Phoenix Tailings is working to accelerate the US rare earth supply chain.
2022 was an important year for the rare earth supply chain. There were major advances in mining and processing, both in the US and throughout the world.
Nick Myers, CEO and Co-founder of Phoenix Tailings, said: “All over the globe, people are waking up to the reality that the rare earth status quo is unsustainable.
“The ongoing electrification revolution means that global demand for rare earth metals will skyrocket. The same old ways of doing business will not be able to meet our needs. The question is how, not if, the sector will expand.”
The increasing demand for rare earths
The independent research firm Adamas Intelligence predicts that global demand will triple, increasing to $46bn in 2035 from $15bn in 2022. So it is no surprise that, last year, there was major investment and progress in every part of the rare earth supply chain.
The US Mountain Pass mine expanded operations and many companies are exploring sites for new mines. Africa also experienced a flurry of mining activity and exploration, with a mine in Malawi announcing it will commence production in 2025 and a British company buying a major stake in a Namibian rare earth mine.
Dr Tomás Villalón Jr, CTO and Co-founder of Phoenix Tailings, said: “Mining and exploration have been getting most of the headlines, but they’re only one part of the rare earth supply chain.
“Until you have usable metal for manufacturing, not just ore dug out of the ground, there’s no actual progress. The world needs an ‘all-of-the-above’ approach to getting the rare earths we’re going to need, and that’s why I’m proud to have founded the first-ever clean metal processing company.”
Establishing a US rare earth supply chain
Phoenix Tailings is the first company to actually process usable rare earth metals here in the US and work towards a steady rare earth supply chain.
“In the 1980s, earth metal processing left the United States and Western Europe, relocating to developing countries with lower labour costs and fewer environmental regulations,” said Myers.
“We can bring a rare earth supply chain back to the United States because our novel process is orders of magnitude more effective than the traditional process, without any of the environmental harms that require lengthy permitting and expensive remediation.”
Currently, Phoenix Tailings is producing neodymium (Nd,) and will shortly expand dysprosium (Dy), terbium (Tb), and ferro-dysprosium alloy (DyFe.) These were selected for initial production because of the immediate commercial demand. Phoenix Tailings’ technology is modular, so they plan to expand production to other rare earths, battery group metals such as nickel and cobalt, and precious metals like gold.
Phoenix Tailings was featured in an earlier issue of The Innovation Platform. If you didn’t read it, the company’s founding story is a little different than most startups. Instead of beginning with technology and trying to commercialise it, Phoenix Tailings built technology to solve the problem of sustainable, economically viable rare earth metal production.
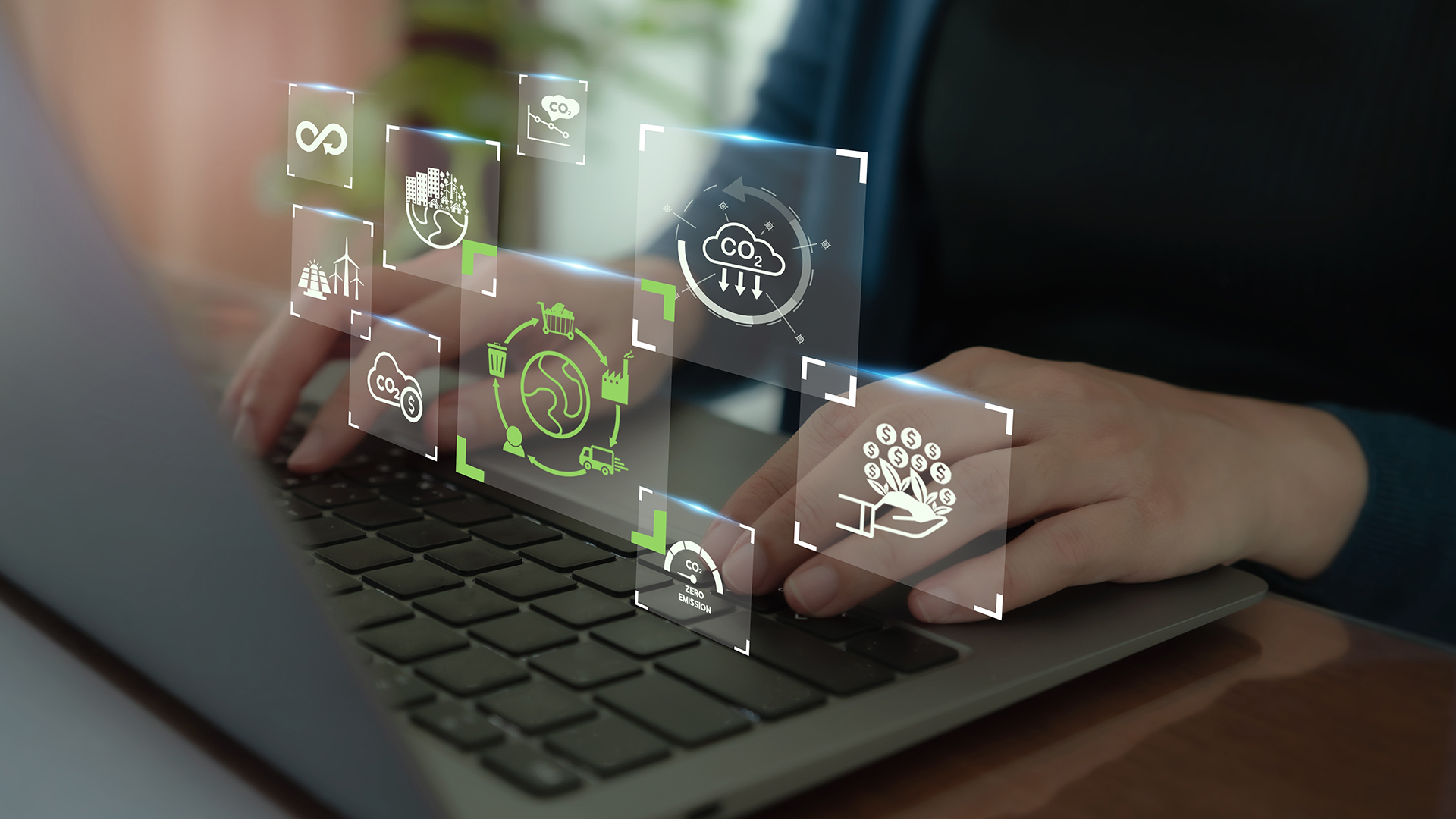
The company was started in 2018 after a fateful conversation by Nick Myers and Dr Tomás Villalón Jr. They were talking about one of the world’s biggest problems – mining waste and the resulting resource scarcity. Every year the mining industry creates over 200 billion tonnes of waste, known as tailings, not because it is not usable, but because it did not have the specific type of metal the mining company wanted. At the same time, wars are fought over natural resources, and those resources have never been in more demand.
“We knew that the way mining had operated for the last 150 years could not be the way it operated for the next 150 years,” said Villalón. With mines running empty, the scramble for the remaining natural resources would increase international conflict and even lead to outright warfare.
Traditional rare earth metal processing was just as troubling. It produces significant carbon emissions and toxic by-products. The traditional rare earth process stood in the way of the clean future promised by electrification since an established rare earth supply chain is essential for all electrified products.
“There was a better way, and we set out to find it,” said Myers.
The evolution of Phoenix Tailings
After recruiting co-founders Anthony Balladon and Michelle Chao, Phoenix Tailings officially started. Within only a few months, the team built a prototype in a Cambridge backyard that produced a small amount of material from tailings.
A year later, Nick left his job to devote himself full-time to Phoenix Tailings. In 2020, the company raised a $1.8m seed round. In 2021, it raised $12m from Series A. The company has also received over $2.4m in government grant funding from the National Science Foundation, the Department of Defense, and ARPA-E.
Now, Phoenix Tailings is thriving. It has 18 employees working out of an office in Woburn, Massachusetts, and a production facility nearby. In addition to the co-founders, the company employs top talent in engineering, operations, chemistry, and in many other specialities. This year, the company signed its first commercial sales agreement. Recently, it entered into a lease option on a tailings site in New York State.
The tailing site represents exactly how Phoenix Tailings wants to change metal production and the rare earth supply chain for the better. Before the mine closed, it was the centre of the county’s economy and created thousands of jobs. In addition to the jobs directly created in mining, the mine supported many small businesses like bars and restaurants.
Reopening the mine as a tailings site will not only get Phoenix Tailings a high-quality, reliable feedstock for producing rare earth metals, it will revitalise the county’s economy and the rare earth supply chain. Specifically, Phoenix Tailings is proud of creating good-paying jobs that do not require a four-year college degree, which have become increasingly scarce due to outsourcing and automation.
Future plans
Phoenix Tailings is currently scaling up production by building a long-term commercial facility. That facility will produce a portfolio of REMs, including neodymium-praseodymium (NdPr), dysprosium (Dy), dysprosium iron (DyFe), and terbium (Tb). The current commercial pilot facility has a ten-tonne-per-year capacity, while the long-term facility will produce 5,000 tonnes. This means the long-term facility will be crucial to meeting the rising global demand for rare earth metals, and ease the pressure on the rare earth supply chain.
The proprietary novel process is the key to Phoenix Tailings’ economic viability. Using selective halogenation to produce oxides and a mixed halide salt reduction to produce metals is not just more sustainable than the traditional mining process — it is also more efficient, using 35-45% less energy.
Phoenix Tailings’ process is also modular. It can adapt to a wide array of feedstocks and, once it is fully operational, produce a large number of end products. This protects Phoenix Tailings from commodity risk since they can change production to reflect market demands. For example, if the price of rare earth metals falls rapidly, the company can focus on producing battery group metals, precious metals, and iron oxide products. Then, when prices revert to the mean, they can pivot back to rare earths.
Finally, because it actively cleans up mining waste, Phoenix Tailings does not encounter the regulatory hurdles of traditional mining or metal processing companies. Its process was specifically designed to operate in the countries with the strictest environmental regulations, such as Australia and New Zealand. The company is currently processing metal in Massachusetts and easily received state and federal approval. The initial tailings site is located on land run by the National Park Service (NPS), and the Phoenix Tailings process does not require any additional permitting to operate in an NPS site.
“The demand for rare earth metals and other critical materials is only going to increase,” said Myers.
“I’m thrilled that Phoenix Tailings is ready to meet the challenges ahead for the rare earth supply chain, ensuring that we build our clean energy future with equally clean components.”
Please note, this article will also appear in the fourteenth edition of our quarterly publication.