Helium is a noble gas most commonly known for its use in balloon inflation. However, the element has more to offer than just lifting balloons – the applications of helium often surprise many.
From welding and metallurgy to cooling superconducting magnets, helium applications play an essential role in various processes across industries. Innovation News Network explores how helium is used in industrial processes and explains why its properties make it such a valuable resource.
What makes helium so special? Well, the answer lies in its unique properties. Helium is an element found on the periodic table with a chemical symbol of He and an atomic number of two. Its physical properties are quite distinct from other elements due to its lightweight, low-density, and colourless nature. On top of that, it has exceptional chemical properties, including extremely high electronegativity values and very low reactivity to most materials.
Its atomic structure consists of two protons and two neutrons arranged in a closed shell configuration, giving it great stability under different conditions. Because of these characteristics, helium can be used for many industrial applications, such as cryogenics and pressurisation systems.
The history of helium applications
Helium applications have a diverse and surprising history. The use of helium for industrial purposes dates back to the early 1900s when various inventors began utilising its unique properties for a range of medical applications. Today, multiple industries rely on this rare element for their production processes.
From metallurgy to medical imaging and semiconductor manufacturing, there are numerous areas where this versatile element proves useful. Its ability to remain gaseous, even at extremely cold temperatures, makes it suitable for cryogenic applications while providing excellent insulation against heat transfer between objects. While helium may be considered a light-hearted element of recreational activities, its importance in the industry cannot be overstated – making it one of the most valuable resources today.
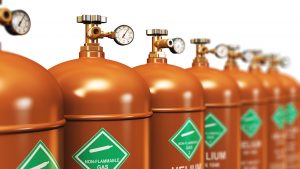
Helium uses: Cooling and lubrication
Helium has been called the elixir of life, but it is also an essential industrial component. Its ability to cool and lubricate is invaluable in many applications, from manufacturing to medical technology. To understand the role of helium applications in these industries, we must first look at its unique properties when used as a coolant or lubricant.
The cooling effects of helium make it ideal for use in cryogenic processes, such as liquefaction and refrigeration. It can be used on large-scale systems like those found in power plants and small-scale equipment like laboratory freezers. Additionally, liquid helium is often employed to manufacture semiconductors and other electronic components due to its low boiling point and high thermal conductivity.
In addition to cooling uses, Helium’s lack of viscosity makes it suitable for certain types of lubrication, such as ‘helicooling lubrication’. This process involves spraying tiny droplets onto parts subject to friction or wear. This is especially useful for aircraft engines where traditional oils may not be viable options due to their tendency to thicken under pressure or temperature changes during flight operations. Furthermore, helium applications do not require regular maintenance since the element only needs recharging with fresh supplies intermittently, making it a particularly cost-effective solution for businesses looking for reliable performance over extended periods.
These two areas alone demonstrate the versatility and importance of helium applications in the industry today, helping maintain efficiency across numerous sectors without compromising safety or reliability standards set by regulatory bodies worldwide. With further technological advancements expected in the years ahead, there could well be other innovative ways to harness this inert gas’ remarkable capabilities yet again.
Manufacturing processes
Due to its unique properties, helium applications have become valuable in many manufacturing processes, including the automotive industry. Helium’s ability to remain inert and non-flammable and its low boiling point is advantageous over other traditionally used gases.
It is beneficial when machining metals and alloys because it can help reduce material oxidation while remaining safe for operators at high temperatures. Helium applications can also be an effective cooling agent during welding operations, allowing welders to work at higher speeds without damaging their materials.
In addition, helium can be used in leak detection systems requiring pressure readings accuracy. This helps manufacturers identify potential problems with equipment before they occur and allows them to address any issues quickly and effectively. Furthermore, helium offers superior performance compared to conventional air systems due to its small size molecules, meaning more precise measurements are possible.
Helium applications have proven to be versatile tools in modern manufacturing processes. By reducing costs associated with traditional tools such as nitrogen or argon gas, companies can make their operations more efficient and profitable by utilising this noble gas’ unique characteristics. As businesses continue to adopt new technologies, using helium will likely become even more commonplace in industrial production settings across the globe.
Welding and cutting technologies
Helium is an elemental gas with various industrial applications, one being in welding and cutting technologies. Its presence has become essential to manufacturing products and objects that require precise cuts or seams. Applications of helium bridge the gap between human creativity and the physical world, providing a platform for projects of all shapes and sizes to be brought to fruition.
Many industries use gas welding torches, including metal fabrication and construction engineering. Helium applications are commonly used in these processes due to their low ignition temperature, which increases safety while minimising risk when working with hot equipment. Gas-cutting techniques also utilise this element as its non-reactive nature allows even heat distribution through materials such as metals without generating sparks. This can be seen in arc welding, where a consumable electrode is heated by electric current, creating molten pools fused together using inert gases like helium to protect against oxidation.
Helium also plays an essential role in modern laser cutting technology; allowing light waves to pass through the material without dispersing too much energy along the way results in cleaner, more accurate results than other methods may produce unassisted. The process involves moving nozzles emitting both abrasive particles and pressurised air, providing additional cooling capacity during operation. In addition, high-powered lasers now employ helium welding techniques offering greater impact strength than traditional welds making them better suited for use on thicker materials or within confined spaces where access may not otherwise be possible.
How can helium aid deep-sea exploration?
Helium applications have numerous benefits for deep-sea exploration, making industrial helium an important supply to consider. The gas is non-flammable and far less dense than air, allowing it to be used as a buoyant agent when exploring the depths of oceans and other bodies of water.
Additionally, its low freezing temperature makes helium an ideal gas for cooling underwater equipment. This helps reduce operational costs since long dives require expensive heating systems that may need frequent repairs due to severe pressure changes in certain areas.
Furthermore, helium’s inert properties make it safe for use with sensitive electronic components found on underwater vessels and robotic submarines. Without worrying about oxygen or nitrogen corroding these parts, manufacturers can confidently build reliable instruments that can explore the ocean without fear of damage or malfunctioning under high pressure. Ultimately, helium applications allow researchers access to new data previously unattainable by traditional means.
Nuclear reactors
Though it may come as a surprise, helium has several industrial applications in nuclear reactors. Understanding how and why helium applications can be used in such a setting is important. Nuclear reactors need to cool the reactor core and prevent radiation from escaping into the atmosphere; helium’s properties make it an ideal choice for achieving these goals.
Helium’s high thermal conductivity means it can efficiently transfer heat away from the core of a nuclear reactor by creating convection currents. This allows reactor operators to maintain safe temperatures within its walls without significant risk of damage or meltdown.
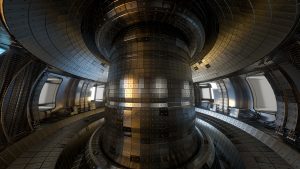
Moreover, helium’s low opacity makes it difficult for radiation particles generated inside the reactor to escape outwards, allowing control over safety levels outside the facility. Studies have shown that compared with other gases commonly used in similar applications, helium provides superior shielding against radiative emissions, minimising radiation exposure risks.
Therefore, it is clear how helium applications play an important role in many industrial applications related to nuclear technology. Its unique qualities render it highly efficient as a cooling agent and minimising unwanted radiation leakage outside containment facilities. By taking advantage of all that helium offers, industries operating nuclear power plants can ensure maximum safety for onsite personnel and those living near them with minimal environmental impact due to radioactive release.
How can helium applications help with leak detection?
Helium is a versatile element and has found many applications in various industries. One of these is its utilisation as an effective leak detector that can detect even the smallest leaks in industrial systems, such as those for refrigeration and air conditioning units.
The leak detection process, coupled with helium applications, involves introducing a small amount of the gas into the tested system and using special equipment to measure any resulting pressure drop or rise. If there is a decrease in pressure within the system, this indicates that there may be a leak present. This method of detecting leaks is much more accurate than traditional methods, which rely on visual inspection alone.
In addition to its accuracy and speed, one of the major advantages of utilising helium leak detectors is their non-toxicity, making them safe to use in hazardous areas or situations where other forms of testing are not possible. However, they have some disadvantages, including cost and difficulty in operation; therefore, they should only be used by experienced personnel who understand how to operate the equipment properly.
Overall, leak detectors paired with helium applications have become invaluable tools for industries worldwide due to their precision, safety, and affordability compared to alternative testing procedures. With proper training and understanding of how best to utilise them, companies can ensure reliable results from their tests every time.
Safety precautions must be taken when handling helium
With its vast range of applications, it is important to take safety precautions when handling helium. The most important question is: how can we ensure this versatile gas is dealt with and stored safely?
To begin with, it is essential to be aware of the specific instructions for handling helium to prevent accidents or injuries. When storing helium, several guidelines must be followed, including ensuring that containers are sealed tightly at all times, avoiding potential combustible materials around the cylinder valves and keeping them away from open flames or sources of heat. Additionally, proper ventilation should also be considered, and sufficient lighting near the area where the helium will be used.
Furthermore, safety regulations should always be followed when handling helium, such as wearing appropriate protective gear like gloves and goggles while transporting cylinders and using specialised tools for opening valves on pressurised tanks instead of relying solely on manual force. It is also highly recommended to regularly inspect cylinders for signs of damage or leakage before use and store them upright in an isolated area away from other chemical compounds, which may cause hazardous reactions if mixed with helium.
Finally, users need to check local laws regarding the disposal of empty containers and ensure they follow the necessary rules accordingly.
The environmental impact of helium applications
The application of helium in these industries has the potential to cause several environmental impacts. The first, and most concerning, is toxic emissions. Helium production emits carbon dioxide into the atmosphere, which can contribute to global warming and ozone depletion. In addition, specific manufacturing processes that require helium as a gas input may also release volatile organic compounds (VOCs) into the environment. These VOCs are known to be toxic pollutants that can lead to atmospheric pollution if not adequately regulated or managed.
Another concern related to helium applications and usage is the finite nature of this noble gas. As a non-renewable resource primarily produced from natural gas extraction sites with limited reserves, industry leaders must ensure efficient management practices when using this valuable material in their operations. Additionally, organisations must reduce waste and conserve resources associated with helium processing and distribution networks.
Given these considerations, there is an urgent need for business owners and operators to become more aware of how they’re using helium and assessing any potential impacts on the environment. To help address this issue, companies should develop strategies such as reusing materials where possible or investing in renewable energy sources instead of relying solely on traditional methods like fossil fuels or nuclear power plants. This would help minimise negative environmental effects while ensuring the sustainability of supply over time.
Cost considerations of helium supply
Helium is an increasingly important element, and it is clear that several industries that require helium applications due to its unique properties. However, its supply and cost can determine the success of any venture. Knowing the factors which affect helium’s availability and price is essential for industrial helium applications.
Storage capacity, transportation requirements, and safety protocols must all be considered. In addition, many governments impose regulations on selling and using helium, which can add additional challenges within the supply chain based on international trading agreements between countries. Considering all these factors helps ensure a successful acquisition operation involving helium. With proper planning, organisations could find themselves able to secure enough helium at reasonable costs or within desired timelines. Therefore, understanding how each factor affects price and availability should be part of any strategy to deploy this critical element in industry-specific projects successfully.
Regulations must be considered when distributing this element
The unknown capabilities of helium applications have provided a wealth of surprises. From its use in medical equipment to the possibilities it offers for industrial applications, helium has become an invaluable resource capable of producing outcomes far beyond what was initially expected. However, regulations concerning its distribution and how they influence the availability and cost of helium supply must be taken into account.
Helium distribution is governed by strict laws that dictate where and when individuals can obtain the gas. The most common source for acquiring helium is licensed vendors, who sell it as part of their business operations. These distributors must abide by certain restrictions imposed by government agencies like the Environmental Protection Agency (EPA). For example, some states require only approved suppliers to transport or distribute liquid helium within their borders. As such, these regulations play a major role in determining who has access to this valuable commodity and affect the overall price charged for its purchase.
In addition to state-level legislation governing helium distribution, there are also federal standards put in place by organisations such as the United States Department of Transportation (DOT), which oversees interstate commerce involving hazardous materials such as liquid helium. These rules impose additional requirements on companies transporting helium across state lines while setting forth guidelines regarding storage and handling protocols necessary for safe shipping practices. By adhering to these safety regulations, vendors ensure that consumers receive quality products at reasonable prices without compromising public health or environmental concerns posed by large shipments of potentially dangerous goods.
Understanding how various regulatory bodies impact the production and sale of helium shows why costs associated with obtaining this essential gas vary so widely between different parts of the world. Supply restrictions stemming from governmental policies combined with an ever-increasing demand create a unique market dynamic – where prices fluctuate depending on geographical location as well as local economic conditions – making predicting future trends difficult yet equally important if a company hopes to remain competitive regarding pricing structures surrounding a product subject to frequent changes in value. Therefore, creating a pricing strategy that is flexible and responsive to the changing market of helium applications is essential.
How can industries secure an adequate supply of helium?
When it comes to securing an adequate supply of helium and maintaining a balanced supply chain, several sources and strategies are available. The main option is procuring natural gas containing helium in its composition. This could be done through a third-party supplier or self-production by extracting it from underground reserves. Existing stocks can also be purchased from other suppliers or governments that have built up large inventories over time.
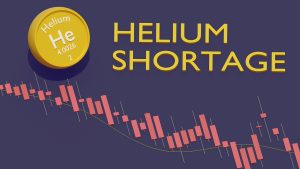
The cost of procuring an adequate amount of helium depends on the chosen source, market fluctuations, and availability. Organisations must stay informed about current prices and trends in global markets to secure a cost-effective supply. They should also consider alternative methods such as developing more efficient extraction techniques, recycling used helium, and obtaining secondary supplies from waste streams produced during oil production processes.
Organisations seeking to procure an adequate supply of helium must consider all these factors when planning their procurement strategy to ensure reliable access at reasonable costs for their operations. By being aware of different options, staying informed about market conditions, and taking advantage of innovative technologies, organisations can increase their chances of success in securing an adequate and cost-effective supply of helium applications for different industries.