The BLACKCYCLE project, with its ambitious objectives, offers a new value chain for a massive tyre circular economy, delivering innovative solutions to give old tyres new life.
The BLACKCYCLE project, co-funded by the European Union’s Horizon 2020 programme, led by Michelin and involving 12 entities from five European countries, is a great success for four reasons:
- The project has delivered five key technologies for a new value chain that will allow the transformation of ELT into segregated, high-quality SRMs. Those high-quality SRMs can be introduced at a significant rate into new tyres with no impact on their performance.
- The project, with all the partners and their skills, has taken a systemic approach, simultaneously considering the technical, societal, economic, and environmental aspects of the value chain.
- The collaborative work between the project members has optimised the global value chain of ELT transformations instead of individual parts of it, as is usually the case when all the actors act individually.
- This project has contributed to the evolution of the ecosystem around the tyre circular economy in Europe. It was the first one to address the feasibility of the ecosystem. It even inspired the creation of a similar project in Korea.1
Factors triggering the creation of the BLACKCYCLE project
The two main reasons for the BLACKCYCLE project’s creation were, at first, the lack of high-quality materials coming from the recycling of ELT for new tyres and, secondly, the creation of an accessible ELT feedstock.
From 2020 until now, about 1.6 billion ELT per year became waste worldwide, representing 26 million tonnes of material. In Europe alone, that quantity accounts for 3.5 Mt/year. The consortium also noted that 50% of tyres collected in Europe were exported to be valorised outside the continent.
Even though 90% of ELTs are collected in Europe, the majority are used for energy recovery or in non-tyre material applications (playground, rubber goods, etc.). Very few of the materials from the recycling of these ELTs are reused to produce new tyres because of their insufficient quality level.
In parallel, Michelin has set the ambitious objective of replacing 100% of the current fossil raw materials contained in tyres with either recycled raw materials or renewable (bio-sourced) raw materials by 2050. It was clear that solutions to obtain high-quality SRMs from the tyre circular economy were needed.
Addressing the four key challenges: Technological, supply chain creation, economics, environmental
Replacing fossil raw materials in a tyre with new raw materials coming from recycled materials faces at least four big challenges that have yet to be addressed.
Technological
A tyre is an extremely technical product because it must ensure various performances at the same time, like Safety (braking distance under different conditions, roads, temperature, wet/dry/snow), lifespan, and energy consumption (Rolling resistance participating to the fuel consumption of the vehicle). To achieve that high level of performance, the tyre contains many technologies that have been introduced over time. It is not acceptable for the end user to lose any of those performances because of the replacement of fossil raw materials. Therefore, new technologies for processing ELTs into high-quality raw materials are needed.
Creation of the supply chain
Having a new technology at the laboratory scale is good, but for tyre applications, large quantities of new raw materials must be supplied. Therefore, the different processes of the value chain to obtain the new raw materials from the ELT have to be scaled up and developed. This means investments and know-how are needed to guarantee the consistency of the quality of the raw material production.
Economics
The big issue is the competition with the current fossil raw materials, where investments have already been amortised and productivity has been fully optimised. The new value chain will need investments and productivity optimisation. An additional difficulty is that the end user’s willingness to pay more for a tyre with an increased level of recycled content is not so obvious. It is, therefore, extremely important to optimise the new tyre value chain by finding, for example, a valorisation of 100% of what is generated by that value chain.
Environmental
The new value chain’s Life Cycle Assessment (LCA) must be better than that used for fossil materials and other current ways of recycling (such as energy valorisation, for example). Furthermore, the new value chain must not introduce new environmental issues.
Those four challenges made it impossible for Michelin to develop that new value chain alone, so a project gathering all the needed skills to address all the questions was necessary.
The importance of collaboration and ambitions
To develop a tyre circular economy, the way to go was to combine all the skills in the same project.
The need to work with all the necessary skills, the large quantity of waste material coming from ELT, and the need for innovating technologies to create high-quality secondary raw materials were the three triggers for launching the BLACKCYCLE project, which was co-funded by Europe in the Horizon 2020 programme, and led by Michelin.
In addition to Michelin, numerous European partners are supporting the project:
- From Germany: ORION carbon black producer, PYRUM pyrolysis operator for rubber, and ESTATO tyre collector and granulator
- From Switzerland: QUANTIS, specialised in LCA
- From Spain: SISENER consulting and engineering company, CSIC-ICB the Spanish National Research Council, ICAMCYL the International Centre for Advanced Materials and Raw Materials of Castilla y Leon and HERA waste manager
- From Greece: CERTH, the Greek Center for Research and Technology Hellas
- From France: MICHELIN, the tyre company; ALIAPUR, an eco-organisation that collects and recycles tyres; AXELERA, the French competitiveness cluster; and INERIS, the National Institute for Industrial Environment and Risks.
The project was launched in May 2020 and ended in June 2024. It was financed at around 70% by the EU’s Research and Innovation funding programme Horizon 2020 (GA n° 869625).
Ambitious objectives
The BLACKCYCLE project has an upcycling ambition, targeting to create a tyre circular economy for ELT by producing high-tech second raw materials (SRMs) from ELTs. This new research project has the ambition to deliver new technologies and optimise a full value chain, from ELT feedstock to SRMs, with no resource waste in any part of the chain and specific attention to environmental impact. The BLACKCYCLE project objectives are:
- To valorise 100% of ELTs selected
- To increase SRM conversion rates into new tyres by up to ten times
- To decrease CO2 emissions by at least 50%
A new tyre value chain
After four years of existence, BLACKCYCLE proposes a new value chain with new technical building blocks to transform ELT into high-quality materials.
The value chain for creating raw materials that can be reused in tyres without negatively impacting tyre performance is quite complex and requires different steps and technological breakthroughs. Let’s describe it:
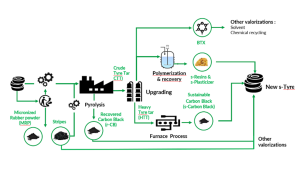
Deconstruction of the tyres
Once collected, the tyres are usually dismembered to separate the different elements, such as metal, fabric, and rubber.
However, tyres are made of different rubber mixtures with very specific compositions. Separating them instead of processing them together increases their value.
For that reason, BLACKCYCLE adds a new step just before the tyre dismemberment, called tyre deconstruction, with two machines designed by MICHELIN:
- IRG (Inside Rubber Grinding extracting inner liner rubber as a Micronised Rubber Powder (MRP) installed in a Michelin facility
- ORC (Outside Rubber Cutting, extracting stripes of the Tread rubber) installed in an ESTATO facility
Inner liner MRP from IRG can be reintroduced in the virgin inner liner rubber of new tyres. Tread stripes from ORC can be subjected to pyrolysis as a feedstock to produce specific oil and recovered CB or go through the cryogrinding process to produce pure tread MRP (MRP is usually made from whole tyres and, therefore, made up of several rubber mixtures).
After the deconstruction operation, the rest of the tyre can be dismembered. The tyre rubber is then reduced to pellets via a granulation process.
Pyrolysis of the granulated rubber
The pellets feed a pyrolysis process. Pyrolysis is a high-temperature treatment of rubber with no oxygen that leads to three fractions: ~15% gas, ~45% oil, and ~40% solid.
- The gas is condensed, and part of it is used to power the process
- The solid part contains an 80% mixture of the tyre’s different carbon blacks, called ‘Recovered Carbon Black’ or r-CB, as well as different minerals (silica, zinc oxide, etc.) With a selected feedstock coming from the ORC tyre deconstruction machine developed by BLACKCYCLE, a better r-CB quality is obtained
- The oil is a complex mixture very rich in C and H called TPO (Tyre Pyrolysis Oil) or CTT (Crude Tyre Tar)
In the project, two pyrolysis processes were developed and optimised in order to get the best oil quality useful for the production of high-quality materials (C/H ratio, limonene content, yield):
• Auger process (SISENER)
• Moving Bed Process (PYRUM)
In parallel, CSIC_ICB also did extensive work to better understand and optimise the key parameters of pyrolysis. CERTH found new catalyst technologies to increase the C/H ratio (important for the s-CB production yield) and solutions to desulphurise the oil.
Oil refining
A new step must be added to make high-quality raw materials from CTT: oil distillation, which requires a new, specific distillation column designed and built by SISENER.
The CTT oil obtained is refined to obtain two fractions:
• HTT Heavy Tyre Tar (~70%)
• LTT Light Tyre Tar (~30%)
It is the quality of these fractions that determines the rest of the chain. CSIC-ICB carried out the optimisation of the column and distillation through experiments carried out in a purpose-built, lab-scale distillation pilot facility.
Transformation of the oil fractions in SRMs: s-CB and s-Resin
The heavy part of the oil called HTT is sent to replace the fossil feedstock of the furnace process of ORION to make a high-quality carbon black (iso quality to commercial ASTM CBs). This carbon black is called ‘Sustainable Carbon Black’ or s-CB because it is obtained from non-fossil resources such as HTT, generated via the ELT pyrolysis process. After optimisation of the furnace process used to make the CB, several tons of three grades have been produced successfully by ORION: N234, N347, and N550, which demonstrate the capacity of the value chain to make drop-in s-CB on the large portfolio of ASTM CB.
The second oil fraction, LTT, is distilled again to obtain another fraction of oil called RTT (Resin Tyre Tar). This fraction is rich in Limonene and other monomers that can be polymerised to get s-resin. It is a highly technical plasticiser. MICHELIN has successfully made an s-resin at the laboratory scale.
The remaining light fraction, mainly composed of BTX (Benzene/Toluene/Xylene), can be sent to petrochemical units to be converted into materials, for example
SMRs validation in rubbers and tyres
MICHELIN has validated all the new SRM (MRP, r-CB, s-CB, and s-resin) in different rubber mixtures by measuring numerous properties.
For r-CB and s-CB (N234, N347, N550), truck and passenger car tyres were built and successfully tested. This demonstrated the possibility of introducing these new SRMs at a significant content without negatively impacting tyre performances and thus closing the loop.
Blackcycle provider of technologies and SRM
In a nutshell, BLACKCYCLE brings new processes and high-quality secondary raw materials at a TRL from three to nine.
Several new processes include:
• Deconstruction machines (ORC& IRG: TRL6),
• Pyrolysis process (Auger: TRL7 and Moving Bed: TRL9),
• Distillation column (TRL7)
Several new SRMs include:
• Innerliner MRP (TRL6),
• Improved r-CB (TRL5),
• s-CB (TRL7),
• s-Resin (TRL3)
An environmentally-friendly viable value chain with a better LCA
QUANTIS preliminary studies show that there is a clear reduction in GHG emissions for the BlackCycle value chain over the conventional energy recovery route and a comparable (and lower) carbon footprint compared to the chemical recycling route. The BLACKCYCLE carbon blacks (sustainable and recovered) also have lower CO2 emissions compared to virgin carbon black at the full life cycle. Recovering the inner liner MRP also leads to three times less CO2 emissions in the production of a virgin inner liner rubber.
In addition to the positive LCA, the HSE risk analysis of the value chain done by INERIS is very reassuring. This work:
- Shows no significant safety or environmental hurdles for the deployment of the BLACKCYCLE value chain
- Provides a lot of useful data and recommendations for future and safe implementation
Preliminary economic study shows long-term viability of the chain
A sensitivity study of some key parameters on the extra cost of the materials produced by the value chain was launched, allowing to identify the most impactful parameters.
The extra cost could be mitigated by:
- Levers coming from BLACKCYCLE: Business model optimisation, valorisation of all by-products, valorisation of SRM in other applications, improvement of SRM quality and yields
- Levers coming from the strategy of SRM ramp-up: Nature and rate ramp-up of SRM in tyres to activate the market demand
- Levers coming from European support: Regulatory and incentives policies to help investment and robust the economic viability
Industrial deployment following the project: What’s next?
A lot of results coming from BLACKCYCLE can be used in support of the deployment of the value chain after the end of the project:
- The technical data of the processes and new SRM, including the associated know-how
- The applications for the by-products of the chain
- The technical-economical studies
- The social acceptance guidelines and tools to prepare the local setup of the industrial equipment
- The HSE actions to put in place (e.g. diffuse emission monitoring, secure site access control)
In addition, some recommendations to the European Commission that could help the deployment of the value chain have been summarised in a policy brief:
- Promote policies that recognise the added value of material recovery from end-of-life tyres to deploy an economically viable recycling value chain
- Create a regulatory framework that recognises pyrolysis technology as a material recovery process
- Incentivise investments in end-of-life tyre recycling processes to ensure their industrial scale-up
- Set EU-harmonised end-of-waste criteria for secondary raw materials derived from end-of-life tyres to ensure legal certainty and free circulation within the single market
- Create a regulatory framework incentivising customers to use recycled materials and avoid virgin fossil or other extraction-based resources.
In conclusion, thanks to exceptional collaborative work, BLACKCYCLE is a game changer. It provides innovative technologies to make the tyre circular economy a reality.
References
- https://www.businesskorea.co.kr/news/articleView.html?idxno=204974
Please note, this article will also appear in the 19th edition of our quarterly publication.