With its new approach to magnets, The Advanced Magnet Lab is enabling the use of lower-cost materials, novel design and manufacturing, revolutionising motors and generators to reinvent the magnet supply chain.
Magnets are at the heart of products like motors and generators, which are in turn used in virtually every sector of society – electrical, manufacturing, consumer products, and transportation. Magnets are a critical component in areas like defence, used for instrumentation, weapons, and vehicles (land, air and sea). In July 2019, the United States signed into law a Presidential Determination to address the nation’s security risk of dependency on foreign adversaries for magnets. This single-source model presents an obvious opportunity for companies able to tap into the source, but also a very clear and present danger to disruption of a magnet supply chain where materials for a product can only be sourced from one, occasionally economically hostile place.
With its innovative approach to magnet technology, the Advanced Magnet Lab, Inc. (AML) located in Melbourne, Florida, is poised to do just that.
China’s stronghold on the magnet supply chain
China dominates the Rare Earth Magnet Industry (REMI), producing greater than 85% of the world’s supply. China’s vertical integration of cheap labour, raw materials, and unsafe environmental standards have resulted in a ‘high-barrier to market-entry’ for competitors worldwide. Magnets are a commodity, sold by the kilogram and metric ton. Historically, companies who have entered the magnet supply chain could not compete, due to China’s ability to control the market.
The conventional approach is the wrong approach
While scale has increased and materials have developed and improved, the materials used to make magnets, magnet technology and the methods for manufacturing magnets have been the same for decades. Conventional magnets and assemblies are expensive and limit design engineers to configurations which are not optimised for performance and cost of the end-use products, such as motors and generators. Magnets are produced in blocks, then cut into small pieces and sold as commodity. They are also restricted in shape, size and mostly single-direction magnetisation, meaning the largest market motors require dozens, hundreds, and sometimes thousands of magnets in an assembly. With very strong magnetic fields, assembly into a motor is complex and costly. Furthermore, the trend is towards higher-grade and better performance, requiring more expensive raw materials and manufacturing and an unclear intellectual property landscape.
Breaking China’s stronghold requires innovation to enable a sustainable REMI supply chain that reinvents technology and transforms the REMI. AML is reinventing the REMI supply chain and addressing every element of the supply chain – materials, manufacturing, performance and assembly.
The AML approach
AML’s approach is not to cut small-piece parts of magnet blocks and selling commoditised magnets. AML magnets are designed and manufactured for optimum size, shape and magnetisation, resulting
in greater performance and lower cost for the end-use product.
AML focuses on several key aspects to achieve
this, including:
- Materials: The AML approach improves the application performance of all existing magnet materials and enables new, lower-cost materials including non-rare-earths;
- Manufacturing: AML prides itself on its novel and state-of-the-art manufacturing. Highly automated, it provides high-rate, high-yield, high-quality, ideal magnetisation and at a much lower capital cost than conventional manufacturing methods;
- Performance: AML replaces conventional north-south configurations with optimised magnet shapes, magnetisation and topologies, resulting in improved performance; and
- Assembly: The topologies reduce magnet count and provide ease of assembly, resulting in solutions at a fraction of the cost compared to conventional magnet assemblies.
AML has a wide range of solutions within its portfolio to reinvent the magnet supply chain.
PM-Wire™
AML has developed PM-Wire – a novel solution for the design and manufacture of magnets which improves performance and lowers the cost of end-use products like motors and generators. This approach is the ideal way to produce magnets, it uses a ‘wire-like’ manufacturing process where all the critical process parameters can be adjusted and precisely maintained for any magnet alloy type – including non-rare-earth materials.
PM-UNIFORM™
Consisting of straight, curved, ring, or helical magnets with transverse or radial magnetisation, these can be produced in metre lengths and offer lower cost assembly and reduced part count.
PM-AXIAL™ for motors
These are curved magnets with axial magnetisation, allowing rotor topologies with breakthrough benefits. The PM-AXIAL has increased performance, with Halbach performance, higher temperature operation and a reduced overwrap and containment sleeve. By being iron free, it is also reduced in weight. Moreover, it has lower cost assemblies due to a reduced part count, ease of assembly and lower grade/cost materials.
PM-360™
Straight, ring, or helical magnets with ‘continuously changing magnetisation direction’, PM-360 offers increased performance, better than Halbach performance, as well as a reduced weight due to being iron free. The PM-360 also has a reduced part count and is easy to assemble, meaning lower cost assemblies for the REMI supply chain.
PM-Wire solution examples
Replacing conventional magnets with PM-Wire improves the performance and lowers the cost of motors. The following are three real-world examples showcasing the technology impact:
- AML replaces the north-south pole configuration in industrial motors with a PM-Wire configuration called PM-AXIAL. Using the same magnet alloy, this solution provides Halbach array performance, increases operational temperature by 20%, eliminates iron in the rotor and reduces the rotor overwrap thickness by 50%;
- PM-360 topology replaces 2,750 Halbach arranged magnets in electric vehicle motors with eight PM-360 rings and eliminates the need to actively cool the motor rotor; and
- PM-AXIAL topology can achieve the U.S. Department of Energy’s electrical vehicle motor power density goals of 50 KW/L with low or no rare-earth content materials.
AML technology and business execution
AML’s approach to the REMI supply chain is unique in technology and business. The company focuses on the end-use product and lets those requirements determine the best PM-Wire solution. AML does not compete in the commoditised, ‘me-too’, ‘piece-part’ magnet market.
PM-Wire Development Phases
The PM-Wire development has followed a number of phases, including:
- Phase 1, where the process was validated using isotropic non-sintered NdFeB having uniform magnetisation;
- Phase 2, which validated ‘continuously changing magnetisation’ (single-piece Halbach array) using anisotropic bonded NdFeB compositions;
- Phase 3, which saw the design, build and commissioning of an advanced PM-Wire Pilot Manufacturing facility funded by the U.S. Department of Defence; and
- Phase 4, which validated NdFeB sintered PM-Wire magnet configurations funded by the U.S.Department of Defence.
PM-Wire applications development
AML has unique experience in the development of magnet-based systems, including motors and generators. Using proprietary software, the company works directly with the end-use product customers based on three scenarios. The first is the ‘plug-and-play’ design, which removes conventional magnets and then optimises with PM-Wire magnets with no change to stator design. Next is the optimisation of an existing design, where a machine design is optimised, including stator, and then further optimised with PM-Wire magnets. Finally, there is the generation of a new design, co-developing a new machine optimised with PM-Wire magnets.
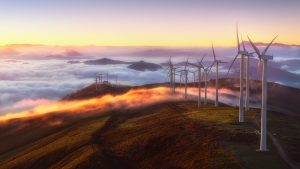
Recycling to magnets
AML is collaborating with ReElement Technologies (ReElement) – a company establishing large-scale production capabilities to recycle end-of-life products such as wind turbines, motors and consumer products.
Extraction of rare earth oxides is needed for the magnet supply chain using a clean and efficient chromatography process. The collaboration will result in production facilities which recycle end-of-life products to manufacturing of PM-Wire magnets for new-life products.
ReElement has leveraged over 40 years of development and commercial success in the pharmaceutical, insulin and sugar industries. This is not a novel technology but rather a new application of an existing one. Its approach has a proven efficacy on a commercial scale to separate and purify both rare earth elements (REEs) and critical battery minerals to ultra-high purity with high throughput. Through its 40+ years of development and commercial application, ReElement can very accurately dial in mass-balance calculations to adapt very quickly to different feedstocks, achieving targeted yield (greater than 95%) and purity (greater than 99.9%) goals very efficiently.
Market approach for the REMI supply chain
AML’s approach to the market is unique. AML focuses on what matters, the magnet-based end-use product like a motor, and optimising the motor for performance and cost. Unlike the conventional approach, PM-Wire provides engineers with a whole new set of knobs to turn in order to optimise motor design. PM-Wire can be used with all existing sintered magnet alloys and opens up new markets for non-sintered. Motor designs can now be fully optimised for performance, including: weight, torque, operating temperature and ease of assembly.
The optimisation process incorporates AML’s unique experience with proprietary software, providing a comprehensive design which considers all aspects of the end-use product design for the magnet supply chain. For example, AML performs design studies which consider a full range of alloy materials ranging from non-rare-earths to non-sintered anisotropic to sintered alloys.
Market readiness
AML today is capable of producing non-sintered magnet solutions at full rate to reinvent the magnet supply chain. A state-of-the-art manufacturing line funded by the U.S. Department of Defence was designed, built and commissioned by AML engineers. This robotic line has the capacity to produce 2-6m per minute of PM-Wire magnets. AML is also currently producing sintered PM-Wire magnets at lab-scale and, over the next 12 months, will be establishing full-rate capabilities for sintered magnets.
AML is supported by the U.S. government and large industry for the collective mission of establishing a sustainable domestic supply chain. Strategic Partners include the U.S Department of Defence, U.S. Department of Energy, U.S. Navy, Oakridge National Laboratory, U.S. Defence & Aerospace Companies, ReElement and more.
For more information about becoming a partner, customer, or for general inquiries please contact info@amlsm.com or call us at +1 321 728 7543. To learn more about AML, visit www.mitusmagnets.com or connect with the company on Facebook, Twitter and LinkedIn.
Please note, this article will also appear in the fifteenth edition of our quarterly publication.