The SIMBA project develops the potential of sodium and sodium-ion battery technology for stationary energy storage applications to support the energy transition, reducing the use of critical materials.
The European Union (EU)-funded SIMBA project, in the frame of HORIZON 2020 (GA No. 963542), brings together 16 partners from European academia and industry in a consortium that aspires to offer an alternative to lithium-ion batteries (LIBs) for stationary energy storage applications.
This occurs in a lapse of time in which the LIB market is mainly saturated by a high request from the quickly expanding electric vehicle (EV) market. The rapid expansion of the lithium-ion battery (LIB) market has led to a surge in metal prices, as indicated by the trends observed in the London Metal Exchange (LME) data.1
However, the adoption of sodium and sodium-ion technology has the potential to alleviate this issue while simultaneously facilitating the integration of renewable energy sources. The transition to a sustainable energy scenario is one of the most significant political measures of the EU to counter climate change. To accommodate the growing proportion of clean energy generated through solar and wind power sources, stationary energy storage will be crucial.
Batteries, as energy storage systems, are vital technologies in the EU’s pursuit of a carbon-neutral society by 2050, representing an essential component in the complete transition to renewable energy sources. The sketch in Fig. 1 represents the ideal scenario with a storage system being the intermediary between different kinds of power plants and end users.
Due to the growing EV market, LIBs are produced at an increasingly large scale, decreasing their production costs and generating new opportunities for their implementation in energy storage at the grid and/or household level. It is expected that, by 2040, the number of EVs will increase by two to three orders of magnitude and stationary storage may reach up to 1300 GWh, compared to 3-4 GWh installed in front-of-the-metre today.2 This raises concerns regarding the future long-term availability and costs of the critical raw materials (cobalt, nickel, lithium and copper) employed in LIBs.
Since LIBs are excellent candidates for the electro-mobility application, the EU still requires innovative technologies for high-performance, reliable, safe, sustainable, and cost-effective batteries to meet the needs of stationary energy storage. Sodium-ion batteries (SIBs) and sodium metal batteries (SMBs) offer the potential to replace the critical materials used in lithium-ion batteries (LIBs) with abundant and sustainable alternatives, paving the way toward greener, more sustainable, low-cost, next-generation energy storage technologies.
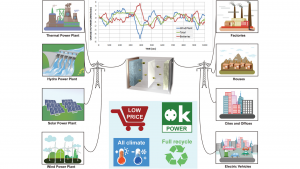
Source: http://www.nrel.gov/docs/fy14osti/59003.pdf
The SIMBA project
The SIMBA project, which started in January 2021, merges together different concepts and aspects related to the development of a new, safe, and low-cost all-solid-state sodium battery technology. It tackles the challenge of reconfiguring the production line of LIBs to accommodate the SIBs while simultaneously developing a recycling strategy.
The project aims to achieve a technology readiness level (TRL) of 5 for a closed-loop concept by the project’s completion, ensuring a final product with optimal functionality. Developing an exploitation strategy beyond the objectives of the SIMBA project is also of utmost importance to elevate the technology readiness level (TRL) further, with a follow-up phase tailed by a market rollout stage.
Careful planning is required, considering various factors such as material innovations, sustainable electrode and cell manufacturing, and enhanced characterisation and comprehension of the electrochemical processes taking place in this groundbreaking battery configuration. The materials and components within SIMBA are state-of-the-art technology, and they are expected to surpass the prototype level.
The ambitious and realistic goal to tackle these challenges has been set by formulating the following objectives:
- Safer batteries using a novel Solid-State Electrolyte (SSE) (TRL3-5) by developing a new class of Single-Ion conducting Polymer Electrolytes (SIPEs) and its production method;
- More durable anodes with a higher energy density by developing materials up to TRL5 using sustainable manufacturing methods;
- Development of ultra-low-cost Prussian White PW) and high energy density layered oxides (P2/O3-type of structural patterns) up to TRL5 as cathode materials;
- Acquiring an in-depth understanding of fundamental mechanisms, including degradation taking place at the Solid-Electrolyte-Interface (SEI) and within the battery components; and
- Upscaling to a highly efficient 12 V, 1 Ah battery module including Battery Management System (BMS) to validate the re-use of materials, recyclability, performance, life cycle analysis (LCA), and potential for further development.
Jointly, these efforts will result in a sodium-based battery demonstrating improved performance, recyclability, and sustainability for a stationary energy storage use-case.
The materials
The conceived storage technology will employ sustainable battery materials, reducing supply risks and restrictions and environmental impact, which are instead currently affecting other technologies, e.g. LIBs.4 For this purpose, biomass-derived hard carbon (HC) and silicon carbonitride ceramics (SiCN) have been selected as anode material candidates for sodium-ion batteries and sodium metal batteries (SMBs), respectively.
Biomass-derived HC anode materials (see Fig. 2a and Fig. 2c) have been prepared with an appropriate bio-precursor, available at a large scale, to ensure scalability of the technology, moderate cost, and elevated sustainability. After screening different carbon sources via pyrolysis, structural characterisation and electrochemical performances, lignosulfonate and spruce sawdust have been selected as precursors for further optimisation in terms of capacity and cycle stability and efficient synthesis conditions.
Ceramics based on SiCNs have been tested for SMBs and presented promising results for a stable and reversible sodium plating empowered by an efficient ceramic matrix. Through various thermal treatments, diverse morphologies and porosities of the SiCN matrix have been successfully generated.
Among them, the SiCN synthesised at 1,000°C has emerged as the most promising option in terms of both plating and insertion capacity, as well as production efforts. Its stabilisation has been obtained by limiting the plated sodium amount. A detailed explanation discussing the influence of the porosity of the ceramic matrix on the electrochemical performance of the SiCN anode material can be found in a SIMBA publication.5
The SIMBA project is examining layered oxides and Prussian Blue Analogues (PBAs) as cathode materials. This battery component is predominantly affected by rising raw material costs and ethical/environmental concerns in LIBs. Therefore, special focus has been dedicated to the Prussian White (PW) system (see Fi. 2b and Fig. 2d), which due to its composition of sodium, iron, nitrogen, and carbon, represents a cost-effective and environmentally-sustainable option for cathode materials. Recent results have shown that PW half-cells maintain 80% capacity retention after more than 1,000 cycles.
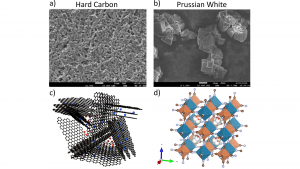
SIMBA also binds together the challenges of moving from Li to sodium-ion (Na-ion) technology with the transition from a liquid to a solid-state electrolyte (SSE) for an all-solid-state battery. The incorporation of a single-ion conducting polymer electrolyte (SIPE)in the sodium full-cell configuration is an ambitious target that would drastically improve the safety of the battery.
Recycling
All the material and product development processes are shadowed by an innovative study on the recycling process, which focuses on the recyclability and reuse of the cells produced within SIMBA.
Cell tear-down procedures are explored for the mitigation of contaminants in waste streams, as well as techniques for direct recycling. This implies a deep analysis of the design for disassembly, separation, and recycling as well as shredding processes and post-processing optimisation for materials extraction (see in Fig. 3 an overview of the recycling procedures). Fundamental processes include mechanical opening under an inert atmosphere, mechanical refining, and sieving of the fractions.
A pioneering sheet delamination technique to successfully separate the electrode materials from other cell components using a cryo-delamination approach has been implemented for a more efficient reclamation of the black mass from current collectors. Additional efforts are dedicated to the re-sodiation of the recovered PW cathode material for remanufacturing and reuse.
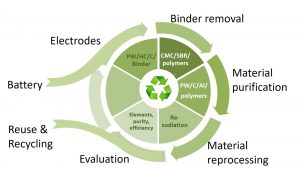
Validation
The SIMBA project partners have formulated use cases with key performance indicators (KPI) to validate the final technology by performing a comprehensive analysis of the various stationary energy storage applications suitable for SIBs, as well as assessing the specific requirements for these implementations.
In addition, they also established a comprehensive framework outlining the essential requirements and parameters that a battery system designed for energy storage applications must meet.
Examples of energy-optimised systems include residential setups in which batteries are utilised for purposes such as maximising self-consumption, managing peak demand, and facilitating load shifting, all of which occur over extended time periods.
To reach the main goal of developing highly cost-effective, safe, all-solid-state-batteries with sodium as a mobile ionic charge carrier for stationary energy storage applications, the SIMBA technology will be validated for both energy and power demanding applications, matching the requirements of three selected specific use cases:
• Telecom power systems;
• Batteries for renewable photovoltaic and wind applications, including small-scale household batteries; and
• DC power solutions for generation, transmission and distribution (frequency regulation).
The SIMBA project consortium
One of the most significant challenges in the development of sodium-ion batteries and SMBs, compared to LIBs, is the larger ionic radius of 1.02 Å of the Na+ cation compared to 0.76 Å radius of the Li+ cation. This feature influences the local structure of the cation and its dynamics.
A thorough understanding of the microscopic level is crucial for the rational, knowledge-driven design of next-generation sodium-based batteries. This profound level of understanding can be gained only by a very close collaboration between advanced analytical techniques and detailed quantum chemical modelling of the local structure and the electrochemical and transport processes inside the material.
The close collaboration happens between four levels: solid-state ex-situ and in-situ measurements (e.g. NMR, XRD, single-particle measurement); atomistic modelling (DFT calculations); mesoscopic modelling (e.g. of ionic transportation, characterisation); and Equivalent Circuit Model level (FHG), electrochemical properties. The last level will be based on the outcomes of the previous levels, and for this strong interconnection, SIMBA relies on co-operation within the academic-led consortium (five universities and four research institutes) in collaboration with industry leaders renowned for their expertise in battery materials.
These include:
- Technische Universität Darmstadt (TUDa), covering the scientific management and co-ordination of the SIMBA project, the ion transport and interface properties, and material development (SiCN);
- Uppsala Universitet (UU), dealing with fundamental research on the material development and characterisation;
- The University of Birmingham (UBham), responsible for the circular economy cell and material lifecycle design;
- The University of Warwick (WMG), responsible for the electrode and cell assembly and cell manufacturing;
- Karlsruher Institut Für Technologie (KIT), leading the lab-scale material and process development, focusing on the development of the polymer electrolyte and LCA analysis;
Commissariat À L’énergie Atomique Et Aux Énergies Alternatives (CEA), responsible for the use case analysis, thermal and hazard cell testing and validation; - Institutt for Energiteknikk (IFE), dealing with the development and manufacturing of the biomass-derived HC anode;
- Ustav Anorganickej Chemie Slovenska Akademia Vied (Institute of Inorganic Chemistry, Slovak Academy of Sciences (SAS)), sharing the activity on the material development (porous ceramics anode); and
- Fraunhofer Institut Für Solare Energiesysteme, responsible for the specification of KPIs and use cases, including reuse and recycling, and BMS and sensor development and integration.
The industrial support, from the material’s availability via cells assessment to the facilities to produce and upscale, is provided by:
- Johnson Matthey PLC (JM), partner of the consortium until December 2022. The respective research on cathode materials is continued under the supervision of TUDa;
- Elkem AS, manufacturer and supplier of anode materials;
- YUNASKO-UKRAINE LLC, responsible for the cell performance testing, module design, validation and demonstration;
- Saft, dealing with the validation of the technology specification, the final usage specifications and the cell stability assessments;
- Altris AB, manufacturer and supplier of PW cathode material;
- TES Recupyl SAS, reclamation and reuse of battery materials; and
- Uniresearch BV, leading the dissemination, exploitation, communication, and data management.
Additionally, the project is supported by an external advisory board consisting of energy distributors, energy storage system producers, and research institutes.
Outlook
The following milestones have been achieved in the SIMBA project’s first two years of activity:
- Key performance indicators definition;
- Generation of the SIMBA Baseline Cell has been successfully achieved with 1 Ah A7 multilayer pouch cells being produced and tested after eight months from the start of the project;
- Setup of in-situ solid-state NMR has been established after 12 months;
- A cryo-delamination technique has been developed;
- Material optimisation for the SIPE up-scaled production; and
- Selection of the best performance materials for the SIMBA cell. The promising achievements obtained up to July 2023 clearly indicate that the formation of a production line for SIMBA battery cells can be considered in future.
References
- https://www.lme.com/en/Metals/EV, (Accessed June 29, 2023). (n.d.).
- I. Tsiropoulos, D. Tarvydas, N. Lebedeva, Li-ion batteries for mobility and stationary storage applications : scenarios for costs and market growth, Publications Office, European Commission, Joint Research Centre, 2018. https://op.europa.eu/en/publication-detail/-/publication/e65c072a-f389-11e8-9982-01aa75ed71a1/language-en.
- T. Liu, Y. Zhang, Z. Jiang, X. Zeng, J. Ji, Z. Li, X. Gao, M. Sun, Z. Lin, M. Ling, J. Zheng, C. Liang, Exploring competitive features of stationary sodium ion batteries for electrochemical energy storage, Energy Environ. Sci. 12 (2019) 1512–1533. https://doi.org/10.1039/c8ee03727b.
- Commission staff working document report on raw materials for battery applications, https://www.innoenergy.com/, (Accessed June 29, 2023). (n.d.).
- M. Melzi d’Eril, M. Joanna Graczyk-Zajac, R. Riedel, On the Reversible Sodium Plating/stripping Reaction in Porous SiCN(O) Ceramic: A Feasibility Study, Batter. Supercaps. 6 (2023).
https://doi.org/10.1002/batt.202200491.
This project receives funding from the European Union’s Horizon 2020 research and innovation programme under Grant Agreement No. 963542.
Please note, this article will also appear in the fifteenth edition of our quarterly publication.