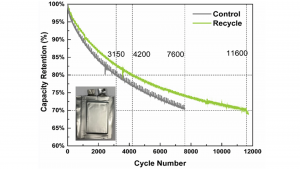
The third process, hydro-to-cathode, is unique.
While similar to hydrometallurgy, instead of extracting and separating the metals out individually and then reintegrating into battery materials, hydro-to-cathode goes from the leaching and dissolution process straight into battery material production (see Fig. 1), avoiding the individual extraction of the reclaimed metals. The hydro-to-cathode method is the least energy-intensive and most efficient of the three processes. It is being commercialised globally at a large scale by Massachusetts company Battery Resourcers.
While still in its infancy, lithium-ion battery recycling alone is not enough to support the continued growth of the battery industry. It will take many years before it can become a significant contributor. Recycling, however, will become an essential part of the overall battery supply chain, supplementing primary sources like mining and reducing the overall cost and carbon footprint of the resulting batteries that use recycled materials. As the volume of lithium-ion batteries skyrockets, recycling will be a vital part of the supply chain to realise the vision of a safe, more sustainable and circular battery economy, to support the economics of rapid battery growth, the reduction of carbon emissions and environmental impact, the stewardship of critical elements like lithium and cobalt, and the elimination of pollution and fire risk from improper disposal of used lithium-ion batteries. However, there remains one key concern about recycling batteries – performance.
Using recycled materials in new batteries
Despite the known benefits of reclaiming and reintegrating the valuable elements contained in old batteries, there are challenges in incorporating these recycled materials into new lithium-ion batteries, especially for EVs. The perception of poor performance in recycled products versus new products is well-known. When considered in the context of the automotive industry, which has some of the most stringent quality control and reliability standards, this perception can derail the vision of a truly circular economy.
Additionally, the battery is such a critical part of an EV that the notion of recycled batteries can undermine consumer confidence in the reliability and performance of the vehicle. “In general, people’s impression is that recycled material is not as good as virgin material,” says Yan Wang, a professor of mechanical engineering at Worcester Polytechnic Institute (WPI). “Battery companies still hesitate to use recycled material in their batteries.” However, a new study released by the United States Advanced Battery Consortium (USABC) puts to rest these perceived quality and performance issues around using recycled materials in new lithium-ion batteries designed specifically for the automotive industry.
In this study, NMC111-type cathode cells were produced using the hydro-to-cathode recycling process. NMC111 is a typical and common cathode material used worldwide in lithium-ion batteries today. For comparison purposes, control cells using NMC111 cathode materials produced using traditionally mined elements and processes were also produced. These cells were then compared using a series of rigorous standard performance tests that measured key parameters such as energy density, power capability, self-discharge, and cycle life, as well as material characterisation tests looking at the material structure and electrochemical properties. Interestingly, the hydro-to-cathode NMC111 performed as well as or, in some cases, even better than the traditional NMC111.
Among the improved performance parameters was cycle life – the recycled cathode cell exhibited over 50% longer cycle life than the traditional cathode cell, surviving 11,600 cycles compared to just 7,600 cycles for the control cell (see Fig. 2). In addition, high power capability was increased by 88% compared to traditional. In tests at a 5C rate (equivalent to about a 12 minute very fast charge), the recycled cathode cell delivered substantially more energy than the traditional cathode cell.
The rationale for this surprising result? As it turns out, the hydro-to-cathode NMC111 particles exhibited a different microstructure resulting in some performance benefits especially related to cycle life and power capability. The particles showed increased porosity and larger voids (see Fig. 2), which improve properties such as lithium diffusivity, which is the ease with which lithium ions travel through the material as the battery is charged and discharged. This results in higher power capability since the flow of lithium ions is essentially faster. It also helps provide strain relief – as lithium ions are inserted or extracted from the cathode material, the cathode particles tend to expand and contract. The modified pore structure allows this expansion and contraction to occur without damaging the particles, which disrupts their ability to store lithium ions and ultimately causes the battery to fail and not hold a charge.
A brighter future from the hydro-to-cathode process
Enormous demands on the lithium-ion battery supply chain extend beyond merely the battery gigafactories into both end-of-life considerations and commodity element resources. Recycling will undoubtedly be a key pillar of the future battery and EV industry for environmental and safety reasons as well as economic and geopolitical ones. While recycled materials can result in poorer performance in some cases, it is clear that novel recycling and synthesis methods like the hydro-to-cathode process can improve the performance of batteries above and beyond traditionally produced batteries.
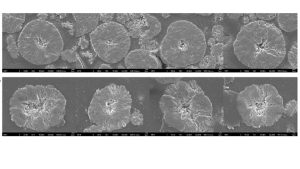
The results from the USABC study show that cathode materials using the hydro-to-cathode process have increased cycle life and power capability compared to traditionally produced cathode materials which use pristine, virgin materials that are newly mined. While more work could be done to investigate the full nature of these results further, it is incredibly encouraging to envision a truly circular and sustainable battery economy. Improved economics, greater safety, lower environmental impact, proper stewardship of critical elements, resilience to geopolitical risk, and higher performance – all combine to make a compelling argument to begin scaling up these recycling and synthesis processes to prepare the industry for a truly sustainable, no-compromises EV and battery future.
References
1 www.linkedin.com/posts/james-frith-424a2b6a_battery-lithium-nickel-activity-6856178805678084097-aKwi
2 www.benchmarkminerals.com/membership/benchmarks-lithium-carbonate-prices-reach-new-all-time-highs
3 www.federalregister.gov/documents/2020/10/05/2020-22064/addressing-the-threat-to-the-domestic-supply-chain-from-reliance-on-critical-minerals-from-foreign
Please note, this article will also appear in the eighth edition of our quarterly publication.