Dr Carlos Ziebert, head of IAM-AWP’s Calorimeter Center, KIT, explains how calorimetric methods can be applied to improve the safety of electric vehicle batteries.
Transport represents over a quarter of total greenhouse gas emissions in the EU, making it a key environmental issue, and the European Commission aims to reduce emissions by 90% by 2050. A key pillar of their ‘Sustainable and Smart Mobility Strategy’ is to introduce at least 30 million zero-emission electric cars (Fig. 1) onto Europe’s roads, replacing the use of petrol and diesel vehicles. To guarantee this goal is achieved, researchers must improve the safety of electric vehicle batteries.
Such electric vehicles are powered by large lithium-ion batteries (Fig. 2), and while these have many advantages, including a high specific energy, long cycle life, and low self-discharge rates, concerns over their safety have had a major influence on consumers’ willingness to adopt lithium-ion battery technology and have hindered the rapid development of electric vehicles.
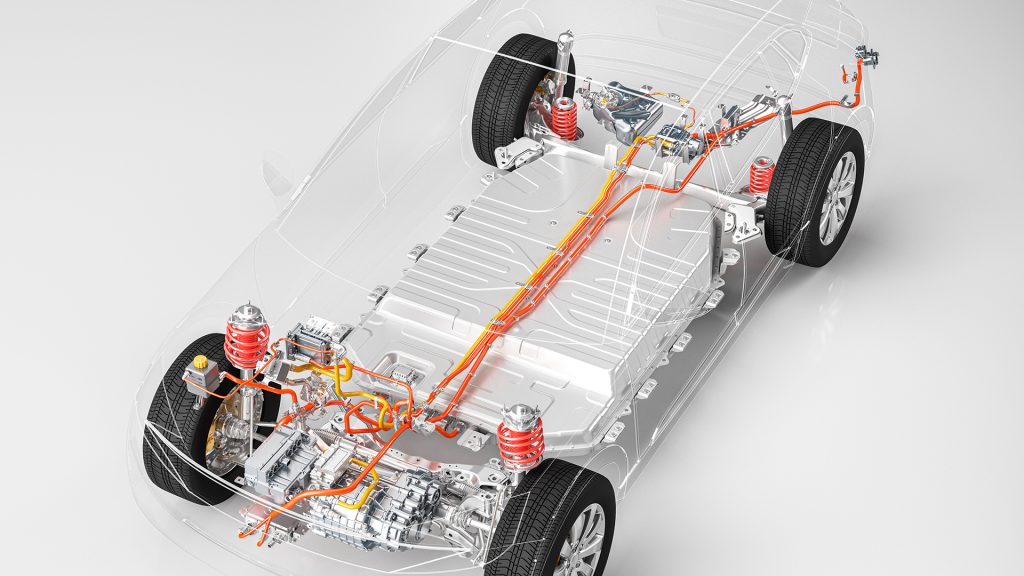
Safety issues
An uncontrollable temperature increase in lithium-ion batteries (known as a thermal runaway) can cause them to ignite, or even explode, and although such instances are few and far between, they do attract negative publicity, which can affect public opinion.
A holistic safety assessment is, therefore, a prerequisite for the upscaling and market acceptance of electric vehicles powered by lithium-ion batteries.
The causes and effects of thermal runaway can be very diverse and complex (as highlighted in Fig. 3). Internal or external mechanical, operating or thermal stresses can lead to an internal heating of the cell which initiates different exothermal reactions, followed by a further temperature and pressure increase. The final effects can be empirically classified by the Hazard Level (1-7).
Cell designs, component integrity, manufacturing, and ageing processes all have critical influence on the safety of lithium-ion batteries.
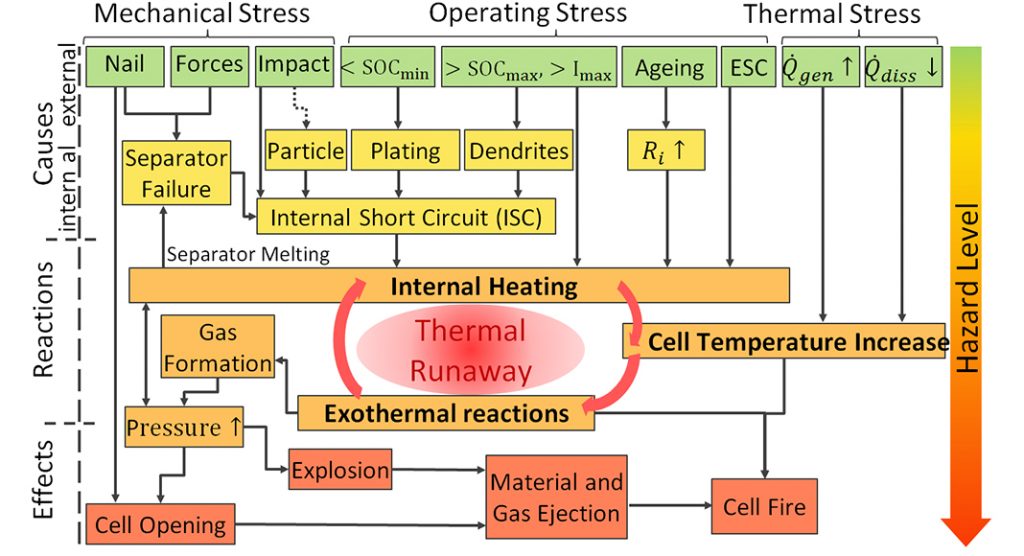
Benefits of battery calorimetry
Calorimetry – or the process of measuring heat data during chemical reactions – allows the collection of the quantitative data required for optimum battery performance and safety. Sophisticated battery calorimetry enables new and quantitative correlations to be found between different critical safety and thermally related parameters. This is very important because you need to know how many Watts a cell will produce under every condition to adapt the battery and thermal management systems. The temperature, heat and internal pressure evolution can be studied, while operating cells under conditions of normal use, abuse or accidents.
There are two main disadvantages of conducting abuse tests without a calorimeter and these are that the maximum safe temperature would be underestimated and the consequences would be understated in terms of severity and speed.
Tests carried out in a calorimeter are much more sensitive than hotbox tests and reveal the entire process of the thermal runaway with the different stages of exothermic reactions. These data are essential for battery and thermal management, as well as safety system design. Combined with multi-scale electrochemical-thermal modelling they provide a powerful tool for thermal runaway prevention and ageing prediction.
Holistic safety assessment
Materials level
On a materials and components level, differential scanning calorimetry (DSC) and extremely sensible Tian-Calvet calorimeters can be used to provide thermophysical parameters such as heat capacity or thermal conductivity and to analyse in detail the possible phase transformations and the thermal stability of new battery materials.
Small-scale cell level
On a small-scale cell level isothermal and larger-scale Tian-Calvet calorimeters from Setaram Instrumentation allow the determination of the heat generated during cycling with great accuracy. Using such calorimeters allows for 21700 format cylindrical cells with a maximum capacity of 5 Ah (currently used in the Tesla Model 3, for example) to be studied. However, such calorimeters are not designed to withstand the high temperatures and explosions that can occur during a thermal runaway.
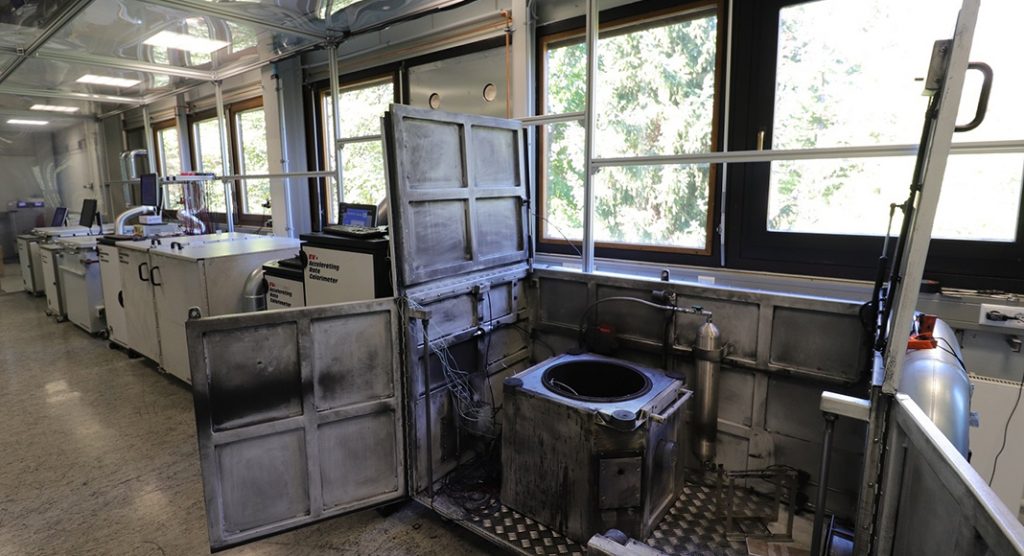
Large-scale cell level
Therefore, the next level is robust adiabatic Accelerating Rate Calorimeters (ARCs), which are available nowadays from different manufacturers in a range of sizes. These allow the evaluation of thermodynamic, thermal and safety data for lithium-ion cells on material, cell and pack level for both normal and abuse conditions (thermal, electrical, mechanical).
The IAM-AWP Calorimeter Center, which was established in 2011, currently operates Europe’s largest Battery Calorimeter Laboratory providing six Accelerating Rate Calorimeters (ARCs) from Thermal Hazard Technology of different sizes. These range from the size of a coin to a 40cm x 30cm automotive pouch or prismatic format with capacities of up to 150 Ah (see Fig. 4). These robust battery calorimeters allow the evaluation of thermodynamic, thermal and safety data for lithium-ion batteries under quasiadiabatic and isoperibolic environments for both normal and abuse conditions (thermal, electrical, and mechanical). The cell is inserted into the calorimeter chamber, which has heaters and thermocouples located in the lid, bottom and sidewalls (see Fig. 5), which adjust the required ambient conditions that are characterised by the related thermocouples.
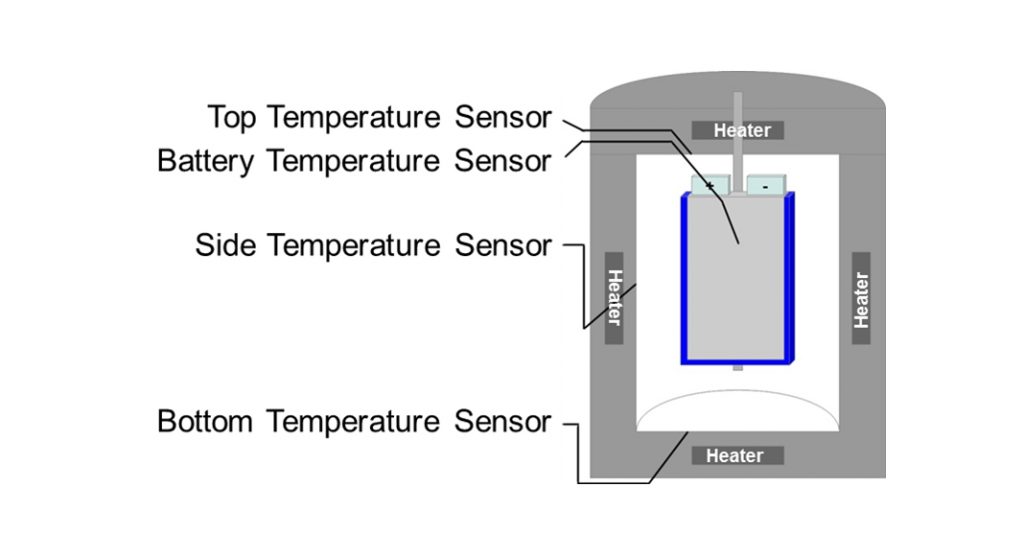
Small-scale pack level
As described in more detail in our recent article in issue 4 of The Innovation Platform, the largest available ARC allows us to study the thermal propagation in small-scale packs, in order to develop and qualify suitable countermeasures, such as heat protection barriers1 The thermal propagation means that the thermal runaway propagates from one cell to the neighbouring cells, and this cascading effect can lead to the complete destruction of the module or pack.
Safety testing in battery calorimeters
It is well-known that the failure of lithium-ion batteries can be caused by mechanical, electrical or thermal abuse, as outlined in the relevant safety testing standards, such as UN 38.3, SAE-J2464, IEC-62133, GB/T 31485 and UN GTR100.2.
The following three safety tests can be performed in the ARCs on cells for electric vehicle applications:
Mechanical abuse: Nail and crush test
When the electric vehicle battery is deformed by an applied force, such as a car crash, or the puncturing of the battery in the bottom of a chassis by a sharp object, mechanical abuse occurs. This is simulated in the ARC by pushing a nail or a blunt object into the cell, which provides not only a pass/fail type test to qualify cells, but also quantitative data by measuring the cell temperature, cell voltage and evolved heat. Often the mechanical abuse causes an internal short circuit because the separator of the battery is damaged or punctured.
Electrical abuse: External/internal short circuit test, overcharge test, over-discharge test
Electrical abuse refers to the abnormal operation of electrical components, such as short circuiting, overcharging, and overdischarging. Typically, electrical abuse is related to a failure of the battery management system, however the trend for fast charging might also increase the risk of thermal runaway because it can lead to the deposition of highly reactive lithium on the carbon anode – the so-called lithium plating. The reason for that effect is that the lithium ions migrate faster than they can intercalate.
The electrical abuse of automotive format cells can be replicated in the ARC by applying an external short circuit, overcharging or overdischarging, leading to different failure modes.
Thermal abuse: Heat-Wait-Seek test, ramp heating test, thermal propagation test
The most frequent abuse test that is performed in ARCs is for thermal abuse, using the Heat-Wait-Seek (HWS) test. As soon as self-heating is detected within the cell, the heaters in the calorimeter chamber immediately follow any change of the cell temperature preventing the heat transfer to the chamber. This causes the temperature of the cell to continue to rise until a thermal runaway occurs, or the chemicals for this exothermal reaction are completely consumed.
Fig. 6 shows examples of cylindrical, prismatic and pouch cells after thermal runaway initiated by an HWS test in an ARC.
For the Ramp Heating test, which mimics a Hot Box test, the temperature of the cells is increased at a constant rate instead of using the stepwise heating method.
For the thermal propagation test a thermal runaway is initiated using one of the abuse conditions described above and the effect on the neighbouring cells is observed.
However, with manufacturers looking to further increase the energy density of cells and their output electrochemical power, new abuse conditions are emerging. In other words, the limit of the electrochemical system of lithium-ion batteries is almost reached. Results in a recent article2 indicate that a new type of abuse condition, electrochemical abuse, is the underlying mechanism for the emerging causes of battery failure.
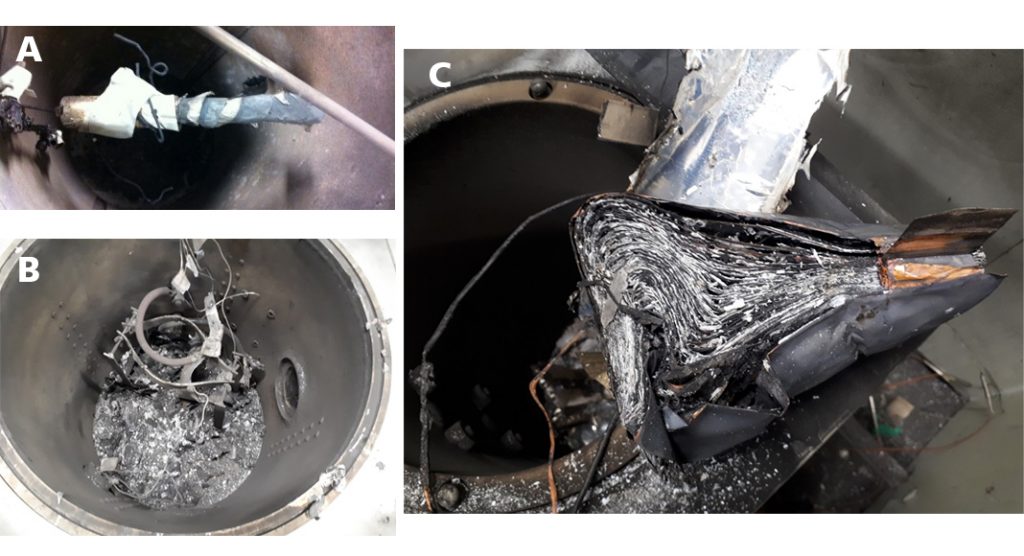
References
- The Innovation Platform – Issue 4, page 102: Innovative calorimetric methods for safer batteries in the renewable energy sector.
- Wensheng Huang, Xuning Feng, Xuebing Han, Weifeng Zhang, and Fachao Jiang, Cell Reports Physical Science 2, 100285, January 20, 2021.