Jacob Bouchard’s proposal for a Low-Earth Orbit Scrapyard aims to tackle space debris by recycling and repairing materials.
This month, we take a different tack in relation to promoting ideas relating to space sustainability and a circular economy by introducing a concept posed by Jacob Bouchard, a citizen scientist from the USA – “A Proposal for a Low-Earth Orbit Scrapyard, Repair, Manufacturing and Recycling Station and Space Debris Removal Programme.”
The ‘Space Enterprise’ is entrenched in linear economics, which has created a landfill, and the space version of the landfill, the result of take–make–waste, is debris. Despite an ever-growing dialogue on space sustainability, there is little evidence of action to change from a single-use mentality, and Jacob’s concept could help kickstart the development of a truly circular economy for space.
Our ethos at 3S Northumbria is to keep space for everyone and ensure the long-term sustainability of space’s benefits. It will take a concerted collective effort to find a solution that works for everyone, and we are here to find the solution(s) that do not create additional future problems. At 3S Northumbria, we are open-minded and eager to collaborate with anyone, no matter how out-of-the-box the idea may seem.
An overview of Bouchard’s project
Bouchard’s project has the singular objective of solving the wicked problem of space debris by not only cleaning up space but also reusing, repairing, and recycling materials that otherwise would be wasted. The hope is that this project helps develop and deploy recycling and reuse technologies with the potential for commercialisation in a terrestrial [or lunar] setting.
The proposal covers the entire scope of space recycling. The first project is a stand-alone, uncrewed robotic drydock to handle satellite repair, servicing, disassembly, construction, preliminary sorting, and cataloguing space debris. The industrial elements will fly in subsequent launches, which open the door for space recycling and manufacturing. In addition to the station, there are specifications for a spaceship fleet specialising in capturing and moving space junk.
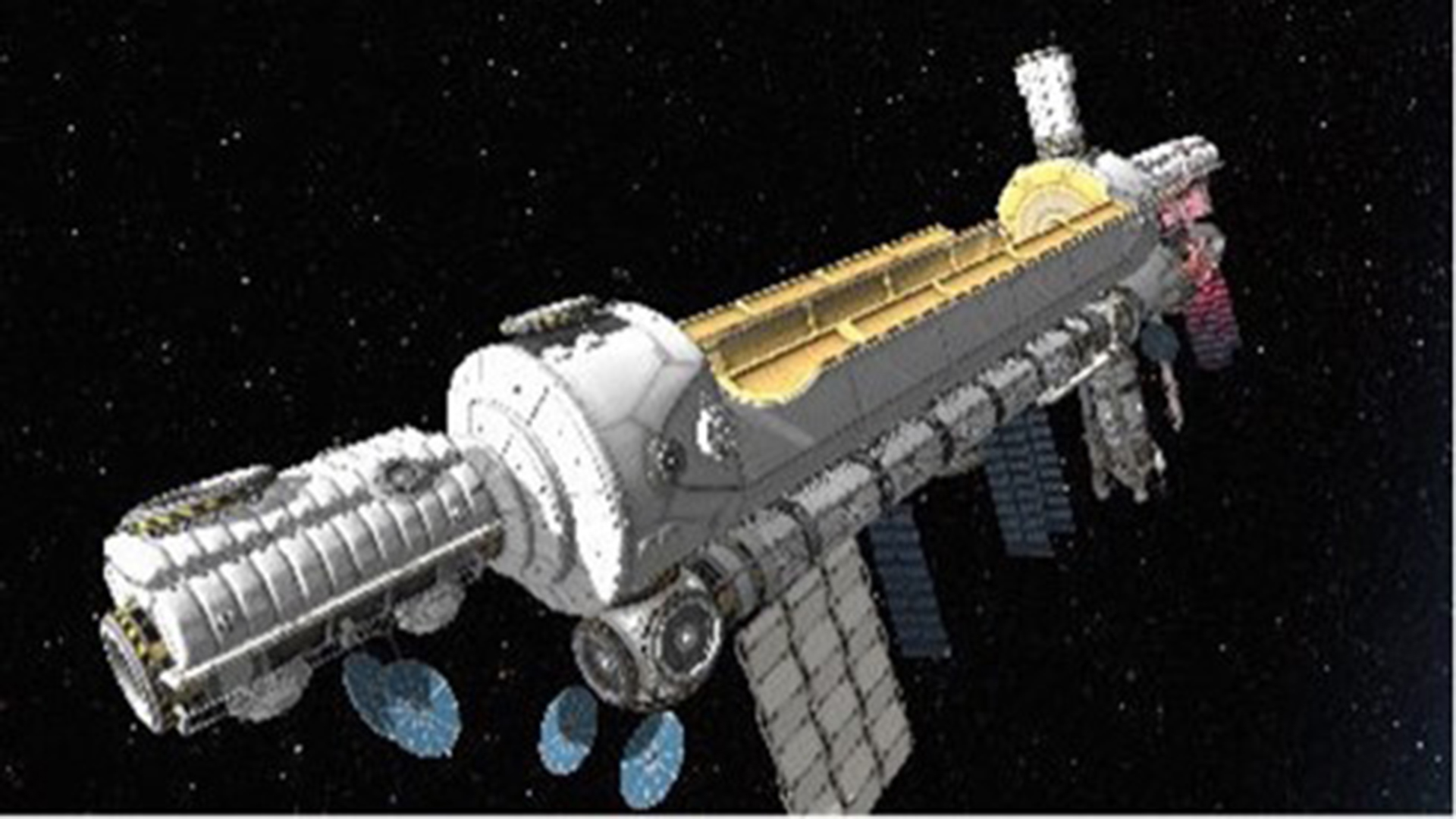
The research in this project will benefit many terrestrial industries and help stimulate green technologies with a strong focus on recycling. These developments would reinvigorate local manufacturing sectors, create jobs, create economic resilience, reduce waste for raw materials and manufactured goods, and reduce the need for international shipping.
The space debris challenge
There are reported to be more than 750,000 pieces of space debris located in orbit, with almost 40,000 of those objects greater than 10cm in size [coffee cup-sized].
Contrary to popular belief, objects do naturally decay/deorbit as there is some atmospheric drag. However, emerging evidence points to these re-entering satellites depositing harmful ozone in the upper atmosphere. The further you go into space, the lower the particle density of the atmosphere and the more time objects take to fall back to the planet.
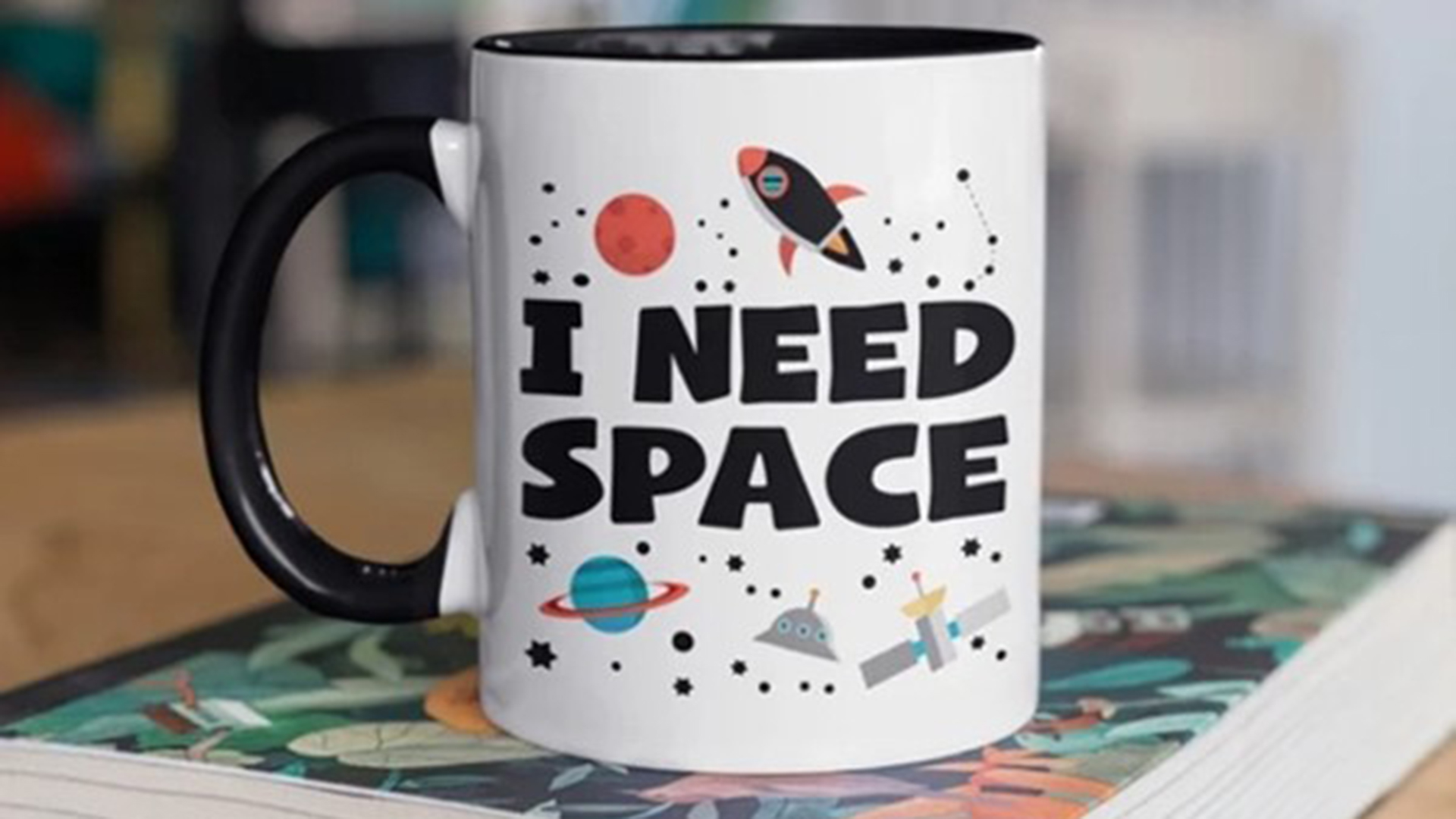
larger
Some objects in low Earth orbit will de-orbit within 20 years; however, most LEO objects take closer to 60 years, but once they are more than 750 km away, it will take more than 100 years.
Everything in space is travelling extremely fast. The lower an object’s orbit, the faster it moves.
For instance, the ISS moves at 28,000km per hour, and the Hubble moves at 27,300km per hour in a slightly higher orbit. Collisions at speeds this fast are catastrophic. A pin can strike with the force of a dynamite stick. Every collision creates the possibility of several more collisions.
According to astrophysicist and former NASA scientist Donald Kessler, if we reach a critical mass of space debris, the collisions can rapidly cascade, potentially destroying most active satellites and everything else in low Earth orbit within a short timeframe.
Salvaging spacecraft
In this proposal, there are specifications for every existing servicing or deorbiting spacecraft, as well as plans for several more craft designed for specific roles. Some are designed to move large rocket boosters efficiently. One type of salvage spacecraft is built on-site.
There are also current and future construction vehicles, some ideas for small debris collection, and other miscellaneous spacecraft. Northrop Grumman’s MEV (Mission Extension Vehicle) is the first and most likely candidate for salvage operations. It is currently the only operational service vehicle. It has been tested and used in space on a few missions and works for this project. Its limited design is built for one purpose. It moves a satellite from one position to another position, extending its life in orbit. However, we have provided a wide array of potential spacecraft options for any situation.
Many of the salvage spacecraft mentioned in this proposal, including the MEV, use multi-directional ion thrusters, sometimes with a gimbal of 180 degrees. The multi-directionality of the thrusters removes the need for traditional monopropellants for relative proximity operations (RPO). The thrusters use noble gases such as Xenon and Krypton for fuel instead of the more traditional hypergolic fuels.
While ion thrusters have a low thrust value, their specific impulse allows for a five to ten times greater fuel efficiency. Otherwise, the refuel launch cost based on the rocket equation would make salvage operations economically unfeasible.
Space station solution
The space station design and launch plan are divided into two parts: The first is the robotics servicing bay, which can operate stand-alone. The second part focuses on the station’s industrial elements.
The plan is to build the robotics bay from a salvaged rocket booster, preferably a Saturn 5 or IB second stage. This ‘Dry lab – Drydock’ concept allows maximum workspace without a heavy and potentially unwieldy launch. The plan is based on the early concepts of Skylab from Werner Von Braun, where a Saturn 5 rocket booster was to be converted into a human-occupied ‘wet lab.’ Now that they exist again, there is an alternate plan to orbit the drydock with a heavy-lift rocket.
The servicing module features a bay door as seen on the space shuttle, a robotic arm for moving salvage into the work bay, and robotic workers such as JAXA’s GITAI or Boston Dynamics Atlas. These right-stuff robots are equipped with several specialised workstations. There is a workstation for cataloguing inventory, a testing station, one for working with hazardous materials, one for cleaning paint and coatings removal, another for working with small things such as electronics, a heavy workstation, A finishing station, and standard assembly and disassembly workstations.
Powder, parts, and materials are transported around the station using pneumatic tubes and pods. The pods are also used for storage. There are several advantages to this sort of system. It is easy to maintain, fast, reliable, and makes inventory easy to track. The second part of the proposal focuses on the more industrial elements of the station, such as the recycling and manufacturing facility. This facility can sort, grind, and smelt materials into powder feedstock for the additive manufacturing process using a 3D printer.
The current station specifications aim to reclaim or recycle 0.86 tons of materials in space per day. Standard facilities on Earth recycle as much as 33,000 tons of material daily. We are hoping to make a much more compact system. Some components could be blender-sized, toaster oven-sized, or Peppermill-sized with room to expand in the future. 0.86 tons would give a 100% or more return on investment within 20 years based on the cost per kilogramme to launch.
Comprehensive recycling processes
There are three types of recycling processes. Chemical, thermal, and mechanical. This project excludes the chemical process as it would be cost-prohibitive unless a closed-loop chemical cleaning process is worked out. It uses the thermal process sparingly, as there is no convection cooling in a vacuum. Instead, it focuses on the mechanical process. Aluminium and Polymer (plastic) are the cornerstones of our manufacturing process. Aluminium and high-quality plastics can be recycled using a strictly mechanical process involving shredding. The basic idea is to grind down materials into powder and then use the powder as feedstock for a 3D-printed additive manufacturing process.
The recycling process of scanning, cleaning, indexing, disassembly, and sorting will provide parts for reuse and manufacturing. A dual process that sorts whole parts for reuse, whilst parts for ‘shredding and smelting’, can become the core additive for 3D printing.
The results will be replacement parts for broken satellites to fulfil servicing contracts. The aim would be to make specific components and spacecraft for servicing and recycling on-site and things we use in the process, including the transport pods, the in-house retrieval spacecraft, CubeSats, and other simple satellites. We can build bigger and more complex things as we improve in the process. Eventually, we will also be able to make advanced parts and materials for use back on Earth, such as semiconductors.
Most space debris is in low Earth, sun-synchronous, counter-clockwise polar orbit. The station should be positioned to run capture and salvage operations with the least fuel expended. Initial simulations put the optimal position in a circular orbit somewhere near 85 degrees inclination with a 750km apogee and perigee. Alternatively, if this project is built in conjunction with the decommissioning of the ISS, it would be launched into an easy-to-reach equatorial orbit at around 500km.
The estimate for the total cost of this project is around $29.6bn, plus or minus 50%, based mostly on Human resources and over 20 years of development and service time. We plan to outsource to nearly 70 aerospace companies and employ around 5504 people. Other than the basic idea of profiting from recycling one ton of material per day, there are several other potential sources of revenue, such as servicing, insurance, disposal contracts, and technology outsourcing.
The full proposal covers the complete spectrum of a space recycling and manufacturing process and shows some of the potential answers. The amount of money involved means there will need to be a large buy-in from those holding the money. Space needs to be for everyone, and everyone needs to advocate for long-term circularity and sustainability.
Redefining decommissioning
As recent events have shown, there is literally nothing that cannot be achieved ‘in space’. Space X has made science fiction, science fact with the Falcon reusable rocket body – ten years ago, we could only dream of reusable rockets, and now SpaceX launches and returns rocket bodies weekly. Additionally, we have seen the successful capture of a returning rocket body. SpaceX has also been awarded an $800m contract to ‘decommission’ the International Space Station, which appears to mean de-orbit and dumping the structure in the South Pacific in 2030! Where is the sustainability in that?
The decommissioning of the ISS creates a unique opportunity to salvage and reuse the Integrated Truss Structure (ITS) before the de-orbit procedure. The ITS is composed of several segments that have been launched and assembled over multiple missions. Key segments include the Z1, S0, P1, S1, P3/P4, S3/S4, P5, S5, P6, and S6 trusses. The truss was recently upgraded with iROSA (ISS Roll-Out Solar Array) panels and new lithium-ion batteries and can produce as much as 240kw of power. It also houses critical systems such as reaction wheels, communication antennas, and thermal controls. The ITS took ten space shuttle launches and approximately 160 spacewalks to build. The development and launch costs alone were around $9.5bn. It is unique and irreplaceable.
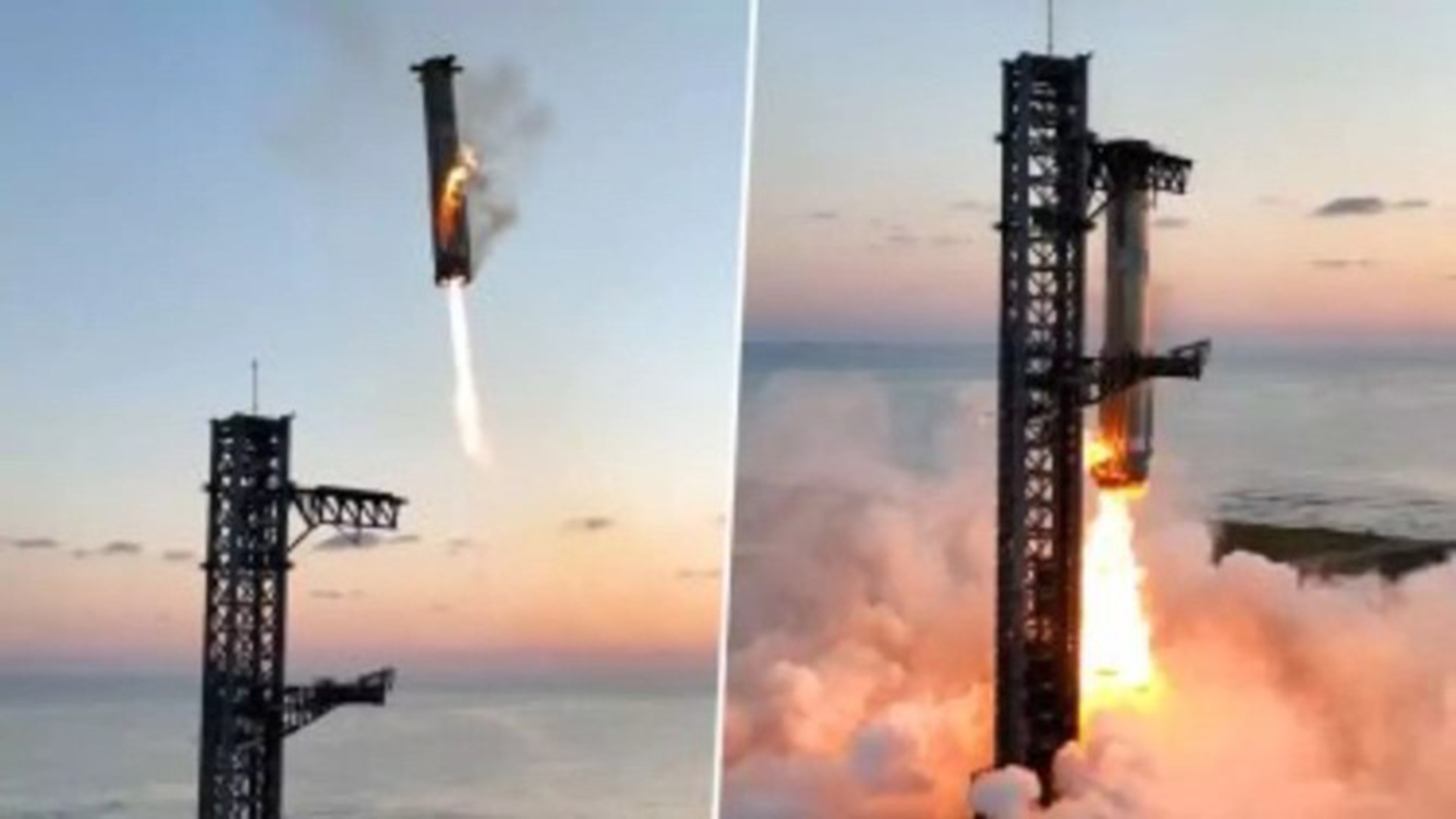
The repurposed Truss could serve as a commercial manufacturing hub or remain a manned research and space tourist destination using all new modules. Additionally, the ITS could be a backbone for the lunar orbital platform ‘Gateway’ (LOP-G), supporting missions to the Moon and beyond as an unmanned manufacturing hub. It could focus on various in-space resource utilisation (ISRU) activities such as recycling, asteroid mining, assembly, or refuelling. Option 2, manned research and tourism, would ensure continuity of scientific research and commercial activities, leveraging the existing infrastructure to provide cost-effective solutions.
A study must assess the ITS’s structural integrity and the feasibility of detachment and modification. A custom-built Remote Command Module (RCM) will be developed to replace the ISS’s standard control functions, handling power management, thermal control, orientation, and communication.
The RCM is mated with the truss at one of the expansion points or to a PMGS. Power lines will be connected, thermal control systems will be integrated, and data connections will be established.
The ISS truss is attached to the rest of the station in only one place: the Unity Module. Robotic arms such as Canadarm2 and ERA will be used to systematically detach the Unity module from the Z1 section of the ITS. There are only 16 bolts connecting the two modules. In a pressurised oxygen-rich environment, humans working from the Unity side could cut and seal power lines, data cables, and ammonia coolant lines.
An orbital transfer would be optimal to ensure the safety and longevity of the ITS and move it to a less congested area of low Earth orbit. The necessary delta-V for the orbit transfer from 400km to 800km is approximately 214 m/s. The Truss has a mass of 54,000kg (119,000 pounds). The Cygnus only carries 2,900kg of fuel. The transfer would require 4,000 kg, and modifications would be necessary.
Space is for everyone, and everyone is needed to ensure its long-term sustainability.
Please note, this article will also appear in the 20th edition of our quarterly publication.