With its state-of-the-art Dutch Electrolyser, EIRES is producing green hydrogen to accelerate the energy transition.
Bert Vreman, a research professional at Nobian and part-time professor at Eindhoven University’s (TU/e) Power & Flow group, explains the mechanical engineering challenges associated with realising cost-effective, industrial-scale electrolysis for green hydrogen production.
With the Dutch Electrolyser as an iconic project, EIRES connects basic research in electrochemical reactor engineering, electrocatalysis, electricity conversion, and process systems engineering at TU/e to the Brainport high-tech industry. The aim is to learn how to upscale a commercially viable, renewable electricity-fed, hydrogen-producing electrolyser to a megawatt scale. Green hydrogen is crucial as a primary fuel to re-generate electricity through fuel cells and a major building block for the chemical industry.
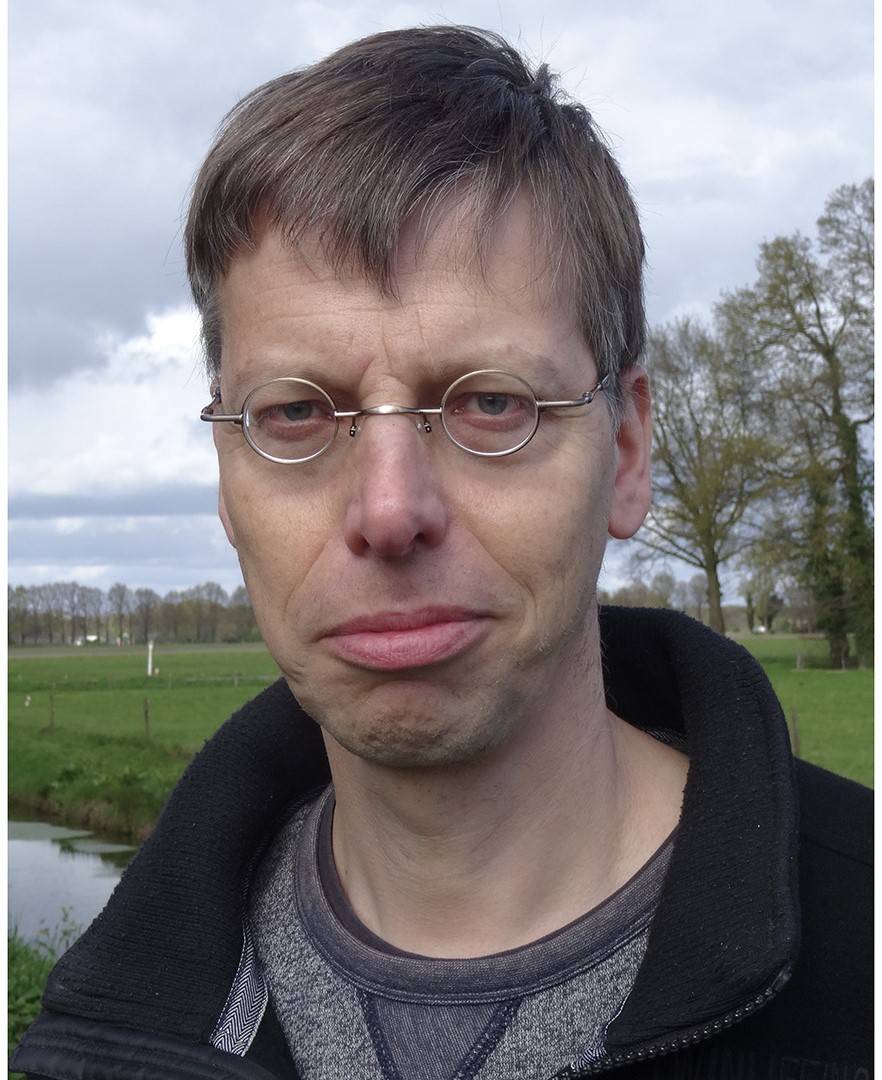
Bert Vreman debunked a common misconception, explaining: “Industrial-scale electrolysers producing hydrogen already exist; that is not the new part here.”
Large-scale electrolysers are commonly used to produce caustic soda, chlorine, and hydrogen from sodium chloride solutions. Still, implementing electrolysers that can produce green hydrogen from water at a large scale is more complex. The keywords here are efficiency and cost-effectiveness since, at the moment, producing hydrogen from natural gas is still cheaper than through water electrolysis.
Difficulties with producing green hydrogen
Producing green hydrogen via water electrolysis is simple: Dip two conductive metal strips in an electrolyte solution and apply a voltage. One of the electrodes attracts positive ions; there gaseous hydrogen is formed. The other does the same with the negative ions, leading to oxygen formation. The process is finished when the hydrogen-containing gas bubbles are collected. However, this process cannot compete with natural gas-based hydrogen production.
One of the problems is that the materials currently used for the electrodes and catalysts are too expensive and rare. Research within the EIRES focus area Chemistry for Sustainable Energy Systems thus focuses on designing and engineering cost-effective materials to replace costly metals and compounds such as platinum and iridium oxide.
Another problem is that the electrolysis process is not as effective as it could be in theory. That is where the EIRES focus area Engineering for Sustainable Energy Systems, comes in.
“We are concentrating on improving the efficiency of the process,” said Vreman. The gaseous bubbles that are formed play an essential role in green hydrogen production. If the liquid electrolyte contains bubbles, the electric current cannot pass through it as easily. Because bubbles are terra incognita, many fundamental questions remain open.
“How are they formed? How do they move along the electrode? What determines how long they will stick to the electrode, blocking its surface and effectively decreasing its activity? How large do they get, and how do they influence the liquid flow behaviour?”
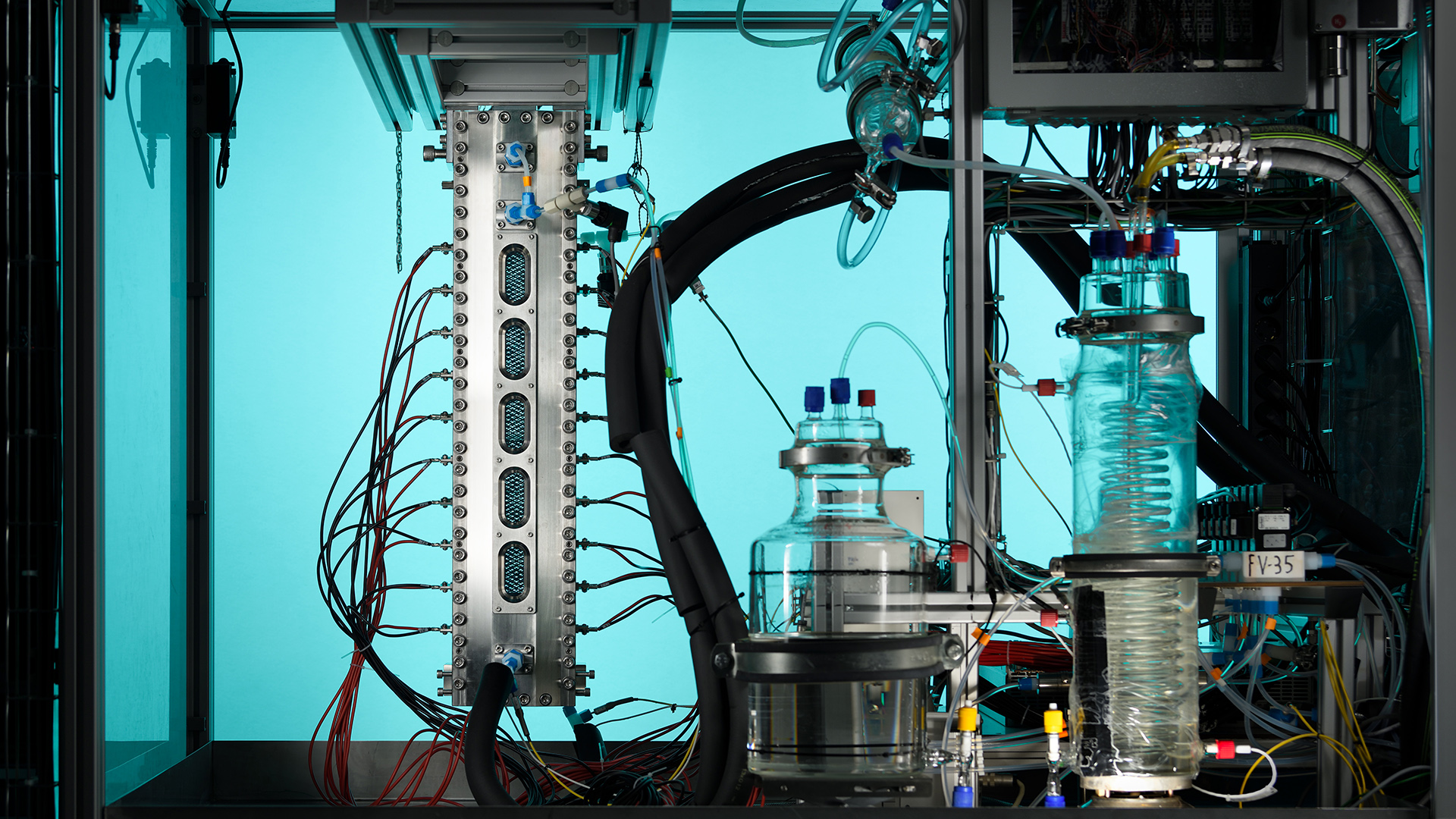
What are some of the complications associated with the process?
What complicates the research tremendously is that it is impossible to put a camera on the electrolyser and observe what happens during green hydrogen production.
“The bubbles are too small, and there are too many of them. With optical methods, you don’t see a thing in electrolysers with macro electrodes at high current density,” Vreman stated. This is why scientists use experiments with small-scale simplified systems and simulations based on physical and chemical models to get an idea of what happens.
Vreman added: “One of the properties we need to study is the coalescence behaviour of the bubbles. So how, when and where do several individual bubbles melt together to form a bigger bubble? To model this behaviour, we need to know the chemical properties of the electrolyte in the vicinity of the bubbles and the electrical charges on the bubble surface. But these also cannot be measured directly during the green hydrogen production process.
“Besides the problem of the lack of experimental data, building realistic bubble models is also complicated because of the interconnectedness of the multitude of parameters that influence the formation and behaviour of the bubble. Think of the contact angle between the bubble and the electrode, the material and geometric properties of the electrode, the chemical composition of the electrolyte and the bubbles, the coalescence, the high gas fraction, the effect of temperature, and the effect of high pressure.”
So, where to start when you want to untangle such a tight and complex knot? “We took an experiment from literature where the gas fraction could be measured and tried to reproduce that with our simulations. And to gain experimental data, we experiment with small-scale, single bubble setups,” Vreman commented.
In addition, together with TU Dresden, EIRES researchers are currently looking into the possibility of micro-CT imaging technology to get a visual of the bubbles.
How can we understand bubble behaviour?
Understanding bubble behaviour is a multidisciplinary endeavour par excellence. Vreman said: “Within TU/e, there is a close collaboration between the Mechanical Engineering, Chemical Engineering & Chemistry departments. Take the Alkaliboost project, a collaboration between TU/e Mechanical Engineering, Chemical Engineering, and the Hydrogen Chemistry Company.
“Another collaboration is the Bubblelectric project, carried out by a consortium of TU/e, TU Delft, the University of Twente, Shell, Nouryon, and Nobian. There are also two PhD students from TU/e working on that project, one in Mechanical Engineering and the other in Chemical Engineering and Chemistry.”
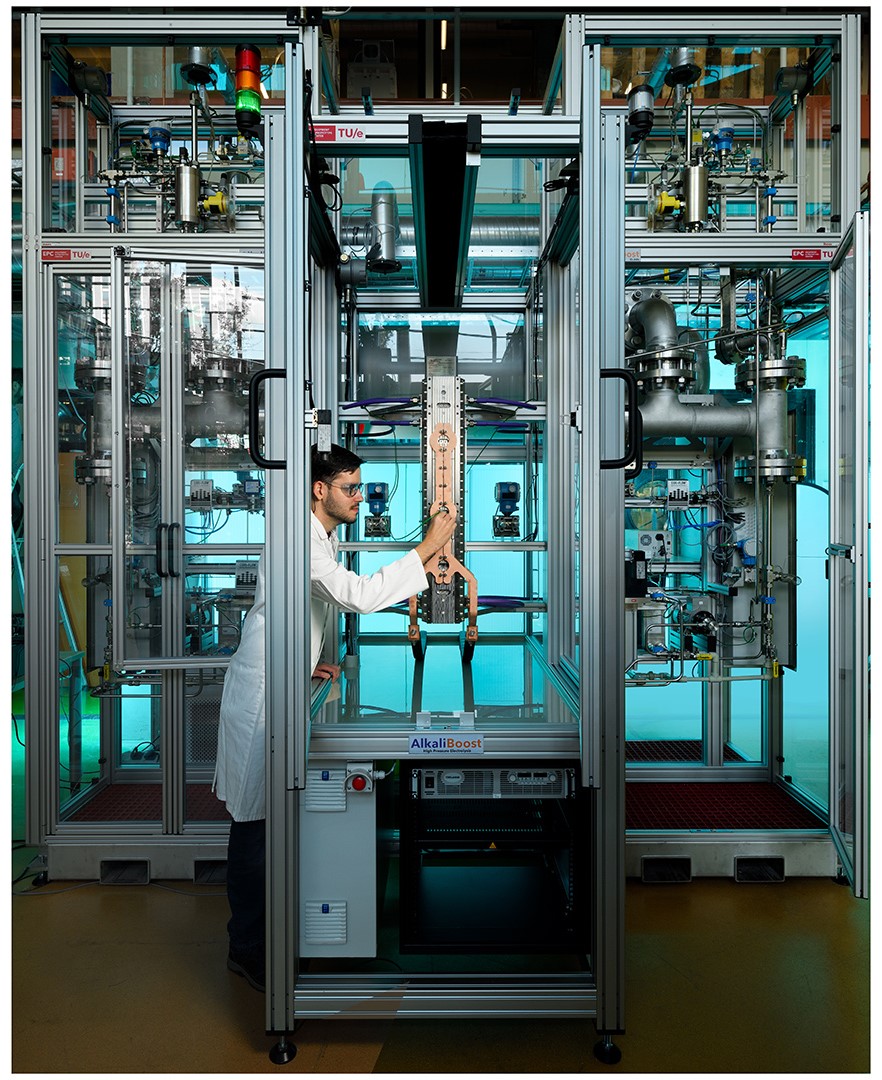
Studying bubbles is a particularly tough area of research. “We only take little steps at a time. After the efficiency gain due to the application of zero gap technology (in which the electrodes are pressed onto the membrane in between), we are not sure how much there is still to gain in terms of efficiency by understanding and controlling the bubble dynamics.
“If we were able to significantly improve the efficiency by removing bubbles faster by increasing the liquid circulation through the electrolyser, if because of our efforts, we needed a large and expensive separator to extract the green hydrogen – we might not have won anything in the end.”
Despite this, Vreman said that there are good reasons to keep investing in this type of research. He concluded: “Bubble dynamics is a fascinating phenomenon for many more applications than water electrolysis alone. It also plays a role in brine electrolysis, lithium chloride electrolysis, boiling and evaporation processes, and bubble column reactors.
“Many people do not realise that green hydrogen production via electrolysis is not just a future experiment – it is extremely relevant today. In the industrial process of producing caustic soda and chlorine, we also make hydrogen. So, when we use electricity from renewable sources to power that process, we are producing green hydrogen already.”