Increasing circularity in construction by developing eco-friendly alternatives to traditional building materials using digital tools and methodologies like Satellites, Digital Product Passports, 6D-BIM and Blockchain technologies.
The global construction industry is a significant driver of environmental impact, responsible for over 30% of the extraction of natural resources, 25% of solid waste generated, and 40% of greenhouse gas (GHG) emissions. A substantial portion of these emissions originates from embodied carbon, which is produced throughout the construction, demolition, and supply chain processes. The European Commission suggests that enhancing material efficiency could cut these emissions by up to 80%.
Cement and steel are key contributors, accounting for over 80% of the total embodied GHGs in construction. While Europe has achieved high recycling rates for steel, further reductions in GHG emissions are pending industry electrification and green energy integration. Conversely, cement used in concrete production remains challenging to recycle, necessitating the exploration of low-carbon alternatives and innovative construction techniques to meet industry targets.
To address these challenges, the RECONSTRUCT project aims to revolutionise construction practices through the development of low-carbon materials, modular construction components, and circular building designs. The project focuses on integrating construction and demolition waste (CDW) and other industrial by-products into new construction materials, designing for modularity and deconstruction, and minimising waste throughout a building’s lifecycle using innovative digital systems and lifecycle assessments.
Digital system for construction and demolition waste management
Construction and Demolition Waste (CDW) quantification and characterisation methods include site visits, waste generation rates, lifetime analysis, classification system accumulation, and variable modelling. These methods are manual, time-consuming, unreliable, and prone to human error. CDW localisation is currently possible only through accessing municipal construction registers. Existing CDW marketplaces do not leverage artificial intelligence (AI) to select optimum waste products, nor do they consider the wider industrial ecosystem for opportunities. The RECONSTRUCT project aims to automate and accelerate the sourcing of secondary materials, like CDW and other waste.
An integrated solution through a User interface (UI) Decision-Support Tool includes a comprehensive digital system designed to localise, quantify, characterise, and source CDW and other waste materials. This system comprises four interconnected modules, each serving a specific function:
- Localisation and Estimation: Using image-processing techniques on Copernicus satellite and drone imagery, this module will identify and estimate the quantity of CDW on construction sites. A cloud-based Earth Observation (EO) data pipeline will preprocess optical and synthetic aperture radar (SAR) imagery, providing Analysis Ready Data (ARD). This data will train deep learning (DL) algorithms for semantic segmentation, identifying CDW in urban areas.
- Quantification and Identification: This module will leverage image processing on CCTV data and drones to quantify and identify large objects and components within CDW. To improve accuracy and efficiency, a prototype DL-based object detection model will be developed.
- Material Characterisation: Portable hyperspectral imaging (HSI) systems will perform real-time characterisation of CDW, determining the material content of rubble. Advanced classification methods will analyse the hyperspectral data, predicting material composition with high accuracy.
- Industrial Symbiosis: Utilising SYNER software, this module will optimise the industrial symbiosis process by mapping industrial activities and waste in a region and facilitate opportunities for resource reuse and waste minimisation.
Circular construction materials and components
Traditional Portland Cement with recycled material (up to 25%) is commercially available, but the CO2 reduction achieved is limited. Alkali-activated cement (ACC) production only generates one-fifth of the GHG of Ordinary Portland Cement (OPC) due to the high content in industrial by-products. AAC is commercially available, but performance and scalability suffer due to the unstable supply of secondary materials. Further, secondary materials with very good potential have not yet been used.
RECONSTRUCT focuses on developing circular construction materials with low virgin content and high recyclability. Due to the challenges regarding the cement contribution to the construction sector embodied GHGs, the project is developing the following low-carbon alternatives:
- Alkali-Activated Cements (AACs): Using as raw materials industrial by-products and wastes like Ground Granulated Blast Furnace Slag (GGBFS) and biomass ash (from almond husks and olive pits), AACs offer a sustainable alternative to Ordinary Portland Cement (OPC), maintaining its performance characteristics and reducing CO2 emissions significantly. The novel AAC formulas will achieve an impressive 80% reduction of embodied carbon compared to OPC while performing equally or better than OPC in key performance indicators (durability, strength, etc.) and at lower costs due to the lower cost of the secondary raw materials.
- Precast Concrete Components: The novel AAC will be used to develop various low-carbon Alkali-Activated Cement Concrete (AACC) precast elements, including pavement blocks, façade panels reinforced with composite bio-based rebars, and modular sandwich floor systems using Textile Reinforced Recycled Concrete (TRRC). These components are designed to ensure durability, modularity, and ease of disassembly, promoting reuse and recycling.
6D-BIM: Enabling circularity across the building’s lifecycle
Measuring the impact created by the implementation of circularity on construction is infrequent, inconsistent, and difficult. Although several standards do exist, they mostly focus on the building’s environmental impact, while a commonly accepted and applied set of metrics and methods to measure both the whole-life carbon and the circularity of projects are desperately needed.
Fortunately, many individuals and groups are working to improve clarity and consistency on these issues. This includes Level(s) framework indicators for sustainable buildings and Environmental Product Declarations (EPD).
Most waste management (WM) plans employed in the industry primarily lean towards the construction phase, and the efforts taken in the planning and design phases to reduce waste are trivial. In contrast, one-third of the waste-causing factors are design incurred. This scenario should be significantly improved via stabilised and reliant workflows throughout the project life cycle to employ systematic thinking. Building Information Modelling (BIM) presents an option for doing that.
BIM is a process for creating and managing information on a construction project throughout the project’s lifecycle. As part of this process, a coordinated digital description of every aspect of the built asset is developed, which includes a combination of information-rich 3D models and associated structured data such as product, execution and handover information.
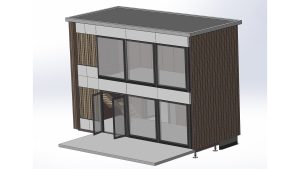
Any dimension, in addition to the three geometrical ones, represents further aspects that the users can set out to model. 4D-BIM is commonly meant to include scheduling information to model construction sequences, and 5D is used when the financial cost of digital objects is added. Although many studies have adopted 3D-BIM for construction and assembly processes, progress is needed in automating the optimisation of waste valorisation in BIM models.
In order to enable the modelling of environmental performance, RECONSTRUCT is developing a 6D-BIM that includes sustainability information and extends the BIM to include information on deconstruction and the second life of materials. This information will come in the form of integrating several tools into the BIM. The first tools are a database that collects information about the environmental performance and circularity potential of construction materials and a cloud-based software that manages that information at a building level (BEDEC and TCQi by ITeC). These tools allow for calculating a circularity passport, Level(s) indicators for sustainable buildings, and Environmental Product Declarations (EPD) based on the building design. The aforementioned 6D-BIM will enable interaction with the materials and building components and retrieve data from EPDs and BIM object databases to propose quantified alternatives of LCA indicators from the design stages.
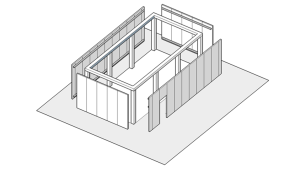
Current tools only do this at detailed design stages, hampering the design stage’s reusability and waste minimisation potential. This tool will incorporate semantic web technologies (Protege, SPARQL), deep learning, and automated LCA optimisation scenarios. It will be able to write the chosen option into the BIM model and upload the area LCI information and the model information in a seamless process.
Digitisation, tracking and tracing throughout the value chain
Deconstruction activities render several issues regarding the characterisation and traceability of building materials due to their high compositional complexity and demand for high-quality/quantity data. In order to create closed material loops and conduct multi-parametric optimisation, we need to achieve full digitisation and track and trace construction materials. To this end, we will expand the concept of the material passport towards a dynamic Digital Product Passport (DPP) for construction. To that end, we will develop a traceability module based on blockchain that allows the secure data collection of materials logistics operations and a mechanism for secure data sharing. All the collected information will contribute to the DPP, allowing the dynamic update of data based on the lifecycle of the product, as well as data about the previous life of the materials. An interoperability layer will allow the exchange of data with the Building Material Passport (BMP) and subsequently with the 4D-BIM.
The design of open-source, multifunctional buildings and the modular prefabricated construction approach
RECONSTRUCT will construct two modular building demonstrators, representing traditional onsite construction and modular prefabricated construction. These demonstrators will validate the project’s innovations and provide real-world examples of circular construction practices.
The Belgian demonstrator will be a modular office building located at Green Energy Park in Brussels. This living lab environment will support the testing and optimisation of the project’s innovations, promoting the benefits of circular construction to a broad audience.
In Barcelona, a traditional onsite construction project will showcase the application of RECONSTRUCT’s materials and methods. This demonstrator will highlight the potential for circular practices in conventional construction settings.
Establishing Circular Territorial Clusters
The circular economy in the built environment is in its infancy. Current research examining the potential for circular construction identifies a need for a clearer understanding of the circular economy and circular business models, as well as greater integration between stakeholders in the construction value chain. To this end, recent research has highlighted the key role of social innovation in the circular economy. According to the Organization for Economic Cooperation and Development (OECD) definition: “Social innovation refers to the design and implementation of new solutions that imply conceptual, process, product, or organisational change, which ultimately aim to improve the welfare and wellbeing of individuals and communities.” In keeping with this definition, the RECONSTRUCT solution seeks to engender new processes and organisational change within the construction industry, which ultimately improves the wellbeing of individuals and communities. To do so, tasks throughout the project draw on frameworks from the social sciences to ensure that the solution developed is co-produced with key stakeholders (including building occupants) who are involved in the whole lifecycle of buildings and the communities in which they are situated. This approach moves beyond current approaches, which privilege the economy above the social and environmental aspects of sustainability.
Along these lines, RECONSTRUCT will adopt the guidelines of the Circular Cities and Regions Initiative (CCRI), develop its ecosystem of innovations as a ‘Systemic Circular Solution’ and establish ‘Circular Territorial Clusters’ in the regions around its two demonstrators (Barcelona and Brussels) in order to roll it out. These activities will involve the creation of regional networks of stakeholders and the use of the Digital Stakeholder platform to facilitate their engagement and participation in the co-creation of policies (including guidelines for public investments, waste regulations, public procurement, regional construction criteria/rules), circular business models, and best practice guidelines that will enable the development of the local circular construction value chain.
Moving towards a circular construction industry
The RECONSTRUCT project represents a significant step towards a more sustainable and circular construction industry. By developing innovative materials, optimising digital tools, and fostering collaboration among stakeholders, RECONSTRUCT aims to reduce the environmental impact of construction, enhance resource efficiency, and promote social innovation. As the industry moves towards a circular economy, initiatives like RECONSTRUCT will play a crucial role in shaping a more sustainable built environment.
Please note, this article will also appear in the 19th edition of our quarterly publication.