Researchers have developed a propeller design optimisation method that paves the way for quiet and efficient electric aviation.
In recent years, electrification has been described as necessary to reduce future aviation emissions. Due to the challenges of longer ranges, interest is chiefly focused on electric propeller planes covering shorter distances. Propellers connected to electric motors are considered the most efficient propulsion system for regional and domestic flights.
The Chalmers University of Technology team has addressed noise issues with electric aviation through their invention. Electrification is seen as having an important role to play in the fossil-free aviation of tomorrow. However, the more energy-efficient an electric aircraft is, the noisier it gets.
Electric aviation propellers cause another kind of emission – noise. The noise from the propeller blades would cause massive disturbances. Future aircraft must fly at relatively low altitudes, with noise disturbance reaching residential areas and animal life.
The researchers aim to overcome this problem in their study, ‘Blade-Tip Vortex Noise Mitigation Traded-Off against Aerodynamic Design for Propellers of Future Electric Aircraft,’ published in Aerospace.
The problem with energy-efficient propellers
When creating propellers for electric aviation, researchers face a dilemma. The ambition of developing electric aircraft that are both quiet and energy-efficient is somewhat thwarted by a trade-off problem.
“We can see that the more blades a propeller has, the lower the noise emissions. But with fewer blades, propulsion becomes more efficient, and the electric aircraft can fly for longer,” explained Hua-Dong Yao, Associate Professor and researcher in fluid dynamics and marine technology at Chalmers University of Technology.
“In that sense, there is a trade-off between energy efficiency and noise. This is something of an obstacle for electric aviation.”
Optimising quiet propellers to overcome noise issues
However, the researchers may be one step closer to a solution for the electric aviation industry. They have succeeded in isolating and exploring the noise that occurs at the tip of the propeller blades, a known but less well-explored source of noise. In isolating this noise, the researchers were able to fully understand its role in relation to other noise sources generated by propeller blades.
These propellers are designed to operate under the same freestream flow conditions and similar electric power consumption. The Improved Delayed Detached Eddy Simulation (IDDES) is adopted for the flow simulation to identify high-resolution time-dependent noise sources around the blade tips.
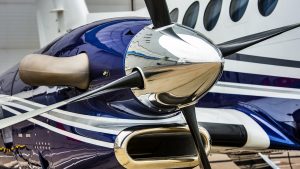
Moreover, by adjusting a range of propeller parameters, such as pitch angle, chord length, and the number of blades, the team found a way to optimise the propeller design and even out the trade-off effect between efficiency and noise.
“Modern aircraft propellers usually have two to four blades, but we’ve found that by using six blades designed using our optimisation framework, you can develop a relatively efficient and quiet propeller.”
Hua-Dong Yao said: “The propeller achieves a noise reduction of up to 5-8 dBA (weighted decibel) with only a 3.5% thrust penalty, compared to a propeller with three blades. That’s comparable to the noise reduction of someone going from speaking in a normal conversation voice to the sound you would perceive in a quiet room.”